Manufacturing self-cleaning fabrics is a key focus of research in the textiles industry currently. Now, a new paper published in Polymers has investigated the control of microscopic features of self-cleaning textiles using common 3D printing technologies.

Study: Influence of Printing Parameters on Self-Cleaning Properties of 3D Printed Polymeric Fabrics. Image Credit: Parmna/Shutterstock.com
Self-Cleaning Fabrics
The textiles industry is a fast-growing industry, valued at $993.6 billion in 2021. The manufacture of fabrics for sectors such as furniture and clothing is a key economic activity in many countries worldwide.
Innovation in the textiles industry has led to multiple technological developments in recent decades, including enhanced functional characteristics such as waterproofing, anti-microbial, anti-static, and self-cleaning.
Self-cleaning fabrics are attractive for many industries. Inspired by nature, these fabrics have become a key focus in the textiles and material sciences sectors. Several biological structures have inspired innovation in this area, such as insect wings, fish scales, lotus leaves, and rice plants.
Self-cleaning fabrics are advantageous for a range of products, improving their aesthetic appeal and having a range of economic and environmental benefits. These advanced textiles help to maintain a clean and contaminant-free surface, decomposing stains and chemicals and avoiding the proliferation of dust and grime on the material.
These fabrics also provide benefits such as water, energy, and time savings due to reduced washing requirements over their lifetime. Finishing methods have been extensively researched in this area. Aside from their potential for the clothing industry, self-cleaning textiles can significantly benefit the medical sector.

Layer height and extruder width definition. Image Credit: Atwah, A. A. et al., Polymers
Methods for Producing Self-Cleaning Fabrics
In recent decades, several methods have been developed to produce these innovative fabrics. Conventional methods have included the creation of rough micro-nano-scaled structures on the surface of low surface energy materials. Other methods have altered low surface energy materials, enhancing their roughness.
Several methods have been explored for the development of photolytic and hydrophobic fabrics, including spin coating, wet chemical synthesis, sol-gel methods, spray coating, chemical etching, LBL, and electrospinning. However, these methods can be hindered by the use of harsh chemicals and complex processing requirements.
Investigating the structural features in self-cleaning fabrics is key to understanding their behavior and the efficient design of textiles with this functionality. These key features and properties include wettability, porosity, and surface roughness. However, currently, there is a lack of study on the control of microscopic features in these fabrics, which hinders further research in this field of textiles design.
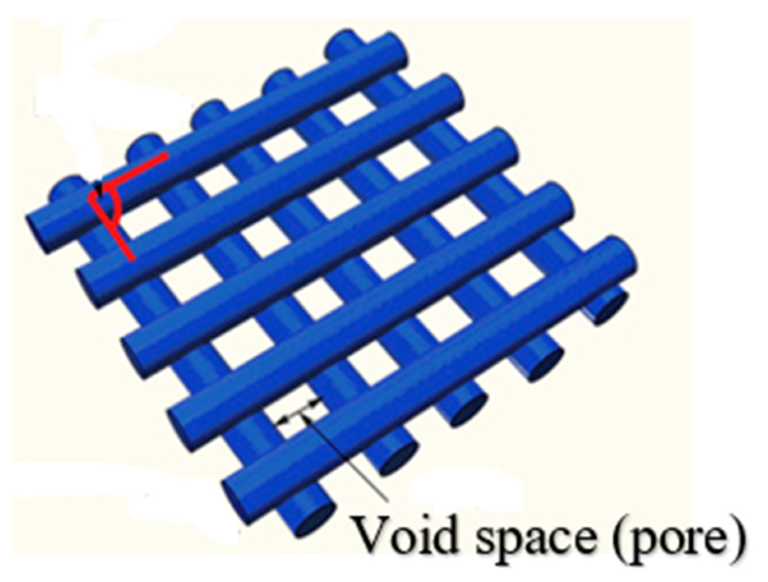
The porosity of textile fabrics. Image Credit: Atwah, A. A. et al., Polymers
The Study
The paper has focused on the aforementioned research gap to improve the design of fabrics with self-cleaning properties. Control of fabrication parameters during manufacturing is a key area of research that has so far gone underserved in the body of research.
