By Surbhi JainReviewed by Susha Cheriyedath, M.Sc.Jun 13 2022
In an article recently published in the Journal of the European Ceramic Society, researchers discussed the additive manufacturing (AM) of polymer-based SiOC/SiC ceramic composites using stereolithography.
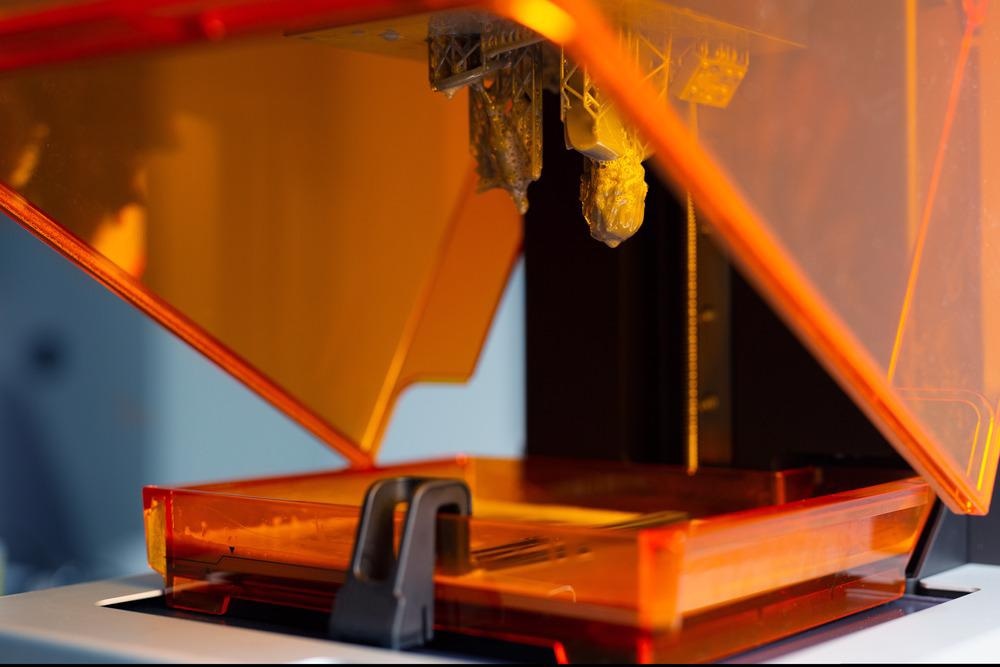
Study: Stereolithography-based additive manufacturing of polymer-derived SiOC/SiC ceramic composites. Image Credit: ZoranOrcik/Shutterstock.com
Background
AM has emerged as a viable manufacturing process for practically all types of materials in recent years. Stereolithography has emerged as a promising technology for producing large-scale parts with high precision, particularly in ceramics. Slurries of ceramic particles and acrylates are lightly cured in a locally resolved way in stereolithography, or more accurately in Lithoz GmbH's lithography-based ceramic manufacture (LCM) technology.
Because stereolithography is a light-based technique, the color and refractive index of the particles are important considerations throughout processing. Additionally, stereolithography-based ceramic AM typically necessitates a particle loading of at least 50% in order to sinter the ceramic green body into a thick structure.
SiC has certain intriguing features, such as excellent mechanical, thermal, and chemical resistance, which could make complex-shaped SiC-based components a viable option. In contrast to the traditional powder-and-sintering-based strategy for producing SiC ceramics, a polymer-derived ceramics (PDCs)-based approach can be explored to enable the manufacturing of SiC-based products.
Polysiloxanes, in particular, have proven to be effective in stereolithography for producing high-quality SiOC ceramic components. Polysiloxanes with modified photoactive moieties, such as thiols, acrylates, or vinyl groups, have been employed as resin in stereolithography for this purpose. As a result, various research on the use of fillers in the PDC-based stereolithography systems has been conducted.
