By Surbhi JainReviewed by Susha Cheriyedath, M.Sc.Jun 9 2022
In an article recently published in the journal Additive Manufacturing Letters, researchers discussed the utility of a flat-top laser beam in selective laser melting for the development of single crystals of pure nickel (Ni).
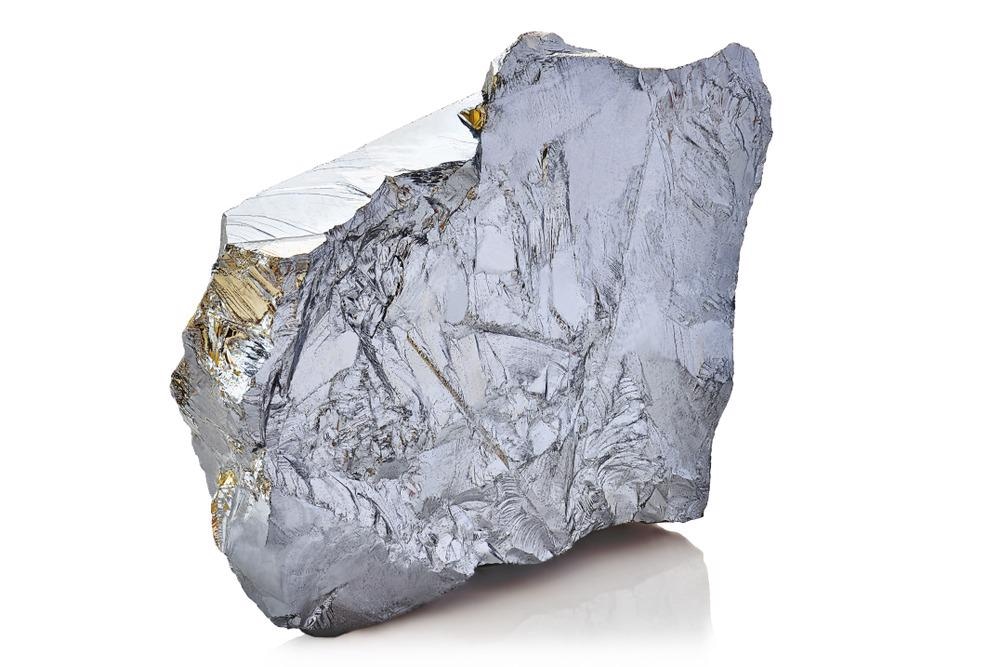
Study: Manufacturing single crystals of pure nickel via selective laser melting with a flat-top laser beam. Image Credit: Sebastian Janicki/Shutterstock.com
Background
Due to the rising usage of high-temperature components, demand for Ni-based superalloy components made by additive manufacturing has surged. Recent studies show that Ni-based single crystal (SX) superalloys could be successfully produced without the need for SX seeds by utilizing electron beam melting.
There have been several reports on the use of selective laser melting (SLM) to fabricate Ni-base SX superalloys. Controlling the defect and grain boundary (GB), strain suppression, and texture homogeneity during SLM is difficult due to the steep thermal gradient induced by rapid heating in the uppermost layer, lower temperature of the underneath layer, and the limited heat conductivity. For exact structural control, complex changes to the scan method or the usage of SX seeds are typically required.
In the as-built SLM product, repetitive thermomechanical cycles cause high strain and dislocation density, which results in dynamic recrystallization (DRX) and the production of new grains. To obtain an SX structure, it is necessary to manipulate the grain structure in the products of SLM using temperature gradients and strain-inducing variables.
A Gaussian-based beam was used in the majority of earlier studies on texture controls and microstructure in SLM. There are currently no studies that provide extensive investigations of the microstructure creation process employing the high-angle grain boundary (HAGB) and flat-top beam suppression.
About the Study
In this study, the authors examined the utility of a flat-top laser profile in SLM to fabricate an SX structure in pure Ni without the need for an SX build plate in the SLM. An SLM 280 HL was used to fabricate the SLM in an Ar environment. High-purity polycrystalline Ni plates were used to examine the single tracks to estimate the melt pool shape. For Tracks 1 and 2, a flat-top beam was employed, while Track 3 used a Gaussian beam.
