An MIT team has engineered a primarily plant-based composite material using CNCs which make up between 60%-90% of the material. If scalable, the material could present an opportunity to fabricate more sustainable natural polymers. The full details of the research are published in the journal Cellulose.
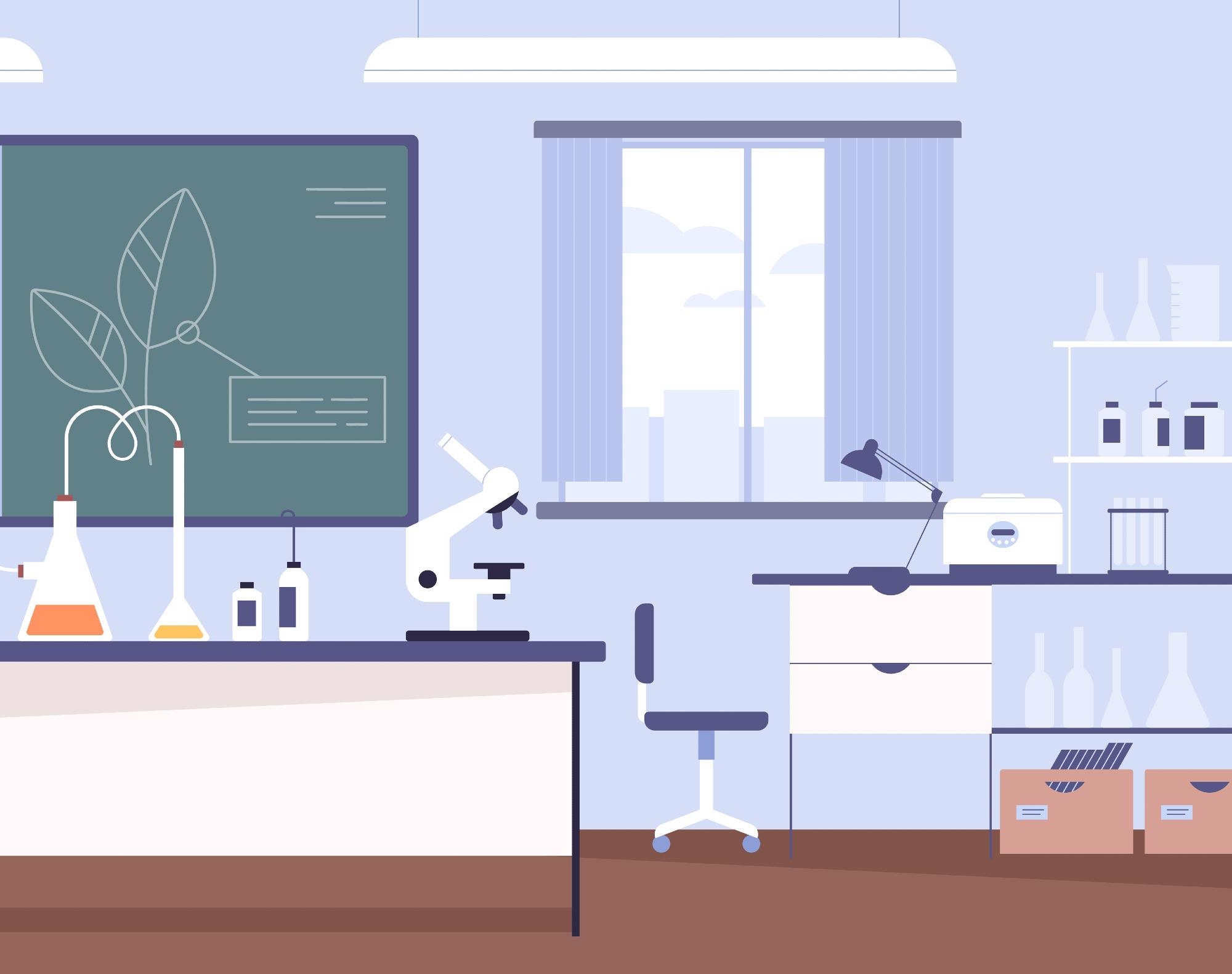
Study: Printable, castable, nanocrystalline cellulose-epoxy composites exhibiting hierarchical nacre-like toughening. Image Credit: GoodStudio/Shutterstock.com
Cellulose is an essential structural component found within the primary cell wall of most green plants, types of algae, and even in some species of bacteria. This makes it nature’s most abundant polymer, and it is typically used to produce paper deriving from wood pulp and cotton sources.
