By Surbhi JainReviewed by Susha Cheriyedath, M.Sc.Mar 14 2022
In an article recently published in the open-access journal Polymers, researchers investigated the rheological characteristics of hydroxypropyl cellulose–derived filaments. They also discussed their potential utility in material extrusion 3D printing.
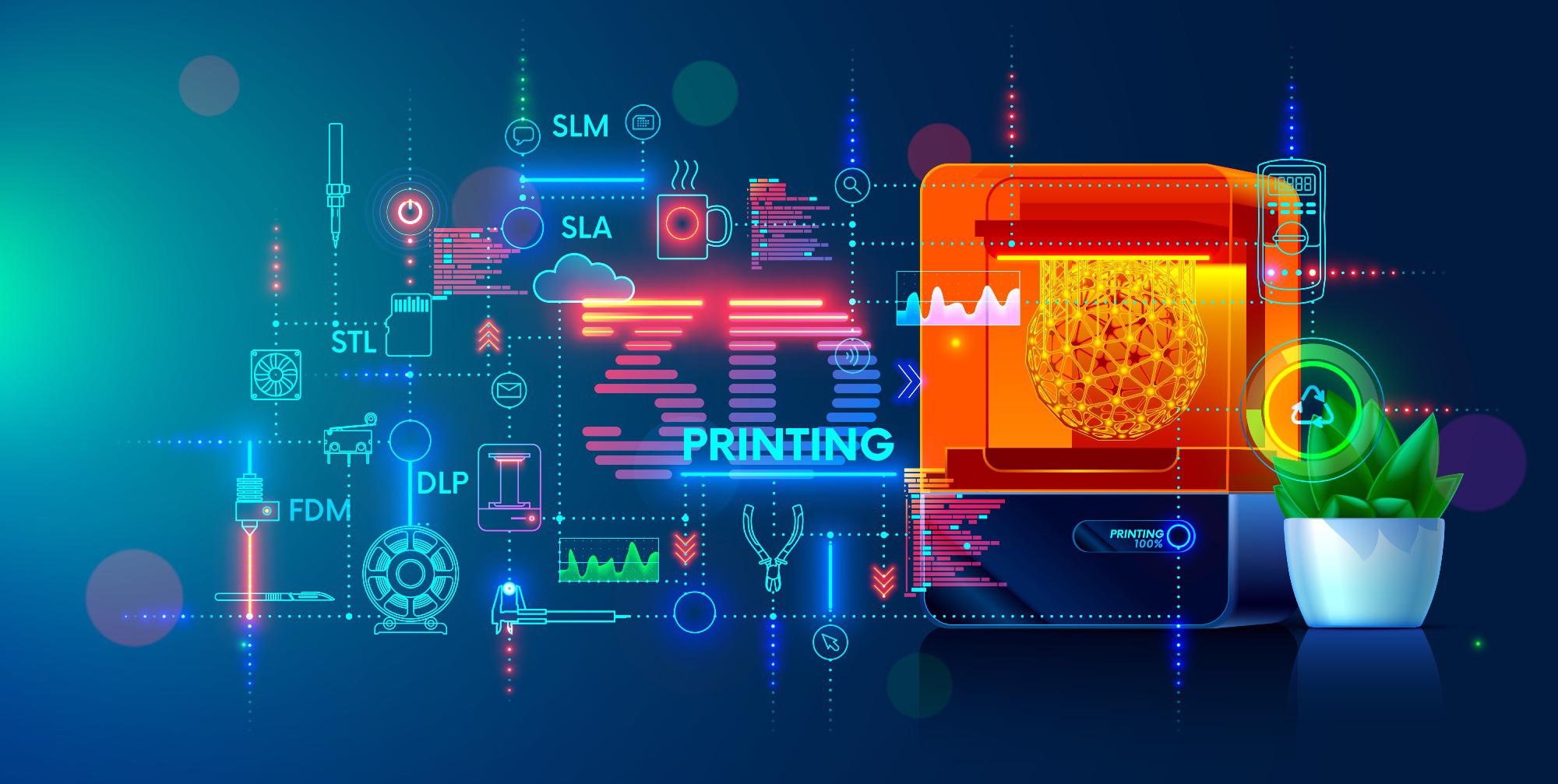
Study: Rheological Investigation of Hydroxypropyl Cellulose–Based Filaments for Material Extrusion 3D Printing. Image Credit: Andrey Suslov/Shutterstock.com
Background
Fused deposition modeling (FDM), also known as material-extrusion three-dimensional (3D) printing, has been widely employed to create a variety of drug-delivery devices. Because of their inherent qualities, polymers now have a variety of commercial applications.
