New research has been published with the aim of evaluating the processing and refinement characteristics of carbon black and graphene nanoplatelets within a matrix of nitrile butadiene rubber. Researchers from the University of Bradford, University of Manchester, and the University of London have contributed to the paper, which has been published online in the journal Polymers.

Study: Graphene Nanoplatelets as a Replacement for Carbon Black in Rubber Compounds. Image Credit: sangriana/Shutterstock.com
Using Carbon Black in Chemically resistant Rubber
In the gas and oil industry, there is a need for high-performance, durable, and chemically resistant elastomer seals that can be easily fitted. Seals must possess excellent performance in extreme conditions. Amongst the materials proposed as reinforcement fillers for nitrile butadiene rubber, a commonly used material for this application, carbon black, has been widely investigated by researchers.
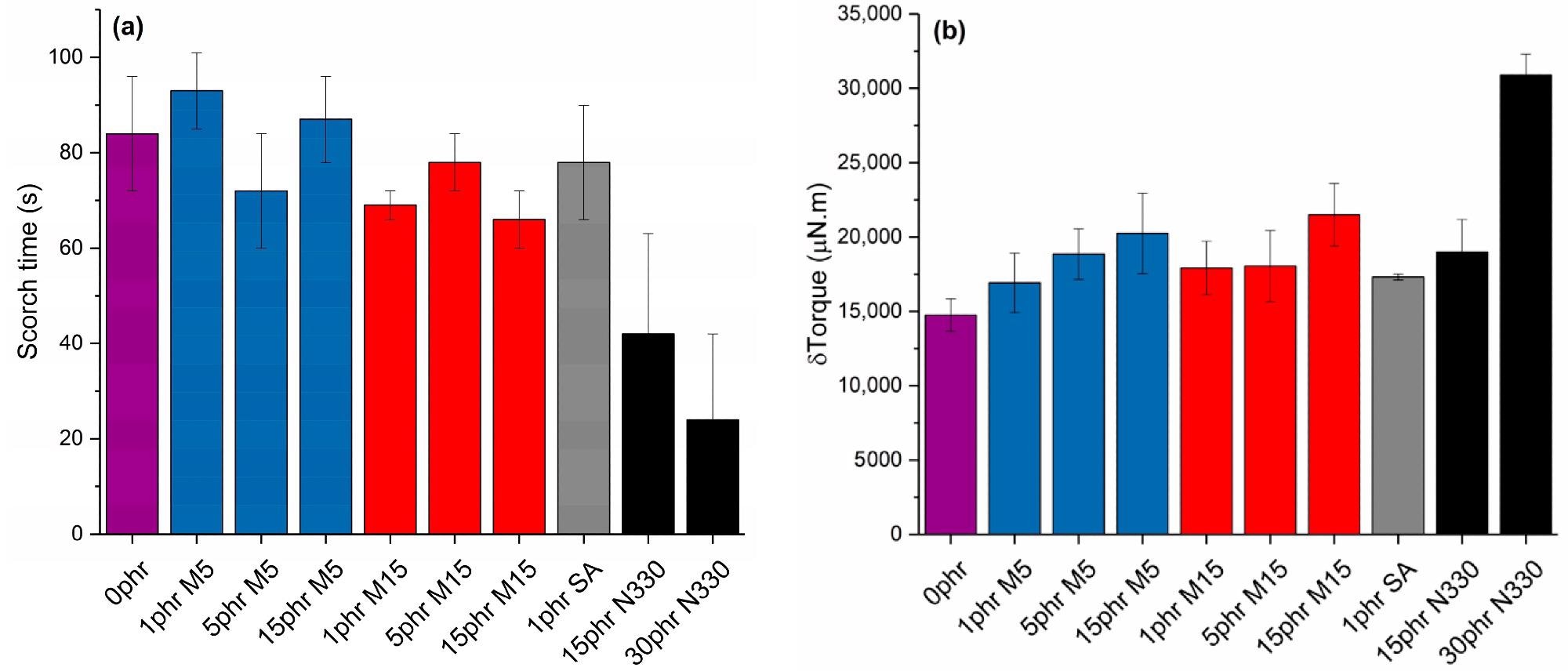
(a) Scorch time and (b) δTorque values for neat NBR and all nanocomposites under study. Image Credit: Innes, J.R et al., Polymers
Carbon black significantly improves the tear resistance of seals and has advantages in terms of cost, facile processing methods. The superior reinforcement capabilities of this material originate primarily from the strong interactions between filler and elastomer matrix.
