A new paper published in the journal Polymers has looked to nature for inspiration on the 3D printing of reinforced shapes that offer good compression strength and energy absorption capabilities.
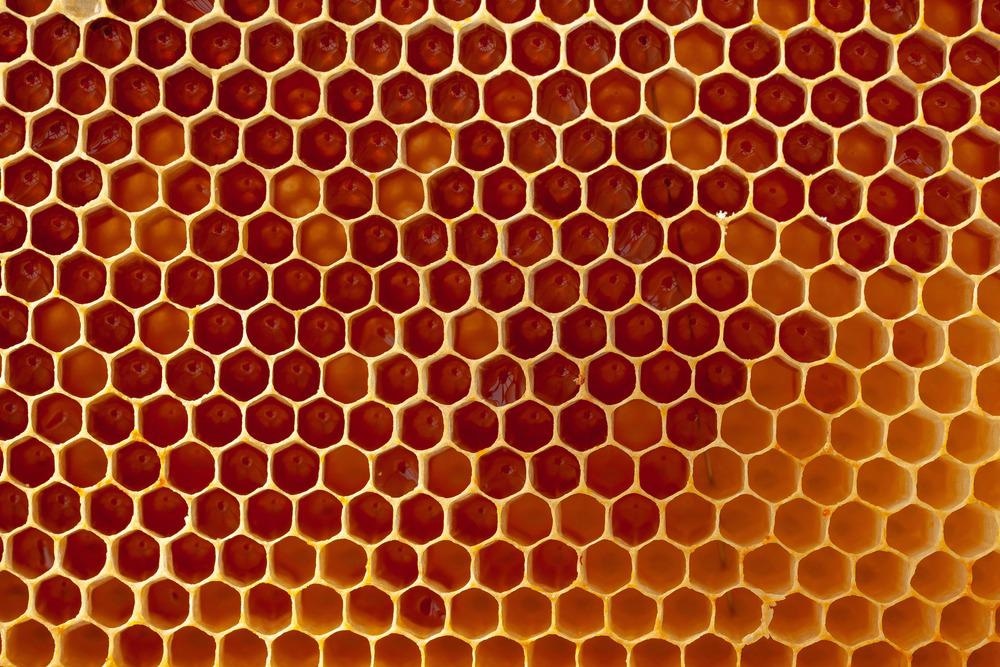
Study: Mechanical performance of honeycomb sandwich structures built by FDM printing technique. Image Credit: Matchou/Shutterstock.com
As one of the most frequently studied and fabricated bioinspired structures is the honeycomb; these structures are a popular choice for installation in the center of sandwich structures due to their ability to absorb impact.
Types of honeycomb structures are characterized according to their geometric shape; for example, hexagonal, tetrahedral, pyramidal, and pentagonal.
These structures see widespread use in applications where there is a need to maintain optimum strength and minimal weight; for example, the aerospace, automobile, railway, and satellite industries.
Illustration of honeycomb reinforced starfish structure. Image Credit: Saufi, S., Polymers
Different types of honeycomb structures also exhibit superior energy absorption when evaluated under compression loading; for example, hexagonal honeycombs offer improvements over their rectangular counterparts. The authors cite numerous studies which have compared these differences.
With this in mind, the authors looked to improve upon the commonly used honeycomb structures to improve their energy absorption and resistance to compression force.
Advances in additive manufacturing – and in particular 3D printing and fused deposition modeling (FDM) technology – have opened up new degrees of complexity in terms of products, shapes, and structures.
FDM fabricates structures layer by layer, and a wide range of materials are compatible with this process including polymers and composites.
Cell size and wall thickness are known to be the key factors in a structure’s ability to withstand load and pressure. It is also well known that adding a secondary structure inside of a honeycomb will increase compressive strength and the structure’s capacity for energy absorption.