Now, a group of researchers at MIT have managed to unlock the unique properties of cellulose nanocrystals (CNCs), chains of self-organized organic polymers arranged in crystal patterns. CNCs are found within cellulose fibers and at the nanoscale demonstrate exceptional hardness and stiffness even outperforming Kevlar and matching aluminum.
Tougher Than Bone and Harder Than Metal
When engineering the new CNC-based composite, the MIT team discovered that the material was tougher than bone and harder than some metals including aluminum alloys. The structural make-up of the material closely resembles ‘nacre’, also known as mother-of-pearl, which is an organic-inorganic composite found on the inner-shell layer of some mollusks.
Like nacre, the microstructure of the cellulose composite takes up a brick-and-mortar lamellar structure: “Mineral-based nanocomposites such as nacre, enamel, and bone achieve high strength and toughness via optimized microstructures that enable hierarchical damage resistance,” explains co-author Professor A. John Hart.
Furthermore, the team also demonstrated the ability to fabricate the CNC-based material through additive manufacturing (3D Printing) and traditional casting methods. They were able to print and cast the material into small lens-type films for testing.
The stiffness, hardness, and fracture toughness of the CNC composites exceed those of many engineering polymers
Professor A. John Hart, Co-Author, MIT
If the team could produce significant amounts of the material, then the plant-based composites would arguably be a better prospect for the environment considering the impact synthetic plastics have on the planet.
Reconstructing Nature’s Abundance
Due to the natural abundance of cellulose, researchers have been exploring various potential uses for cellulose nanocrystals which are easily extracted via way of acid hydrolysis. However, the amounts they have been able to extract haven’t matched the amount incorporated into previous composites.
The issues holding back development included the tendency for CNC crystals to form aggregate clumps when bonding with synthetic polymer molecules which produced weak, poor performing materials. However, the MIT team decided to increase the amount of CNCs in their composite, which could be shaped into durable forms with high strength and hardness.
Once they had developed a suitable ratio of CNC and synthetic polymer, the team was able to produce a composite that could be poured into a cast or fed through a 3D printer nozzle. This deconstruction and subsequent reconstruction of the cellulose materials is a novel application of plant-based materials.
For any clumps that formed in the gel, the team applied a probe sonicator to disperse the CNCs across the material for optimal bonding with the synthetic material: “The process of dispersion of CNCs in the gel is critical to avoid precipitation of large aggregates of CNCs and phase separation,” explains Hart.
Improving the Curing Process
Once the materials had been either printed or cast, they were left to cure and dry forming the solid, hard composites that demonstrated the excellent resistance properties similar to nacre. The hardness and stiffness properties of the material make it unique in the sense it could be formed in the same way as many plastics while demonstrating the performance of metal alloys.
“The addition of significant fractions of CNCs to petroleum-based polymers can potentially improve the mechanical properties and reduce the environmental impact of these ubiquitous materials,” Hart said.
One of the things the researchers noticed during the curing process of the plant-based composite material was that it had the tendency to shrink. While this is not a major issue on a small scale, it could present issues for fabricating larger objects and shapes as it could cause them to split or crack when curing.
Therefore, while the material does present an exciting opportunity to one day potentially replace plastics on a larger scale, the researchers will need to first find ways to improve the curing process of the CNC-based composite to avoid shrinkage issues and make the material scalable.
References
Rao, A., Divoux, T., Owens, C.E. et al. Printable, castable, nanocrystalline cellulose-epoxy composites exhibiting hierarchical nacre-like toughening. Cellulose (2022). https://link.springer.com/article/10.1007/s10570-021-04384-7
Disclaimer: The views expressed here are those of the author expressed in their private capacity and do not necessarily represent the views of AZoM.com Limited T/A AZoNetwork the owner and operator of this website. This disclaimer forms part of the Terms and conditions of use of this website.