A paper recently published in the journal Engineering Fracture Mechanics analyzed the interlayer fracture behavior of layered concrete to prevent weak interlayer zone (ILZ) formation.
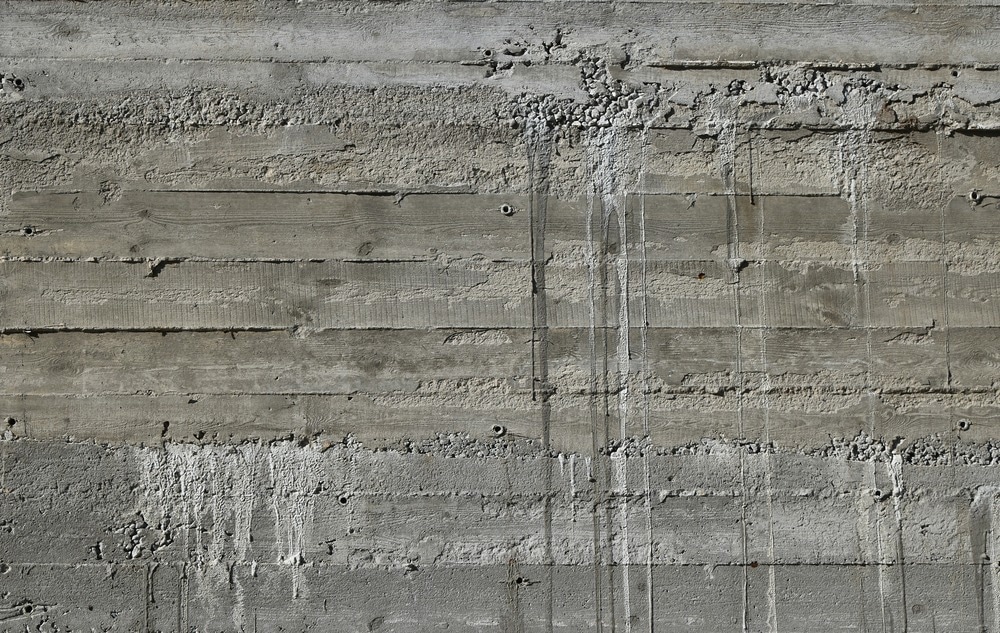
Study: Interlayer fracture behaviour of functionally layered concrete. Image Credit: Breaking The Walls/Shutterstock.com
Background
Additive manufacturing (AM)/three-dimensional (3D) printing and automatization can facilitate the transition from conventional monolithic concrete forms towards more effective structural composites or functionally-graded elements, as these advances allow efficient fabrication of functionally-layered concrete (FLC).
In FLC, material layers with various mix compositions can be tailored to specific thermal or mechanical performance requirements of the layered concrete to use the concrete more efficiently, leading to cost savings and a reduction in the carbon dioxide footprint in the environment.
For instance, a lower cement lightweight concrete core in an FLC can improve the thermal performance or reduce the dead load of the layered concrete. Similarly, a higher cement mix can be utilized as the outer layer to improve the stiffness or durability of the concrete.
However, the deposition of various wet-on-hardened and wet-on-wet concrete layers induces the risk of a weak ILZ between two adjacent concretes. The ILZ is susceptible to cold joint formation and introduces a weak zone in the concrete depending on the mix compositions and casting conditions. Additionally, the fresh-state behavior and rheology and the surface quality/character of the wet layers also influence the ILZ behavior.
In 3D concrete printing applications, the ILZ is often formed between the adjacent concrete mixes with the same compositions and different print delay times. The deposition/pour delay times and mix compositions can potentially interact to influence the ILZ behavior of the FLC.
Thus, successful production of FLC requires an understanding of wet-on-wet casting of multi-layered elements with different concrete mixes and time delays. Specifically, the evaluation of the fracture performance of the IL transition zone is necessary to understand the ILZ behavior of FLC.
The Study
In this study, researchers assessed the interlayer fracture properties of single- and multi-mix concrete samples cast in layers and evaluated the effect of different pour/print delay times between deposition of each layer on the ILZ behavior of these samples to understand the interlayer bond compatibility and strength of functionally-graded multi-mix and single mix concretes prepared with different print delay times.
