Published in the journal Carbon, researchers have investigated the spatial distribution of CNTs with different length scales during ball milling, sintering, and hot extrusion.
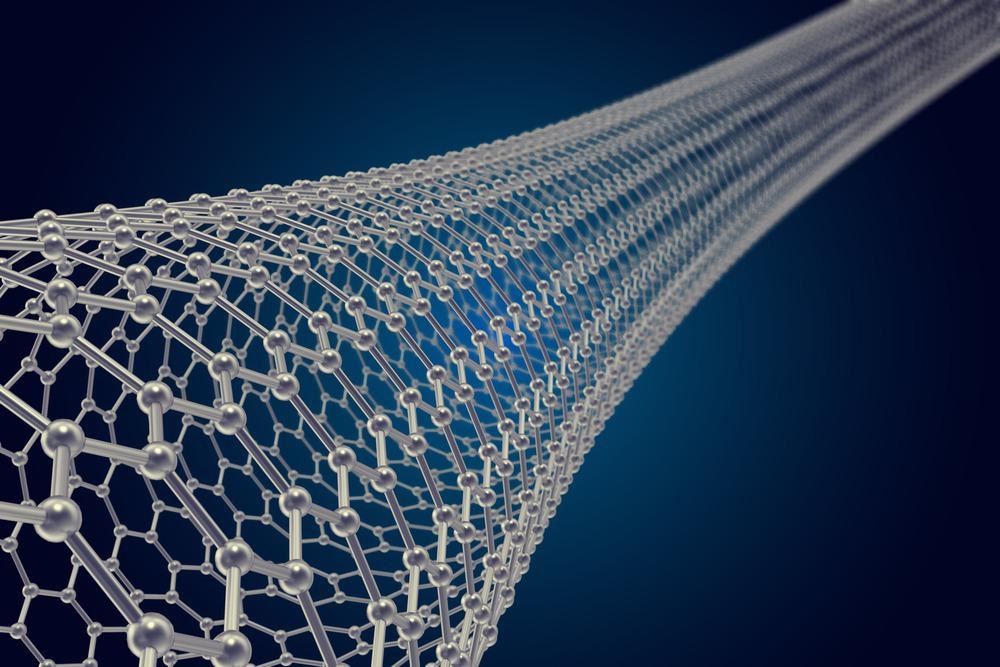
Study: Effect of thermomechanical treatment and length-scales on spatial distribution of CNTs in Al matrix. Image Credit: Rost9/Shutterstock.com
CNTs, or carbon nanotubes, are tubes of carbon with diameters measured in nanometers. Single-wall carbon nanotubes are one of the allotropes of carbon, intermediate between fullerene cages and flat graphene, which are considered excellent reinforcements for aluminum matrix composites (AMCs).
Due to the increasing demand for stiff and strong structural materials in the transportation industries including aerospace and automobile, bolstering CNT/Al composites and AMCs would be a good strategy to meet such demand. Typically, precipitation hardening is considered to be an effective strengthening strategy but is still limited in terms of stiffness.
Now a team of researchers at the School of Material Science and Engineering, Shanghai Jiao Tong University, have found the conditions that could improve both the strength and the modulus (stiffness) of materials.
CNT/Al Composites
Improving both the strength and stiffness of CNT/Al composites would offer the automobile and aerospace industries a boost in building stronger lighter vehicles and machinery, which are crucial factors in today’s market.
Thus, CNT/Al composites are considered to be novel attractive conductive materials due to their lightweight in combination with potential high strength and high conductivity. Methods for adding CNTs into aluminum include ball milling, sintering, and hot extrusion, however, these methods are not able to distribute the CNTs evenly, which results in a material with a lower mechanical strength than expected.
CNTs typically build up at grain boundaries and this is usually aggravated by the ball milling and sintering processes. The team discovered that the hot extrusion thermomechanical process allowed CNTs to enter the grains which consequently increases mechanical strength and stiffness.
Inspired by the precipitates in the alloy, changing intergranular CNTs to intragranular CNTs can not only effectively increase the elastic modulus, but also effectively increase the strength through the Orowan mechanism and maintain a considerable elongation by improving the work hardening rate
Genlian Fan, Corresponding Author, School of Material Science and Engineering, Shanghai Jiao Tong University
Until now, the factors and mechanisms that influence the intragranular distribution of CNTs in Al matrix composites (AMCs) have not been well-documented and the team set out to reveal the effect of length-scale in long and short CNTs.
Throughout the work, the team used scanning transmission electron microscopy to document and characterize how spatial distribution evolved after CNT/Al composite had gone through the fabrication processes.
Long vs. Short CNTs
From their results, the team was able to assess the effects of external stresses on the CNT distribution which in turn revealed the critical length of CNTs that could enter the grains and thereby yield a stronger material.
The team discovered that the intragranular distribution of CNTs could not be accomplished by ball milling or sintering processes alone – even with short CNTs. The mechanism of intragranular CNT distribution is related to the thermomechanical process of hot extrusion.
Furthermore, the team compared long and short CNTs for optimal intragranular distribution and discovered that the critical length of CNTs for entering grain interiors is ~103 nm, with the optimal length ~95 nm.
The CNTs that exceeded the critical length could not enter the grains and instead congregated around grain boundaries which results in intergranular dispersion. Thus, the key conditions for satisfying intergranular dispersion are grain size (length-scale of CNTS) and applied stress with thermomechanical activation.
Based on the research, the team is able to further understand the strengthening mechanisms which could lead to the development of advanced CNT-reinforced Al and other metal composites for critical engineering applications in a range of industries, including automobile and aerospace.
Reference
Q. Liu, G. Fan, Z. Tan, F. Saba, Q. Guo, D. Xiong, Y. Su, Z. Li, D. Zhang, Effect of thermomechanical treatment and length-scales on spatial distribution of CNTs in Al matrix, Carbon (2022), https://www.sciencedirect.com/science/article/pii/S0008622322000240?via%3Dihub
Disclaimer: The views expressed here are those of the author expressed in their private capacity and do not necessarily represent the views of AZoM.com Limited T/A AZoNetwork the owner and operator of this website. This disclaimer forms part of the Terms and conditions of use of this website.