A paper recently published in the journal Materials demonstrated the application of magnetic shape memory alloys (MSMAs) in actuator design.
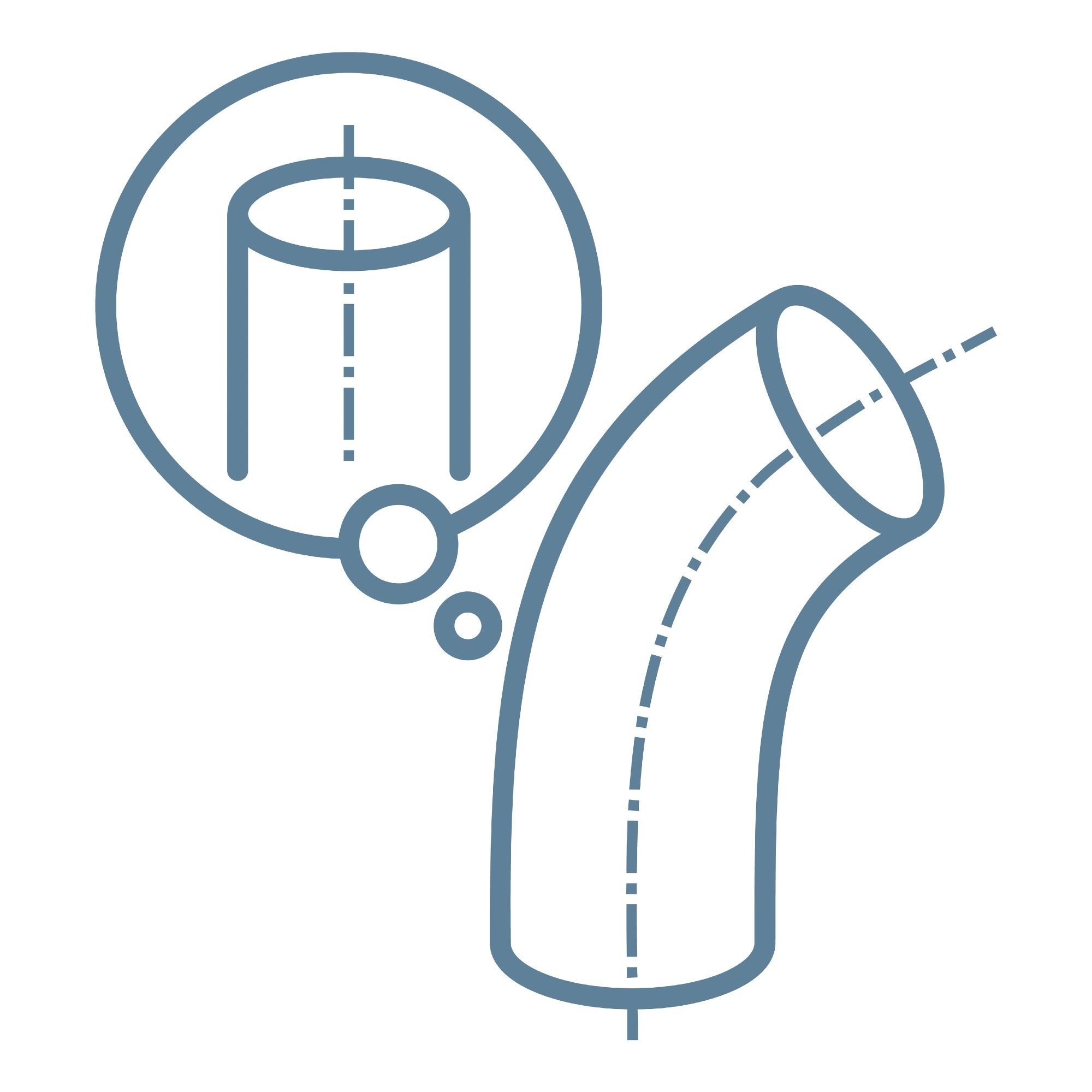
Study: Design and Control of Magnetic Shape Memory Alloy Actuators. Image Credit: Dmitry Kovalchuk/Shutterstock.com
Background
Smart materials, such as magnetostrictive materials and piezoelectric materials, are typically used as drive elements. For instance, piezoelectric crystals are currently utilized in high-precision actuators, such as actuators used in atomic force microscopes, owing to their very short response times, sub-nanometer resolution, and high-dynamic bandwidth, which make them suitable for very accurate and fat positioning tasks.
However, both magnetostrictive and piezoelectric materials display a weak deformation in the range of tens of micrometers, which is a significant disadvantage.
