Writing in the journal Energies, a team of scientists from France has investigated the properties of 3D-printed polycarbonate. The research has implications for the future design of insulating materials in the construction industry using additive manufacturing methods.
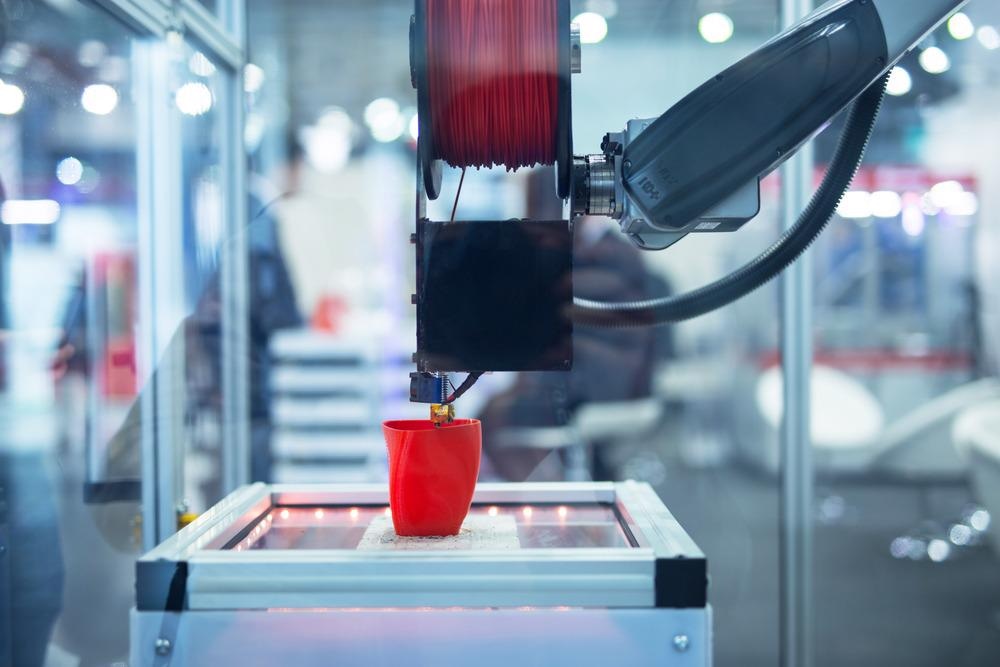
Study: Mechanical and Thermal Properties of 3D Printed Polycarbonate. Image Credit: guteksk7/Shutterstock.com
Background to the Research
Poorly insulated buildings contribute to the significant levels of energy consumption in the construction sector through heat loss to the external environment and increased electricity and gas use in the winter months. To tackle this problem, several countries have introduced regulations governing the use of suitable insulation and materials.
Recent work has been conducted to develop more environmentally friendly and efficient insulating materials. Polycarbonate has potential as an insulating material in the construction industry due to physical stability at elevated temperatures and fire resistance.
Designing materials with locally-controlled architectures provides powerful benefits for the manufacture of insulators. Porosity, connectivity, and shape adaptations allow the design of more efficient materials. Finite element computations provide enhanced abilities in material design.
Conventional manufacturing methods such as foaming and molding cannot achieve the design freedom and customizability required for the manufacture of advanced insulation materials, however. Due to the limitations of conventional methods, additive manufacturing (AM) has become an attractive alternative technique.
General scheme showing the methodology used to determine mechanical and thermal properties of PC. Image Credit: Bahar, A et al., Energies
Additive manufacturing confers the benefits of low waste, design freedom, cost, and energy-saving potentials for the construction industry. Applying this technology to the manufacture of bio-sourced insulation materials would be a game-changer for the construction of new buildings and retrofitting existing structures with new insulation.
There are, however, some limitations with AM techniques that currently hinders their widespread application for this purpose.
Large-scale use can be limited by long production times due to current restrictions on printing speeds. Several strategies have been explored in recent years to overcome slow printing speeds, including designing new nozzles which can achieve fast deposition rates and multi-nozzle systems. For any strategy to be successful, there must be a trade-off between part size and resolution.
Amongst the various AM technologies explored for this purpose, fused deposition modeling has emerged as an extremely powerful candidate. This widespread technology combines the benefits of cost-effectiveness and simplicity without the need for additional tooling or post-processing steps for the printing of polymeric materials and structures. Several studies have focused on optimizing the parameters of this powerful manufacturing method.
The Study
The present study has explored the manufacture of polycarbonate insulation materials with fused deposition modeling. The mechanical and thermal properties of the feedstock material have been thoroughly categorized in the study. Thermal properties analyzed include diffusivity and conductivity, and the tensile properties analyzed include stiffness and strength.
Specific shapes were employed for mechanical testing (dogbone shapes) and thermal testing (parallelepipedic) to meet testing standards. Adhesion problems were avoided by adapting the sample’s overall length to the printing process.
