Dielectric cure monitors are used for measuring the electrical properties of a thermoset using AC signals across a wide frequency range. Although resistance measurement using DC techniques can also provide data about a material, it has limitations and drawbacks that should be taken into consideration by users.
More specifically, the phenomenon of electrode polarization would not only distort DC resistance data but would also lead to misinterpretation of the state of cure.
Dielectric Cure Monitoring
Dielectric cure monitoring, also called Dielectric Analysis (DEA), quantifies the permittivity (ε′) and resistivity (ρ) of a polymer. Both permittivity and resistivity are the dielectric properties of a material.
As such, resistivity has a frequency-dependent (ρAC) component because of the rotation of stationary dipoles, and a frequency-independent (ρDC) component because of the flow of mobile ions.
Frequency-independent resistivity, often known as DC resistivity, essentially extends across a wide frequency range that includes DC (0 Hz). Since frequency-independent resistivity corresponds to the state of cure, it serves as a valuable material probe of polystyrenes, polyurethanes epoxies, sheet molding compounds (SMC), bulk molding compounds (BMC), and other thermosets.
To highlight the correlation with mechanical viscosity, the name ion viscosity (IV) was coined in the early 1980s as a substitute for frequency-independent resistivity. It relies on ionic mobility. The following equation defines ion viscosity.
DC Resistance Measurements
Through AC measurements of thermosets, a complete range of data relating to the cure state can be obtained. Simpler DC techniques offer limited yet useful data. Resistance monitors are actually highly sensitive ohmmeters that drive current via the material between two electrodes using a DC voltage source.
Frequency-independent resistivity, also called ion viscosity, is different from resistance by just a scaling factor. This scaling factor relies on the geometry of sensors; therefore, problems relating to ion viscosity apply to resistance as well.
Instruments that use DC measurements achieve simplicity but they also compromise on flexibility, and possibly accuracy, because of the disadvantages given below:
- DC measurements are only capable of obtaining DC resistance
- Frequency-independent resistance can be quantified across a wide frequency range that includes DC (0 Hz)
- Capacitance, frequency-dependent resistance, and frequency-independent resistance are measured by AC techniques
- Frequency-independent resistance, also called ion viscosity, is the accurate term describing DC resistance
- DC measurements are likely to create distorted data due to electrode polarization
- Release layers do not enable DC measurements
- Release layers can be described as very thin insulating sheets that are utilized to prevent a material from bonding to a platen or mold
- Release layers not only block DC current but also inhibit the measurement of DC resistance
- Systematic errors may occur in DC measurements
- It is not possible to distinguish thermal drifts, offset voltage drifts, and leakage currents in circuits from the actual DC signal
Electrode Polarization in AC and DC Measurements
Most often, it is not useful to quantify frequency-independent resistance (ρDC) through DC signals. During early cure, the electrode polarization (EP) phenomenon can produce a blocking layer across sensor electrodes, especially when a material is highly conductive, and promote unusually high apparent ion viscosities.1
A plot of resistivity from AC measurements of 5-minute epoxy is shown in Figure 1. All data are plotted against an axis marked as ion viscosity and could be collectively known as ion viscosity.
Three features can be seen in Figure 1:
- Overlapping or almost overlapping curves indicate the dominance of true ion viscosity, or frequency-independent resistivity
- Relates well with cure state
- Induced by the movement of mobile ions
- Diverging curves indicate the dominance of frequency-dependent resistivity
- Does not relate well with cure state
- Caused by dipole rotation
- Electrode polarization distorts 1 and 10 Hz curves for about 2 minutes
.jpg)
Figure 1. Ion viscosity/resistivity during cure of 5-minute epoxy. Image Credit: Lambient Technologies.
At the start of the cure, electrode polarization significantly distorts the 1 Hz data, as illustrated in the expanded plot of Figure 2. Such a distortion alters the predicted single minimum in ion viscosity/resistivity to a peak with two local minima.
.jpg)
Figure 2. Expanded ion viscosity/resistivity around the time of minimum viscosity. Image Credit: Lambient Technologies.
Data obtained from 10 Hz measurements reveal the distortion to a relatively less degree because increasing frequency decreases the boundary layer effect. Moreover, measurements taken at even higher excitation frequencies — 1 to 10 kHz — do not exhibit any distortion and accurately detect the ion viscosity minimum.
In a majority of the cases, information about cure can be mathematically restored.1,2 Figure 3 demonstrates how boundary layer correction, also known as electrode polarization (EP) correction, is able to recover the affected data. Following EP correction, 1 and 10 Hz ion viscosity exhibits a correct minimum and is consistent with the higher frequency data.