Shape memory alloys (SMAs) have gained considerable attention as a viable alternative to other non-conventional actuators in several disciplines owing to their large deformation compared to the other groups of smart materials. However, the dynamics of thermally-activated SMAs (TSMAs) are extremely weak, specifically during the cooling phase, with the step response time constants equal to almost a few seconds.
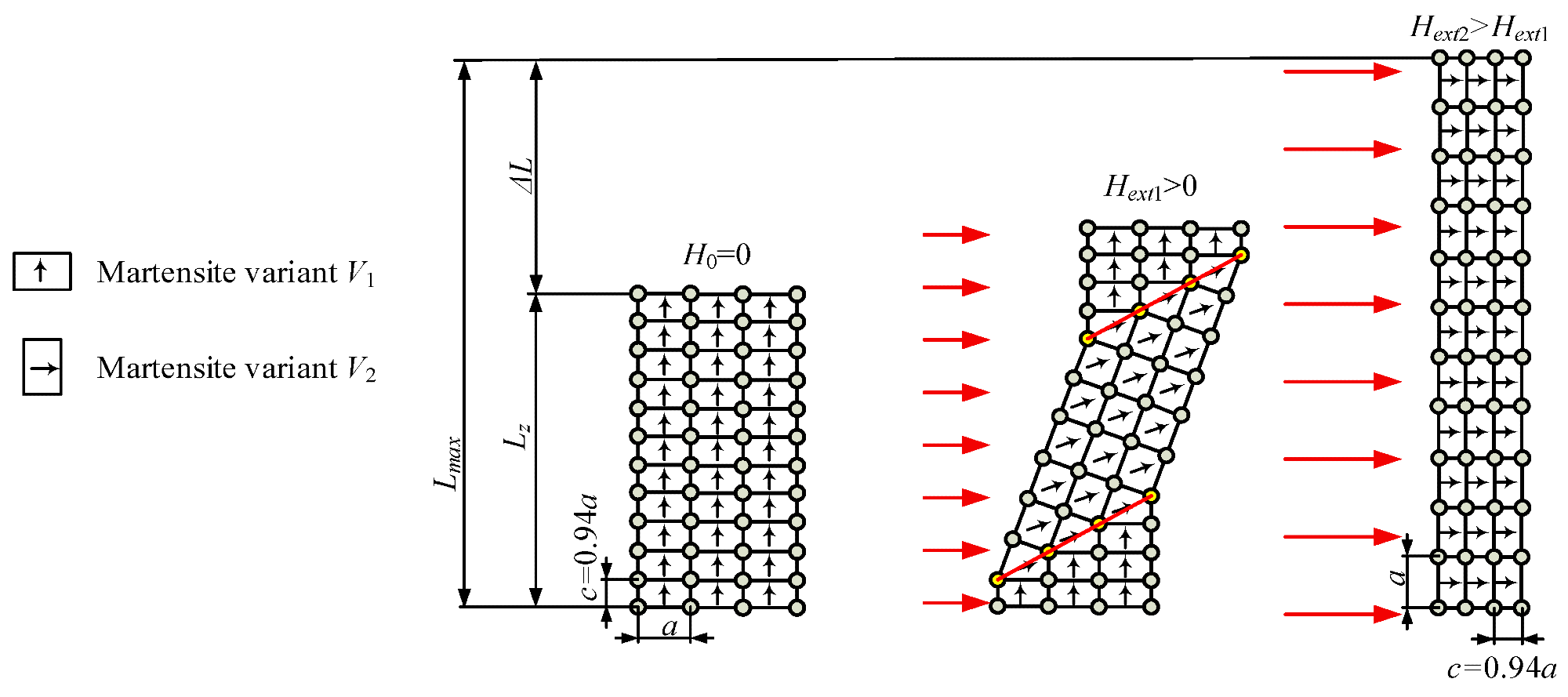
Deformation of a crystal lattice in a magnetic field, where a and c are the lengths of a single martensite cell (c = 0.94a). Image Credit: Minorowicz, B. et al., Materials
MSMAs, one special group of SMAs, can change their properties such as relative magnetic permeability and shape due to martensite cell rearrangement in the presence of an external magnetic field, leading to the generation of force and repeatable strains up to 6%. MSMAs also demonstrate higher operating frequencies than TSMAs, making them suitable in several actuation applications, specifically in low-displacement positioning devices. Additionally, the dynamics of MSMAs are considerably better than TSMAs.
Thus, MSMA-based actuators can potentially overcome the limitations of actuators based on magnetostrictive/piezoelectric materials and TSMAs by combining the strain scope of TSMAs and the dynamic response in milliseconds, which is comparable to the response time of magnetostrictive/piezoelectric materials.
