By Surbhi JainReviewed by Susha Cheriyedath, M.Sc.Jun 6 2022
In an article recently published in the journal Otology & Neurotology Open, researchers discussed the development of a three-dimensional (3D)-printed human ear model for standardizing blast exposure testing of hearing protection devices.
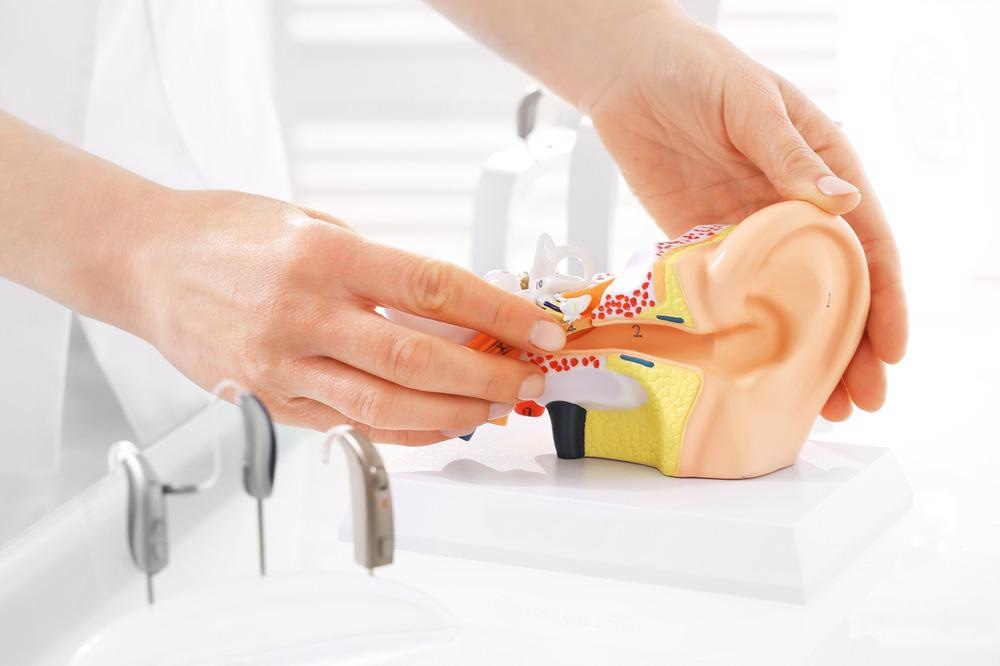
Study: A 3D Printed Human Ear Model for Standardized Testing of Hearing Protection Devices to Blast Exposure. Image Credit: Robert Przybysz/Shutterstock.com
Background
In the context of active combat, hearing loss can occur as a result of blast-related ear injuries like tympanic membrane (TM) rupture. Hearing protection devices (HPDs) are required to prevent hearing loss while deployed in hazardous situations, and despite the fact that a variety of HPDs are extensively available, some troops believe that HPDs diminish situational awareness. Advanced HPDs have been designed to improve perceived situational awareness and HPD compliance; however, current research shows that more HPD improvement is needed, as well as trustworthy and efficient testing procedures.
Previous research into the efficacy of HPDs when subjected to noise impulses or blasts used a variety of computational and experimental methodologies. The protective efficacy of various earplugs has been studied using human cadaveric temporal bones (TBs). Testing HPDs in high-pressure situations with computational models is both cost-effective and time-efficient. 3D printing technology is a fascinating tool for creating personalized otolaryngology solutions. 3D printed models have the potential to stimulate the ear's function for mastoid surgery; yet, no models for generating HPDs have been created using 3D printing. A model that takes advantage of the advantages of 3D printing could substantially improve HPD evaluation.
Computer models used for 3D printing, illustrating the finite element model of the ear and 3D printed TB. A, Finite element model of the human ear with the ear canal, middle ear, and cochlear load. B, Sectional view of the assembled CAD model showing the enclosed ear canal and middle ear tissues. C, Lateral view of the CAD model of the 3D printed TB highlighting the ear canal entrance. The model’s shape was designed to mount into the head block for blast exposure tests. D, Medial view of the CAD model of the 3D printed TB. The pressure ports to the ear canal near the TM (P1) and middle ear cavity (P2) are shown where pressure sensors are threaded for measurements. A port for access to the stapes footplate for future studies is also shown. E, Exploded view of the 3D printed TB’s CAD model showing the parts to be printed separately: outer ear, middle ear, and cavity seals. CAD indicates computer-aided design; TB, temporal bone; TM, tympanic membrane. Image Credit: Kavimughil, M et al., Otology&Neurotology
About the Study
In this study, the authors developed a 3D printed TB model which was built with flexible and hard polymers. The proposed model included the TM, ear canal, middle ear suspensory ligaments/muscle tendons, ossicular chain, and middle ear chamber.
