A recent study presented in the Additive Manufacturing journal has explored the production and properties of 3D printed alloys with a specific focus on the roles of the solute and nucleant in grain refinement processes.
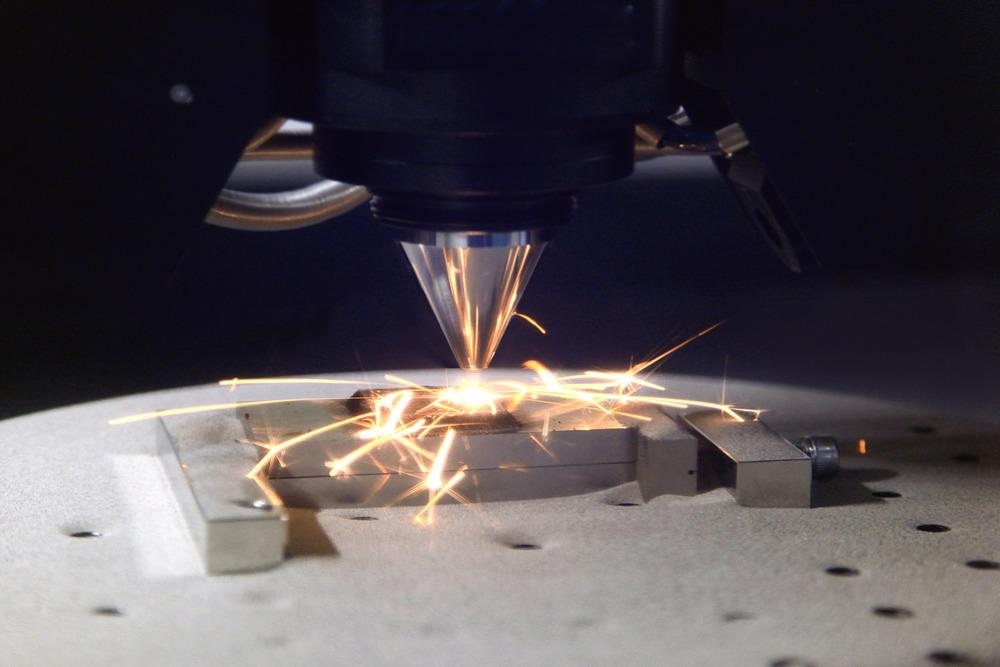
Study: Demonstrating the roles of solute and nucleant in grain refinement of additively manufactured aluminium alloys. Image Credit: sspopov/Shutterstock.com
The advent of state-of-the-art powder-based additive manufacturing techniques has led to a revolution in the manufacture and engineering of advanced metallic materials.
Modern techniques such as selective laser melting (SLM) have been shown to facilitate considerable flexibility and rapid fabrication potential, affording manufacturers a high degree of design freedom in terms of parts’ complexity and functionality.
The most notable downside to these techniques lies in their tendency to form coarse-textured columnar structures within the additive manufacturing-fabricated components.
This phenomenon is linked to the way in which additive manufacturing processes solidify the material used. Extremely large thermal gradients and high cooling rates are present within relatively small melt pools – a factor that can result in epitaxial grain growth.
Because additive manufacturing processes work by building layers of a structure on top of one another, there is also a need to partially re-melt the previous layer as a subsequent layer is deposited. This process often sees the new layer growing epitaxially from the existing grains, leading to the growth of columnar grains which may even span multiple layers.
These coarse columnar microstructures may lead to sub-optimal mechanical properties and increased susceptibility to hot cracking due to the high thermal shock which typically occurs during additive manufacturing.
Thankfully, these issues can be addressed with grain refinement techniques. A recent study presented in the Additive Manufacturing journal has explored this with a specific focus on the roles of the solute and nucleant in this grain refinement process.
Grain refinement in traditional metal casting is typically achieved through inoculation – the process of adding a small number of nucleant particles (to trigger surface nucleation) – or the addition of suitable solutes into molten metal. This helps to restrict grain growth via heterogenous nucleation within the constitutional supercooling zone generated by the solutes.
There has been a great deal of interest in leveraging this useful inoculation treatment and/or solute addition approach in metal-based additive manufacturing to facilitate effective grain refinement in fabricated parts.
There have already been a number of successful examples of this process, leading to the development of an analytical solution referred to as the Interdependence Model.
Using this model, it has been possible to determine that heterogeneous nucleation takes place on effective nucleants within the constitutional supercooling zone generated by solutes and that this process is capable of inhibiting epitaxial grain growth via grain refinement.
Video Credit: Markforged/Youtube.com
Various numerical models have also been developed which are able to accurately correlate grain size with a range of variables related to solidification, for example, the cooling rate, overall undercooling ahead of the solid/liquid interface, and nucleant particle density.
These models provide excellent insight into the grain refinement mechanisms in the majority of cast alloys, but uncertainties remain in terms of understanding these grain refinement mechanisms in the context of additive manufacturing.
Further research was required to ascertain whether or not the solute growth restriction method used in conventional metal casting is directly applicable to metal-based additive manufacturing, due to this process being routinely subjected to extremely large thermal gradients and high cooling rates.
There is a danger that the solidification conditions required of additive manufacturing could limit or even eliminate the generation of constitutional supercooling zone ahead of the solid-liquid interface, resulting in far less efficient growth restriction capabilities for solutes used.
Using SLM as an example technique, the authors looked to investigate whether the growth restriction factor employed in metal casting methods was also appropriate for use in understanding solutes’ capacity for effective grain refinement when taking into account the large thermal gradients common to additive manufacturing, and whether or not these high thermal gradients (and cooling rates) limit or even negate the role of solutes entirely.
The study learned that despite rapid cooling during the SLM process, it was still necessary to add solutes to generate enough undercooling to induce heterogeneous nucleation to achieve significant grain refinement. It was also confirmed that solutes’ refining efficiency increases as their concentration increases.
It was possible to ensure good grain refinement during the SLM process by adding a combination of solute and nucleant particles, with grain size decreasing as growth restriction increased.
One of the study’s key findings was that, unlike conventional cast metals, there is a non-linear relationship between the grain size and the growth restriction factor. The author’s theorized that this may be due to the large thermal gradient common to SLM hindering the formation of sufficient constitutional supercooling zone ahead of the solid/liquid interface limiting the growth restriction effect of the solutes.
The study highlighted that there would appear to be good potential to leverage the effective grain refinement techniques used in metal casting within additive manufacturing methods. Forming a useful basis for further work in this area, this work could also open up the potential for further optimization of additive manufacturing processes.
References
Qiyang Tan, Yu Yin, Arvind Prasad, Gan Li, Qiang Zhu, David Henry StJohn, Ming-Xing Zhang, Demonstrating the roles of solute and nucleant in grain refinement of additively manufactured aluminium alloys, Additive Manufacturing, 2021, 102516, ISSN 2214-8604, https://www.sciencedirect.com/science/article/pii/S2214860421006631?via%3Dihub
Disclaimer: The views expressed here are those of the author expressed in their private capacity and do not necessarily represent the views of AZoM.com Limited T/A AZoNetwork the owner and operator of this website. This disclaimer forms part of the Terms and conditions of use of this website.