Most smart material-based actuators have not been commercialized until now, owing to their nonlinear behavior, which increases the difficulty in regulating position through closed and open-loop control. The nonlinear behavior is attributed to hysteresis, which significantly influences the positioning accuracy.
The most common strategy used to overcome this problem involves initial hysteresis modeling, followed by the inversion of the hysteresis model, and finally using the inversed model as the compensator in a closed or open-loop control system.
Hysteresis modeling can be divided into two techniques. The first technique involves the mathematical description of the physical phenomena, while the second technique is based on the phenomenological theory. The generalized Prandtl-Ishlinskii model (GPI) is considered more effective than other hysteresis models as it can model various hysteresis shapes and can be analytically inverted easily.
The Study
In this study, researchers demonstrated the design, modeling, and nonlinear control of a newly proposed MSMA actuator. The actuator structure was composed of a 3 × 10 × 32 mm3 MSMA sample placed in an air gap in a magnetic core made from low-carbon steel.
One side of the actuator stand was equipped with a 0.43 N/mm stiff coil spring and push rod, while the opposite side with an HBM U9B force transducer with a ± 50 N measuring range. The push rod was passed through a polytetrafluoroethylene (PTFE) sleeve driven by a micrometer screw, which enabled the adjustment of the compressive force from 0 N to a blocking force of up to 6-7 N. Two coils were located on both sides of MSMA, and the actuator displacement was measured using an optical transducer.
The dynamics model of the MSMA actuator was proposed, and the transfer function of the model was derived. The GPI model was proposed for MSMA actuator hysteresis modeling as the model was suitable for modeling constant nonlinear hysteresis. The model was inverted (Inverse GPI) and used for hysteresis compensation in the control system. A special test stand was designed and prepared to experimentally analyze the performance of the MSMA actuator with compensation. An ILD-1700-2 triangular laser sensor was employed for actuator position measurements.
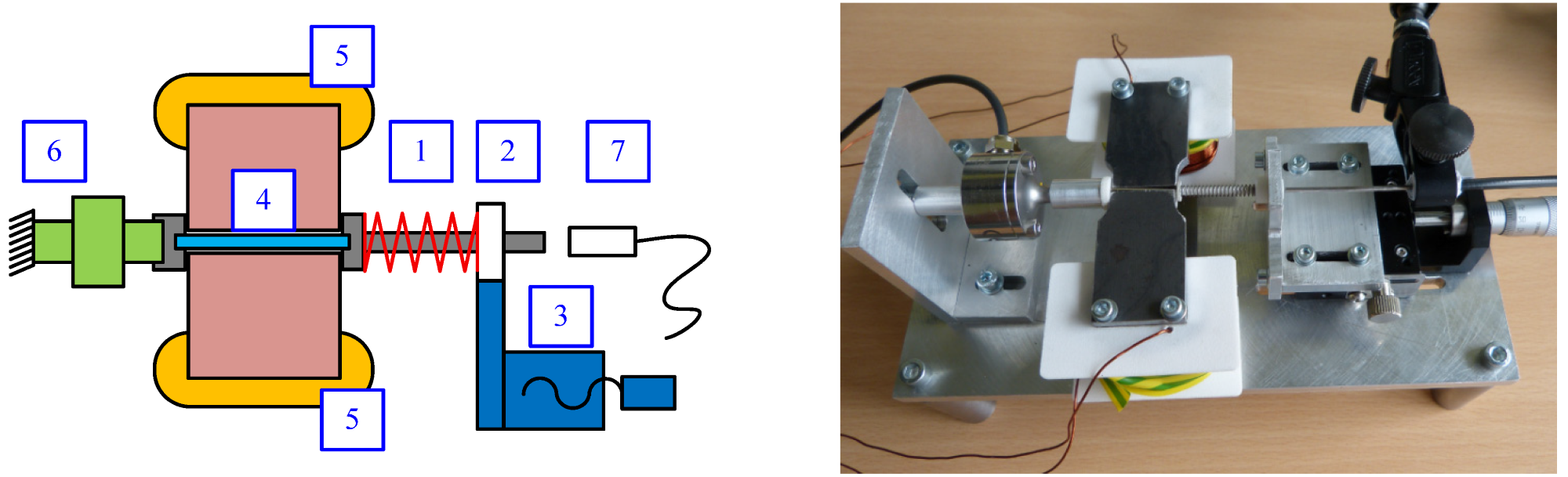
Design of the MSMA actuator used for preliminary studies: 1—coil spring, 2—PTFE sleeve, 3—table, 4—air gap with MSMA, 5—coils, 6—force transducer, 7—displacement transducer. Image Credit: Minorowicz, B. et al., Materials
Observations
An MSMA actuator was designed successfully with a blocking push force (Fb) of 70 N and a minimum repeatable strain of one mm. The developed actuator efficiently operated with 3 × 10 × 32 mm3 MSMA samples, which ensured an available operating range of up to one mm despite the great dynamics and deformation range of the samples.
