A recent study in Scientific Reports explored how volume energy density (VED) during laser powder bed fusion (L-PBF) affects the microstructure and corrosion resistance of NiTi alloys (Nitinol). The research focused on scan (XY) and built (XZ) planes, using electron backscatter diffraction (EBSD) for microstructure analysis and differential scanning calorimetry (DSC) for phase change temperature measurement.
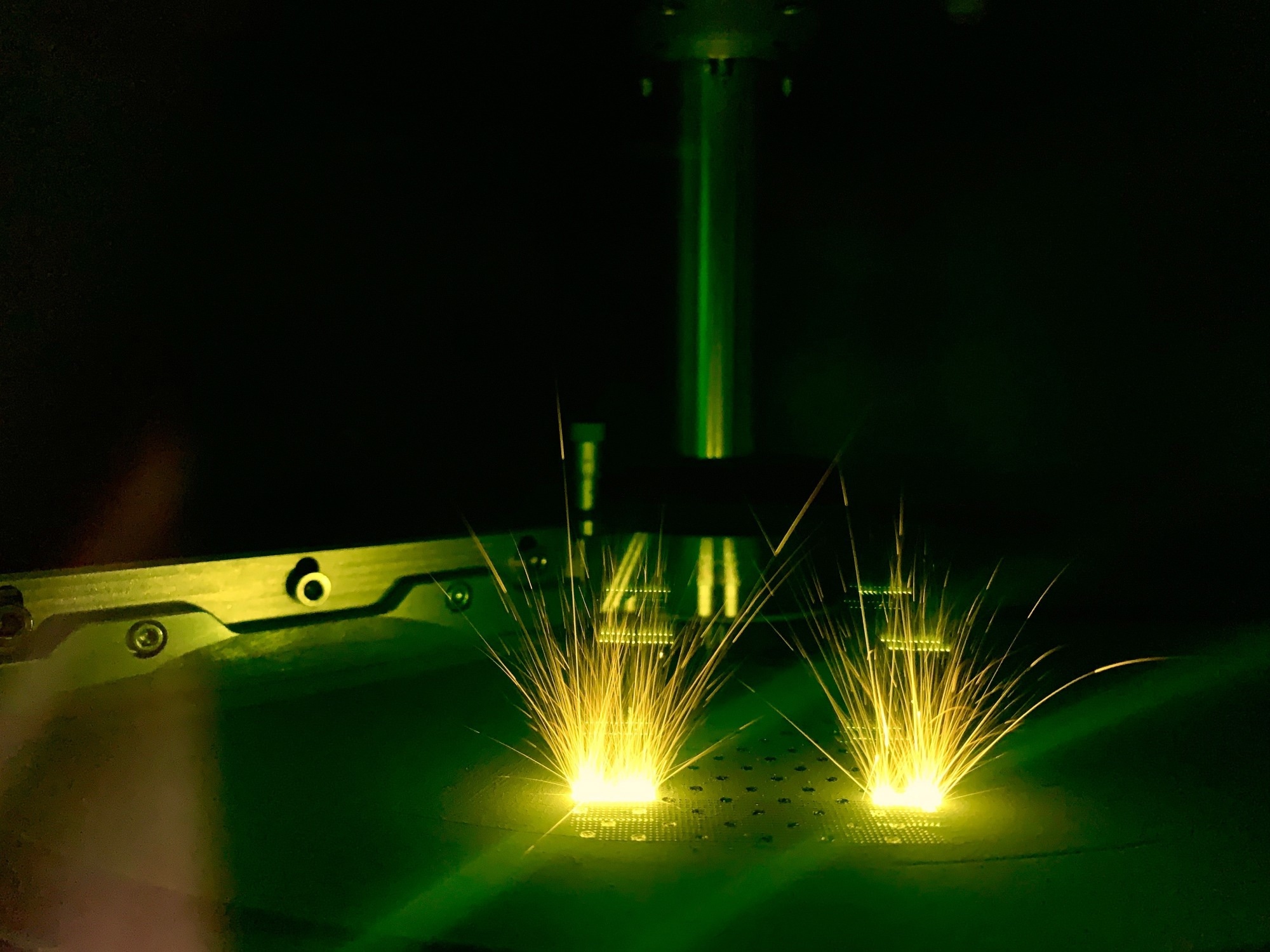
Image Credit: dr_christian_bay/Shutterstock.com
Background
Nitinol is widely recognized for its shape memory, biocompatibility, super-elasticity, and exceptional corrosion resistance, making it valuable for applications in aerospace, biomedical devices, automotive components, robotics, and smart sensors.
