In a recent study published in the journal Materials, researchers from China developed a permeable brick by utilizing industrial solid waste.
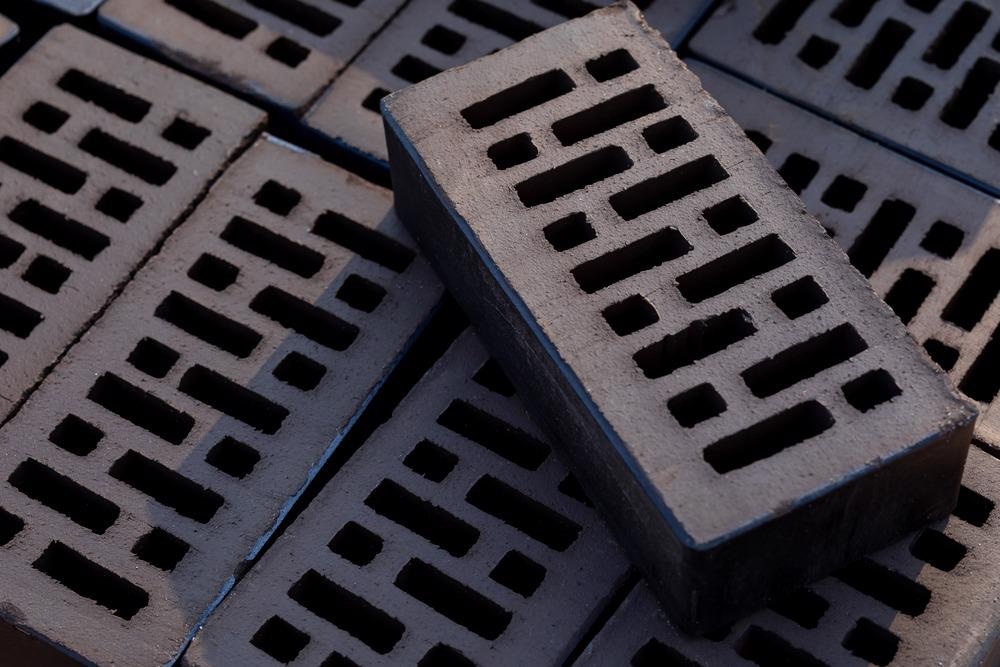
Study: Microstructure Evolution and Improved Permeability of Ceramic Waste‐Based Bricks. Image Credit: LariBat/Shutterstock.com
Solid Waste-Based Permeable Bricks
In recent times, substantial amounts of minerals and fossil resources are used to support rapid industrialization. Due to this, industrial solid waste (ISW) is accumulating at an extremely high rate, causing severe air and water pollution and unexpected environmental risks. As a result, ISW must be managed cost-effectively and energy-efficiently via recycling.
In the current study, all new solid waste-based permeable bricks were made from waste ceramic coal gangue and magnesium slag using pressing and sintering. The primary objective of this work was to prepare new permeable bricks and achieve extensive resource utilization of ceramic waste (CW) materials, coal gangue (CG), and magnesium slag (MS).
Additionally, the researchers attempted to prepare permeable bricks that will satisfy national standards and provide a new option for pavement material selection for large-scale engineering solid waste applications.
The preparation process of permeable bricks. Image Credit: Zhou, W et al., Materials
Methodology
The primary materials used in the study were CG, MS, and CW. Initially, CG and MS went through the dewatering process and then they were ground and crushed into powders using ball milling equipment. CW was ground and crushed into a specific distribution using standard sieving apparatus to function as fine and coarse aggregates in permeable bricks, and MS and CG were used to produce the mixing binder.
Following that, deionized water, CW, and the mixing binder were blended into a mixture and left to sit for 24 hours to develop into a brick mixture. A uniaxial hydraulic sampling machine pressed the brick mixture into cylinder bodies, and then the samples were heated in an oven. Further, the samples were sintered at temperatures of 1125 °C, 1175 °C, 1150 °C, 1200 °C, and 1225 °C in an electrical furnace at a heating rate of 5 °C/min in an air atmosphere for 1 hour and cooled to room temperature to produce final specimens.
Elemental sample analysis was performed using an X-ray fluorescence analyzer, and the mineralogical compositions of prepared bricks were examined using an X-ray diffraction (XRD) analyzer. The microstructure of the permeable bricks was examined using a scanning electron microscope (SEM).
The permeability coefficient was evaluated using Chinese engineering standard GB/T 25993‐2010, and the apparent porosity was measured by applying the Archimedes principle. The final test results were taken as an average of three measurement values.