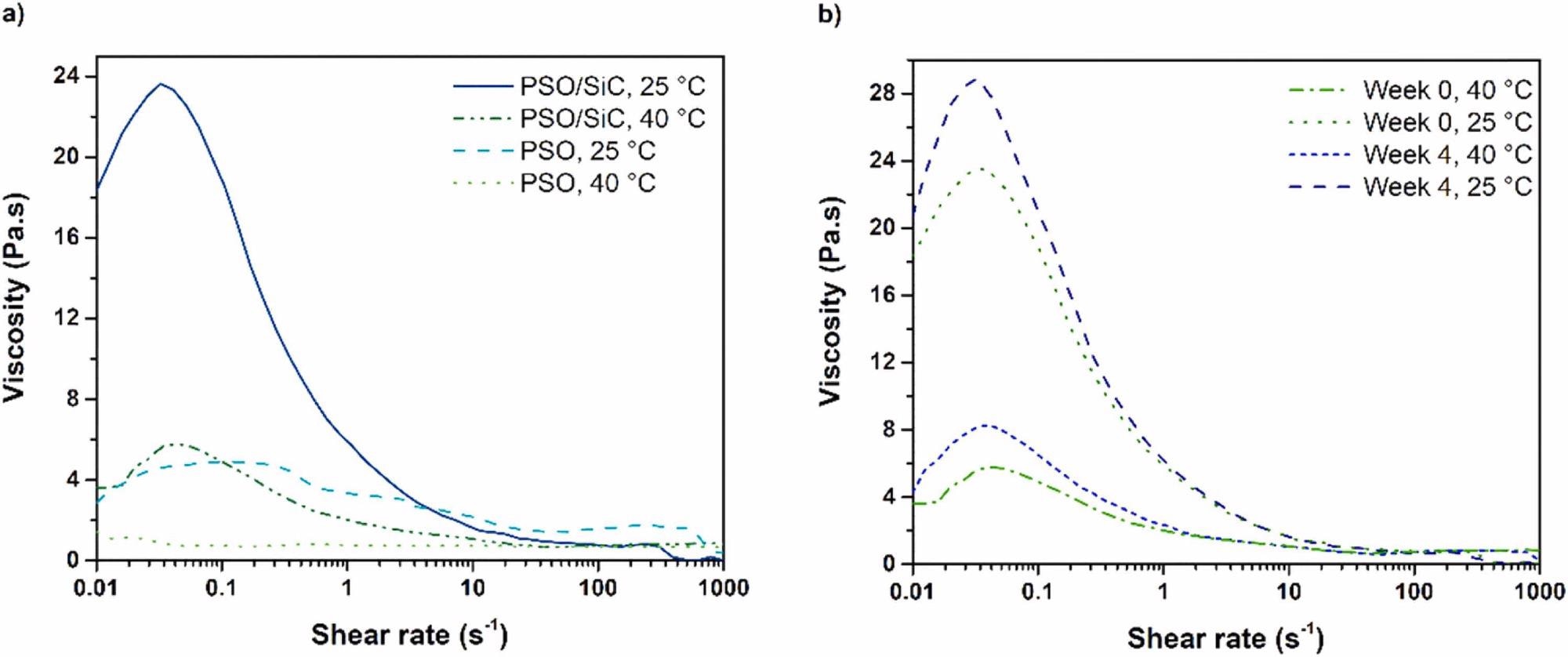
(a) Rheology flow curves of unfilled and 20 wt.% SiC-filled PSO resin at 25 and 40 °C, directly after synthesis; (b) Comparison of rheology flow curves of SiC-filled PSO resins directly after synthesis and after four weeks of storage at 25 and 40 °C, respectively. Image Credit: Brognara, L et al., Journal of the European Ceramic Society
About the Study
In this study, the authors designed a unique polymer-derived SiOC/SiC composite system appropriate for advanced geometric patterns achievable by lithography-based ceramic manufacture to overcome problems commonly encountered during AM of ceramics using the polymer precursor pathway.
The team demonstrated the preparation of highly efficient SiC-based materials, which were unavailable via conventional LCM. In this case, stereolithography was used to produce a new type of SiOC/SiC composite into complicated designs. Processes taking place during the various production steps, from polymer suspension synthesis to polymer-to-ceramic conversion, were explored in order to better understand the important aspects impacting the final material's qualities.
The researchers assessed the final SiC/SiOC composite ceramic in terms of mechanical, structural, and chemical properties to further investigate the possibilities of this new material. In terms of mechanical characterization, the emphasis was on the testing of bulk ceramic specimens, which was critical for the determination of the material's classification in contrast to conventional structural ceramics.
To suit the requirements of LCM, a modified specimen geometry was devised for the well-established Ball-on-Three-Balls-test. The composite was categorized as a structural ceramic due to its performance, and it laid the groundwork for the preparation of a new class of AM materials.