Carbon black particles range in size from tens to hundreds of nanometers and their activity comes from their abundant surface groups. Carbon black possesses an onion-like nanostructure with an amorphous core. Oxygen-containing functional groups on the surface of the material aid dispersion within polymer matrixes, increasing the density of crosslinks and influencing the elastomer’s properties.
Developing High-performance Fillers
Recently, research has moved away from the use of carbon black as filler materials in elastomer matrixes due to the need for multifunctional elastomer nanocomposites which meet high-performance demands and the discovery of new nanomaterials. Graphene and multi-walled carbon nanotubes have been investigated in recent years to satisfy these demands.
Graphene possesses several characteristics which make it an attractive candidate for polymer composite fillers, including its large surface area/aspect ratio, unique mechanical properties, and electric and thermal conductivity. However, its high cost and difficulties in scalability restrict its industrial-scale use.
To overcome this issue, research has focused on carbon-based nanomaterials such as graphene oxide, reduced graphene oxide, and graphene nanoplatelets. Amongst these materials, graphene nanoplatelets have emerged as an attractive filler material for nanocomposite polymers due to their low cost and similar properties to graphene.
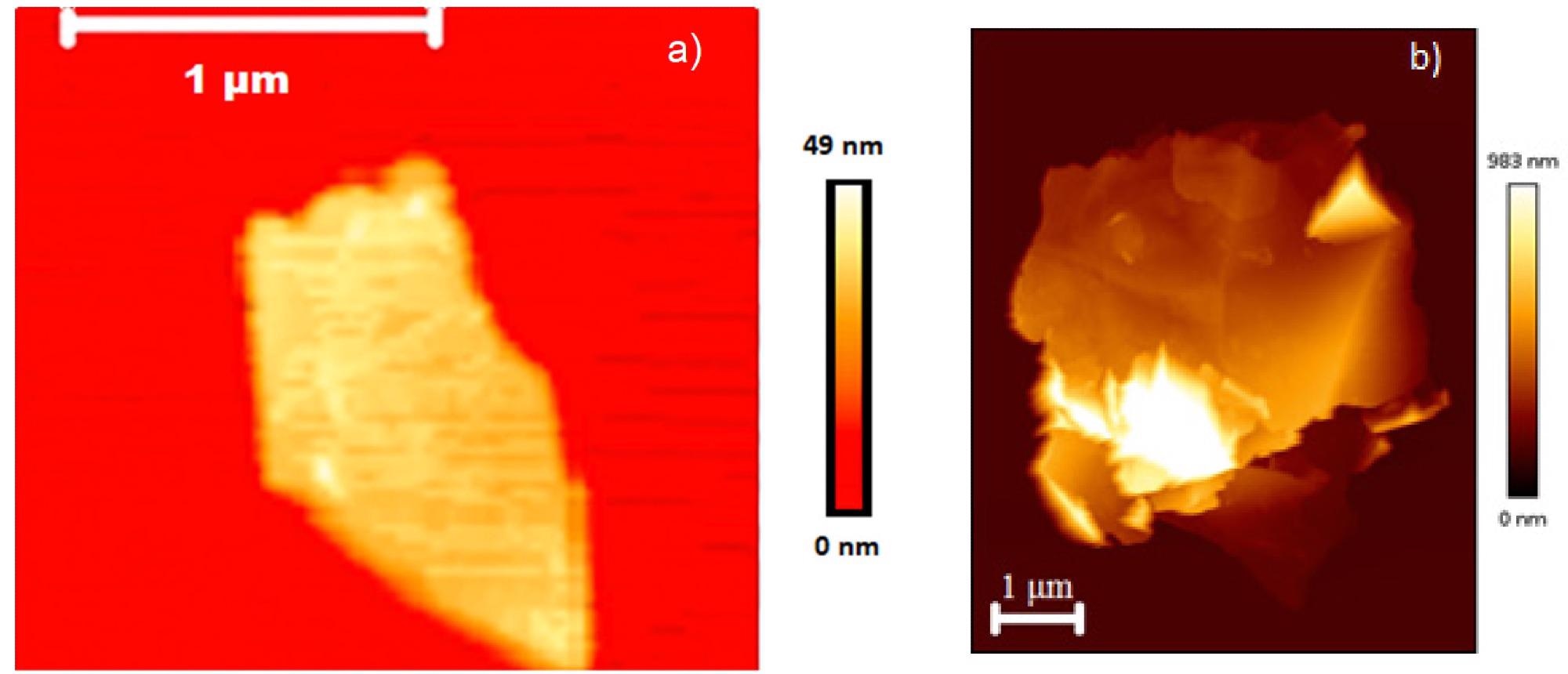
AFM images of typical M15 flakes: (a) a flake with an aspect ratio of 61 and (b) an agglomerated flake with an aspect ratio of 20. Image Credit: Innes, J.R et al., Polymers
Previous work by the authors of the current study has indicated that in terms of mechanical reinforcement, the nanocomposite’s modulus is independent of that of the filler. The strength of the interface with the matrix and the orientation and aspect ratio of the filler are important parameters that affect the nanocomposite material’s performance.
