We are all familiar with the popular foam plastic insulation material, polystyrene when it comes to protecting consumer items and for its application in the food industry in the form of plastic trays and containers. The flame retardancy of this material is explored in the journal Materials.
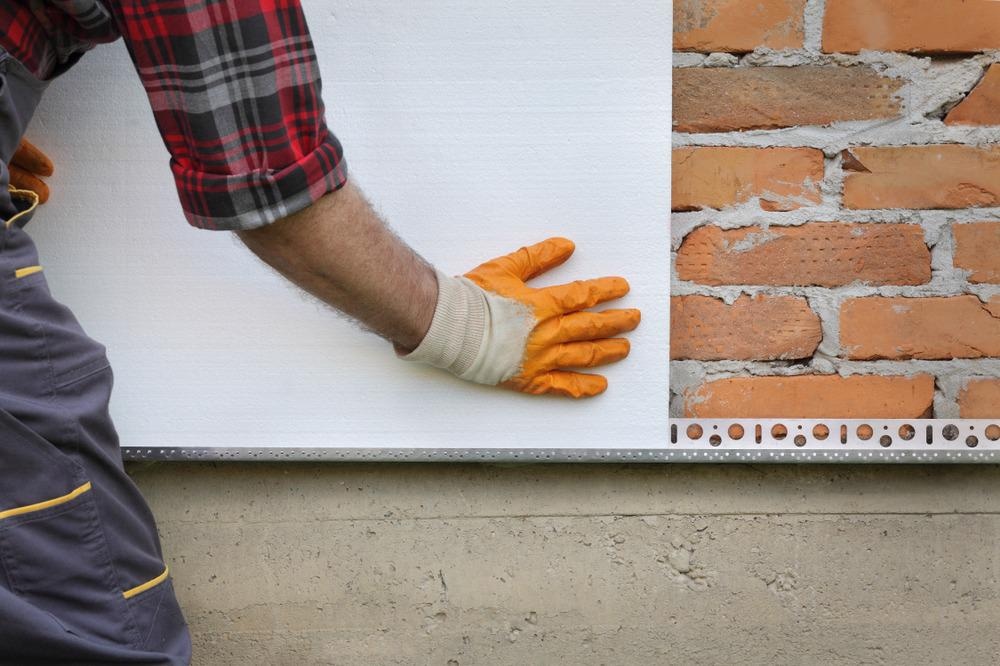
Study: An Effective Expanded Graphite Coating on Polystyrene Bead for Improving Flame Retardancy. Image Credit: Sima/Shutterstock.com
In recent years, this widely-used synthetic polymer material has found major application in construction as expanded polystyrene (EPS) is used as an insulated panel system in floors, walls, and roofs in both domestic and commercial buildings. However, one of the major drawbacks of EPS is the fact that it is highly flammable and can ignite at relatively low temperatures.
Therefore, a team of researchers at the Korean Institute of Civil Engineering and Building Technology have devised a flame-retardant coating using expanded graphite (EG) along with a process for applying the coating evenly to a beaded polystyrene surface. Their bid is to improve the flame retardancy of commercial EPS beads using the coating in order to deliver an effective fire safety solution.
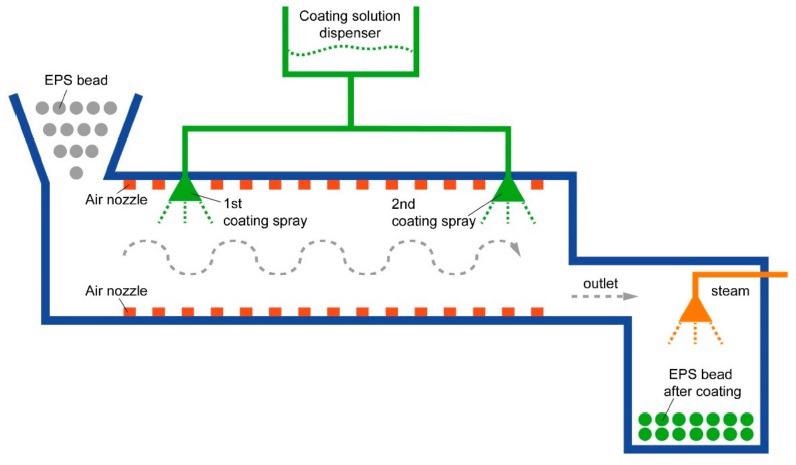
Case for coating polystyrene beads with the flame-retardant coating solution. Image Credit: Bae, M et al., Materials
Improving Safety Standards
While EPS panels are being deployed on construction sites all over the world, safety standards regarding nonflammability typically vary. In Korea, the government has started to implement material standards that means that these materials should at least pass the semi-nonflammability test in order to be fit for purpose on-site.
However, most commercial EPS panels do not pass current safety standards, and this is what directed the Korean researchers to their task. Led by senior research fellow Dr. Jaesik Kang, the team aimed to add a “monomer capable of imparting flame retardancy to the main chain of the polymer to prepare a flame-retardant polymer,” Kang explained.
