A new paper published in the journal Polymers investigates the tribology of carbon fiber reinforced polymer composites (CFRPS,) an emergent material solution to meet the demands of several industries. The work has been conducted by scientists from the Technical University of Cluj-Napoca in Romania.

Study: Experimental Investigation of the Tribological Behaviors of Carbon Fiber Reinforced Polymer Composites under Boundary Lubrication. Image Credit: GO BANANAS DESIGN STUDIO/Shutterstock.com
Carbon Fibers
Carbon fibers were first produced in the mid-nineteenth century, with considerable progress in their development and industrial applications made in the latter half of the twentieth century. Defined as fibers with at least 92% carbon content by weight, they possess excellent mechanical, physiochemical, chemical, and thermal properties.
Beneficial properties of carbon fibers include their superior tensile and flexural properties, low density, and high chemical and thermal stability in the absence of oxidizing agents, superior creep resistance, and high electrical and thermal conductivity. Fibers containing in excess of 99% carbon are called graphite fibers.
Multiple industries exploit the properties of carbon fibers, with the carbon fiber industry rapidly expanding in recent decades to meet their demands. They are used in the aerospace industry, automobile construction, military applications, and structural and non-structural elements in construction. Carbon fibers are utilized in medical items, pressure valves, cars, sports items, and drilling components.
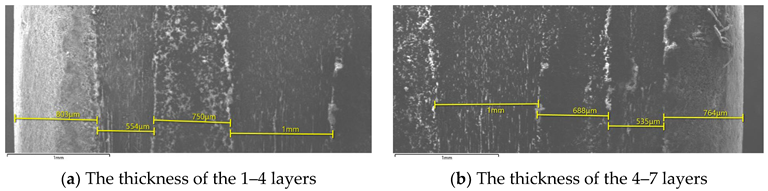
SEM images of the layers that make up the tested composite material. Image Credit: Birleanu, C et al., Polymers
Carbon Fiber Reinforced Composites
Recent research over the past few decades has seen the development of several advanced and innovative carbon fiber-reinforced composite materials. In the automotive industry, for instance, these composites offer the benefits of low weight and enhanced aesthetic appeal, and they are used in elements such as doors, bumpers, and bonnets.
The microstructures of carbon fibers are the main reason that fibers and their composites have found wide commercial viability in several industries. Moreover, their length, orientation, and concentration in composites are features that govern their efficacy in a wide range of industrial applications.
The superior damping performance of carbon fiber reinforced composites makes them incredibly useful materials for applications such as high-speed drive shafts, robotic arms, and machine tool shafts. Through this damping effect, composites can dissipate vibrations effectively, improving the durability of these technologies.
Carbon fiber reinforced composites are typically prepared by carbonizing a liquid precursor-impregnated fiber platform with carbon-containing gas precursors such as methane. The resulting materials possess a number of beneficial properties, such as high specific strength, low thermal expansion coefficients, toughness, stiffness, and self-lubricating capacities. Additionally, they possess enhanced refractory properties.
Some studies have been conducted recently on the tribological properties of carbon fiber-reinforced composites. Stick-slip phenomena are undesirable in many engineering applications, causing wear, vibration, noise, energy loss, and damage to components. Wear and friction in composites depend on multiple parameters such as sliding speed, normal load, friction surface roughness, and lubrication.
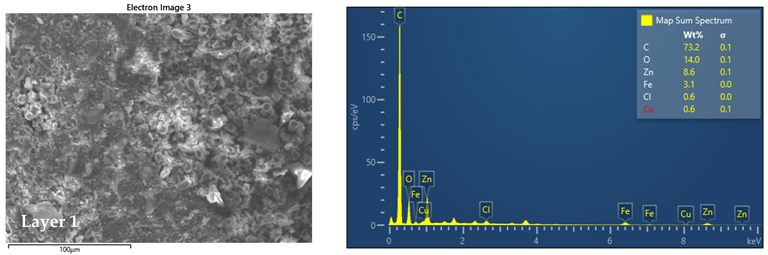
SEM images and EDS analysis of layer 1. Image Credit: Birleanu, C et al., Polymers
The Study
Currently, there is a lack of knowledge on the tribological properties of CFRPs, though pioneering studies have revealed significant factors that govern wear and friction behavior.