Platform and building temperatures were optimized to avoid platform decohesion or warpage. The authors discovered that the manufacturer-recommended platform temperature (260 oC) was insufficient for successful prints.
A Universal Testing Machine was employed to perform tensile tests. A high-speed camera was used to monitor sample deformation. Thermal properties were assessed using transient hot probe methods to measure localized temperature changes over time. A hot wire probe was used to measure thermal conductivity, with a hot plane probe used to measure thermal effusivity.
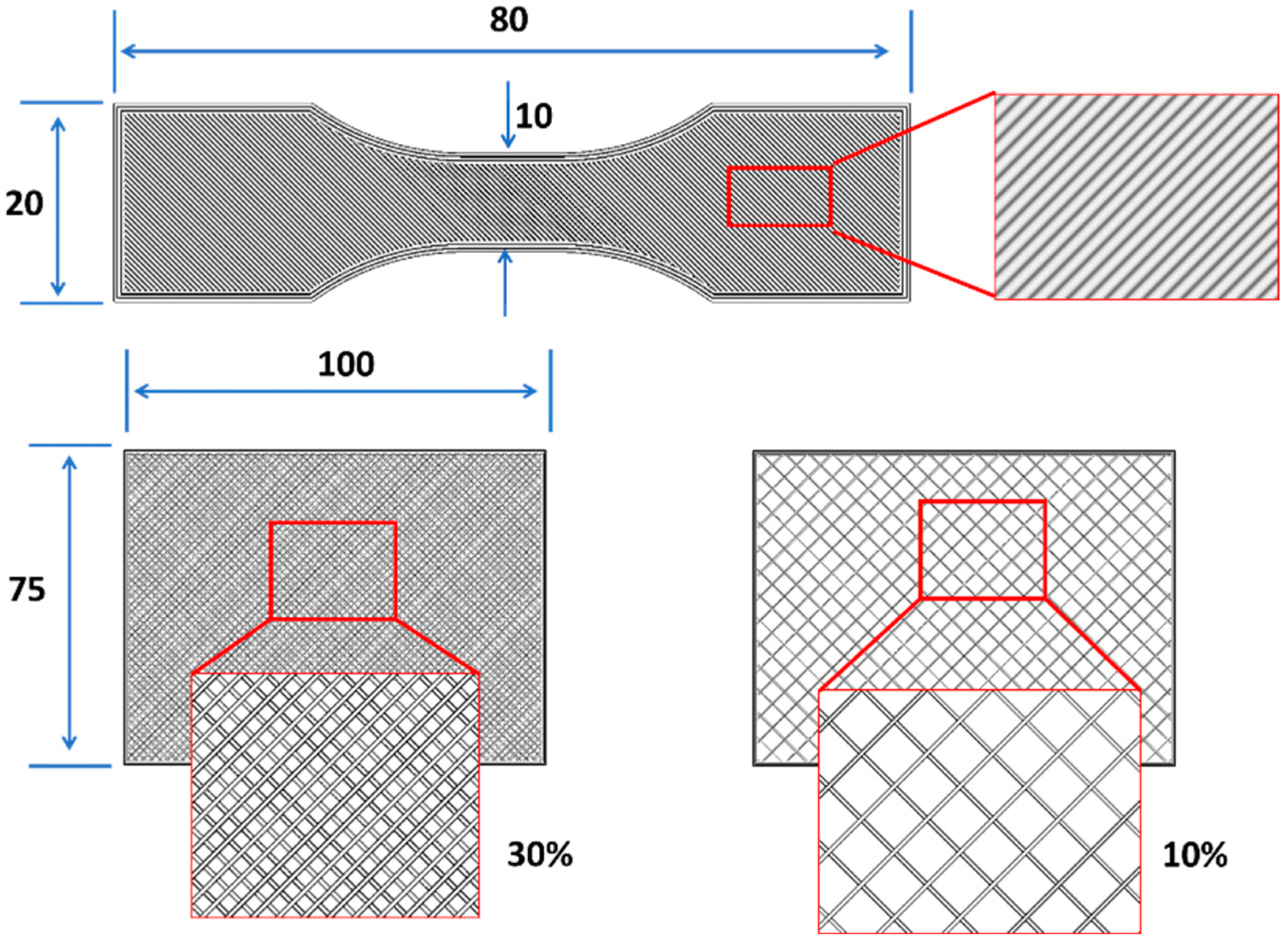
Sample dimensions used for PC 3D printing. Image Credit: Bahar, A et al., Energies
Results of the Study
Experimental results demonstrated that the optimal printing temperature is 280 oC. At this temperature, the tensile ranking of the material is the highest. The 3D-printed polycarbonate possesses extremely high tensile strength and stiffness.
Thermal analysis has revealed the logical effect of infill rate on effusivity, diffusivity, and thermal conductivity. The authors have concluded that this is related to the presence of insulating air in the polycarbonate material. Thermal properties were better than hemp concrete, another currently employed insulation material.