In the pharmaceutical industry, a variety of polymer mixes, pharmaceutical excipients, and drug content have been melt-extruded to improve the printability and drug-release profile of polymer composites. To develop diverse solid compositions and improve medication bioavailability, hot-melt extrusion (HME) uses extensive mixing and a high temperature.
Melt processing of highly viscous dispersions or highly concentrated pharmaceuticals faces many obstacles. For research and clinical manufacturing, an extrusion printer that follows good manufacturing procedures was recently created.
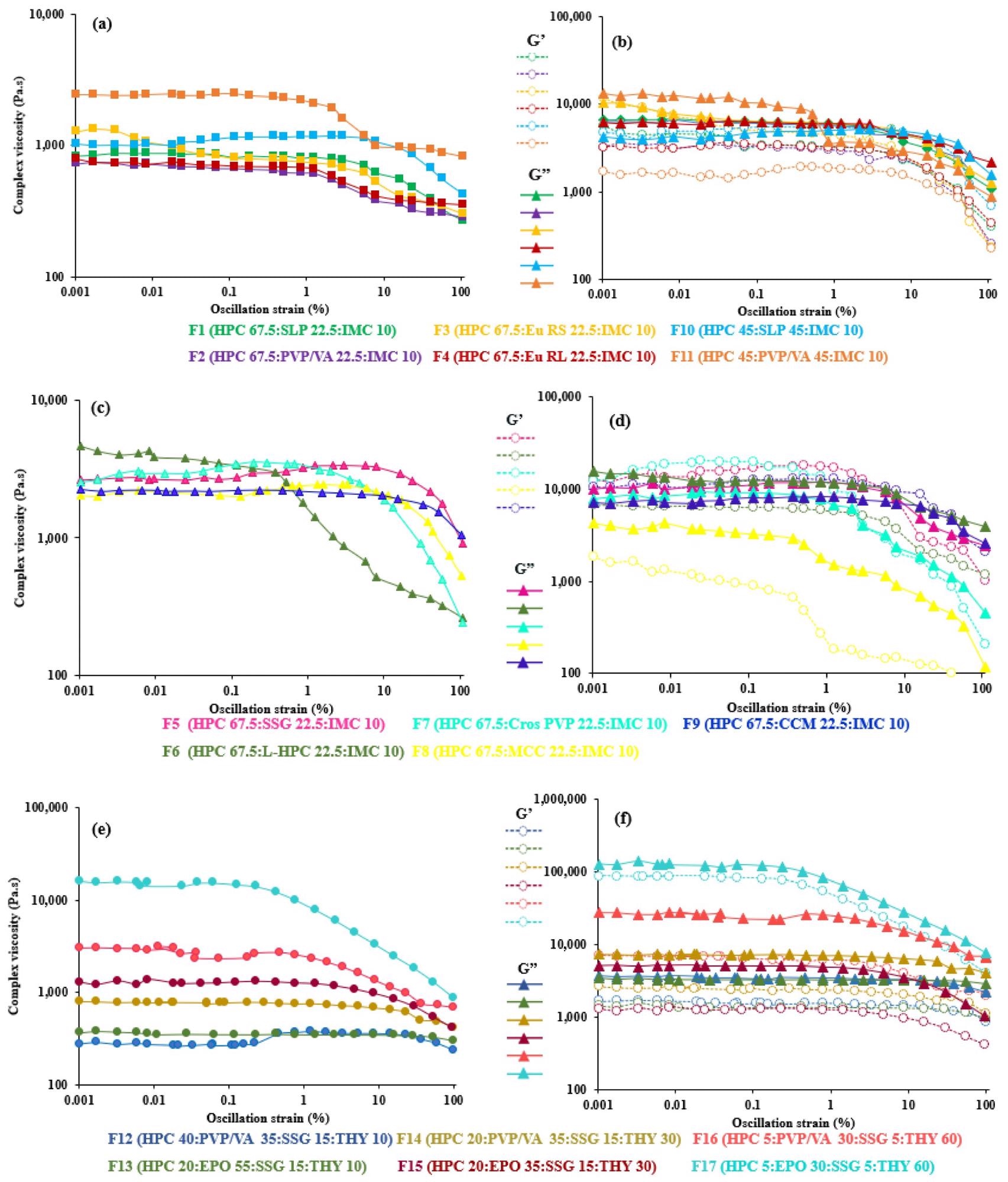
Effect of strain on complex viscosity (left) and storage (G’) and loss (G”) moduli as function strain (right) of (a,b) 67.5–45% HPC:polymer mixtures, (c,d) 67.5% HPC:disintegrant mixtures and (e,f) 40–5% HPC: polymer mixtures at 200 °C. Image Credit: Than, Y. M., et al. Polymers
To screen printable formulations and analyze the viability of polymer mixes for the printing of specialized delivery systems, dose control, drug-release characteristics, enhanced medication access, and personalized medicines, an efficient approach is required. Rheology is a versatile tool that may be used to characterize materials such as polymer crystallization, mechanical characteristics, stability, and degradation.