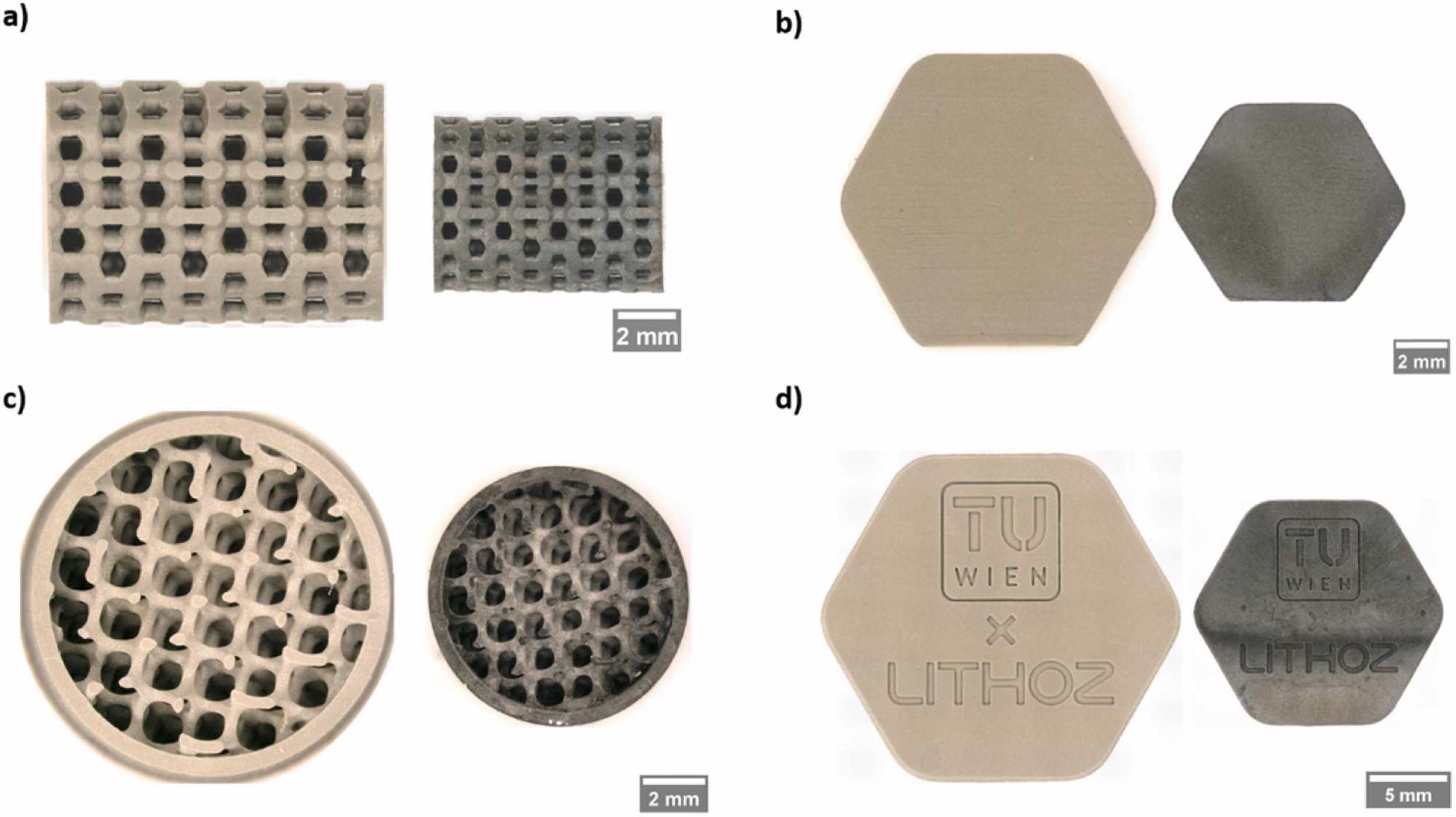
Printed and pyrolyzed PSO/SiC demonstration designs before (left) and after pyrolysis (right); a) wurtzite open lattice; b) hexagonal B3B-test specimen; c) enclosed lattice; d) hexagonal inscribed plate. Image Credit: Brognara, L et al., Journal of the European Ceramic Society
Observations
A second exothermic reaction could be identified in the pure SiOC sample starting at 1200 °C, which indicated that the material was degrading further. The SiC/SiCO sample had no exothermic signal over 1000 °C; however, there were two endothermic peaks at 1050 °C and 1400 °C. After an initial mass loss of 1.6%, the material started to degrade at 560 °C in the composite sample. At higher temperatures, there was a 1.3% increase in mass. At 670 °C, the SiOC sample displayed the first signs of degradation, which continued at higher temperatures.
The unfilled samples had a hardness of HV0.5 = 825 ± 46, but the SiC-filled SiOC material had a hardness of HV0.5 = 957 ± 85. The apparent density of the SiC-filled composites was 2.32 g cm-3, which equated to a relative density of 94.3%. A shrinkage of 24.2% in the XY plane and 28.6% in the z-direction was determined for the filled samples.
The photoreactive resin system containing 20 wt.% SiC had good viscosity, photocuring speed, and sedimentation resistance. SiC particles were well disseminated throughout the polymer-derived SiOC matrix after printing and pyrolytic conversion. The addition of particle SiC boosted handleability, lowered shrinkage, and dramatically increased critical wall thicknesses up to 5 mm when compared to an unfilled polysiloxane-based resin system. The biaxial Ball-on-Three-Balls testing approach provided SiOC/SiC composites with a typical strength of 325 MPa.
