A group of Madrid-based researchers has developed a method for producing shape memory composites that could help develop shape-memory materials suitable for use across an extensive range of industrial sectors and application areas. The research is published in the journal Polymers.

Study: Shape-Memory Composites Based on Ionic Elastomers. Image Credit: Gorodenkoff/Shutterstock.com
Shape memory polymers have relatively good application potential in the biomedical and construction industries, as well as an expanding shape memory polymer market. Meeting demand in the automotive and aerospace sectors will advance product usage in the near future.
While it has been predicted that the biomedical end-use field could be the most promising area for shape-memory polymers, they are limited in terms of mechanical properties for use in other applications, such as in regard to flexibility, when compared to shape-memory alloys.
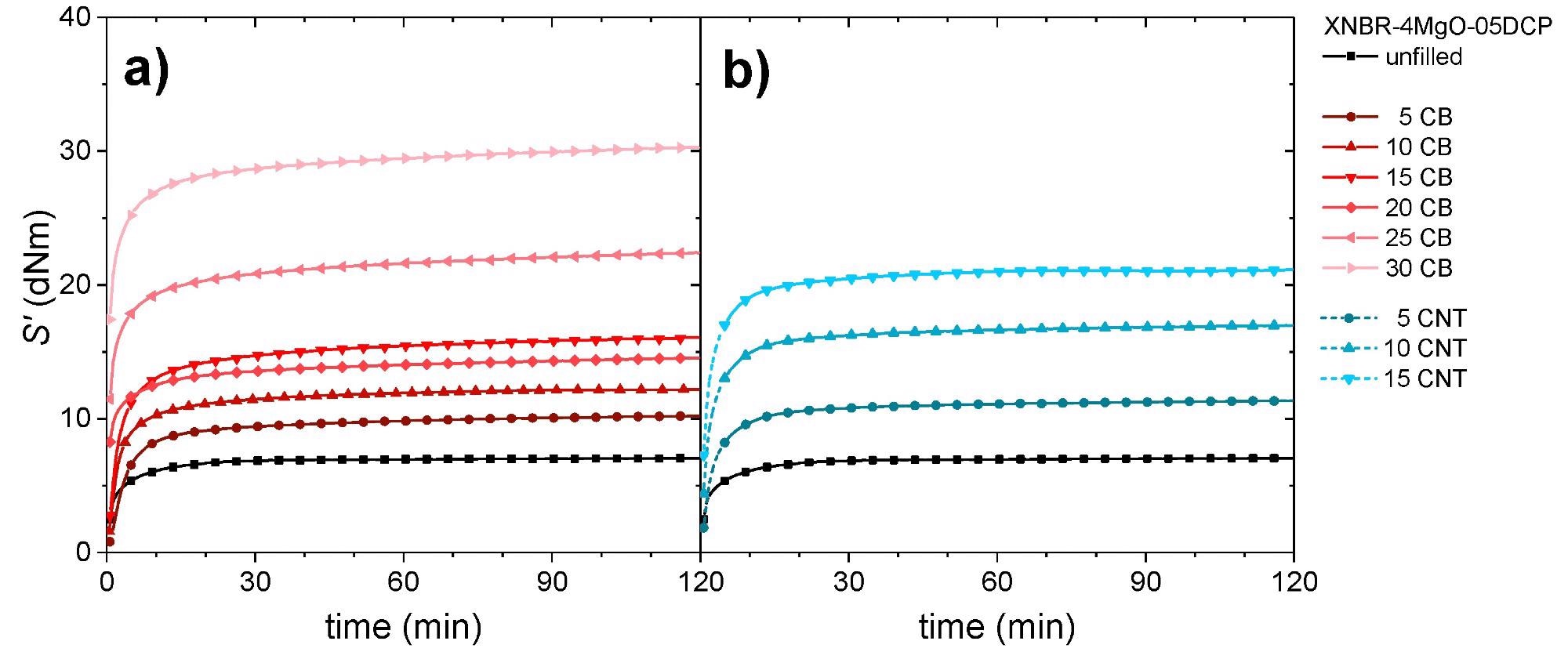
Evolution of the vulcanization curve (through the elastic component of the torque, S’) of the systems reinforced with different amounts (phr) of (a) CB and (b) CNT. Image Credit: González-Jiménez, A. et al., Polymers
Published in the journal Polymers, a team led by Dr. Antonio González-Jiménez of the Materials Science and Engineering Area, Rey Juan Carlos University, Madrid, detail how enhancing features such as crosslinking, changing deformation features, and adding elastomers and fillers to the polymer matrix could produce superior shape-memory materials.
