By Surbhi JainReviewed by Susha Cheriyedath, M.Sc.Feb 8 2022
In a study published in the book Iron Ore, researchers examined and evaluated the recent developments in the use of biomass in various steel and iron-making processes, as well as their potential to reduce fossil CO2 emissions, from a technical standpoint.
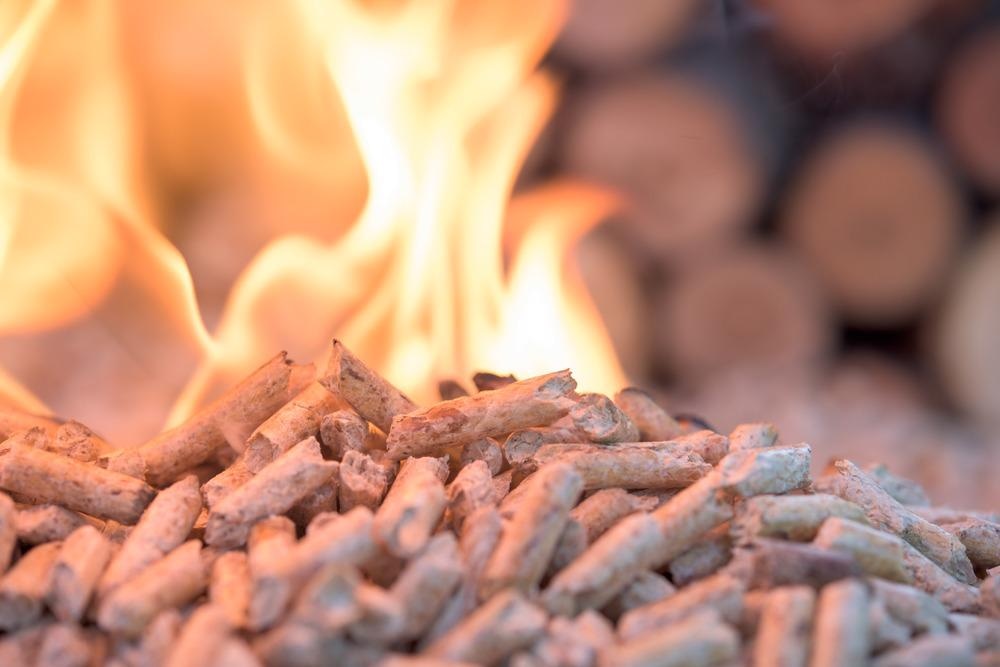
Study: Utilization of biomass as an alternative fuel in iron and steel making. Woodhead Publishing Series in Metals and Surface Engineering. Image Credit: tchara/Shutterstock.com
Background
The iron and steel industries are significant sectors that have a direct impact on society, economic growth, stability, and national security. Fossil fuels are the primary reducing agents and source of heat in the production of iron and steel, and thus a significant contributor to worldwide anthropogenic CO2 emissions.
Due to the rapid rise in energy prices as well as government commitments to reduce CO2 emissions, the reduction of gas emissions and the specific energy consumption are major priorities of iron and steel production. Iron-making processes have recently undergone significant adjustments and improvements in order to minimize energy consumption and CO2 emissions.
Modifications and reductions in energy consumption have been compensated for by increased total production, resulting in a continuous substantial increase in CO2 emissions.
In order to reduce CO2 emissions in the iron and steel sector, more focus has recently been dedicated to utilizing renewable biomass as a reducing source as well as a source of heating rather than fossil fuels. Partially substituting renewable biomass products and thermally treated biomass in place of fossil fuels in iron and steel-making processes is one of the few choices that may be implemented in the short and medium-term, both from an economical and technical point of view. However, several technical and economic hurdles are still faced in the utilization of biomass in the steel and iron industries.
About the Study
In this book, researchers investigated in depth the use of biomass in iron and steel production through an extensive literature survey. Biomass application strategies were discussed for reducing CO2 emissions.
The utility of biomass products in the integrated steel plant was examined based on their applications in (1) bio-coke making via blending of biomass with coking coal; (2) sintering to make bio-sinter; (3) pelletizing/briquetting to make bio-composites and/or bio-briquettes; (4) partial replacement of coke, nut coke, or pulverized coal in the blast furnace; and (5) bio-recarburization of steel in the ladle furnace.
Subsequently, recent studies and investigations into biomass utilization in steel and iron-making, as well as its impact on process performance and product quality, were presented and addressed. The practicality of using bio-agglomerates such as bio-sinter, bio-coke, and bio-briquettes to replace typical top charging agglomerates was also examined. Additionally, the possibility of replacing pulverized coal with biomass materials in the production of iron and steel was discussed.
Observations
In this study, researchers observed that biomass addition to coal blends was limited to 5 wt. to 10 wt. %. This was attributed to the fact that adding biomass to a coal blend affects the coke's quality by lowering its strength and increasing its reactivity. According to many studies, particle size, density, and volatile content were important parameters to be considered when introducing biomass to a coal blend.
More from AZoM: Differential Thermal Analysis of Technical Ceramics
Some studies showed that the major fuel utilized in the sintering process was coke breeze, which accounted for 10% of the total CO2 emissions in the integrated steel factories. The researchers also observed potential of pyrolyzed charcoal to partially replace coke breeze in the sintering procedure with lower SOx and NOx emissions. The replacement ratio was found to be enhanced by increasing the size, density, and reactivity of biochar particles.
The team also noted the introduction of biomass into the blast furnace was shown through the briquetting method as well as through tuyeres. It was also observed that injection of biomass products into the blast furnace minimized the consumption of coal/coke and reduced CO2 emissions. Porous structure, low ash content, low sulfur content, and high hydrogen concentration were some of the benefits of biomass.
Further, it was also shown that the use of biomass instead of fossil carbon in steel production resulted in a decrease of 10–12% of CO2 emissions from the steel industries. Studies on the replacement of injected fossils with neutral carbon carrying materials revealed that biomass was a viable alternative due to its low sulfur and phosphorus content.
Conclusions
In this book, the researchers discussed the primary applications for biomass in iron and steel production. Overall, this review concluded that decisive efforts and innovative approaches are required to reduce reliance on fossil carbon and thus safeguard the steel industry's long-term viability.
The authors believe that one of the few possibilities that can be implemented in the short- to medium term is the replacement of fossil carbon with renewable and neutral carbon (biomass).
Disclaimer: The views expressed here are those of the author expressed in their private capacity and do not necessarily represent the views of AZoM.com Limited T/A AZoNetwork the owner and operator of this website. This disclaimer forms part of the Terms and conditions of use of this website.
Source:
Mousa, E., Ahmed, H., Chapter 20 - Utilization of biomass as an alternative fuel in iron and steel making. Woodhead Publishing Series in Metals and Surface Engineering, Iron Ore (Second Edition), Woodhead Publishing 665-690 (2022). https://www.sciencedirect.com/science/article/pii/B9780128202265000203