The prepared composites had high thermal stability in oxygen-free atmospheres and were expected to have high stability under air atmospheres, in addition to their excellent mechanical strength.
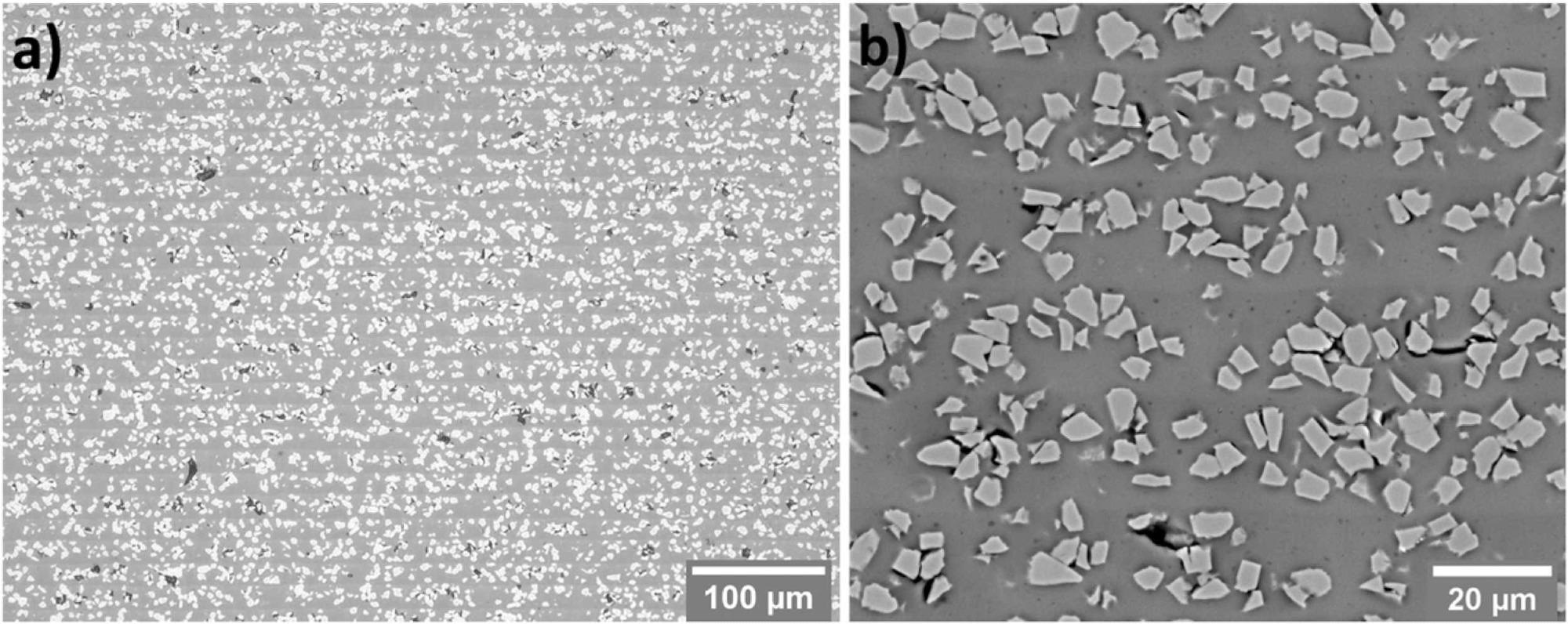
Ceramographic cross-sections of PSO/SiC composites: (a) light microscopy image; (b) backscattered electron microscopy image. Image Credit: Brognara, L et al., Journal of the European Ceramic Society
Conclusions
In conclusion, this study elucidated the development of a novel PDC-based, SiC-filled material system for LCM, with excellent sedimentation stability and viscosity. In both SiC-filled and unfilled preceramic systems, fast and full photocuring reactions were demonstrated. When compared to unfilled preceramic polymer systems, the use of fillers allowed to overcome the limitations of the PDC approach in terms of specimen geometry and critical wall thickness, as well as the production of components with a wide range of features sizes.
A new type of hexagonal specimen geometry was introduced for strength assessment of AM-based materials utilizing the Ball-on-Three-Balls-test. The authors believe that this work represents a significant step forward in the successful integration of SiC-based materials into the LCM process.
Disclaimer: The views expressed here are those of the author expressed in their private capacity and do not necessarily represent the views of AZoM.com Limited T/A AZoNetwork the owner and operator of this website. This disclaimer forms part of the Terms and conditions of use of this website.
Source:
Brognara, L., Fantini, M., Morellato, K., et al. Stereolithography-based additive manufacturing of polymer-derived SiOC/SiC ceramic composites. Journal of the European Ceramic Society (2022). https://www.sciencedirect.com/science/article/pii/S095522192200471X