3D additive printing is becoming more commonplace in today's industries. To improve the properties of printed polymers, a paper published on chemxriv has explored the incorporation of aramid nanofibers (ANFs) into printable photoresins.
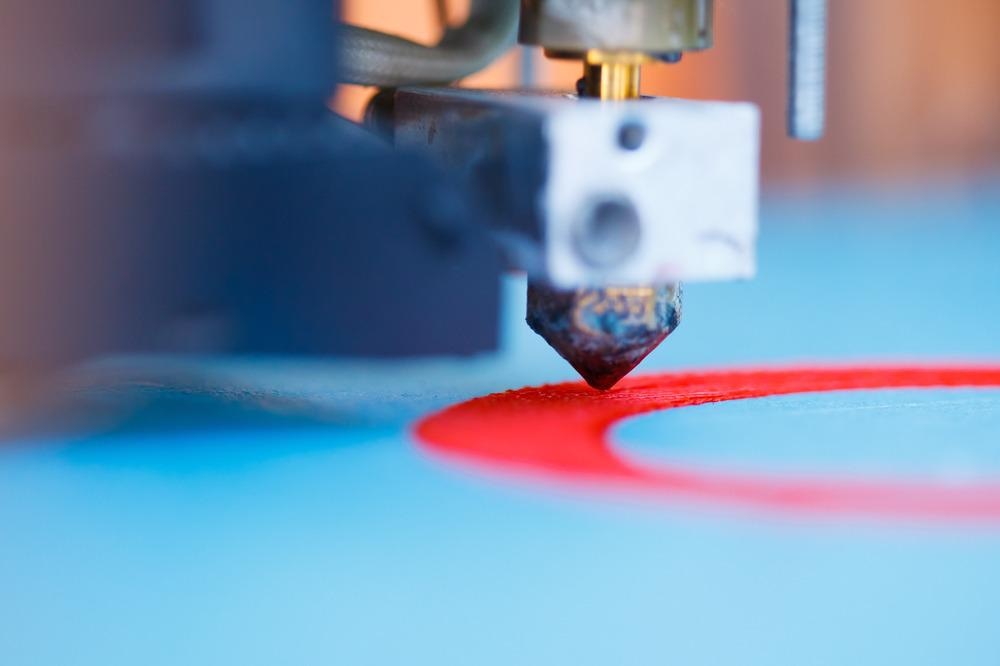
Study: 3D Printing of Aramid Nanofiber Composites by Stereolithography. Image Credit: nikkytok/Shutterstock.com
3D Printing: A Revolutionary Technology
3D printing is a revolutionary technology that creates three-dimensional objects layer-by-layer. 3D printing technologies have been used to manufacture medical devices in the automotive industry, on board the International Space Station, and are even being used to print entire houses.
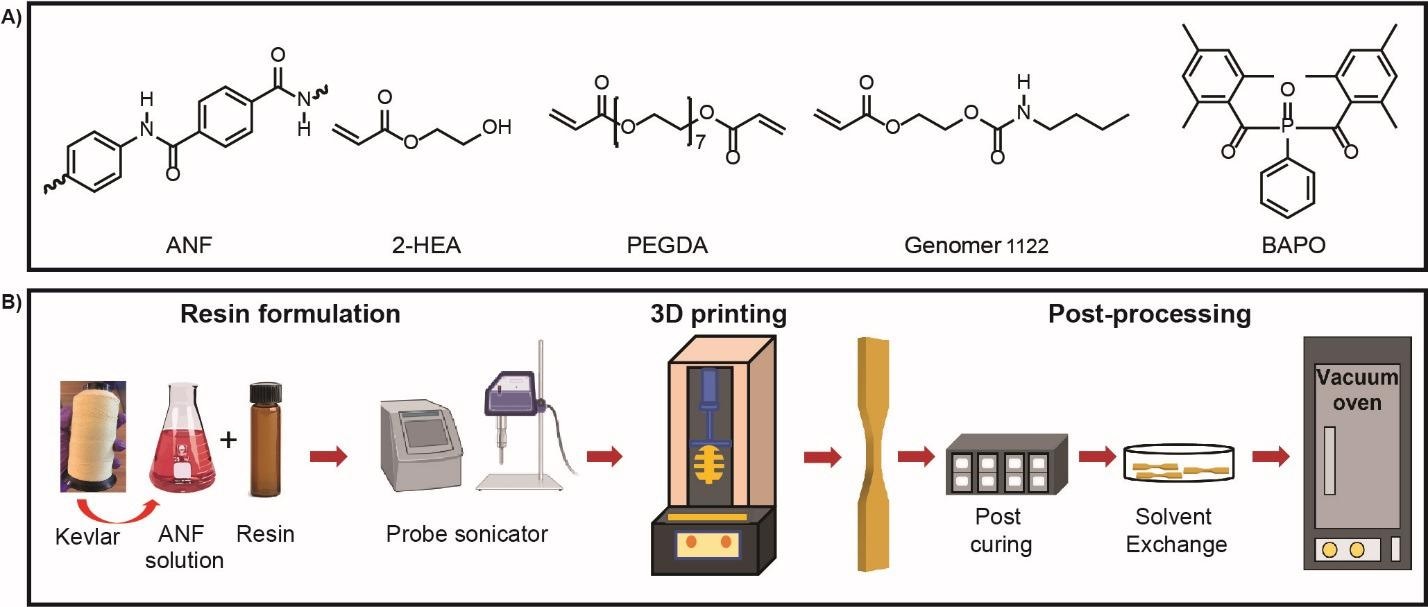
(A) Molecular structures of the components used for the formulation of an ANF containing photoresin. (B) A schematic diagram for the steps followed for the nano filler preparation, photoprinting and post processing procedures followed for the printed nanocomposites in this study. Image Credit: Perera, S et al., chemxriv
3D printing produces highly complex, customized structures cheaper than conventional mold-based fabrication methods, and produces less waste than traditional manufacturing. Additionally, 3D printing can take advantage of a plethora of materials to create commercially useful products. Much focus has been placed on improving both the technology and the properties of materials used for 3D printing.
Vat Polymerization and Stereolithography
Recently, there has been increasing attention on vat polymerization printing methods in the 3D manufacturing field. This is due to their high fabrication speeds and resolution. Stereolithography is a vat polymerization process that uses a laser to achieve photopolymerization of a photoinitiator containing acrylate-based resins.
