A recent article published in Scientific Reports proposed incorporating 1 wt.% silica nanorods in aluminum-10 wt. % zinc (Al-10Zn) alloys to enhance corrosion resistance and limit failure events. This influence of nano-silica was validated through microstructural, mechanical, and electrochemical studies.
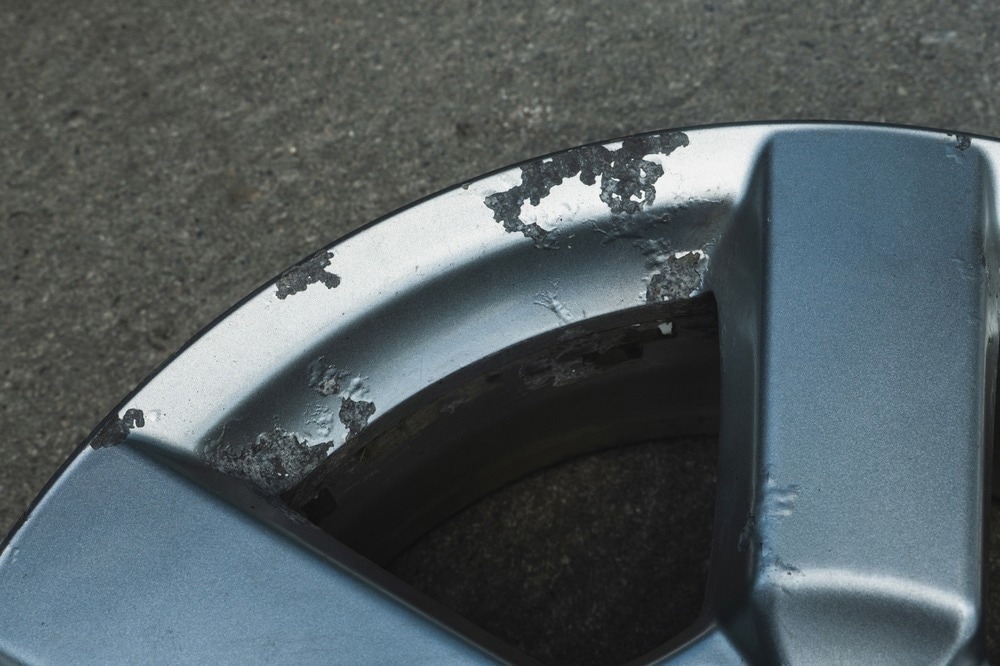
Image Credit: Georgiy M/Shutterstock.com
Background
Al-Zn alloys were originally developed for lightweight military bridges and are widely used today in marine engineering, ship transportation, and rail transit systems. However, their further application is limited because of stress-corrosion cracking along welds.
Many solutions have been explored to address faults and produce Al-Zn components with enhanced mechanical performance. Among various proposed solutions, such as parameter optimization, alteration of alloy composition, and post-processing techniques, reinforcing alloys with nanostructures has emerged as a promising concept.
Various nanomaterials, including SiO2, TiO2, CuO, Al2O3, and SiC, are used as reinforcements to improve the properties of Al-Zn alloys. Nanoparticle-reinforced matrix offers several nucleation sites for solidification, enhancing alloys’ durability and strength. Adding small dosages of nano-silica can also delay microstructure development and improve corrosion resistance.
This study explored the impact of silica nanostructures on the physical, mechanical, and electrochemical properties of Al-Zn alloys.
Methods
Al-10 wt% Zn alloy (AZ) was fabricated by melting high-purity constituents in a vacuum and cast into dimensions of 16×80×200 mm3. Subsequently, 1 wt.% of commercial silica nano-powder (10-80 nm particle size) was added to the AZ alloy after remelting mechanically at 1000 K in a vacuum furnace. The resulting nanocomposite (AZS) was solution-treated at 500 °C for two hours and quenched in cold water.
The AZ and AZS samples were cast into thin sheets and homogenized before use. Subsequently, they were aged for 2 hours at 423, 443, and 463 K, and they were quenched with cold water to protect their structure.
X-ray photoelectron spectroscopy (XPS) was used to determine the chemical composition of the composites, while X-ray diffraction (XRD) examined their crystal structure. Their microstructure was observed using an optical microscope, and Keller’s reagent etching was employed to reveal grain orientations and boundaries.
Scanning electron microscopy (SEM) was performed on the specimens to determine surface structures and changes before and after aging at various temperatures. Transmission electron microscopy (TEM) verified the nanostructure of SiO2 powders.
The mechanical performance of AZ and AZS composites was investigated through tensile strength and microhardness measurements. Finally, their corrosion behavior was analyzed in a 3.5 % NaCl solution through electrochemical impedance spectroscopy (EIS) measurements.
Results and Discussion
SEM images of the fabricated composite revealed a uniform microstructure with two different metallurgical phases: the α-Al matrix and the β-Zn phase. Nucleated Zn particles were evident on the grain boundaries. These Zn particles support the adherence of SiO2 nanorods to each other, which form precipitates at the outer grain boundaries and enhance the strength of the samples.
The AZ alloy underwent grain refinement after adding SiO2 and with aging. The structure of all aged samples exhibited a more uniform distribution of Zn and SiO2 compared to as-cast samples, especially in AZS compared to the AZ base alloy.
With increasing aging temperatures from 423 to 443 K, the tensile stress-strain curves of AZ and AZS shifted toward higher stress values, but an ultimate drop in the yield stress was observed at 463 K. Additionally, decreased strain rates at higher temperatures resulted in lower strength and dynamic recovery in composites.
The hardness values of AZ and AZS decreased with increasing aging temperature, with a significant rise at 443 K (transition temperature). This anomalous peak behavior at 443 K was attributed to favorable nano-silica size distribution in the AZ base alloy. The open circuit potential (OCP) of AZ and AZS samples increased steadily with increasing aging temperature, being greater for AZS due to the presence of nano-silica.
The optimal aging temperature for AZ and AZS was concluded to be 463 K from the potential shift observed in EIS studies. Furthermore, AZS exhibited a lower corrosion rate than AZ with decreasing corrosion current density over the testing period. The corrosion process was inhibited for AZ and AZS with increasing aging temperatures. The improvement in electrochemical and mechanical properties of the Al-based alloy was attributed to uniformly distributed SiO2 nanostructures.
Conclusion
Overall, the researchers comprehensively analyzed the impact of adding silica nanorods and varying aging temperatures on Al-10Zn alloy’s microstructure, as well as its mechanical and electrochemical properties.
The ultrafine grains formed due to silica nanorods improved the alloy hardness by up to 13.8 %, ultimate tensile strength by up to 79 %, and corrosion resistance by up to 89.4 % compared to Al-10Zn bulk. Thus, silica nanorods combined with appropriate aging helped realize a superior nanocomposite with limited failure events under loading and high corrosion resistance.
This study's findings can expand the application of silica-incorporated Al-Zn alloys in the automotive, construction, and aerospace industries.
Journal Reference
AbdElRhiem, E., Barakat, YF., Abdelaziz, SM., Mostafa, MM., Nada, RH., Mohamed, SG. (2024). Corrosion suppression and strengthening of the Al-10Zn alloy by adding silica nanorods. Scientific Reports. DOI: 10.1038/s41598-024-64323-x
Disclaimer: The views expressed here are those of the author expressed in their private capacity and do not necessarily represent the views of AZoM.com Limited T/A AZoNetwork the owner and operator of this website. This disclaimer forms part of the Terms and conditions of use of this website.