By Surbhi JainReviewed by Susha Cheriyedath, M.Sc.Jul 15 2022
In an article recently published in the journal Materials Today Communications, researchers discussed the construction of a 3D printable material from recycled disposable masks after use.
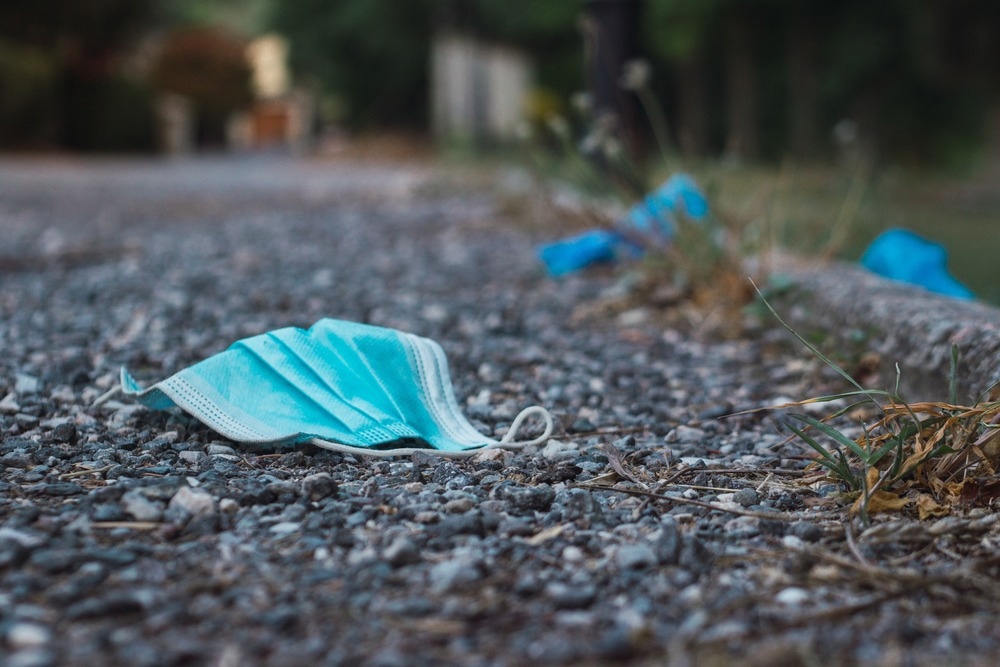
Study: Designing a 3D printable polypropylene-based material from after use recycled disposable masks. Image Credit: ancoay/Shutterstock.com
Background
The use of facial masks as the primary tool for reducing infection is a common practice increasingly seen across the globe in the aftermath of the Covid-19 pandemic. These "personal protective equipment" (PPE) items are often disposable and made of polymeric material. As a result, the environmental impact is not insignificant. Such trash must subsequently be treated in accordance with national legal requirements.
Recent research that examined the composition and recyclability of face masks has brought up additional issues due to the fact that they are constructed of numerous components that are difficult to recycle together. To efficiently recover polypropylene (PP) for recycling, a choice and shredding procedure were, therefore, necessary, and the expenses that resulted had to be taken into account.
However, because PP is regarded as a "commodity," it needs to be developed for high-added value items where the profit margin permits economically viable recycling. Undoubtedly, the extrusion method employed in 3D printing, also known as fused filament fabrication (FFF) and fused deposition modeling (FDM), is one of the qualifying industries. In this method, the cost of the filaments is significantly higher than the cost of the actual material. The development of filaments made from recycled materials is a key component of the expanding hunt for more environmentally friendly materials, which also affects additive manufacturing.
About the Study
In this study, the authors added different amounts of talc to the mixture in a small-scale extrusion machine to provide the polypropylene materials made from clean surgical masks with appropriate rheological and thermal qualities. This was not a wholly satisfying solution and so a first-use polypropylene copolymer was used in place of some of the masks. Two formulations that contained 35 and 50 wt.% of material derived from pristine masks and 20 wt.% of talc were used for 3D printing. The formulations were then scaled up using a lab twin-screw extruder and by recycling cleaned after-use masks (AUM) to mimic field recycling conditions as closely as feasible. The extruded pellets were eventually verified as extrusion material for 3D printing after being treated to make printing filament. Tensile specimens that were 3D printed were examined for their microstructure and mechanical characteristics.
In a small-scale device, various talc concentrations were applied to the clean masks' filtering material. Pristine masks or recycled sanitized after-use masks and first-use PP copolymer were utilized to build up two specific formulations in a lab twin-screw extruder. The pellets were then spun and verified as a material for 3D printing using industrial extrusion machinery.
The researchers compared the mechanical characteristics of the standard tensile specimens that were 3D printed together with a commercial 3D printable material in order to assess the quality of the 3D printed objects. After-use masks gathered from specialized bins in businesses and schools as well as brand-new masks from a single manufacturer were both used. In these locations, brand-new masks were dropped off at the entry and thrown away at the exit after use. A professional company cleaned the used PPE in accordance with the law.
Observations
According to the findings, it was not possible to create a material with adequate rheological properties and volumetric shrinkage from mechanically regenerated masks alone. Despite the improvement of the chosen performances, neither the mask-based materials nor those with talc added up to 40% of the weight were sufficient. First-use polypropylene copolymer partially replaced the number of masks in the formulation to overcome this restriction.
The obtained materials were determined to be appropriate for the 3D printing technique when the rheological and shrinkage characteristics were taken into account, and a filament with a nominal diameter of 1.75 mm was successfully generated using AUM-based material. While the filament with 50 wt% of AUM had a variability of 6% and an average diameter of 1.54 mm, the filament with 35 wt% of AUM had a section variability of 9%. These filaments caused a filling percentage variation of -20 and -25%, respectively, among the specimens for the mechanical tests and the fully filled geometry.
Mechanical tests for both formulations revealed stiffness that was nearly twice as high and strength that was exactly on par with that of the commercial 3D printable material. The commercial material's variable quality and quantity of filler, which was further supported by a variation in the physical behavior of the perimeter upon breaking, was primarily responsible for the variance in toughness.
Conclusions
In conclusion, this study elucidated mask material recovery for 3D printing applications to recycle potentially harmful wastes. Two formulations were created using pristine (M) and sanitized AUM.
Both AUM-based formulations were suitable for industrial testing and even allowed for the speculation of a higher mask content. For the first time, acceptable filaments for the creation of extruded 3D printed items were created using disposable filtering masks.
The authors mentioned that the results of this study are meant to serve as a starting point for the future creation of novel formulations to valorize trash with such significant environmental impact.
More from AZoM: Can Machine Learning Reduce AFM Uncertainty?
Disclaimer: The views expressed here are those of the author expressed in their private capacity and do not necessarily represent the views of AZoM.com Limited T/A AZoNetwork the owner and operator of this website. This disclaimer forms part of the Terms and conditions of use of this website.
Source:
Battegazzore, D., Cravero, F., Bernagozzi, G., et al. Designing a 3D printable polypropylene-based material from after use recycled disposable masks. Materials Today Communications 103997 (2022). https://www.sciencedirect.com/science/article/abs/pii/S2352492822008510.