Stereolithography can produce smooth finished, high-quality objects with a resolution as small as 10 micrometers. The technique requires photoresins that contain mono- or oligomers in a liquid state that can rapidly polymerize when exposed to light and must have low viscosity. Currently, the choice of resins for the technique is limited as many currently face fabrication challenges and the resultant printed structures have insufficient mechanical and thermal properties.
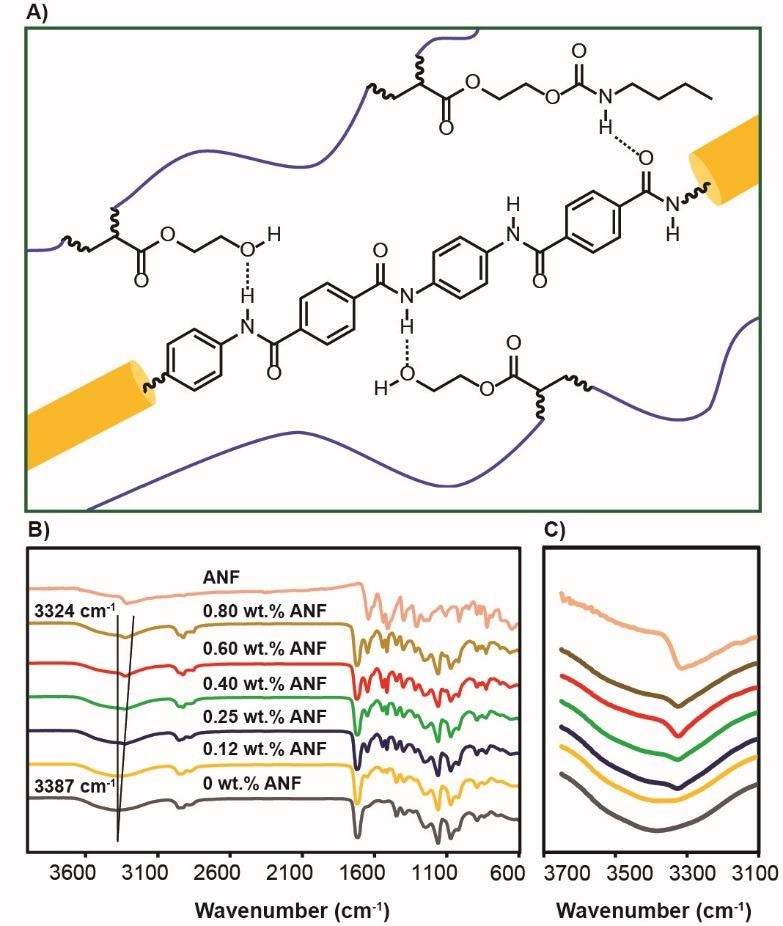
(A) Hydrogen bond formation between ANFs (am-ide groups) and photoresin (hydroxyl groups). (B) FT-IR spectra for control photoresin and nanocomposites with different concentrations of ANFs after 3D printing. (C) Expand-ed hydroxyl stretching region of the control photoresin and the nanocomposites with different concentrations of ANFs after 3D printing. Image Credit: Perera, S et al., chemxriv
Improving Photoresins for Stereolithography
There is a pressing need for photoresins with better properties that can produce viable 3D printed structures. To this end, composites and nanocomposites have been explored. Composites are advantageous as different additives can be mixed with polymer matrices at a low cost, and the process is also scalable. Materials with a range of attractive properties can be produced.
Nanofillers such as carbon nanotubes and cellulose nanocrystals have been explored as they improve the mechanical, electrical, and thermal properties of composite materials. Even though the field has produced numerous polymeric nanocomposites, the application of these in 3D printing, and especially in vat polymerization methods, is still limited.
Using Aramid Nanofibers in Stereolithography Printing
