In a paper published in the journal Additive Manufacturing Letters, researchers demonstrated the use of additive manufacturing (AM) in the fabrication of flexural sensors for assessing the influence on the sensor output by the sensor geometry, thus highlighting the significance of geometrical design consideration in the fine-tuning of flexural sensors for AM.
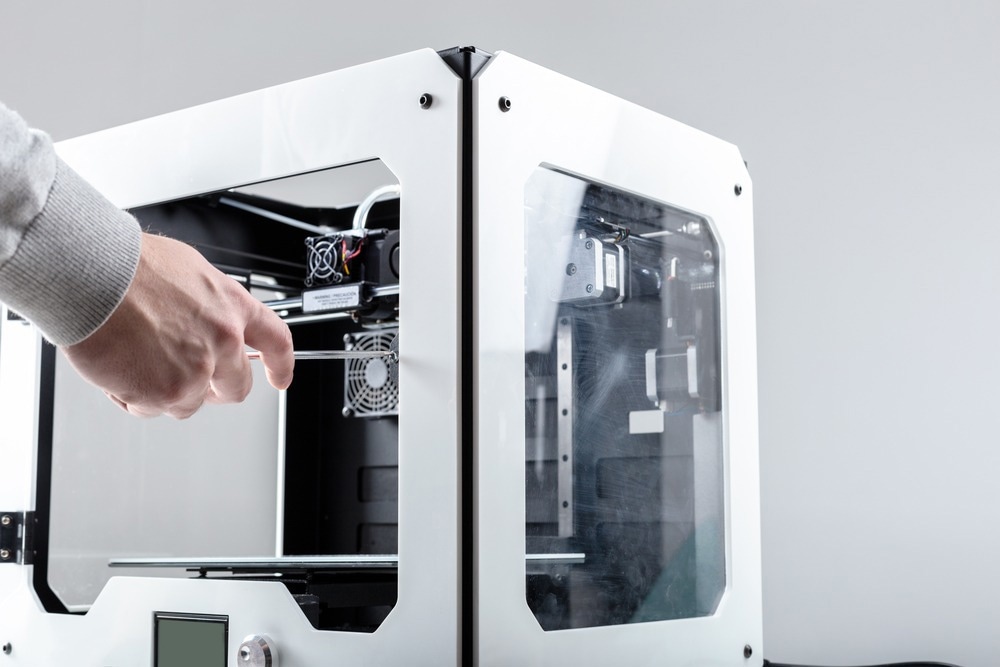
Study: Conductive Compliant Mechanisms: Geometric tuning of 3D printed flexural sensors. Image Credit: FabrikaSimf/Shutterstock.com
Background
Additive Manufacturing (AM) has created new possibilities for sensors since the manufacturing technology allows for customization in specific applications. This property has lately been used in applications such as soft robotics and wearables. Different AM techniques offer unique benefits in terms of printing rates, accuracy, and available materials. Numerous studies have been conducted to improve the sensors' performance by modification of the material constituents. Nonetheless, little is known about the basic aspects of the influence on the sensor output by the sensor shape.
Conductive polymer composites (CPCs) make for an appealing choice of material for sensors that can detect large amounts of strain. Because of the high entanglement of the long carbon nanotubes (CNTs), CNT-based compounds are often applicable in high-strain operations. Another substance used to make CPC sensors is conductive carbon black (CCB). Pure strain values are simple to interpret, but several flexural sensor applications may involve a combination of compressive and tensile stresses encountered during bending. Although it is simple to comprehend in terms of pure strain, it is more difficult to understand in terms of the combination of tensile and compressive stresses that occur during beam bending.
About the Study
In this study, the team produced three sensors featuring different deforming measurement regions and tested them to assess the influence of sensor geometry. They aimed to demonstrate how the flexural sensor geometry may be enhanced throughout the design process. Comparison of the three sensors was carried out on an experimental test apparatus that allowed for cyclic sensor loading while measuring their resistance.
To achieve a stable filament and adequate dispersion, the conductive filament was prepared in two steps. The stabilization of the extrusion process was followed by the discarding of the run-in material prior to filament preparation. Material extrusion additive manufacturing (MEX) was used to produce three different sensor designs. The short flex and extended flex designs were bent about a fixed location with a smaller or larger bending area, respectively. All sensor designs were produced in three sets.
The sensors' bending characterization was conducted using custom-built test equipment. Each sample was subjected to two tests. The conductive network microstructure was characterized using a scanning electron microscope (SEM). Before microscopy, cryo-fracturing of the filament and cryo-microtoming of the sensor specimen were conducted. Impedance spectroscopy was carried out under voltage excitation at 0.5V amplitude.
Observations
The conductive network was observed in the sensors’ cross-section. The network showed no significant alignment after sensor fabrication. The phase and magnitude of the resultant impedance showed identical responses in all samples. The characteristics of the responses were extremely flat, implying that the filament's electrical behavior was similar to a typical resistor over the whole observed spectrum.
The three sensors had varied bending section lengths but were designed under identical footprints, hence the difference observed was the deformation concentration. At maximum bending angles, the average relative change in resistance was 0.16%, 4.30%, and 0.77% for extended, short, and simple flex sensors, respectively. They were made from similar materials and sustained the same degree of bending. However, their output amplitudes were vastly different.
The tensile strain through bending appeared as the dominant influence on the conducting network during a whole bending cycle for short flex. For half the bending cycle, simple flex exhibited both an increase and a decrease in resistance. The layers’ fusion was due to the MEX process, which could be moderated through printing temperature and speed, allowing further means to modify the signal of the sensor. The force required to bend the extended flex sensor was around one-quarter of the force required for bending the simple flex sensor. Short flex sensors, on the other hand, required 25 times the force to bend than the simple flex sensors.
Conclusions
To summarize, the researchers determined the dependence of flexural sensor response on the bending section's length. Although all designs were subjected to the same degree of bending, the signal outputs varied significantly. The short flex sensor outperformed the extended flex sensor by 27.7 times and the simple flex sensor by 5.6 times. These results demonstrated that the internal tensile and compressive stresses influence the sensor signal depending on the concentration of the bending.
Furthermore, this study opens new possibilities for combining and integrating sensors into compliant systems. Additional improvements could be achieved by researching the effects of the MEX process on other performance characteristics like recovery and response times. According to the authors, enhancing signal output linearity and sensor reproduction is crucial for future development to examine the impact on other properties due to the sensor geometry.
More from AZoM: Powering Wearable Electronics with Body Heat
Disclaimer: The views expressed here are those of the author expressed in their private capacity and do not necessarily represent the views of AZoM.com Limited T/A AZoNetwork the owner and operator of this website. This disclaimer forms part of the Terms and conditions of use of this website.
Source:
Frederik Grønborg , Tiberiu Gabriel Zsurzsan , Anders Egede Daugaard , Jon Spangenberg , David Bue Pedersen , Conductive Compliant Mechanisms: Geometric tuning of 3D printed flexural sensors, Additive Manufacturing Letters (2022), doi: https://linkinghub.elsevier.com/retrieve/pii/S2772369022000573