The team measured the melt pool depths on both sides of the BD–HD plane at sites in the middle. The multi-layers were created using the observed melt pool geometry combination. The hatch gap was set between 70 and 200 μm, and the layer thickness was kept at 30 μm. A Microtrac S3500 laser diffraction particle size analyzer was used to quantify the average particle size of Ni powder. A 90° rotation scanning approach was used to laser scan the SD–HD plane. On polycrystalline stainless steel 304 plates, cylindrical specimens were printed.
The researchers sectioned and ground all the specimens with #320 and #600 abrasive paper before being mechanically polished with diamond and colloidal silica suspensions. The microstructure of the specimens was studied using scanning electron microscopy (SEM) and electron backscatter diffraction (EBSD).
Observations
Using Pantleon's modeling based on Nye's tensor that utilized 18 geometric dislocation configurations on the (111)<110> FCC slip system, the GND in FT1, FT2, and G1 were calculated to be 0.71x1014, 1.07x1014, and 1.28x1014 /m2, respectively. Regardless of the locations, the GND distribution was comparable for FT1 and FT2. GND values in FT1 regions 1 and 2 were 0.90 x1014 /m2 and 0.89 x1014 /m2, respectively. GND discrepancies between regions 3 and 4 in FT2 were insignificant at 0.99x1014 /m2 and 0.77x1014 /m2, respectively. G1 had a heterogeneous GND distribution, and region 5, which represented the melt pool center, had a GND value of 1.70 x1014 /m2.
The GND near the melt pool's edge, G1's region 6, had a value of 0.67x1014 /m2. The texture of the SX structure in FT1 was found to be around [017]<100>, which indicated an ±8° divergence from the BD. Track 3 with ET = 6.25 J/mm2 had a deeper depth of 148.06 μm than its width of 144.48 μm, which indicated that it was Gaussian-based. In Track 1 with ET = 5.10 J/mm2, the melt pool width and depth were measured to be 143.67 and 20 μm, respectively. Track 2 had a breadth and depth of 488.98 μm and 68.79 μm, respectively, with a greater ET of 8.57 J/mm2.
The development of a planar melt pool resulted from the optimization of the parameters. Without using an SX seed, a homogeneous near-(001)<100> texture with suppressed HAGB was produced in high building heights of greater than 20 mm.
Furthermore, the planar melt pool hindered HAGB formation by suppressing geometrically required dislocation build-up and strain-induced continuous dynamic recrystallization. Without using an SX seed, an SX structure with homogenous near-(001)<100> texture and inhibited HAGB was effectively created.
Conclusions
In conclusion, this study elucidated the development of a homogenous near-(001)<100> SX structure composed of pure Ni with suppressed HAGBs by using utilizing SLM without an SX seed by optimizing the planar melt pool with a flat-top beam.
The planar melt pool helped maintain a nearly uniform near-(001)<100> development along the BD while also limiting strain accumulation, which might lead to continuous dynamic recrystallization (CDRX)-induced HAGB production. The authors mentioned that the planar melt pool generated by the flat-top beam to achieve an SX structure without the use of an SX seed is expected to be used in future work for a wider spectrum of metals and alloys.
They believe that the implementation of multiple laser concepts in the SLM process, notably for generating the SX structure, will bring fresh insights into the procedure necessary to obtain the desired microstructure and associated attributes.
Disclaimer: The views expressed here are those of the author expressed in their private capacity and do not necessarily represent the views of AZoM.com Limited T/A AZoNetwork the owner and operator of this website. This disclaimer forms part of the Terms and conditions of use of this website.
Source:
Jodi, D. E., Kitashima, T., Koizumi, Y., et al. Manufacturing single crystals of pure nickel via selective laser melting with a flat-top laser beam. Additive Manufacturing Letters 100066 (2022). https://www.sciencedirect.com/science/article/pii/S2772369022000408