The team behind the research published on chemxriv developed a process for developing aramid nanofiber containing photoresins that can be printed using stereolithography.
Aramid nanofibers, which are comprised of Kevlar fibers, have been the subject of recent research. These nanocomposite materials display exceptional strength and stiffness due to their strong intermolecular interactions. Even including a small amount of these fibers in a polymer matrix increases mechanical properties such as toughness and tensile strength.
Additionally, aramid nanofibers can be used in applications such as water purification, biomedical technologies, and products that require advanced infrared absorption. However, these materials are still not commonly used in 3D printing. Reasons for this include the difficulties of incorporating them into printable, homogenous mixtures of resins.
Overcoming Issues with Aramid Nanofibers
As aforementioned, one of the main problems with using these nanocomposites is the difficulty of manufacturing a homogenous photoresin including them. To overcome this problem, the aramid nanofibers were added to the resin in a solution using dimethyl sulfoxide.
Another issue is the quality of printed structures. To avoid the induction of defects such as cracks and produce parts that retain their resolution and shape, the team developed an optimized post-print processing method.
The resulting printed products displayed elevated tensile strength and toughness due to the inclusion of aramid nanofibers into the polymer matrix, although reduced mechanical properties were observed above a certain concentration of aramid nanofiber loading in the printable material. The study demonstrated that aramid nanofibers are attractive additives to provide nano-scale reinforcement of structures using photoresins without compromising their printability.
