Many important industries are making increasing use of flexible sensors for a variety of applications. Now, a paper published in the journal Materials has presented a new method for fabricating a flexible, noncontact sensor using PEDOT:PSS and a printer paper substrate.
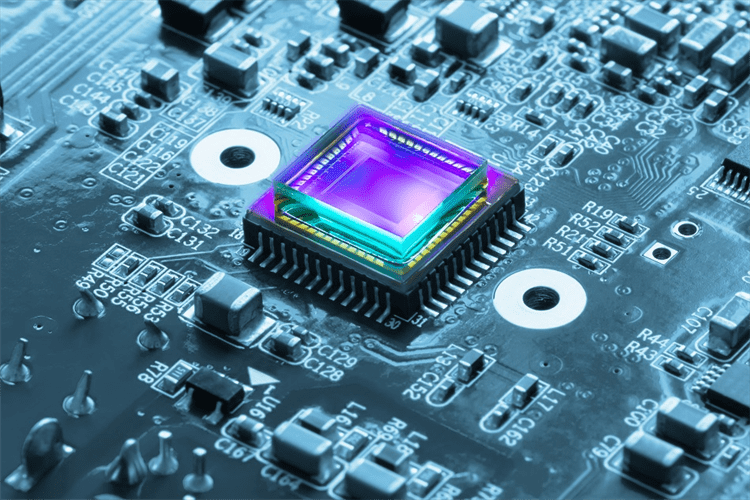
Study: A Flexible Temperature Sensor for Noncontact Human–Machine Interaction. Image Credit: Andrew Berezovsky/Shutterstock.com
The Importance of Flexible Noncontact Sensors
Several industries use flexible sensors for numerous applications. These include robotics, health monitoring, and wearable electronic skin, with the field making significant advances in recent decades. More recently, the Covid-19 outbreak has crystallized the need for remote control of everyday objects such as elevator panels and doors to prevent cross-infection, and research into reliable, low-cost flexible non-contact sensors has intensified.
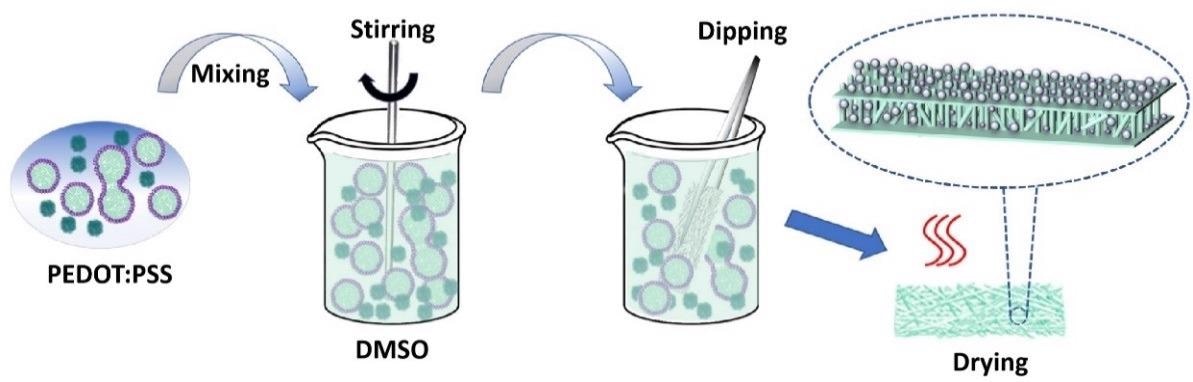
Schematic diagram of the preparation process for flexible temperature sensors. Image Credit: Chen, S et al., Materials
Flexible non-contact sensors have several advantages over conventional sensing equipment. They offer enhanced efficiency levels, seamless contact with the wearer’s body (which is a dynamic system) and long-term monitoring of parameters such as body temperature.
The real-time temperature response is advantageous for applications such as electronic skin, and as a basic physiological parameter, can inform medical diagnosis. Additionally, one of the most commercially viable uses of real-time body temperature sensing is the control and monitoring of human-machine interactions.
Requirements of a Flexible Noncontact Sensor
Flexible, wearable noncontact sensors need to have several physical, mechanical, and electrical properties and characteristics.
Firstly, they need to be able to withstand the physical deformation that occurs from the everyday movements of the wearer. Secondly, they need to have performance that can be matched with traditional thermometers in terms of sensitivity, accuracy, repeatability, and response time.
Additionally, they must be able to reliably operate in the range of 20-50 oC, which is the normal range of body temperature, and must also demonstrate superior anti-interference.
Moreover, they must be able to be manufactured at a large-scale and low cost. Ideally, their manufacture should be environmentally friendly. Many of their electrodes are constructed from materials such as graphene and metallic nanomaterials, which can be sensitive to pressure and strain, causing signal crosstalk.