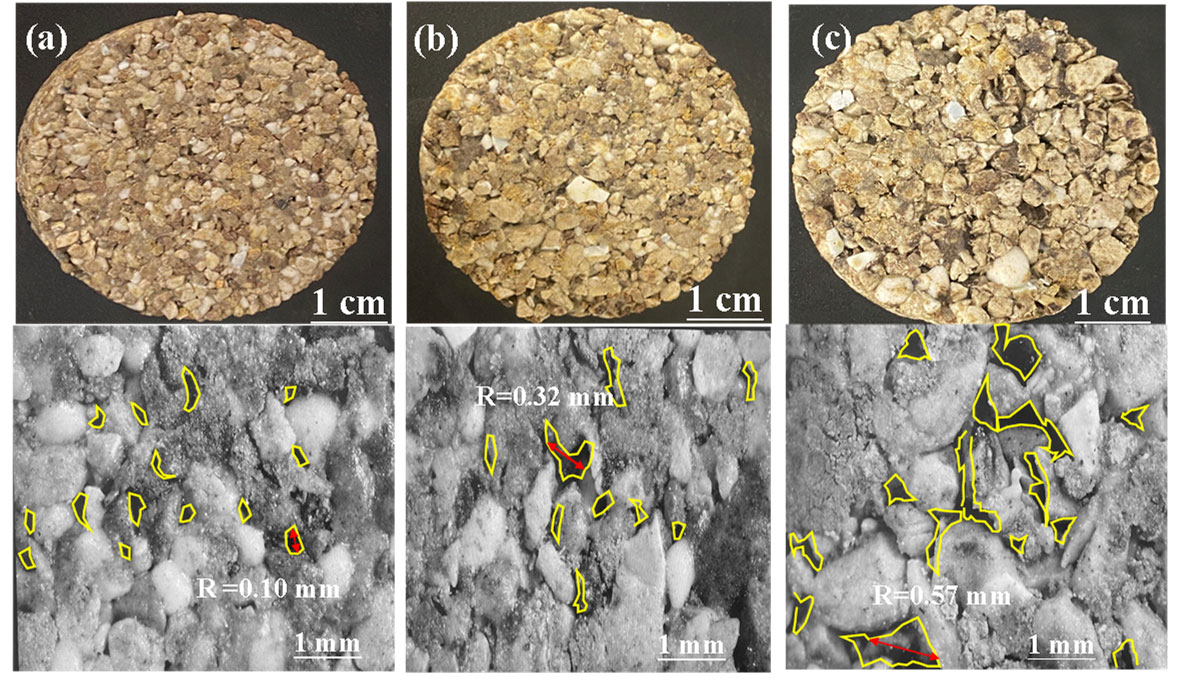
Optical images of the sample at 1200 °C with different content of coarse aggregate: (a) 0%; (b) 50%; and (c) 100% c. Image Credit: Zhou, W et al., Materials
Results
The chemical composition test demonstrated that the CG contains a weighted composition of 61.39% SiO2, 23.76% Al2O3, and 4.14% Fe2O3, and the MS contained CaO and Al2O3. The mixture of MS and CG contained SiO2, Al2O3, and CaO and was used as a mixing binder.
The XRD results of the raw materials demonstrated that the CG primary consisted of quartz and kaolinite phases. The mineral phase of MS was made of dmisteinbergite and wollastonite phases, and the spectra of CW demonstrated the presence of mullite and quartz phases.
SEM analysis revealed that samples with different aggregate gradations have entirely different internal structures, and different gradations of CW were visible on the surfaces of permeable bricks. The brick sample's skeleton structure was unstable due to the high content of coarse aggregates, which resulted in high permeability and low mechanical strength.
Additionally, the average size of pores rapidly increased as the content of coarse aggregates increased, resulting in an increment in the average size of the primary pores to over 200 µm, whereas sub-pores below 200 µm were observed in fine aggregates.
The energy-dispersive X-ray spectroscopy results showed that the content of Si and Al increased gradually in the samples, while the content of O increased in the opposite direction as the sintering temperatures increased, and the samples also contained Fe, Mg, and Na elements.
The study of the effect of sintering temperature revealed that sample properties improved significantly at temperatures above 1150 °C, and the permeability coefficient reached its maximum at 1225 °C. However, with sintering temperatures above 1200 °C, the compressive strength rapidly decreased.