.jpg)
Figure 3. Resistivity/ion viscosity with boundary layer (EP) correction. Image Credit: Lambient Technologies.
Once the boundary layer correction is applied, only 1 Hz ion viscosity can be used to track the whole 5-minute epoxy cure, as illustrated in Figure 4.
.jpg)
Figure 4. 1 Hz ion viscosity with boundary layer (EP) correction. Image Credit: Lambient Technologies.
Release Films with AC and DC Measurements
Figure 5 shows a sensor in a mold with a release film. Since release films are often made from electrically insulating materials, including PTFE, they can pass only AC signals. This makes cure monitoring with DC techniques unviable. But an appropriately designed dielectric sensor enables AC cure monitoring via a release film.
.jpg)
Figure 5. Dielectric sensor with release film. Image Credit: Lambient Technologies.
Figure 6 illustrates a 1" Single Electrode dielectric sensor from Lambient Technologies. The sensor is installed in a press platen and covered using Northern Composites HTF-621 — a PTFE-based release film that measures just 0.001" thick.
.jpg)
Figure 6. 1″ Single Electrode sensor in press platen with HTF-621 release film. Image Credit: Lambient Technologies.
Figure 7 compares an ion viscosity of 100 Hz quantified with and without the HTF-621 release film while curing BMCs.
.jpg)
Figure 7. Comparison of BMC cure with and without release film,100 Hz AC measurement. Image Credit: Lambient Technologies.
The curves are almost the same except near the time of minimum ion viscosity, when the effect of the boundary layer distorts the measurements via the film.
In a majority of the cases, this distortion can be mathematically corrected and data relating to the cure can be restored.1,2,3 Figure 8 illustrates how the affected data is recovered by boundary layer correction.
Following correction, ion viscosity quantified with the release film accurately follows ion viscosity quantified without the release film. It must be noted that for both these tests, the slight variations between curves are mostly caused by process temperature variations.
.jpg)
Figure 8. Comparison of raw ion viscosity and ion viscosity with EP (boundary layer) correction. Image Credit: Lambient Technologies.
While DC measurement of resistance provides a simple technique for cure state probing, it has the following drawbacks:
- Inability to quantify the cure state using vacuum bags or release films
- Potential distortion of data caused by electrode polarization
Figure 9 compares BMC’s DC measurements using the 1" Single Electrode sensor with and without the HTF-621 release film. Data from the 100 Hz AC measurements are also plotted for reference purposes.
.jpg)
Figure 9. Comparison of AC and DC measurements of ion viscosity. Image Credit: Lambient Technologies.
Even without any release film, DC measurements exhibit considerable distortion close to the time of ion viscosity minimum. Although the distortion of AC data can be corrected, DC data cannot be corrected. Moreover, it is not possible to make DC measurements through the release film, as indicated by the high ion viscosity at the instrument’s measurement limit.
Conclusion
DC measurements of resistance can be made easily, but they have drawbacks when compared to AC measurements of dielectric properties. Electrode polarization may distort DC data in the case of thermoset cure monitoring and lead to misinterpretation of the cure state.
While electrode polarization can also have an impact on low-frequency AC measurements, the extra information obtained from dielectric characteristics makes it possible to correct the distorted data.
DC techniques need direct contact with the composite or thermoset, and are not capable of measuring through vacuum bags and release films. Therefore, AC measurements become specifically useful in the field of manufacturing.
AC techniques are capable of monitoring cure through insulators, and make it easy to use the sensors underneath a release film. This prevents issues that occur when a material adheres to the sensor. In vacuum-assisted resin transfer molding (VARTM) and other analogous processes, AC measurements via the vacuum bag do not introduce breaks in the bag that may turn out to be a source of leakage.
References
- Day, D.R.; Lewis, J.; Lee, H.L. and Senturia, S.D., Journal of Adhesion, V18, p.73 (1985)
- Lambient Technologies application note AN3.29, “Electrode Polarization and Boundary Layer Effects”
- Lambient Technologies application note AN3.19, “Electrode Polarization with AC and DC Cure Monitoring”
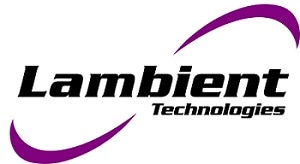
This information has been sourced, reviewed and adapted from materials provided by Lambient Technologies.
For more information on this source, please visit Lambient Technologies.