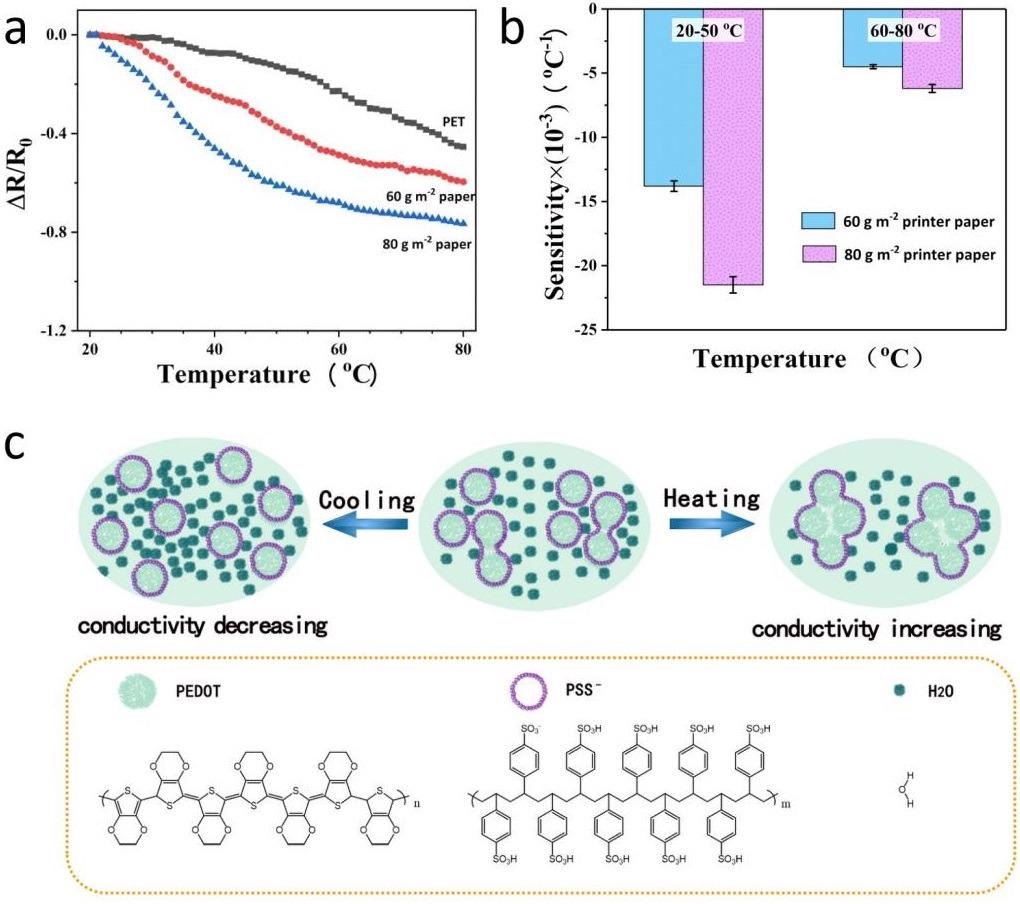
Effect of flexible substrates on sensitivity. (a) Variation curves of the normalized resistance (ΔR/R0) with respect to temperature for three flexible temperature sensors; (b) the sensitivity of paper-based sensors within different temperature ranges; (c) schematic diagram of temperature response mechanism for PEDOT:PSS based sensor. Image Credit: Chen, S et al., Materials
Constructing a Flexible Sensor out of Inkjet-Printed PEDOT:PSS and Paper
Writing in Materials, a team led by Shiqi Chen has demonstrated a flexible non-contact sensor fabricated by printing PEDOT:PSS onto everyday printer paper with simple dip-drying methods. PEDOT:PSS has gained significant attention in recent years for its use in flexible sensors. It is an aqueous solution of PEDOT and PSS, with adequate conductivity and good levels of optical transparency.
Fabrication techniques such as inkjet printing, dip-drying, and direct-print dispensing make it possible to obtain films of PEDOT:PSS and integrate them into various electronic devices, taking advantage of their superior electrical and optical properties. These films serve as active components in flexible electronic devices due to their sensitivity to environmental factors such as humidity, temperature, and pH. These factors affect the resistance of the films.
Another property that makes PEDOT:PSS films ideal as active layers for flexible devices is their lack of sensitivity to heat and pressure when prepared on a suitable substrate that does not have high levels of elasticity or special microstructures.
For this reason, the team chose everyday printer paper for the dip-drying process. The process involved submerging the paper in the solution and then drying it to prepare it for use as a flexible sensor. The team designed a temperature-based game controller interface to demonstrate the potential of the sensor, which also could be used as a rehabilitative device for adults suffering from hand dyskinesia.
Due to its stability and sensitivity to temperature ranges that fall within normal human body temperature ranges, the temperature-sensitive paper could quickly identify the proximity of objects with different temperatures. Due to this advantageous behavior, the prepared dip-dried PEDOT:PSS printed paper can reliably be used to control human-machine interactions as a noncontact flexible sensor.
