A new paper in the journal Nanomaterials has demonstrated the development of novel 3D-printed polymer composites incorporating fillers such as graphene using a solvent-free process.
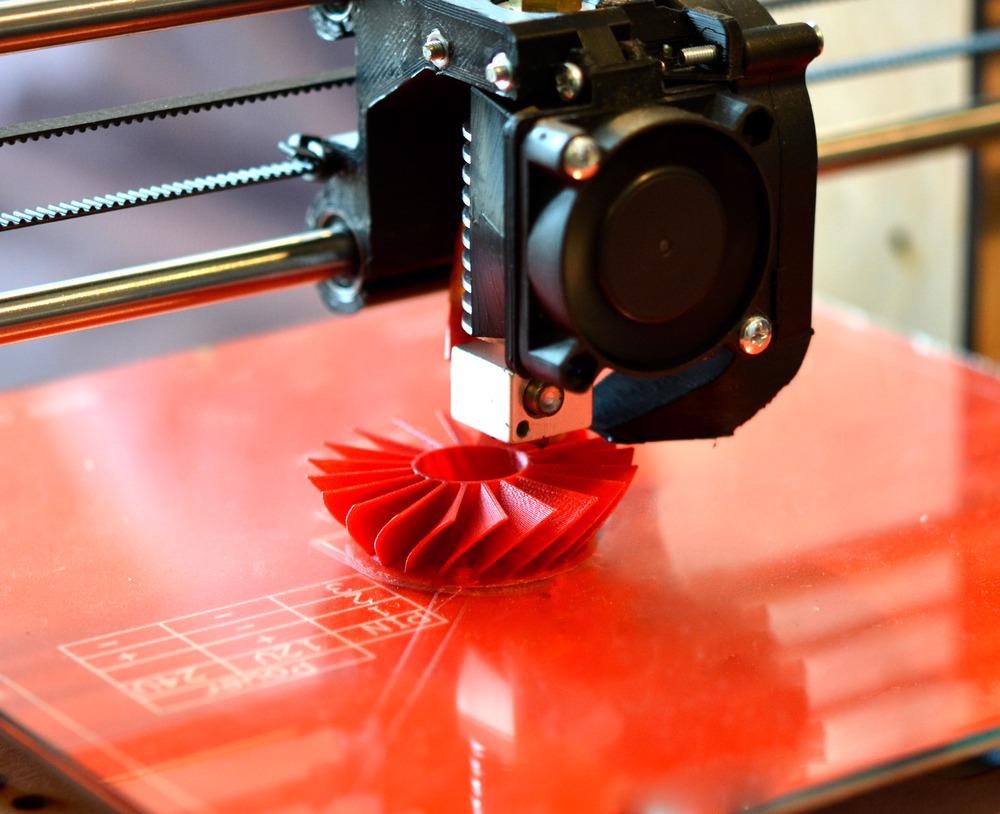
Study: Three Dimensional Printing of Multiscale Carbon Fiber-Reinforced Polymer Composites Containing Graphene or Carbon Nanotubes. Image Credit: MarinaGrigorivna/Shutterstock.com
3D Printing Polymer Composites
Manufacturing thermoplastic composites incorporating different multiscale reinforcements using 3D printing has been a focus of recent research in materials science. Embedding multiscale filler particles can enhance the properties of 3D-printed polymers, such as their mechanical properties, electrical conductivity, and thermal stability.
This area of research has found application in the field of additive manufacturing due to its potential to improve fused filament fabrication, a common 3D printing technology, by expanding the library of materials it can print products from. Intense research in the past decade has been conducted into the synthesis of new polymeric materials for a variety of industries.
Several nano- and micro-scale particles have been evaluated for their potential to impart polymeric formulations with enhanced properties in current research. Carbon-based materials, for instance, can improve mechanical properties such as stiffness, enhanced corrosion resistance, and weight reduction.
nanomaterials-12-02064" type="">
Extruded filaments of neat ABS, ABS/MCF, ABS/MCF/CNT, and ABS/MCF/GNP composites. Each composition is detailed in the inset. Image Credit: Residori, S et al., Nanomaterials
Micro fillers such as milled carbon fibers and nanofillers such as graphene nanoplatelets and carbon nanotubes have been investigated in studies over the past few years as polymer composite modifiers. Nanocomposites incorporating conductive nanoparticles have shown great promise in 3D-printed devices such as micro-batteries, electronic sensors, and micro-circuits.
