A new paper in the journal Composites Science and Technology has explored the development of bio-based electrically conductive inks for use in additive manufacturing. The research has been carried out by a team from France and Italy.
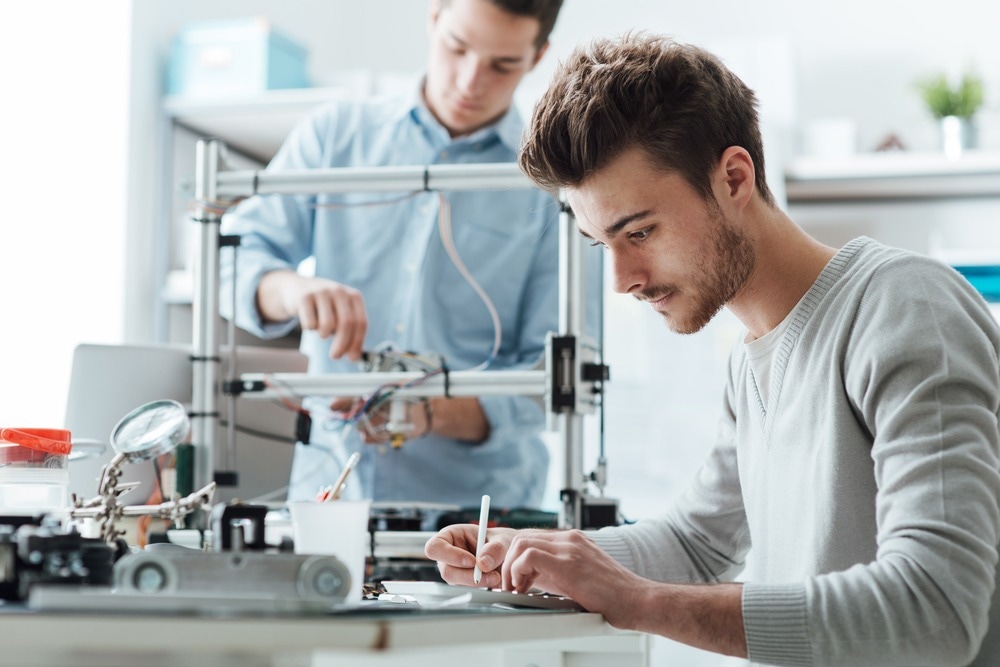
Study: Bio-based formulation of an electrically conductive ink with high potential for additive manufacturing by direct ink writing. Image Credit: Stock-Asso/Shutterstock.com
Fabricating Functional Materials with Additive Manufacturing
Additive manufacturing is a revolutionary technology that provides significant benefits for multiple industries. Additive manufacturing techniques offer the advantages of eco-friendliness, significantly reduced material waste, cost-effectiveness, design freedom, and multifunctional material fabrication.
The manufacturing of functional materials has become a hot-button topic in the field of additive manufacturing in the past decade, with electrically conductive materials and device components a key focus of research. Electrically conductive materials are essential for applications such as 3D-printed sensors and energy storage technologies.
Several studies have reported the development of electrically conductive materials, such as incorporating electrically conductive fillers into thermoplastics which are then printed using additive manufacturing techniques such as fused deposition fabrication. Other studies have incorporated fillers into UV-curable resins to print functional materials using stereolithography.
These materials are limited in terms of their electrical conductivity due to the low concentration of fillers that can be incorporated in polymer matrices. Other methods explored in research include the direct printing of electrically conductive inks using direct ink extrusion techniques.
This direct ink extrusion route provides the improved tailoring of composite materials and makes possible the incorporation of non-melting fillers and binders such as thermosetting resins, hydrogels, and cellulose fibers. Direct ink writing has been successfully employed to print conductive inks, incorporating conductive particles such as silver wires, graphene, oligomers, polymers such as PLA, and epoxy resin precursors.
Printability Requirements of Conductive Printable Inks
Electrically conductive printable inks must satisfy several key printability parameters. The filament must be extrudable and not cause nozzle clogging and should retain filament shape maintenance and shape fidelity after printing and solidification. Furthermore, to be efficient electrical conductors, sufficient amounts of electrons must be conducted after solidification in the printed inks.
Carbon nanotubes are widely reported conductive fillers for use in these printable inks, but there are some key material challenges associated with them. Entanglement and agglomeration of carbon nanotubes due to the nanomaterial’s strong steric interactions and high aspect can cause nozzle clogging, impacting the ink’s printability.
Binder choice is important as it must be compatible with fillers and act as a sufficient dispersion medium. Thermosetting resins are a good candidate for binders as they have tunable viscosity and are compatible with electrically conductive fillers such as carbon nanotubes. Furthermore, the polymer matrix can be further carbonized to enhance its electrical conductivity. Organic polymers have emerged as superior binder candidates.
The Study
The new paper in the journal Composites Science and Technology has demonstrated the development of a novel bio-based electrically conductive ink for 3D printing of functionalized devices using direct ink writing. The ink uses furanic resin, which fulfills carbonization requirements for printable conductive inks and incorporates carbon nanotubes and cellulosic fibers.
The effect of carbon nanotube morphology on the rheological behavior of inks and their dispersibility in ethanol was investigated in the paper, and different ink formulations were prepared to optimize the bio-ink's rheological behavior. Moreover, the printability and electrical conductivity of the novel bio-ink were optimized. The potential increase in electrical conductivity was further assessed using a pyrolysis step.
Study Findings
The authors demonstrated the successful formulation of electrically conductive furan resin-based bioinks with superior potential for printability using direct ink writing additive manufacturing techniques.
A formulation incorporating 4 wt % low-aspect ratio carbon nanotubes and 15 wt% cellulose fibers exhibited the optimal rheological behavior. Moreover, this specific formulation displays good electrical conductivity of at least 3.5 10-1 S/m. The improved dispersibility of low aspect ratio carbon nanotubes and enhanced electrical conductivity informed their selection for incorporation in the composite bio-ink.
Carbonization of a 27 wt% cellulose-containing composite yielded an increase in electrical conductivity up to 2 103 S/m. Carbonizing samples with 4 wt% carbon nanotubes yielded a composite ink with more than double this electrical conductivity. In the composites containing carbon nanotubes, there was a fivefold increase in the order of electrical conductivity magnitude when they were pyrolyzed.
In Summary
The research has successfully demonstrated the development of bio-based printable composite inks containing different filler amounts. The biocomposites possess tunable electrical conductivity and can be considered to be candidates for the direct fabrication of tailored 3D printable products.
More from AZoM: Strong and Heat-Resistant Synthetic Fiber Kevlar and its Composites
Further Reading
Bouzidi, K et al. (2022) Bio-based formulation of an electrically conductive ink with high potential for additive manufacturing by direct ink writing Composites Science and Technology 109765 [online, pre-proof] sciencedirect.com. Available at:
Disclaimer: The views expressed here are those of the author expressed in their private capacity and do not necessarily represent the views of AZoM.com Limited T/A AZoNetwork the owner and operator of this website. This disclaimer forms part of the Terms and conditions of use of this website.