Three concrete mix compositions were selected to prepare the functionally-graded multi-mix and single mix concrete cubes. These compositions included a dense and high strength concrete/cement intensive concrete/Mix A served as a durability material or stiff outer layer material, a low strength lower cement mix/Mix B as a wall core or slab element to reduce the carbon dioxide footprint, and finally a low strength/lightweight mix/Mix C as a core material to improve the thermal properties and reduce the self-weight.
The layered concrete specimens were fabricated using a conventional casting method by casting layers with various base mix combinations and were compared with analogous specimens with layers of the same base mix compositions or non-layered single homogenous specimens.
Single mix cubes were prepared by combining mix C-C, B-B, and A-A, while the multi-mix cubes were produced by combining mix B-C, A-C, and A-B. Non-layered homogenous cubes were prepared using mix C, B, and A. Overall, wedge splitting tests were performed on 81 layered cube samples cast using different pour delay times and concrete mix combinations.
200 × 200 × 245 mm concrete cubes with 30 mm deep notches that were split into two equal parts were fabricated using the three selected concrete mixes to perform the wedge splitting test to deduce the fracture behavior of the layered concretes and the influence of four different pour delay times of 0.5, 1, 2, and 4 h was investigated.
The hardened and fresh state behavior of the base mixes, including the time-dependent rheology, consistency, and setting, was characterized and quantified. The fracture parameters such as the softening tail energy, initial softening energy, pre-peak softening energy, total fracture energy, and notch tensile strength of the single mix and multi-mix specimens were compared.
Observations
Layered concrete samples with layers of different and same base mix compositions deposited in different print delay times were prepared successfully. In the single mix samples with various pour delay times, the critical pour delay time after which the cold joint formations/interlayer fractures were observed was primarily influenced by the concrete mix composition.
For instance, the low strength and low strength/lightweight concrete mixture demonstrated a higher critical pour delay time than the high strength concrete mix. However, both low-strength mixes displayed similar critical pour delay times due to similar water to cement ratio and cement type in the mixtures.
The final and initial setting for Mix A was observed at 4.9 and 4.2 h, respectively, and at 6.8 and 6.0 h for both Mix C and Mix B. Thus, the initial and final setting/open time of all base mixtures was above the maximum pour delay time of four h.
However, cold joint formations were observed at one h pour delay for single mix specimen A-A and at 0.5 h pour delay for multi-mix specimen A-B, which indicated that the cold joint formation was not correlated to the final and initial setting time of the mixtures.
The critical pour delay time of multi-mix specimens was prolonged compared to the analogous single mix specimens when Mix A was combined with Mix C or Mix B. However, no increase in the pour delay time was observed in multi-mix specimens where the low strength/lightweight mix/Mix C was combined with low strength mix/Mix B.
Fracture parameters of the multi-mix specimens were significantly influenced by the base mix compositions and pour delay time. Thus, the performance of fracture parameters of multi-mix samples differed from the performance of the comparable lower grade layered single-mix specimens. Moreover, better fracture properties were observed compared to the base mixes for specific multi-mix compositions and delay times.
A shorter pour delay time did not result in a better interlayer fracture performance for all samples. For instance, multi-mix combinations where a low strength/Mix B or a low strength/lightweight/Mix C was combined with the high strength mix/Mix A displayed a higher total fracture energy and notch toughness for one h pour delay compared to 0.5 h pour delay.
The total softening energy of all multi-mix samples was higher compared to the weaker single mix specimens for pour delay times between one and four hours. However, lower softening energies were observed in all multi-mix combinations at 0.5 h pour delay time.
Taken together, the findings of this study demonstrated that controlled fabrication processes, specifically the pour/print delay times and judicious mix compositions, can mitigate the formation of weak ILZs.
Disclaimer: The views expressed here are those of the author expressed in their private capacity and do not necessarily represent the views of AZoM.com Limited T/A AZoNetwork the owner and operator of this website. This disclaimer forms part of the Terms and conditions of use of this website.
Source:
Maier, M., Lees, J. Interlayer fracture behaviour of functionally layered concrete, Engineering Fracture Mechanics 2022. https://www.sciencedirect.com/science/article/pii/S0013794422003988?via%3Dihub