Smart Materials
Shape memory materials belong to a class of smart materials which may also be known as functional materials. They have the ability to react and adapt to external environmental conditions. Such materials are able to physically change their shape and recover their original form after exposure to various stimuli.
For some time now, shape-memory materials of different compositions have attracted the attention of researchers due to their multi-functional abilities and increased demand for advanced components such as soft actuators.
Therefore, researchers have concentrated their efforts on developing newer smart materials that respond to various stimuli such as light, heat, magnetic fields, electricity, as well as exposure to water and humidity.
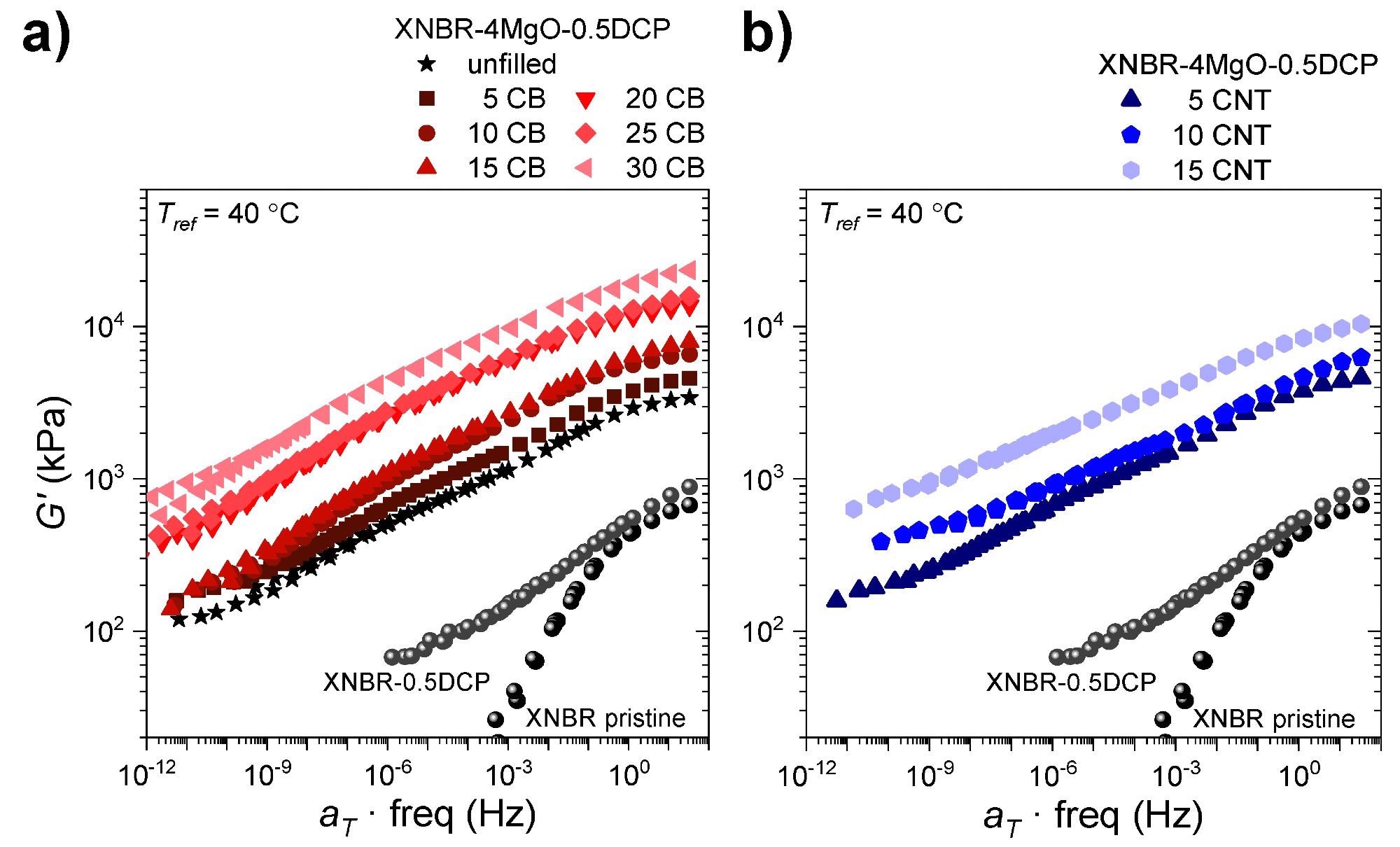
Master curves in which the elastic modulus (G’) is represented with respect to the frequency of the XNBR-4MgO-0.5DCP samples with (a) CB contents between 0 and 30 phr and (b) CNT contents between 0 and 15 phr. The curves were obtained from the principle of time–temperature superposition with Tref = 40 °C. Image Credit: González-Jiménez, A. et al., Polymers
With a drive towards the development of soft actuators Dr. González-Jiménez explains, “In recent years, different approaches have been made to obtain polymers that preserve an elastic nature in their temporary shapes, including an interpenetrating crystallizable thermoplastic network with an elastomeric matrix liquid crystalline elastomers and blends of elastomers and small molecule additives."
Therefore, the team focused their efforts on three primary objectives: (i) evaluating the influence of introducing conductive fillers (carbon black) and nano-fillers (multiwalled carbon nanotubes) on the network structure and shape-memory properties of XNBR compounds crosslinked with covalent and ionic bonds; (ii) comparison of the reinforcement efficiency of various fillers by studying their viscoelastic behavior, mechanical properties, and electrical properties; and (iii) developing a proof of concept of contemporary, advanced applications on the basis of using ionic elastomers with enhanced thermal and electrical conductivities.
Shape Memory Elastomeric Composites
The effect of introducing conductive- and nano-fillers into XNBR compounds has been studied to varying degrees in order to establish ways to improve various functions of shape memory materials such as elasticity, conductivity, and thermal stability.