The Study
The authors of the study have evaluated both graphene nanoplatelets of different diameters and carbon black as reinforcement fillers for nitrile butadiene rubber.
It has been noted in the research that some studies have reported on using graphene as a reinforcement filler for this industrially important rubber, but there has not been sufficient in-situ and ex-situ characterization to model the micromechanics of composite rubbers. Nitrile butadiene rubber is commonly used in the oil and gas industries due to its superior oil resistance and good mechanical properties.
Previous research has evaluated the performance of nanocomposite rubbers containing low loadings of graphene nanoplatelets, which may be insufficient to meet the demands of materials that are used for high-performance applications.
Previous studies have compared these nanomaterials to nitrile butadiene rubbers reinforced with low loadings of carbon black and hybrid nanomaterial combinations. Results indicated improvements in mechanical properties, gas barrier properties, and scorch time using graphene nanoplatelets compared to rubbers reinforced with carbon black. Graphene oxide has also been used to produce reinforced nitrile butadiene rubber using solution-blending techniques, with improved mechanical properties observed at low filler contents.
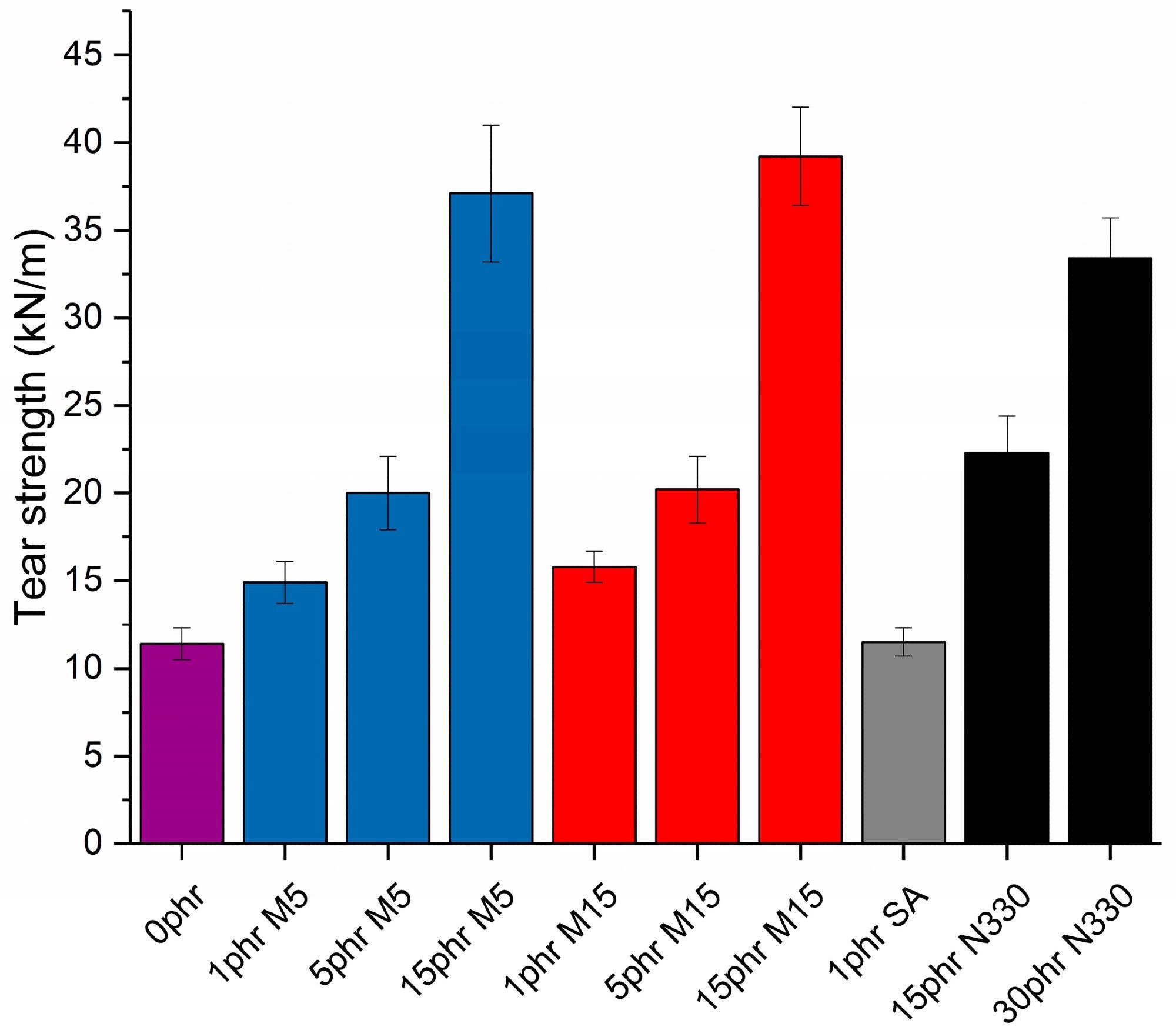
Tear strength values for neat NBR and all nanocomposites under study. Image Credit: Innes, J.R et al., Polymers
The authors have stated that the novelty of their research is the in-situ and ex-situ measurement of the graphene nanoplatelets aspect ratios and the use of experimental results to elucidate information on the material’s micromechanics. Atomic force microscopy was used to provide ex-situ measurement of the graphene nanoplatelet’s aspect ratio, which was compared with in-situ scanning electron microscopy results.