Laser Doppler vibrometry was used to measure the TM movement during sound stimulation. Pressures at the ear canal entry (P0) and near the TM in the ear canal (P1) were measured after the TB model was exposed to blasts with or without HPDs. All of the findings were compared to those found in human tuberculosis patients. The passive HPDs' protective effect during explosion was correctly tested using a 3D printed TB model, and the potential for usage as an acoustic transmission model was evaluated.
The team described the construction of a 3D-printed ear model that anatomically and mechanically approximated the middle and outer ear for successful measurement of passive HPDs during the blast exposure. Experiments with and without HPDs exposed the 3D printed TB to the blast overpressures, and the findings were compared to cadaveric TBs for validation. The pressure at the ear canal entry and near the TM was measured in these trials.
The researchers created the 3D printed TB using a finite element model based on histological cross-sectional scans of a 55-year-old human male with tuberculosis. The structural components of the outer and middle ear of humans were included in the 3D printed TB model and the finite element.
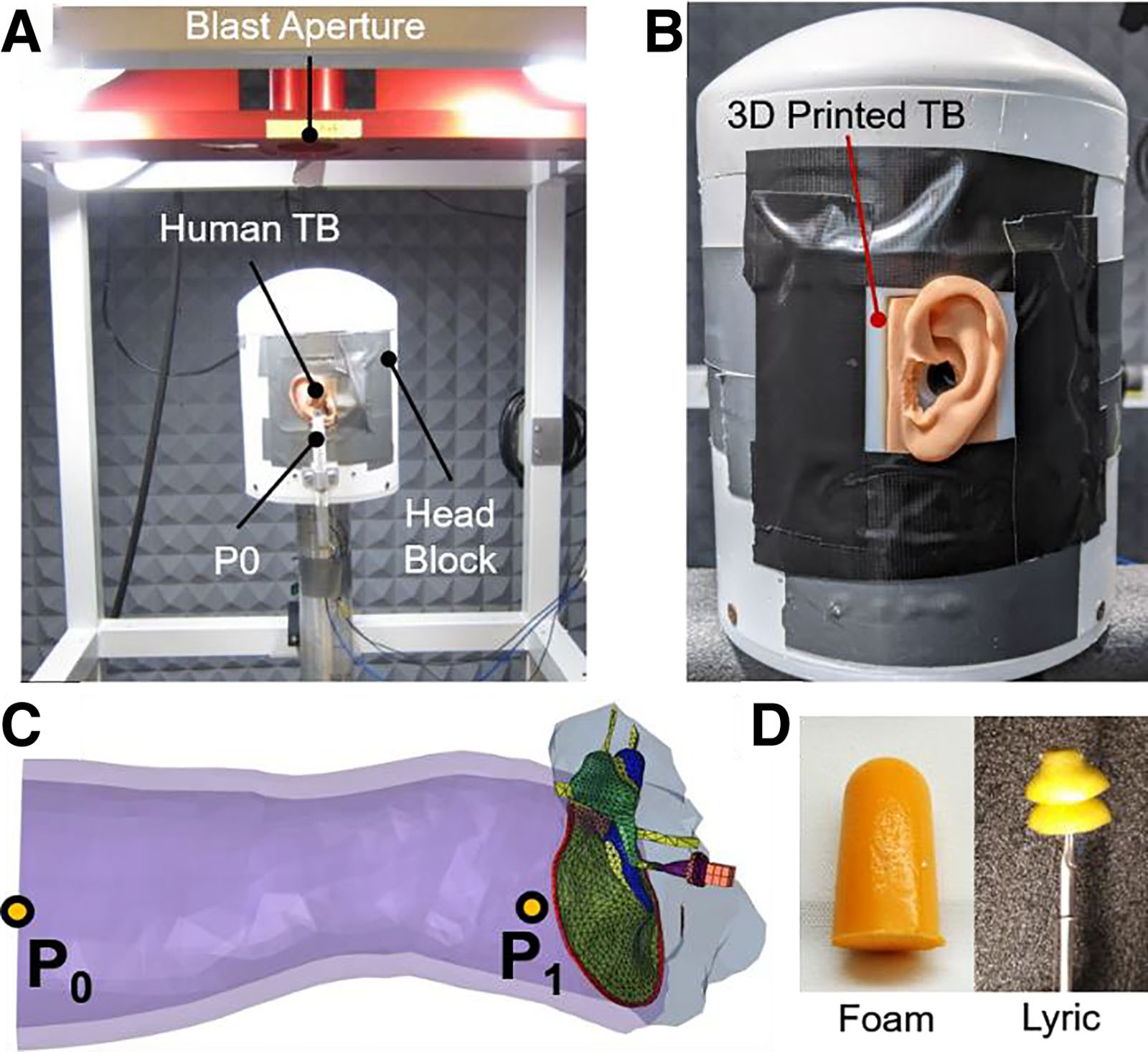
Experimental blast setup and pressure sensor placements used to measure blast wave transmission in ear models. A, Image of the blast test setup within an anechoic chamber where the “head block” sits below the blast aperture. A human cadaveric TB is mounted to the head block and the pressure sensor P0 is mounted outside of the ear canal entrance. B, Image of the 3D printed TB mounted to the head block. C, The finite element model highlighting where the pressures were monitored during blast exposure: at the entrance of the ear canal, P0, and in the ear canal near the TM, P1. D, Images of the foam earplug (left) and Lyric earplug with a stick holder (right) used in blast exposure tests. TB indicates temporal bone; TM, tympanic membrane. Image Credit: Kavimughil, M et al., Otology&Neurotology
