Researchers combine many elemental metals to create a class of material known as enduring high-entropy alloys (HEAs). Applications involving high stress, harsh temperatures, radiation, and wear and tear could profit from the usage of HEAs. They can be produced by additive manufacturing (AM), also known as 3D printing, however this generally has poor ductility.
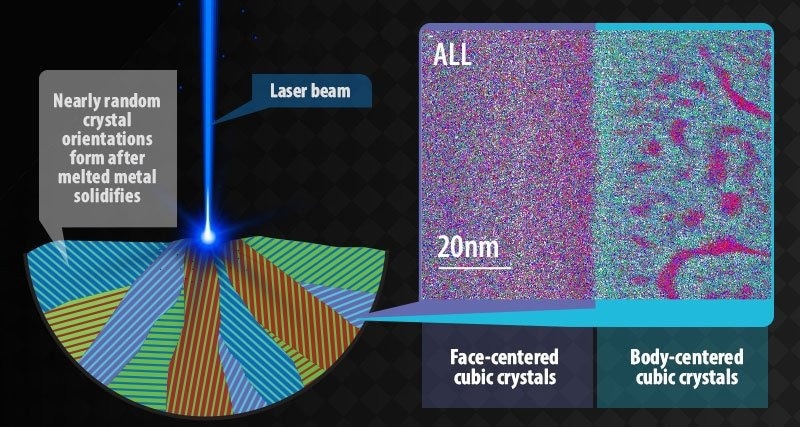
Images of the two crystal structures (right) found in a high-entropy alloy (left) made by additive manufacturing. Image Credit: University of Massachusetts Amherst
This indicates that 3D-printed HEAs are hard to construct and do not stretch or flex sufficiently under stresses to avoid breaking. Researchers have now created HEAs that are far more ductile and stronger with the use of laser-based AM. To learn more about the processes underlying these performance gains, they employed electron microscopy, neutron and X-Ray scattering, and other techniques.
The Impact
One day, the manufacturing sector could use stronger and more easily molded HEAs. Light and complicated HEA components require enhanced fracture resistance, durability, and dependability to function in various applications. Customers and businesses would gain from this, for instance, as it would make it possible to produce stronger goods, machinery that lasts longer, and safer and more fuel-efficient cars.
Furthermore, AM using lasers to fuse powdered alloys into solid metal forms is extremely energy-efficient. Due to this, it is appealing to create novel HEAs.
Summary
Nanometer-thick nano-lamellae, or thin layers of plates, with great strength were created by the laser-based AM technique; the unique edges of the plates allow for some slippage, or ductility. The plates are composed of layers of face-centered cubic (FCC) crystal structures, which have an average thickness of about 150 nanometers, and body-centered cubic (BCC) crystal structures, which have an average thickness of about 65 nanometers.
The new HEAs outperformed the strongest titanium alloys with high yield strengths of almost 1.3 gigapascals. With the same yield strength, these HEAs also provide an elongation of around 14%, which is more than that of other AM metal alloys. The amount of bending that a material can endure without breaking is called its elongation.
The researchers were able to investigate the internal mechanical load sharing of the HEA samples under strain due to neutron data obtained from the Spallation Neutron Source, an Office of Science user facility at Oak Ridge National Laboratory (ORNL) operated by the Department of Energy (DOE).
The Center for Nanophase Materials Sciences, another DOE user facility at ORNL, provided the researchers with an atom probe equipment to help them obtain comprehensive three-dimensional (3D) images of the compositions and microstructures, which are made up of alternating layers of nano-lamellae.
At Argonne National Laboratory’s Advanced Photon Source, another DOE Office of Science user location, the phases of several annealed samples were examined using X-Ray diffraction.
This study was carried out at the DOE Office of Science user facilities Spallation Neutron Source, Advanced Photon Source, and Center for Nanophase Materials Sciences. The National Science Foundation, the University of Massachusetts Amherst, and the Laboratory Directed Research and Development program at Lawrence Livermore National Laboratory all provided funding for this research.
Journal Reference
Jie, R., et. al. (2023) Strong yet ductile nanolamellar high-entropy alloys by additive manufacturing. Nature. doi:10.1038/s41586-022-04914-8