Electroactive shape recovery behavior of the XNBR nanocomposite with 15 phr of CNTs as a function of the time of application of a constant voltage of 50 V. Image Credit: González-Jiménez, A. et al., Polymers
“The most popular approach to create elastic behavior in order to deform material into a different shape is the introduction of a dual network, where at least one of them presents a thermal transition, such as glass transition or melting temperature,” states Dr. González-Jiménez.
The Madrid-based researchers introduced carbon black with a high specific surface as well as multiwalled carbon nanotubes. After preparing samples they applied a series of tests and methods to observe shape memory behavior, electrical conductivity, and thermal conductivity. The team observed increases in the elasticity and thermostable behavior that allows the samples to recover their original or permanent shape demonstrating shape memory functionality.
“The introduction of carbon nanotubes results in the best fixing properties being obtained (between 4 and 10% improvement with respect to the unfilled material for the CNT contents studied),” explains Dr. González-Jiménez. Reinforcement using the nanotubes was the most effective approach, while reinforcement with carbon black has a comparative influence but more than double the amount of filler than that of the nanotubes was required.
The team was able to successfully develop shape memory elastomeric composites through the introduction of carbon black and carbon nanotube fillers, enhancing the shape memory behavior of the materials. Furthermore, the researchers also observed improvements in fixing properties as well as thermal conductivity as well as the possibility of developing materials that can be manipulated via electric currents.
Overall, the developments have opened up the field for selective shape recovery which will require further research to assess specific application areas. This should expand the application potential of shape memory composites.
References & Further Reading:
González-Jiménez, A.; Bernal-Ortega, P.; Salamanca, F.M.; Valentin, J.L. Shape-Memory Composites Based on Ionic Elastomers. Polymers 2022, 14, 1230. https://www.mdpi.com/2073-4360/14/6/1230
Disclaimer: The views expressed here are those of the author expressed in their private capacity and do not necessarily represent the views of AZoM.com Limited T/A AZoNetwork the owner and operator of this website. This disclaimer forms part of the Terms and conditions of use of this website.