Observations
The displacement of 3D printed TM followed a similar pattern to that of the human TM at frequencies less than 3 kHz, but the 3D printed TM's displacement was significantly smaller than that of the humans. The largest difference between the 3D manufactured TM and the human TB average was 0.058 µm at 275 Hz, while the closest readings were at 5248 Hz with a difference of 0.003 µm.
For the human TB and 3D printed TB, the values of peak P0 pressure were 5.89 psi and 5.92 psi, respectively, and the A-duration corresponding to the P0 waveforms for the 3D manufactured TB and human TB were 0.28 and 0.32 ms, respectively. The human TB and 3D printed TB produced P1 pressure waveforms with peak values of 10.38 psi and 9.79 psi, respectively, at 0.79 and 0.69 ms. The A-duration corresponding to the P1 waveforms for the 3D printed TB and human TB were 0.08 and 0.05 ms, respectively. The A-durations and P1 peak pressures were similar, and the 3D printed TB had a faster time-of-arrival for the P1 peak than the human TB.
The attenuated peak pressures at P1 caused by HPDs ranged from 0.92 to 1.06 psi in the 3D printed TB, with blast peak pressures of 5.62–6.54 psi at P0, and the observed findings were within the mean and SD of published data.
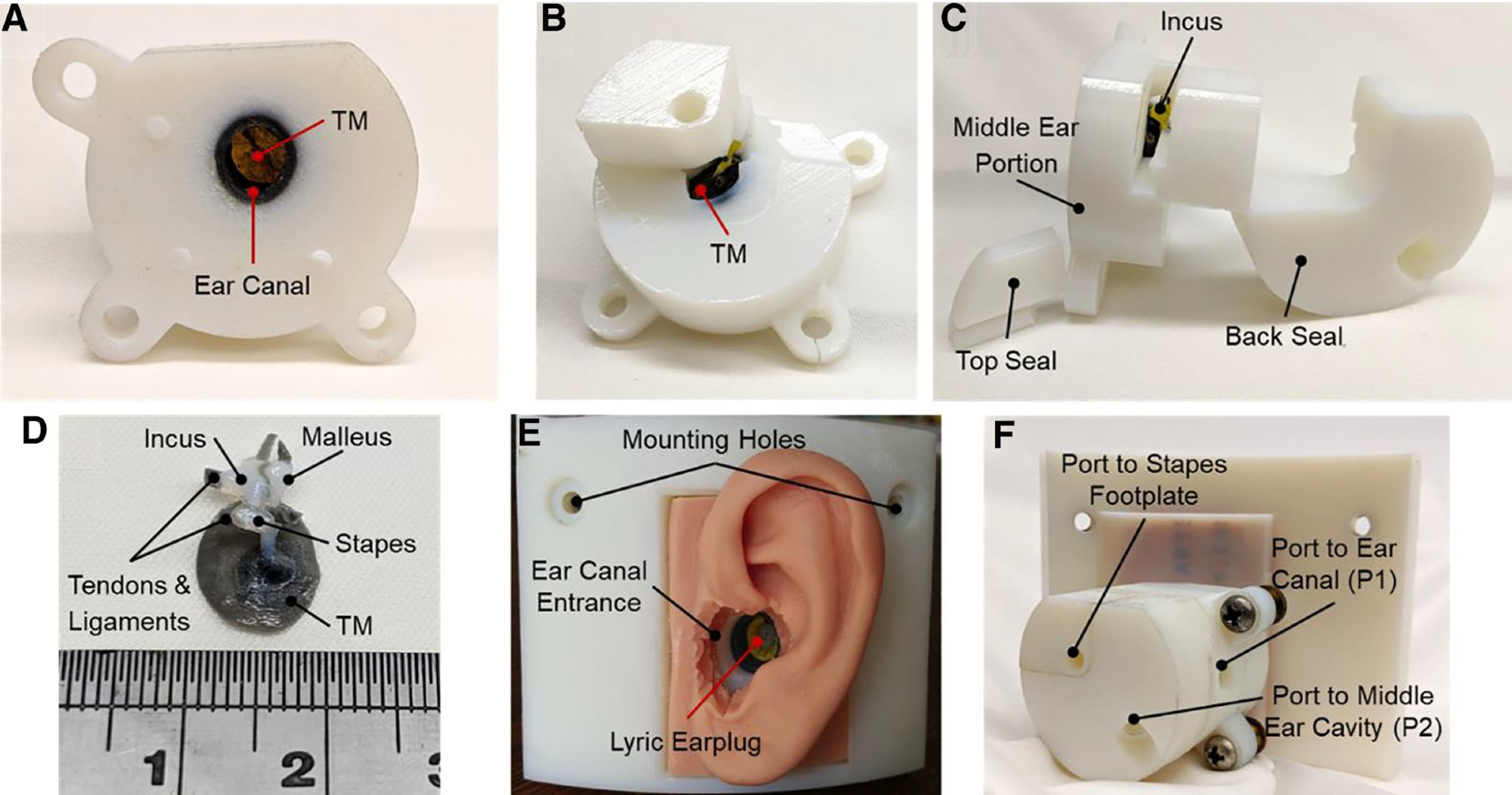
Images of a finished print of the 3D printed TB’s unassembled middle ear portion. A, Lateral view of the middle ear portion showing the ear canal and TM within. B, Medial view of the middle ear portion of the 3D printed TB showing the opening used for cleaning. C, Posterior view of the 3D printed TB’s middle portion with the seals. D, A 3D print of the ossicles, TM, and ligaments and tendons from