The current paper in Polymers has investigated wear and friction in unidirectionally oriented CFRPs. Tribological behavior with respect to the sliding direction of composites under dry lubrication and boundary conditions has been thoroughly studied in the research.
Tribological experiments were performed at a range of normal loads from 20-80 N at room temperature. Speeds of 0.4 to 2.4 m s-1 were used during the tests. Experiments were performed over different time periods to assess the material samples’ tribological behavior.
The tribosystem’s wear and friction mechanisms were analyzed and interpreted, along with the wear-induced morphological characteristics and resultant wear residues. Furthermore, the friction time’s influence on the composite materials’ friction coefficients was examined under stationary and moving conditions (using a spinning disc).
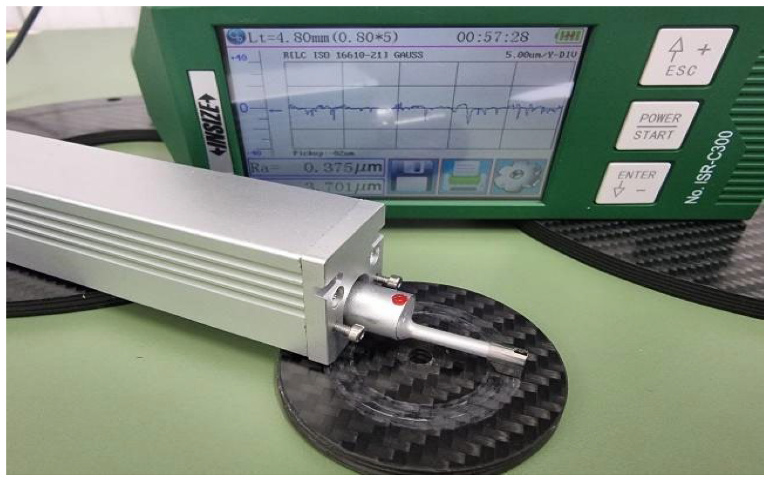
Experimental set-up for roughness measurements using the INSIZE ISR—C300 device. Image Credit: Birleanu, C et al., Polymers
Research Conclusions
It was revealed that both sliding speed and applied load contribute significantly to controlling wear and friction. Additionally, the samples all possessed a predominantly worn surface due to abrasive wear. In the disc experiment, intermittent loading caused wear effects. Furthermore, the authors concluded that analyzing resulting wear debris is difficult. In the spinning disc experiment, comparatively higher wear values were observed compared to the stationary pin experiment.
Carbon fiber reinforcement has a notable effect on the wear and friction characteristics, with experiments demonstrating the lowest observed wear limit and friction coefficient. Additionally, the hardness and elastic modulus of the samples is considerably enhanced.
There seem to be two factors that contribute to reducing polymer wear. Firstly, fibers support a proportion of the applied load when exposed to sliding surfaces. Secondly, fiber reinforcements reduce stress between roughness peak contacts by smoothing the counterface’s surface.
In summary, the research revealed several important findings on the tribological behavior of CFRPs, which provides crucial information for future studies on these industrially important materials.
Further Reading
Birleanu, C et al. (2022) Experimental Investigation of the Tribological Behaviors of Carbon Fiber Reinforced Polymer Composites under Boundary Lubrication Polymers 14(18) 3716 [online] mdpi.com. Available at: https://www.mdpi.com/2073-4360/14/18/3716
Disclaimer: The views expressed here are those of the author expressed in their private capacity and do not necessarily represent the views of AZoM.com Limited T/A AZoNetwork the owner and operator of this website. This disclaimer forms part of the Terms and conditions of use of this website.