It is difficult to control fabrication parameters using traditional manufacturing techniques currently in use. This challenge facilitates the development of surface coating methods to imbue most fabrics with self-cleaning properties.
Currently, there is an increasing focus on additive printing, otherwise known as 3D printing, due to its advantages such as free-form design and reduced material waste. 3D printing holds vast potential for the manufacture of self-cleaning materials due to its superior control of fabrication parameters compared to conventional manufacturing methods.
This enhanced control makes it possible to control the structure of materials at the microscopic, woven fabric level to produce fabrics with desirable properties. Amongst the various 3D printing methods, fused filament fabrication has exciting potential for the fabrication of functionalized fabrics.
The team used fused filament fabrication in the research to produce self-cleaning fabrics for the textiles industry. Several parameters were investigated by the authors, including layer height, orientation angle, and extruder width. The authors used these parameters to control the microscopic self-cleaning properties of fabric samples.
Three different flexible thermoplastic materials were used to produce self-cleaning fabrics in the research. These were TPU 98A, TPC flex45, and TPE felaflex. A pre-set criterion was employed to quantify self-cleaning characteristics of the materials.
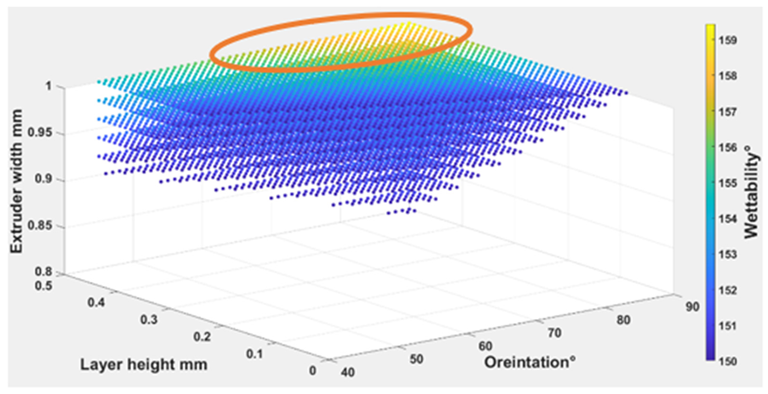
The possible combination of the printing parameters range for (O), (LH), (EW) to achieve the best self-cleaning performance for wettability. Image Credit: Atwah, A. A. et al., Polymers
Various parameters were adjusted and combined to demonstrate their effect on properties such as contact angle of wettability, surface roughness, and material porosity. The optimal self-cleaning fabric surface was investigated by adjusting a combination of layer height, extruder width, and two printing orientations. Modeling was employed to identify optimal 3D printed fabric self-cleaning properties.
The authors concluded that printing parameters have a significant effect on the final microscopic properties of self-cleaning fabrics. Adjusting the combination of extruder width and layer height vastly impacts the material’s surface roughness, wettability, and porosity. Porosity changes were also dependent on the material. Out of the three materials, TPE displays the optimal self-cleaning capabilities.
The Future
Overall, the paper has demonstrated the impact of adjusting printing parameters on self-cleaning properties, with experimental results agreeing with models. The results of the research can be used in the future to estimate printed fabric’s self-cleaning abilities, providing significant benefits for the further development of these important materials.
Further Reading
Atwah, A. A. et al. (2022) Influence of Printing Parameters on Self-Cleaning Properties of 3D Printed Polymeric Fabrics Polymers 14(15) 3128 [online] mdpi.com. Available at: https://www.mdpi.com/2073-4360/14/15/3128
Disclaimer: The views expressed here are those of the author expressed in their private capacity and do not necessarily represent the views of AZoM.com Limited T/A AZoNetwork the owner and operator of this website. This disclaimer forms part of the Terms and conditions of use of this website.