Nonetheless, the influence of filament rheological qualities on printability is unknown and underappreciated. The rheological properties of the polymer melt are crucial in defining the best extrusion settings and the properties of the extruded object. The rheological features of polymeric systems for material extrusion 3D printing have received little attention. Furthermore, hydroxypropyl cellulose-containing polymer composites have a significant potential for fabricating 3D-printed medications.
About the Study
In the present study, the authors presented the rheological properties of formulations of successfully printed tablets for both immediate and controlled release. Hydroxypropyl cellulose was combined with various medications (indomethacin or theophylline), polymers, and disintegrants in various ratios to produce printable filaments. Larger processing viscosity windows were discovered.
The rheological features such as shear-thinning behavior, viscosity, and viscoelastic properties of 17 hydroxypropyl cellulose-based compositions were tested that were effectively printed as instant and controlled release delivery systems.
At different ratios, additional polymers and/or disintegrants (e.g., microcrystalline cellulose, sodium starch glycolate, low substituted hydroxypropyl cellulose, crospovidone, or croscarmellose sodium) were added to the feedstock filament. Indomethacin and theophylline were utilized as model medicines.
The viscosity, shear-thinning behavior, and viscoelastic properties of printed filaments were investigated as a function of frequency and temperature. The samples' complex viscosity, loss modulus (G"), storage modulus (G'), and crossover point were also examined.
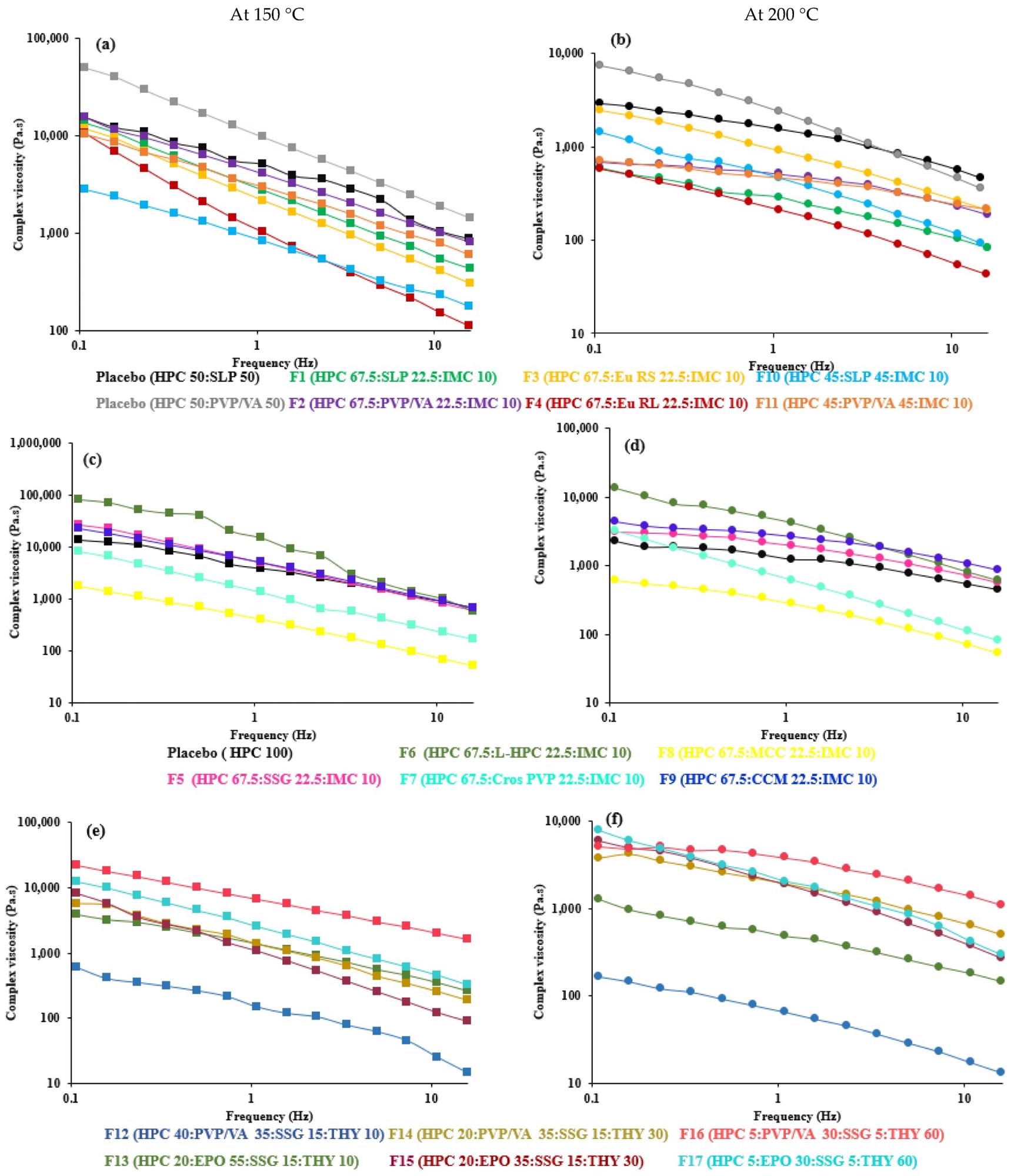