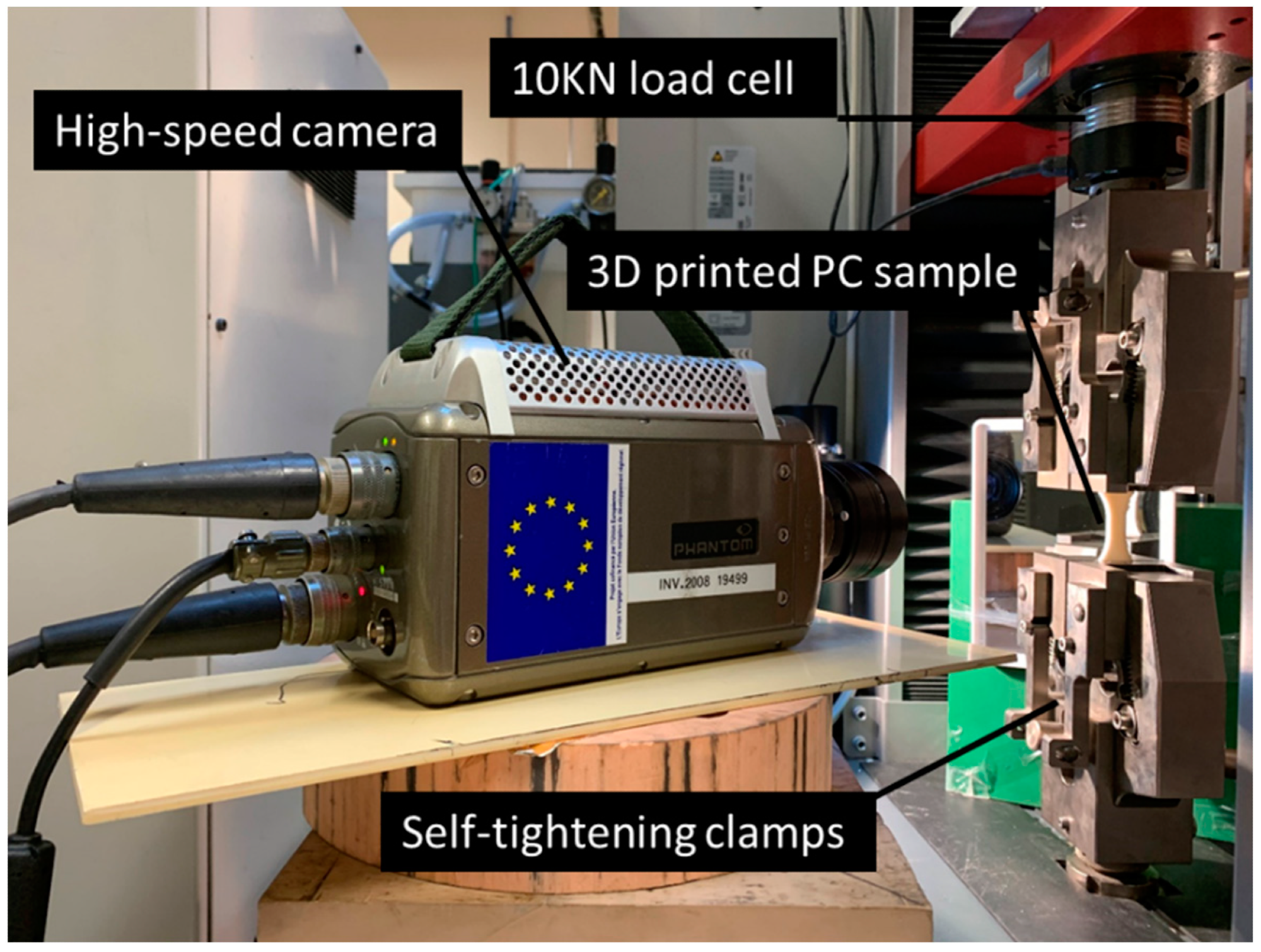
Mechanical testing setup. Image Credit: Bahar, A et al., Energies
In Summary
The authors have demonstrated the suitability of fused deposition modeling for the manufacture of advanced insulation materials based on polycarbonate, a cost-effective, durable, lightweight, strong, and easily shapable material.
Based on the observed performance and properties, the authors have concluded that 3D-printed polycarbonate can be considered for thermal energy storage and insulation purposes. The suitability of this material and the superior design freedom and simplicity of fused deposition modeling has the potential to be revolutionary for the fabrication of building insulation in the future.
Further Reading
Bahar, A et al. (2022) Mechanical and Thermal Properties of 3D Printed Polycarbonate Energies 15(10) 3686 [online] mdpi.com. Available at: https://www.mdpi.com/1996-1073/15/10/3686
Disclaimer: The views expressed here are those of the author expressed in their private capacity and do not necessarily represent the views of AZoM.com Limited T/A AZoNetwork the owner and operator of this website. This disclaimer forms part of the Terms and conditions of use of this website.