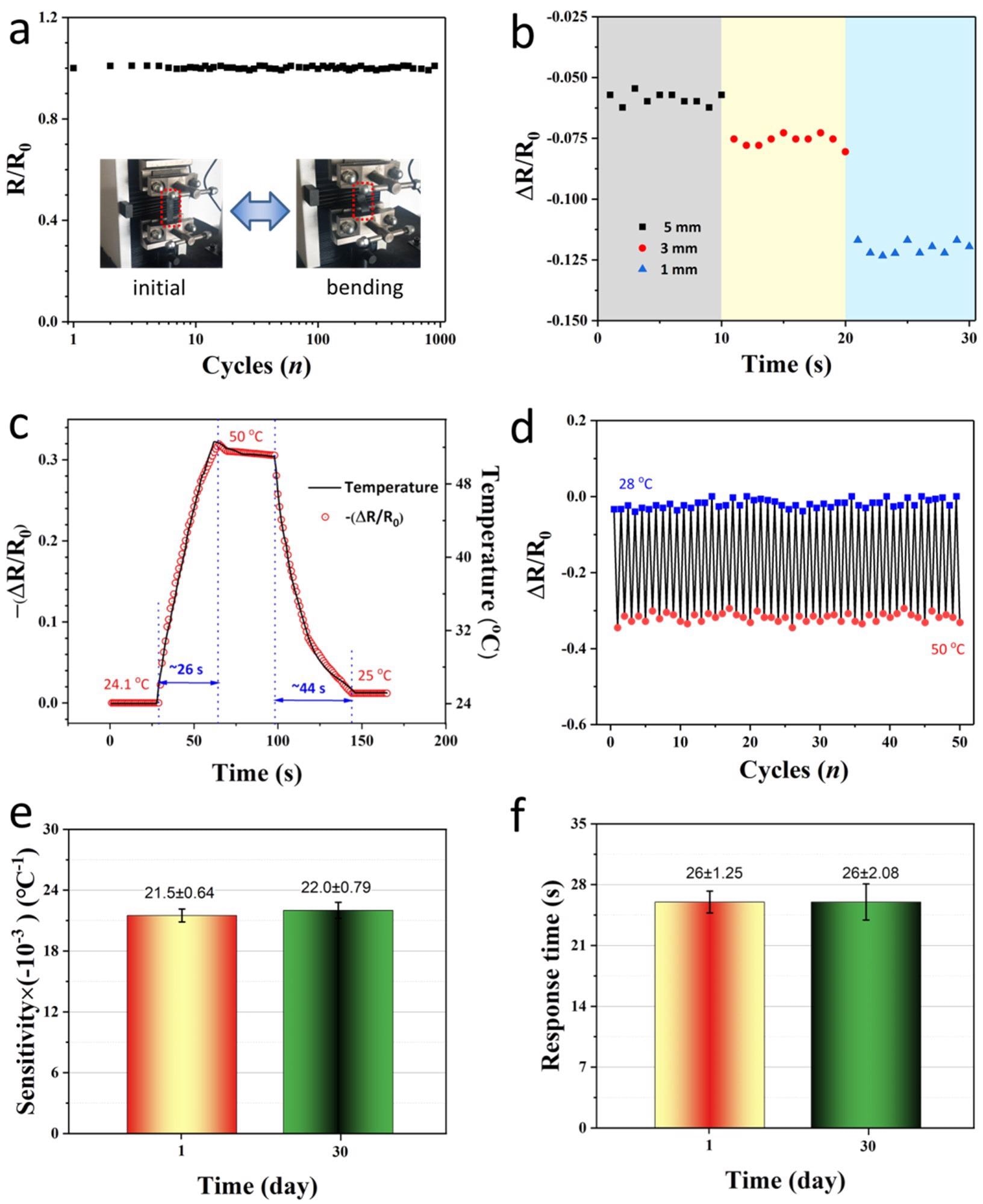
Temperature-sensitive performances. (a) Sensing stability of PEDOT:PSS paper buckled from initial to -30% for 1000 times; (b) Temperature sensitivity of the PEDOT:PSS paper at a finger proximity distances of 1, 3, and 5 mm, respectively; (c) The response time curve ranges from 28 °C to 50 °C; (d) Multi-cycles temperature-sensing stability tested between 28 and 50 °C. Comparison of (e) sensitivity and (f) response time of the same sensor between Day 1 and Day 30. Image Credit: Chen, S et al., Materials
What This Research Means for the Future
Whilst there has been plenty of research into the use of PEDOT:PSS solutions for flexible electronic devices, to date there has been little research into the use of this substance as a non-contact interface for human-machine interaction control. This research has provided a significant contribution to the development of flexible non-contact sensors for this purpose.
By developing a flexible material with superior sensitivity, fast response time, and enhanced stability combined with ease of large area preparation and low cost, the material created by the research team has potential as an application for electronic skin, intelligent human-machine interaction interfaces for robotics, and next-generation intelligent medicine advances.
Further Reading
Chen, S et al. (2021) A Flexible Temperature Sensor for Noncontact Human–Machine Interaction [online] Materials 14:23 | mdpi.com. Available at: https://www.mdpi.com/1996-1944/14/23/7112
Disclaimer: The views expressed here are those of the author expressed in their private capacity and do not necessarily represent the views of AZoM.com Limited T/A AZoNetwork the owner and operator of this website. This disclaimer forms part of the Terms and conditions of use of this website.