Effect of angular frequency (0.1 to 15 Hz) on complex viscosity of 67.5–45% HPC:polymer mixtures (a,b), 67.5% HPC:disintegrant mixtures (c,d) and 40–5% HPC:polymer mixtures (e,f) at 150 °C (left) and 200 °C (right). Image Credit: Than, Y. M., et al. Polymers
Observations
The drug load, polymer composite, disintegrant type, temperature, and shear rate all had an impact on the complicated viscosity, shear-thinning behavior, and viscoelastic characteristics. The printable mixes' viscosity was in the 10–1000 Pa.s range at 100 rad/s rotational frequency.
With a broad slope of complex viscosity from -0.28 to -0.74, all formulations displayed shear thinning behavior. The presence of 30–60% medication or disintegrant resulted in higher viscosity readings. Microcrystalline cellulose, on the other hand, was discovered to be an alternate addition for lowering the storage and loss modulus of disintegrants.
With a rise in temperature, all-polymer composites showed a drop in complex viscosity. Increasing the temperature by 50°C from 150 to 200°C over the angular frequency resulted in a one-order-of-magnitude decline in viscosity. The slopes of the graphs demonstrated the impact of the shear rate on viscosity.
The shear rate had a greater impact on the viscosity than the temperature. The results showed that the processing viscosity windows were in the range from 10 to 1000 Pa.s at an elevated frequency. No discernible difference was found in viscosity or shear-thinning between the controlled and immediate release systems.
Solid fillers like those containing a lot of medication or disintegrants had an impact on the shear thinning, viscosity, and viscoelastic profiles, which resulted in intrinsic and unique values for each formulation.