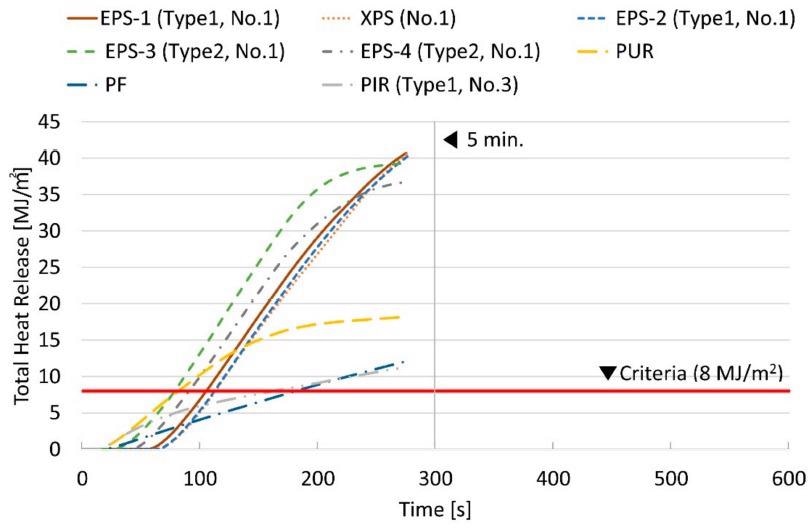
THR with foamed plastic insulation specimens according to the cone calorimeter. Image Credit: Bae, M et al., Materials
Expanded graphite (EG) was identified as a good candidate for the intended application due to its unique properties. When in contact with the heat of fire the graphite expands and generates an intumescent layer which retards the spread of flames and thus minimizes one of the biggest dangers of fire combustion—the release of toxic fumes.
While EPS itself demonstrates toxicity levels equal to or less than natural or organic materials, the spread of a fire in a building can lead to the release of toxic fumes from other building materials including chemical-based paints and adhesives. Therefore, due to the low-flame retardant efficiency of EPS it is necessary to improve safety standards and devise methods in order to do so.
Application of Expanded Graphite
As the name suggests, expanded graphite has the capacity to expand, which contributes to its flame-retardant effect. Graphite possesses a special layered structure that facilitates the insertion of molecules between the graphite layers. So, when the materials come into contact with fire, the graphite layers are pushed apart like an accordion.
In order to evenly apply the EG to the beaded surface of EPS, the team manufactured the flame-retardant solution prepared from a water-soluble composition of EG and other additives. The result was a fire retardant expanded polystyrene block (FR-EPS).
“The flame-retardant coating solution contains 10 to 30 wt% of a porous particle, 5 to 20 wt% of a starch, 20 to 50 wt% of a flame retardant manufactured with the EG, and 20 to 30 wt% of a water-based binder. A total of 0.1 to 3 wt% of a silane (silicone compound) and 3 to 15 wt% of a thermosetting resin are included as additives,” explained Kang.
For the study, materials were subjected to tests under ambient air conditions in accordance with KS F ISO 5660-1, which is the ISO standard for reaction to fire tests. For comparison, the team used a variety of non-EG-treated EPS blocks of various compositions and then measured the results against the Fire Retardancy Index (FRI).
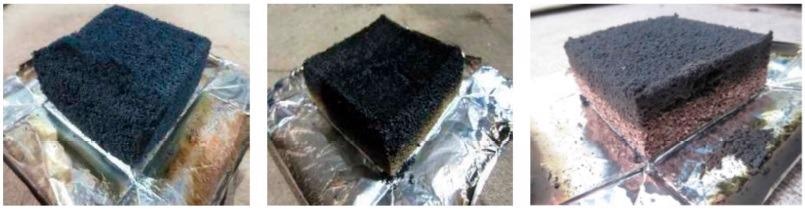
FR-EPS samples after the cone calorimeter test. Image Credit: Bae, M et al., Materials
The materials were then subjected to both horizontal and vertical burning tests. Overall, the FR-EPS based on EG demonstrated better performance levels, “FRI values of FR-EPS proved the ‘excellent’ level and had higher FRI values compared with FRI values of other polystyrene composites,” said Kang.
While some of the commercially available EPS products exhibited a high level of self-extinguishing in horizontal burning tests their levels remained low in vertical testing. However, the FR-EPS confirmed high-levels of self-extinguishing in both horizontal and vertical tests – improving two levels in the latter.
The FR-EPS also passed the standard for semi-nonflammability in regulations therefore showing that coating EPS with a water-soluble flame retardant manufactured from expanded graphite achieves good fire safety standards.
Kang and his team successfully produced an effective flame-retardant coating based on expanded graphite to improve flame retardancy of expanded polystyrene beads. Introducing both more stringent policies and such methods to improve flame retardancy in construction will inevitably produce safer environments for those living and working within the buildings.
References
Bae, M.; Lee, H.; Choi, G.; Kang, J. An Effective Expanded Graphite Coating on Polystyrene Bead for Improving Flame Retardancy. Materials 2021, 14, 6729. https://www.mdpi.com/1996-1944/14/21/6729
EUMPS, ‘Behavior of EPS in Case of Fire’. August, 2002. [https://eumeps.org/: Accessed November, 2021]
Disclaimer: The views expressed here are those of the author expressed in their private capacity and do not necessarily represent the views of AZoM.com Limited T/A AZoNetwork the owner and operator of this website. This disclaimer forms part of the Terms and conditions of use of this website.