L-PBF, a precision materials processing technique, allows for the fabrication of complex metallic structures with tailored properties. By adjusting L-PBF process parameters such as laser power and scanning speed, the phase transformation temperatures of Nitinol can be controlled.
However, the VED, which influences the melting and solidification during fabrication, is critical in determining the material's microstructure and corrosion resistance.
Methods
Gas-atomized NiTi powder containing 52.7 at.% Ni and 47.3 at.% Ti was used to fabricate cubic (10×10×10 mm) Nitinol samples via L-PBF. The powder's morphology and composition were assessed using scanning electron microscopy (SEM) and energy dispersive spectrometry (EDS). Samples were fabricated with a consistent layer thickness of 60 µm, a hatch spacing of 80 µm, and varying laser parameters to achieve different VED values.
XRD confirmed the phase structure, while SEM and EBSD were used to analyze grain size, orientation, and phase distribution. DSC measured phase transformation temperatures, and the Archimedes method determined sample density. Vickers microhardness testing evaluated mechanical properties.
Electrochemical studies were performed using a three-electrode setup with a saturated calomel electrode as the reference, a graphite rod as the counter, and the printed samples as working electrodes. A 3.5 % NaCl solution served as the electrolyte. Tafel slopes were analyzed to determine corrosion current density, corrosion potential, pitting potential, and corrosion rate. X-ray photoelectron spectroscopy (XPS) was performed to characterize the surface of the samples.
Results and Discussion
Four laser parameters were used to produce nitinol samples with different VED values. All samples exhibited a single austenite B2 phase with no secondary phase in XRD patterns. Additionally, DSC analysis revealed an austenite finish (Af) below room temperature in all the samples, which resulted in a B2 austenitic super-elastic phase structure at room temperature.
Increasing VED resulted in higher residual stresses in the nitinol samples, which was attributed to the lattice distortions induced by non-uniform thermal gradients during the L-PBF process. Higher VED could increase the thermal gradient and cooling rate, inducing greater lattice strain due to constrained thermal expansion and phase transformation stresses.
EBSD analysis demonstrated that the sample produced using higher laser energy density underwent discontinuous dynamic recrystallization, resulting in grain refinement. Consequently, clear preferential microstructural morphology and grain orientations were observed in the XY and XZ planes. The XY planes had a uniform chessboard pattern, while the XZ plane exhibited more elongated columnar semi-elliptical grains.
Electrochemical testing demonstrated that samples fabricated with high VED exhibited significantly improved corrosion resistance, with a seven-fold increase compared to low-VED samples. XPS analysis indicated that high-VED samples formed a stable, TiO2-rich passive film, providing superior corrosion resistance. In contrast, low-VED samples formed a mixed and less stable film of TiO2 and Ti2O3.
Conclusion
The study demonstrated that L-PBF can be optimized to produce NiTi components with tailored microstructural and corrosion properties. Compared to traditional methods like air plasma spraying and high-velocity oxy-fuel, L-PBF offers advantages such as dense, crack-free microstructures and the formation of stable passive layers. These characteristics significantly enhance corrosion resistance, making L-PBF a suitable fabrication method for aerospace, biomedical implants, and marine environments applications.
By fine-tuning L-PBF parameters, Nitinol alloys can be engineered for specific microstructural and corrosion behaviors, expanding their usability in environments requiring long-term durability and corrosion protection. This work highlights the potential of L-PBF to advance the fabrication of high-performance NiTi components for critical applications.
Journal Reference
Perumal, G., et al. (2025). Exploring the role of volume energy density in altering microstructure and corrosion behavior of nitinol alloys produced by laser powder bed fusion. Scientific Reports. DOI: 10.1038/s41598-024-84222-5, https://www.nature.com/articles/s41598-024-84222-5
Disclaimer: The views expressed here are those of the author expressed in their private capacity and do not necessarily represent the views of AZoM.com Limited T/A AZoNetwork the owner and operator of this website. This disclaimer forms part of the Terms and conditions of use of this website.