Writing in the journal Polymers, a team of researchers from China has investigated the properties, applications, and challenges of 3D printed polymers for use as reinforcement materials in cement.
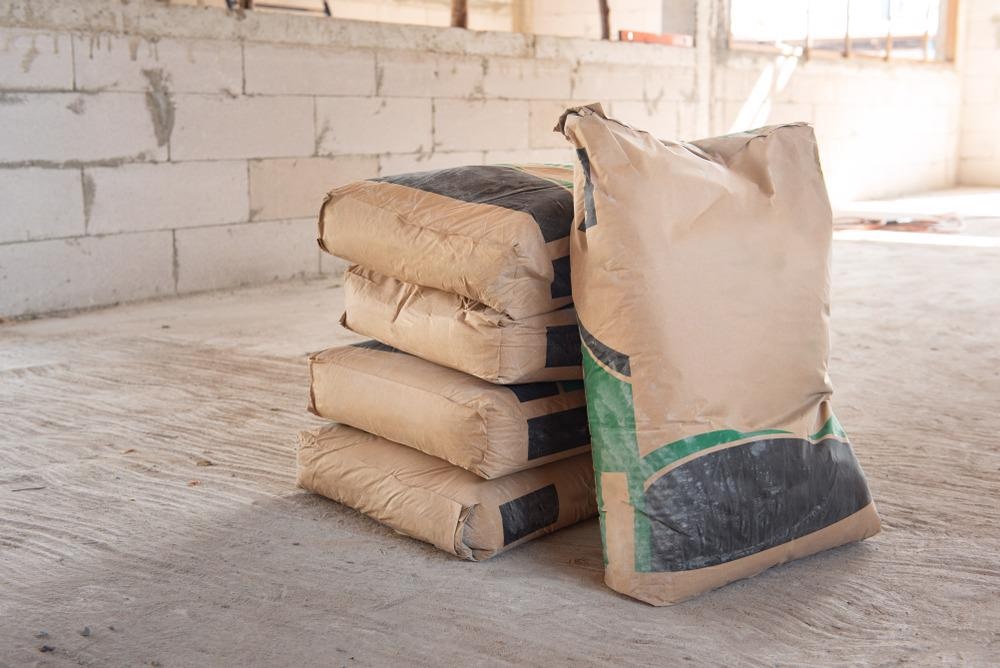
Study: Properties of 3D-Printed Polymer Fiber-Reinforced Mortars: A Review. Image Credit: MK photograp55/Shutterstock.com
Reinforcing Cement with Fibers
Cement is a crucial building material. The mechanical, physical, and physiochemical properties of cement are well-known. The properties of cement can be improved by incorporating filler materials, and in recent decades there has been significant research into the engineering applications of fiber-reinforced composites and geopolymer composites.
Fibers evaluated for use as reinforcing filler materials in cementitious materials and 3D-printed mortars include traditional fibers as well as synthetic and natural polymers. Research has focused on both virgin materials and valorizing waste streams from multiple industries for use as materials for this purpose.
Architectural 3D Printing
3D printing, otherwise known as additive manufacturing, is a technology that has disrupted many different industries, facilitating a new paradigm in manufacturing and advanced materials research. Several different 3D printing techniques have been developed in recent years, including stereolithography, fused deposition modeling, and digital light processing. 3D printing fabricates structures and device components layer-by-layer or, in some cases, continuously, typically by extruding a material slurry through a nozzle.
For the construction industry, 3D printing has proven to be a revolutionary technology. Presently, 3D technologies in architecture typically adopt D-shape technologies and Contour crafting. Whilst D-shape techniques are a powder deposition and construction process, Contour crafting only prints the outer layer of a component, which is then filled with mortar.
In recent years, 3D-printed mortars have been widely researched in the architecture industry. This technology has the advantage of needing no templates and can achieve rapid molding and fine processing. Multiple layers, as well as the adhesive elements between the layers, can be continuously extruded using this technology, and mortar performance can be met with free forming.
However, traditional reinforcement elements such as steel rebars cannot be incorporated into 3D-printed mortars, facilitating the need for filler materials for reinforcement purposes and enhancing properties such as mechanical and structural strength, impact resistance, and toughness.
Traditional fibers which have been explored by researchers include steel, glass, and carbon. Each of these reinforcement elements has its own advantages and drawbacks, however. Steel improves properties such as tensile strength, but rusts easily. Glass fibers resist corrosion but are insufficient for resisting alkali conditions and wear. Carbon fibers are lightweight, cheap, and possess high strength, but have poor impact resistance and toughness.
The Study
The study in Polymers has investigated the application and properties of polymer fibers for use as reinforcement fillers for 3D-printed mortars. Replacing traditional fibers with polymers is advantageous, as it reduces the cost of manufacturing and can improve the performance of printed mortars. Using polymers can control crack formation and development, imbuing the material with greater impact resistance and resistance to liquids.
Several unadulterated polymer fibers have been used in research, including polyvinyl alcohol, aramid, polyethylene, and polypropylene. The properties of 3D printed mortars can be influenced by the fiber’s geometric characteristics, mechanical properties, and elongation. Both aramid and polyvinyl alcohol have similar mechanical properties to steel and possess superior impact and fatigue resistance. Other fibers possess a low elastic modulus and improve the impact resistance and toughness of 3D printed mortars.
More from AZoM: Elemental Composition of Wines by Region
Fibers additionally have an effect on the workability of 3D-printed mortars. Working performance includes cohesion, water retention, and fluidity. Aside from the fluidity of the mortar, its setting time and thixotropy must be controlled. Fibers can help to restrain the structure’s deformation and help to obtain a desired uniform and continuous printing of material. Polymer fibers have less of an effect on nozzle blockage than steel fibers, for instance. The authors have explored the effects of different polymer fibers on workability.
Additionally, the research has highlighted how polymer fibers influence the mortar’s mechanical properties, which govern the performance of printed mortar. The influence of single polymer fibers was extensively explored and categorized by the authors alongside the influence of hybrid polymer fibers. The effect of fibers on the mortar’s interlaminar bonding strength was discussed in depth in the study.
Based on their experimental observations, the authors have concluded that polymer fibers improve the shape retention of mortar mixtures and reduce fluidity, but have little effect on the mortar’s compressive strength. Whilst the flexural strength is enhanced, attention should be paid in research to the mortar’s anisotropy and the fiber direction’s orientation.
Challenges identified by the authors include insufficient theoretical research on the interaction between polymer fibers and the 3D mortar’s matrix, and a lack of engineering practice and applications for 3D printed mortars reinforced with polymer fibers. Moreover, further study is needed on the interactions between fibers and additives such as nanomaterials.
Finally, the authors have highlighted several ways these challenges can be overcome, including actively exploring improving the properties of 3D printed mortars, studying surface modifications, and more research on hybrid fibers.
Further Reading
Liu, J & Lv, C (2022) Properties of 3D-Printed Polymer Fiber-Reinforced Mortars: A Review [online] Polymers 14(7) 1315 | mdpi.com. Available at: https://www.mdpi.com/2073-4360/14/7/1315
Disclaimer: The views expressed here are those of the author expressed in their private capacity and do not necessarily represent the views of AZoM.com Limited T/A AZoNetwork the owner and operator of this website. This disclaimer forms part of the Terms and conditions of use of this website.