within the middle ear cavity of the 3D printed TB. The ossicles were imaged without the surrounding material and with a scale to highlight the detail and size of the middle ear tissues. E, Lateral view of the assembled 3D printed TB with a Lyric earplug inserted into the ear canal. A silicone mold of the pinna was adhered to the 3D printed TB to simulate the outer ear. F, Medial view of the assembled 3D printed TB showing the ports to measure the pressures at the TM and in the middle ear cavity and to access the stapes footplate. TB indicates temporal bone; TM, tympanic membrane. Image Credit: Kavimughil, M et al., Otology&Neurotology
Conclusions
In conclusion, this study elucidated the development of a 3D printed TB for enabling standardized blast testing of HPDs. Two HPDs were used to assess the protective function of the 3D printed TB during the blast. With an HPD in place, the attenuated peak pressure near the TM was as low as 0.92 psi with a blast peak pressure of 5.62 psi at the ear canal entry, while without an HPD, the pressure near the TM was 9.79 psi with a similar blast peak at the ear canal entrance.
The pressure measurements in the 3D printed TB were well within the mean and SD of published data from human cadaveric TB tests.
Disclaimer: The views expressed here are those of the author expressed in their private capacity and do not necessarily represent the views of AZoM.com Limited T/A AZoNetwork the owner and operator of this website. This disclaimer forms part of the Terms and conditions of use of this website.
Source:
Kavimughil, M., Leena, M. M., Moses, J. A., et al. A 3D Printed Human Ear Model for Standardized Testing of Hearing Protection Devices to Blast Exposure. Otology & Neurotology Open 2(2) e010 (2022). https://journals.lww.com/onojournal/Fulltext/2022/06000/A_3D_Printed_Human_Ear_Model_for_Standardized.1.aspx?context=LatestArticles