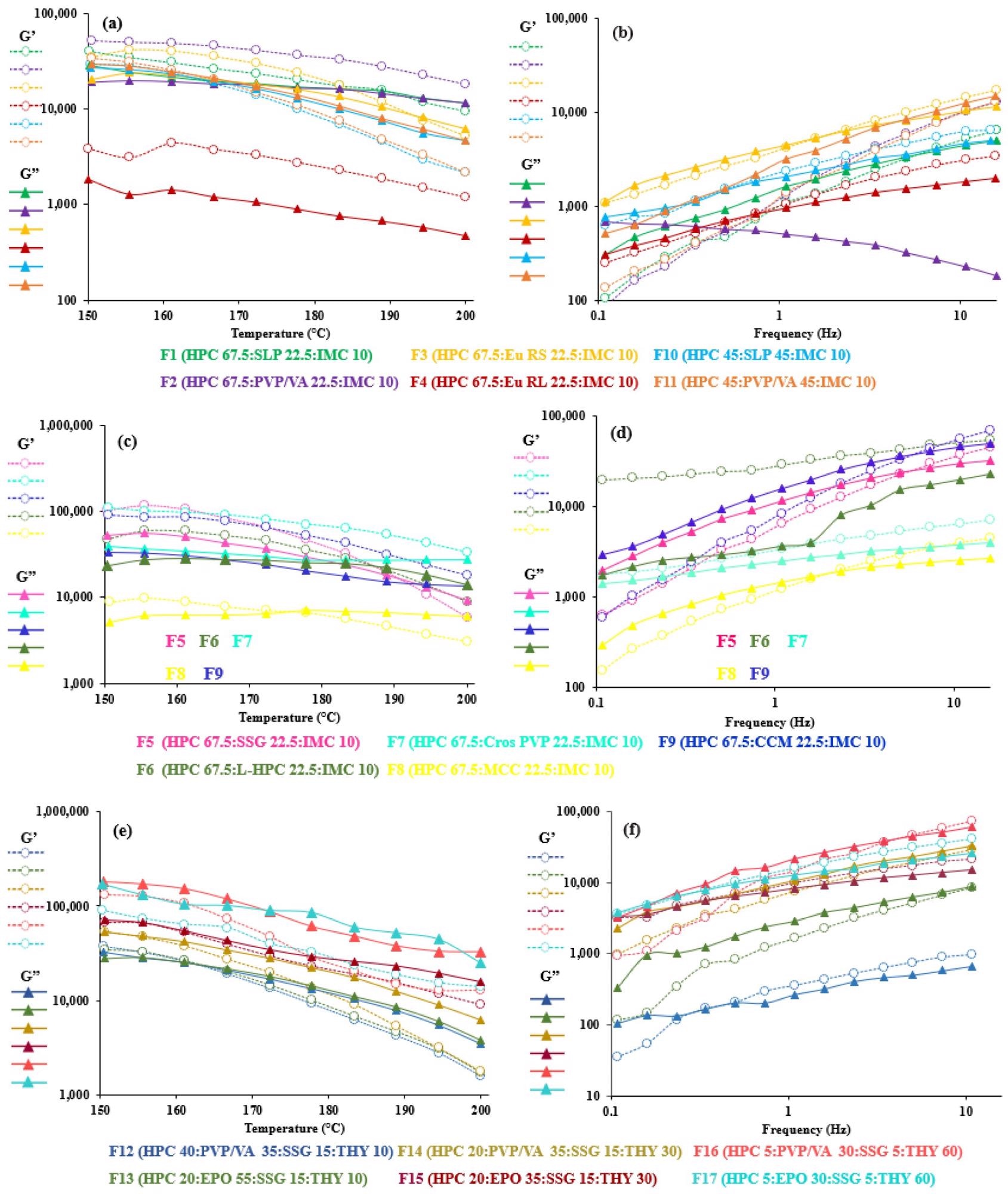
Viscoelastic properties (storage modulus (G’) and loss modulus (G’’)) of 67.5–45% HPC: polymer mixtures (a,b), 67.5% HPC:disintegrant mixtures (c,d) and 40–5% HPC:polymer mixtures (e,f) upon increasing temperatures at 1 Hz (left) and at 200 °C (right). Image Credit: Than, Y. M., et al. Polymers
Conclusions
In conclusion, this study investigated the complex viscosity and viscoelastic parameters of the 17 compositions for successfully printed immediate- and controlled-release tablets by using a rheometer. Hydroxypropyl cellulose-L (HPC) was utilized in various ratios to make printable filaments, whereas microcrystalline cellulose (MCC) was used as an alternate additive to minimize the disintegrants' storage and loss moduli. High drug loading in filaments with 60% THY slowed the solidification of the composites, which resulted in 1.4 and 2.0 values of tan δ.
The authors emphasized that preformulation and subsequent development of material-extrusion 3D-printing medicines will benefit from this rheological data. They also believe that the findings of this study can be used to generate further FDM-printed therapeutic items.
Disclaimer: The views expressed here are those of the author expressed in their private capacity and do not necessarily represent the views of AZoM.com Limited T/A AZoNetwork the owner and operator of this website. This disclaimer forms part of the Terms and conditions of use of this website.
Source:
Than, Y. M., Suriyarak, S., Titapiwatanakun, V., Rheological Investigation of Hydroxypropyl Cellulose–Based Filaments for Material Extrusion 3D Printing. Polymers 14(6), 1108 (2022). https://www.mdpi.com/2073-4360/14/6/1108