By Surbhi JainReviewed by Susha Cheriyedath, M.Sc.Jul 6 2022
In an article recently published in the journal Additive Manufacturing, researchers discussed immersion precipitation printing for the non-templated manufacturing of patterned fluoropolymer membranes.
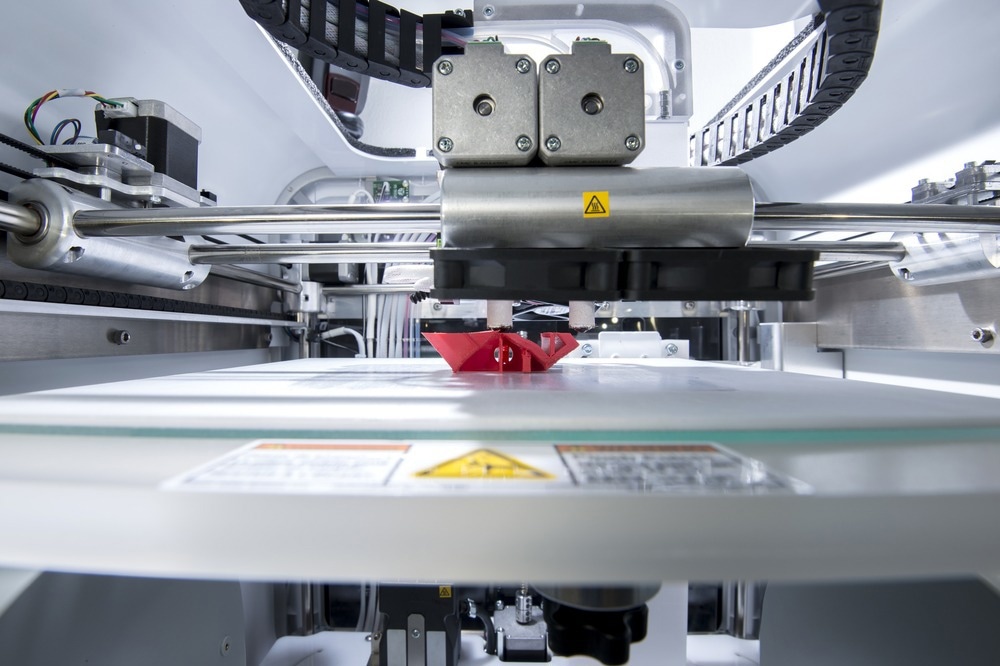
Study: Non-Templated Manufacturing of Patterned Fluoropolymer Membranes via Immersion Precipitation Printing. Image Credit: RomboStudio/Shutterstock.com
Background
The most popular polymeric membrane material is polyvinylidene fluoride (PVDF), which has good mechanical and thermal stability. Porous spacers are drawing greater scientific interest, generating studies emphasizing spacer design optimization to enhance fluid dynamics.
Patterning the membrane's active surface has recently been proposed as a method to do away with spacers. However, for nanoimprint lithography (NIL), the imprinting procedure calls for high pressure and temperature. The porosity of the patterned membrane is reduced by this compression at high temperatures. A polydimethylsiloxane (PDMS) replica template or mold must be directly cast with a bulk polymer solution according to PSµM.
Immersion precipitation printing (ipP), a material extrusion technique used in 3D printing, uses in situ precipitation during direct ink writing (DIW) to solidify low to moderately viscous inks. A novel potential for simultaneous DIW and nonsolvent induced phase separation (NIPS) exists with membrane manufacturing employing ipP. Notably, it has been found that both bi-continuous and spherulitic membranes have the same total porosity. It is crucial to optimize membrane permeability and separation efficiency, since it is anticipated that these processes will have a significant impact on the shape and size of the pores.
About the Study
In this study, the authors demonstrated a quick and easy method for the production of fluoropolymer membranes with a patterned porous surface via ipP. In order to create turbulent flow and hence lessen the membrane fouling, the patterns functioned as permeate spacers, which were normally introduced to a membrane separately. The permeate spacer's direct phase inversion during membrane manufacturing resulted in a porous morphology.
The team carried out studies on the pure water permeability of membranes with patterns or spacers made of a variety of fluoropolymer materials, including PVDF and synthetic dehydrofluorinated PVDF (dPVDF). The first study on the fabrication of patterned fluoropolymer membranes using ipP without the use of a template, mask, or glue is presented.
The researchers showed how to make various patterned structures of various sizes and geometries, as well as how to combine PVDF and dPVDF for patterned membranes. Scanning electron microscopy (SEM) was used to examine the microstructure of the manufactured membranes, and a dead-end stirred cell was used to evaluate pure water permeability. Porosity and equilibrium water content (EWC) was also determined.
Observations
The pure water permeability (A) was found to be slightly higher than that of dPb for the membrane that had a dPVDF base with PVDF patterns (dPbPw). Although the patterning was comparable in both, it was found that this value was significantly lower than A for dPbdPw. The unpatterned PVDF membrane, Pb, had an A of 549 ± 48 LMH bar-1 compared to the membrane PbdPw's 327 ± 3 LMH bar-1. A was 2070 ± 35 LMH bar-1 for the dPVDF membrane with no pattern (dPb), while A was 2714 ± 73 LMH bar-1 for the dPVDF membrane with dPVDF waves.
The A of the PVDF membrane with no patterns, Pb, was 549 ± 48 LMH bar-1, but after the addition of waves, A increased to 838 ± 79 LMH bar-1 for PbPw. The porosity increased from 44.5% ± 0.6% to 49.0% + 0.6%, but the EWC increased from 31.0% ± 0.5% for dPb to 35.0% ± 0.6% for dPbdPw. Fluoropolymer/DMAc inks had a total polymer content of 12.5 wt.%, while fluoropolymer/PVP/DMAc inks had a total polymer content of 16.25 wt.%. The membrane surface and permeate spacer were also found to have a close mechanical relationship.
Due to the PVDF's longer residence periods in isopropanol (IPA), the density of the base's cross-sectional length increased. Wave-like patterning, on the other hand, displayed an increase in permeability, which suggested that these patterns could one day operate as an integrated spacer. It was also found that wave-like patterning with similar polymers offered a more practical patterning solution and that PVDF and dPVDF together changed the membranes' shape.
Conclusions
In conclusion, this study proposed a non-template method for fabricating patterned membranes using ipP in IPA and phase inversion in de-ionized (DI) water. This technique was applied to the fabrication of dPVDF, PVDF, and hybrid membranes. Pyramid-like designs proved to be unworkable for PVDF, and thus both micro-and macro-patterning were thoroughly investigated.
The authors mentioned that the proposed straightforward ipP method exhibits promise as a workable substitute for the fabrication of fluoropolymer membranes where total control over pattern height, fidelity, and form are necessary.
They believe that the innovations from this study will make it possible to fabricate patterned membranes easily and without the use of a template, doing away with the necessity of a separate permeate spacer.
Disclaimer: The views expressed here are those of the author expressed in their private capacity and do not necessarily represent the views of AZoM.com Limited T/A AZoNetwork the owner and operator of this website. This disclaimer forms part of the Terms and conditions of use of this website.
Source:
Imtiaz, B., Sherrell, P. C., Barlow, A. J., et al. Non-Templated Manufacturing of Patterned Fluoropolymer Membranes via Immersion Precipitation Printing. Additive Manufacturing 103017 (2022). https://www.sciencedirect.com/science/article/abs/pii/S2214860422004092