The linear model discussed by the researchers revealed that permeability and compressive strength have a strong relationship with apparent porosity and the consistency of the developed samples.
The study of the impact of mixing binder composition on brick properties proved that the optimum results were observed at 60% coarse aggregate, 20% fine aggregate, and 20% mixing binders sintered at 1200 °C for 1 hour. Additionally, at a 12% CG ratio, the maximum compressive strength of 56.04 MPa was observed due to mixing the binder with 10% CG, which added appropriate amounts of Cao, SiO2, and Al2O3.
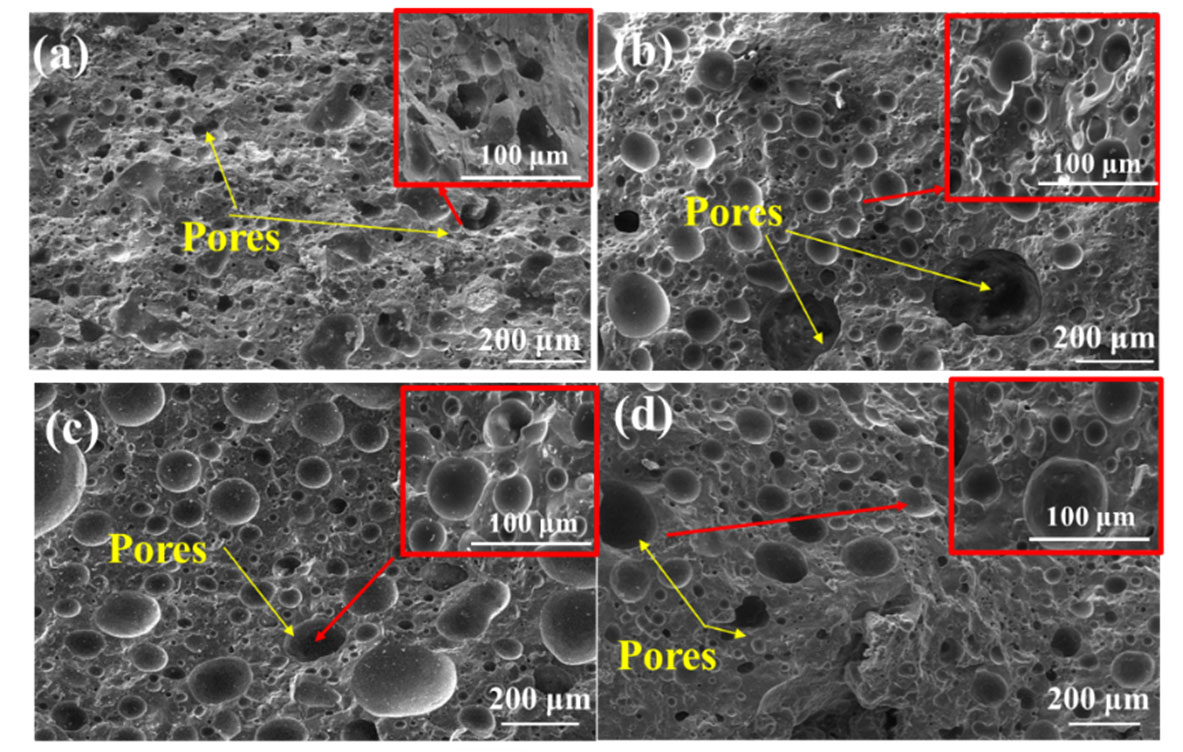
SEM morphologies of samples sintered at 1200 °C with different CG contents: (a) 0%; (b) 8%; (c)12%; and (d) 20%. Image Credit: Zhou, W et al., Materials
Conclusion
The current study demonstrated the use of magnesium slag and coal gangue in producing permeable bricks. The study findings illustrated that large-scale and resource-based usage of magnesium slag and coal gangue solid waste could contribute to environmental protection. However, more extensive research is needed before the as-produced sample bricks can be used extensively in real-world engineering applications.
Disclaimer: The views expressed here are those of the author expressed in their private capacity and do not necessarily represent the views of AZoM.com Limited T/A AZoNetwork the owner and operator of this website. This disclaimer forms part of the Terms and conditions of use of this website.
Source:
Zhou, W.; Du, H.; Kang, L.; Du, X.; Shi, Y.; Qiang, X.; Li, H.; Zhao, J. Microstructure Evolution and Improved Permeability of Ceramic Waste‐Based Bricks. Materials 2022, 15, 1130. https://www.mdpi.com/1996-1944/15/3/1130