The GPI model proposed for MSMA actuator hysteresis modeling and compensation enabled the linearization of input-output characteristics. The control of nonlinear objects was achieved through adequate compensation strategies and techniques.
Although a maximum of four A current was considered during the actuator design process, a lower excitation current will be necessary to generate the required flux density considering that the relative permeability of MSMA increases with deformation.
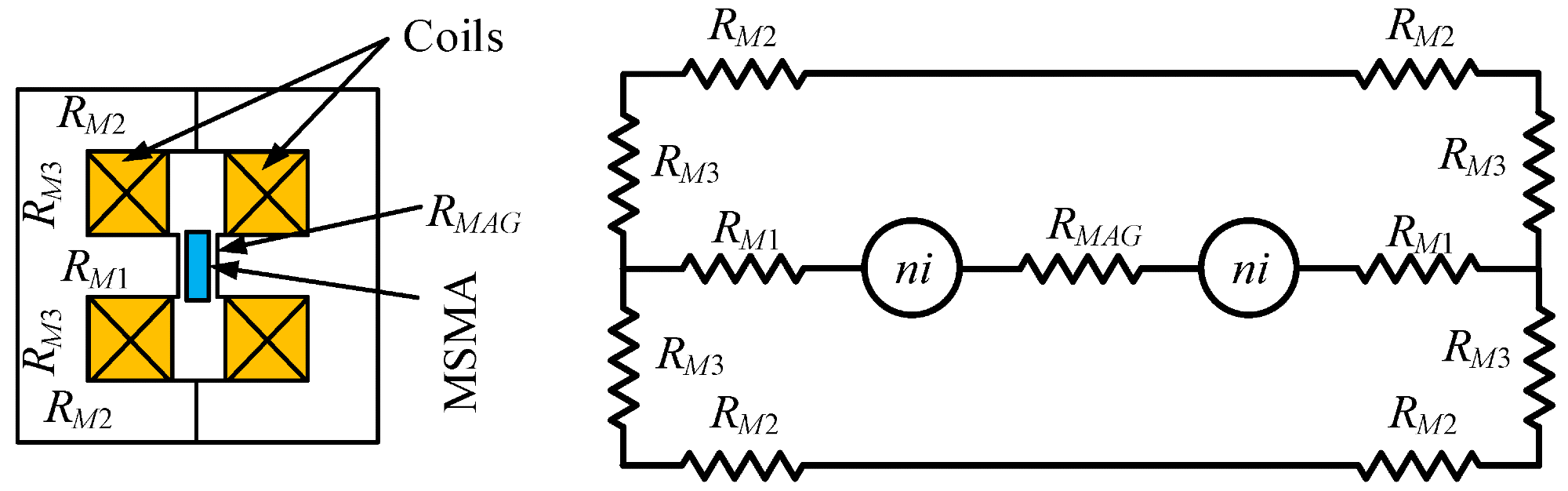
Equivalent magnetic circuit. Image Credit: Minorowicz, B. et al., Materials
Maximum elongation was obtained for three A current, which was significantly less than preliminary calculations. In the prepared actuators, the coil size was determined by current density and heat emission in wires. The compensated MSMA actuator demonstrated a positioning accuracy of ±2 µm.
The major limitations of the MSMA-based actuators were relatively low dynamics, hysteresis, and the need for using springs to return the transducer to its initial position. However, the actuators can still be utilized in several practical devices, specifically in positioning systems.
A considerably lower hysteresis modeling error was achieved using the GPI hysteresis model compared to the modeling errors reported in previous studies, which showed the effectiveness of the model.
To summarize, the findings of this study demonstrated the feasibility of using MSMAs in actuator design and MSMA-based actuators in designing a new class of high accuracy, innovative positioning transducers. In the future, the application of MSMA can be considered in the electrohydraulic or electro-pneumatic transducers and special brakes.
Disclaimer: The views expressed here are those of the author expressed in their private capacity and do not necessarily represent the views of AZoM.com Limited T/A AZoNetwork the owner and operator of this website. This disclaimer forms part of the Terms and conditions of use of this website.
Source:
Minorowicz, B., Milecki, A. Design and Control of Magnetic Shape Memory Alloy Actuators. Materials 2022. https://www.mdpi.com/1996-1944/15/13/4400