Studies have demonstrated enhanced toughness, increased Young’s modulus, tensile strength, elastic modulus, and many other advantageous properties of polymer composites produced using fused deposition modeling. The incorporation of multi-walled carbon nanotubes, for instance, has a direct correlation between resistance change and concentration, with an enhanced response at reduced loads.
Other studies have carbon nanotubes at certain concentrations in different polymeric composites enhance their electrical conductivity. ABS composites incorporating dispersed graphene nanoplatelets possess increased thermal stability and elastic modulus but a decrease in strain at break and stress. Furthermore, improved interfacial shear strength has been observed in graphene nanoparticle-modified polypropylene.
Optimizing materials and production processes to maintain a balance between properties and processibility is crucial to designing modified polymeric formulations for the 3D-printed manufacturing of products and components. The use of multiscale particles has been extensively evaluated.
The Study
The authors have employed a novel solvent-free process to produce multiscale composite filaments. Direct dispersion of different scaled reinforcements in an ABS polymer matrix was investigated in the paper. Carbon-based filler materials (milled carbon fiber, carbon nanotubes, and graphene nanoplatelets) were used in the research in different ratios.
Common processing techniques such as twin-screw extruders and internal mixers were used to manufacture the multiscale composites for fused filament fabrication of components. The produced filaments have a diameter of 1.75 mm, standardized. Composite material properties after production via fused filament fabrication 3D printing were thoroughly evaluated in the paper to highlight reinforcement effects.

Schematic of the 1BA dumbbell and parallelepiped specimen (80 mm × 10 mm × 3.8 mm) (a), the arrangement of 3D-printed samples in Sil3r software (b), and detail of infill pattern (c). Image Credit: Residori, S et al., Nanomaterials
Study Findings
Several modifications to the properties of the polymer matrix were observed by the authors. Carbon nanotubes and graphene nanoplatelet fillers improved the modulus and strength of composites, but the addition of milled carbon fibers reduced the strain at break values. Nanofillers also improved the electrical conductivity of composites, with carbon nanotubes providing the best enhancement of this property.
The final sample density and properties were greatly influenced by the production process. Samples suffered from a loss of ductility of up to 65%, due to the presence of voids formed during 3D printing. An interesting observation made by the authors was that this effect was different in each composite. All composites with carbon nanotubes possess a low resistivity.
In addition, the authors presented both comparative and selective parameters to evaluate the optimal compositions. Compositions were evaluated based on processability and properties to elucidate their suitability for applications such as sensors and thermoelectric devices.

Electrical resistivity of CM and 3D-printed samples in different MCF and CNT contents. Image Credit: Residori, S et al., Nanomaterials
In Summary
In the new paper in Nanomaterials, the authors have demonstrated a novel process for producing multi-scaled polymer composites incorporating different carbon-based fillers. Printing filaments produced by this solvent-free direct dispersion method with fused filament fabrication was explored.
The process itself influences the final qualities and properties of printed materials. Alongside this, the properties differ depending on which filler was used in the samples. Samples showed good mechanical properties and electrical resistivity properties. Filler component ratio also had a large influence on properties. However, voids were created during fused filament fabrication, which can limit the performance of parts.
Overall, the paper has demonstrated a potentially advantageous multiscale polymer composite production process, which will prove beneficial for a number of applications in multiple industries, such as sensors and thermoelectric devices.
Further Reading
Residori, S et al. (2022) Three Dimensional Printing of Multiscale Carbon Fiber-Reinforced Polymer Composites Containing Graphene or Carbon Nanotubes Nanomaterials 12(12) 2064 [online] mdpi.com. Available at: https://www.mdpi.com/2079-4991/12/12/2064
Disclaimer: The views expressed here are those of the author expressed in their private capacity and do not necessarily represent the views of AZoM.com Limited T/A AZoNetwork the owner and operator of this website. This disclaimer forms part of the Terms and conditions of use of this website.