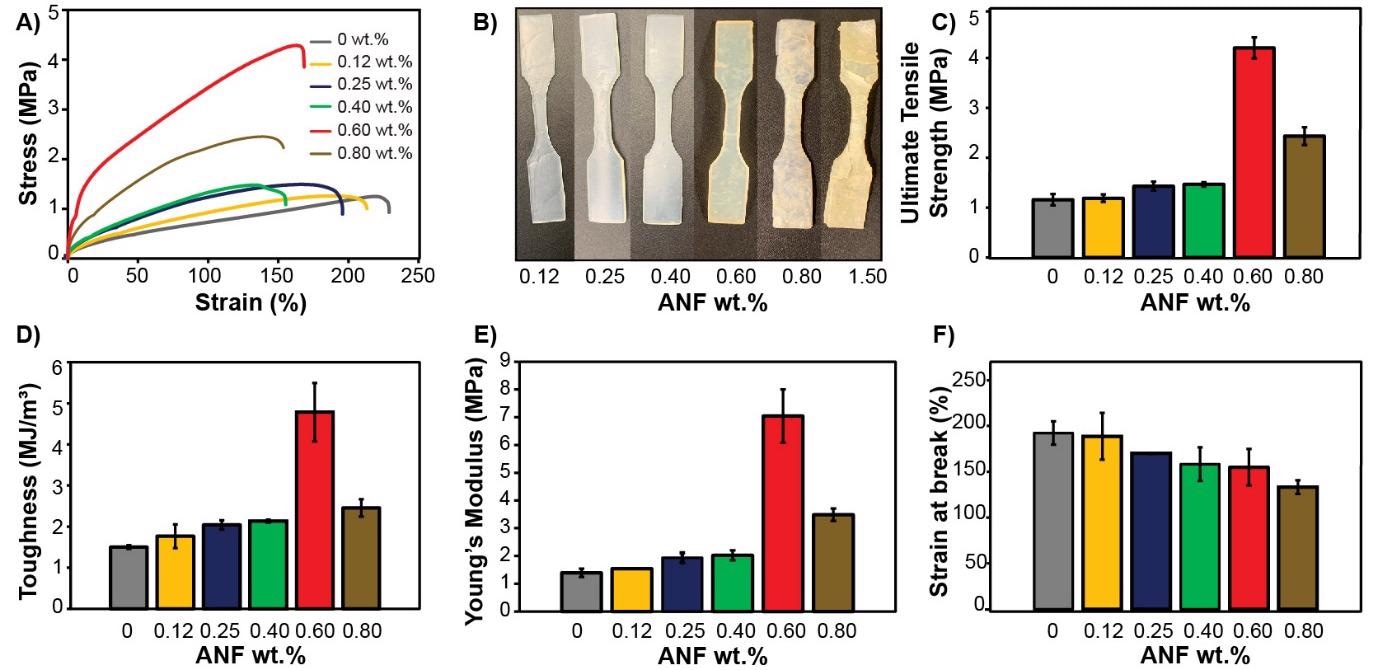
Evaluation of mechanical properties of the control photoresin and the ANF nanocomposites. (A) SLA printed tensile specimens of nanocomposites with different concentrations of ANFs. (B) Representative stress-strain curves. (C) Ultimate tensile strength. (D) Toughness. (E) Young’s modulus. (F) Strain at break of the control photoresin and nanocomposites with different concentrations of ANFs. Image Credit: Perera, S et al., chemxriv
The Future
The field of 3D printing is rapidly becoming more commonplace as industries leverage its benefits to produce materials with superior mechanical and electrical properties that cost less and are more sustainable. By developing new techniques and advanced materials, including nanocomposites, scientists working in the field of 3D printing are building the future of the industry.
The research paper has demonstrated the potential of aramid nanofibers and their use in stereolithography printing to produce commercially viable materials in a scalable manner. The team has identified a few challenges that still need to be addressed, however. They have stated that their future work in this area will be developing new resin composites that have higher aramid nanofiber loading, using the post-print processing methodology set out in the research.
Disclaimer
Important Notice: ChemRxiv publishes preliminary scientific reports that are not peer-reviewed and, therefore, should not be regarded as conclusive or treated as established information.
Further Reading
Perera, S et al. (2021) 3D Printing of Aramid Nanofiber Composites by Stereolithography [online] chemxriv.org. Available at: https://chemrxiv.org/engage/chemrxiv/article-details/618b13682bf8a9adf5d6510c
Disclaimer: The views expressed here are those of the author expressed in their private capacity and do not necessarily represent the views of AZoM.com Limited T/A AZoNetwork the owner and operator of this website. This disclaimer forms part of the Terms and conditions of use of this website.