Previous studies have indicated that agglomeration causes reduced mechanical properties at high graphene loadings but have not fully elaborated on the reasonings. Furthermore, previous studies have not demonstrated this via simultaneous measurement of the graphene nanoplatelet’s aspect ratio and micromechanical modeling.
A major contribution in the research was the determining of the relationship between filler loading and the change in aspect ratio due to agglomeration. The authors comprehensively evaluated the tensile, hardness, and tear properties of composite materials and applied the micromechanical models to the modulus results.
Results of the research demonstrated that nitrile butadiene rubber reinforced with graphene nanoplatelets had reduced curing times and its scorch time is doubled, the material is stiffer and more flexible, and possesses improved tear strength, and the introduction of small amounts of graphene nanoparticles significantly increases the material’s modulus without a significant change in hardness.
Overall, the research indicated that graphene nanoplatelets as fillers possess advantages over carbon black, especially for applications that require increased elongation at break and reduced hardness, and is softer, which could reduce damage during installation.
Further Reading
Innes, J.R, Young, R.J & Papageorgiou, D.G (2022) Graphene Nanoplatelets as a Replacement for Carbon Black in Rubber Compounds [online] Polymers 14(6) 1204 | mdpi.com. Available at: https://www.mdpi.com/2073-4360/14/6/1204
Disclaimer: The views expressed here are those of the author expressed in their private capacity and do not necessarily represent the views of AZoM.com Limited T/A AZoNetwork the owner and operator of this website. This disclaimer forms part of the Terms and conditions of use of this website.