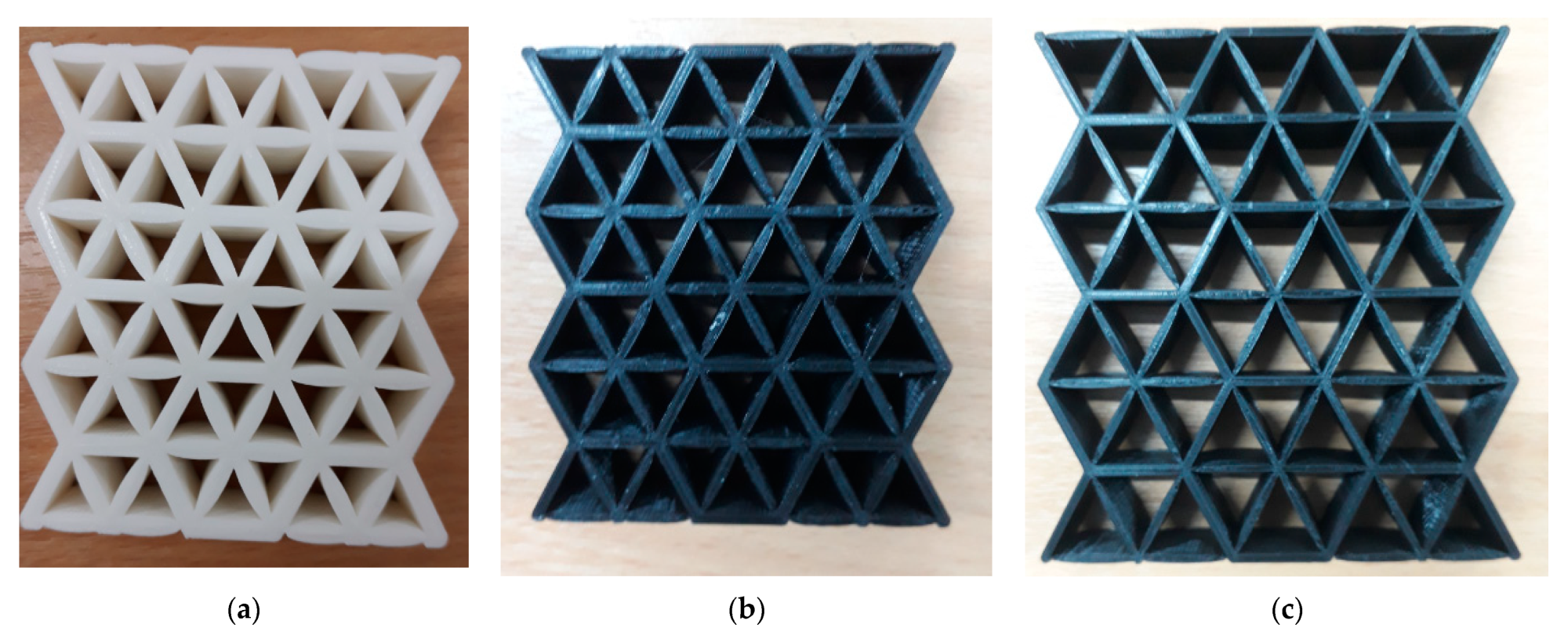
The final 3D printed specimens for (a) cell size 20 mm, thickness 2.5 mm, (b) cell size 25 mm, thickness 2 mm and (c) cell size 30 mm, thickness 1.5 mm. Image Credit: Saufi, S., Polymers
Because the honeycomb’s energy absorption capabilities are closely linked to its relative density, the authors posited that reinforcing a hexagonal honeycomb structure with starfish shape may yield a more robust and compression-resistant structure than the more commonly employed hexagonal honeycomb alone.
They used a 3D printing technique to generate a range of hexagonal honeycomb structures with starfish-shaped reinforcements, printing these with a range of cell wall thicknesses and cell sizes.
The structures were made from polylactic acid (PLA) and were designed using the Solidworks® software prior to conversion to standard tessellation language (STL) format for 3D printing.
As well as looking at the specific properties of the starfish-shaped reinforcement, the study also aimed to investigate the more general energy absorption capabilities of bioinspired structures, using a number of tools to evaluate their energy absorption, specific energy absorption, crushing force efficiency, and the impact of cell size and cell wall thickness on these metrics.
In order to calculate the structures’ capacity for energy absorption, results from compression tests were plotted in a load-displacement curve to determine a maximum peak value – essentially, the maximum load the structure can resist. The energy absorption value was calculated based on the area under the load-displacement curve.
The study revealed that a structure exhibited higher peak load capabilities as a result of larger cell size and cell wall thickness. Most notably, comparisons between wall thicknesses revealed a uniform pattern – increases in wall thickness increases led to increases peak load increases, irrespective of core size. The peak load was also found to decrease as cell size increases.
Interestingly, in terms of compression behavior, the smallest wall thickness exhibited improved performance over the larger wall thickness. It was actually noted that as wall thickness increased, efficiency decreased irrespective of cell size.

(a) Schematic of sample orientation during test. (b) Sample orientation during test. Image Credit: Saufi, S., Polymers
It was also determined that a higher crushing force efficiency value was generated from a smaller energy absorption value - as wall thickness increases, crushing force efficiency decreases, but energy absorption increases.
The authors proposed that these findings could be further explored, and structures further optimized by looking into means of improving the structural joint or node performance. It was also highlighted that the structures’ capabilities under dynamic loading conditions could prove to be a further avenue of investigation.
The development of these more robust reinforced honeycomb structures could be key to improving safety and crash resistance in a range of transport and other applications.
References
Gohar, S., Hussain, G., Ali, A., & Ahmad, H. 2021. Mechanical performance of honeycomb sandwich structures built by FDM printing technique. Journal of Thermoplastic Composite Materials. https://journals.sagepub.com/doi/10.1177/0892705721997892
Saufi, S. A.S.A., M. Y.M. Zuhri, M. L. Dezaki, S. M. Sapuan, R. A. Ilyas, A. As’arry, M. K.A. Ariffin, and M. Bodaghi 2021. "Compression Behaviour of Bio-Inspired Honeycomb Reinforced Starfish Shape Structures Using 3D Printing Technology" Polymers 13, no. 24: 4388. https://www.mdpi.com/2073-4360/13/24/4388
Disclaimer: The views expressed here are those of the author expressed in their private capacity and do not necessarily represent the views of AZoM.com Limited T/A AZoNetwork the owner and operator of this website. This disclaimer forms part of the Terms and conditions of use of this website.