Toray Advanced Composites is a key player in the development and manufacture of cutting-edge, high-reliability materials for use in the space market. Materials manufactured by Toray Advanced Composites are used on most spacecraft, satellite, and planetary rover launched in the Western world. The company has more than two decades of space flight heritage, making it the only materials company that has the pedigree, experience, or breadth of product knowledge to meet the challenging requirements of the space, launch, and satellite industry.
In partnership with its customers and with a close eye to evolving market needs, Toray Advanced Composites has developed a wide-ranging product portfolio of resin systems for use on high modulus PAN and pitch carbon fiber and specialty fabrics, in addition to standard reinforcements.
.jpg)
Toray’s Objectives
- Connecting the planet
- Furthering scientific understanding
- Reducing weight
- High reliability
Commercial Satellites and Launch Vehicles
Toray Advanced Composites continues to develop and serve its longstanding customers who are supplying larger, higher resolution and more accurate reflectors, and more deployable structures for the construction of ever-larger telecommunications satellites to house more powerful and sophisticated payloads.
Toray also supplies a complete range of products to fulfill the requirements of today’s heavy-lift commercial launch vehicles used for sending high-value missions reliably into space.
Science and Exploration
Toray’s next-generation materials support science missions from NASA and ESA to go further than ever before to unveil the secrets of the universe. The next-generation spacecraft will journey to more aggressive, colder, and hotter environments, and with greater numbers of planetary rovers and landers. In time, the company’s materials will play an important role in sending humans to Mars.
New Space
Today’s rapidly evolving “New Space” market brings in new challenges to address the material demands of hundred strong, mass-produced satellite constellations, greater numbers of launch-on-demand vehicles, and swarms of high flying “pseudo-satellite” drones. New Space will bring new science, “big data,” and internet connectivity to billions of more people.
Satellite Product Applications
.jpg)
Launch Vehicle Product Applications
.jpg)
Space, Satellite, Launch
Product overview
Thermoset Prepregs Epoxy
|
RESIN MATRIX |
DRY Tg ONSET |
CURE TIME AND TEMPERATURE |
KEY PRODUCT CHARACTERISTICS |
OUTGASSING, CTE/ CME OR HOT/WET DATA |
OOA/VBO |
TOUGHENED |
LOW MOISTURE ABSORPTION |
SPACE/ SATELLITE |
LAUNCH |
EX-1522 |
Epoxy |
180 °C (356 °F) |
2 hours at 177 °C (350 °F) |
• Excellent mechanical properties
• Good balance of properties between cyanate ester and epoxy |
TML 0.28%
CVCM 0.01%
WVR 0.16%
TML-WVR 0.12% |
Ο |
Ο |
Ο |
Ο |
|
TC250 |
Epoxy |
140 °C (285 °F) or 180 °C (356 °F) with post cure |
60 minutes at 88 °C (190 °F), followed by 2 hours at 130 °C (265 °F) |
• NCAMP qualified
• Long out life of 60 days and the ability to post cure makes it ideal for large structures |
Wet Tg 125 °C (257 °F) |
Ο |
Ο |
|
|
Ο |
RS-36 / RS-36-1 |
Epoxy |
181 °C (358 °F)
190 °C (374 °F) |
90 minutes at 177 °C (350 °F) |
• ESA qualified for solar array
• High toughness
• Low moisture absorption |
TML 0.4%
CVCM 0.01%
WVR 0.17%
TML-WVR 0.12% |
Ο |
Ο |
Ο |
Ο |
|
TC275-1 |
Epoxy |
164 °C (327 °F) or 183 °C (362 °F) with 177 °C (350 °F) post cure |
6 hours at 135 °C (275 °F) Optional post cure of 2 hours at 177 °C (350 °F) |
• Ideal for large structure fabrication
• Low density
• Excellent toughness for impact resistance |
Wet Tg 136 °C (277 °F) |
Ο |
Ο |
Ο |
|
Ο |
TC350-1 |
Epoxy |
191 °C (376 °F) |
2 hours at 177 °C (350 °F) |
• OOA/VBO processable
• Good hot/wet properties |
Wet Tg 160 °C (320°F) |
Ο |
Ο |
Ο |
|
Ο |
Thermoset Prepregs BMI
|
RESIN MATRIX |
DRY Tg ONSET |
CURE TIME AND TEMPERATURE |
KEY PRODUCT CHARACTERISTICS |
OOA/VBO |
TOUGHENED |
LOW MOISTURE ABSORPTION |
SPACE/ SATELLITE |
LAUNCH |
RS-8HT |
BMI |
310 °C (590 °F) |
2 hours at 177 °C (350 °F) followed by 6 hours at 232 °C (482 °F) |
• Excellent elevated temperature performance
• Good toughness and moisture resistance |
|
|
Ο |
|
Ο |
Thermoset Prepregs Cyanate Ester
|
RESIN MATRIX |
DRY Tg ONSET |
CURE TIME AND TEMPERATURE |
KEY PRODUCT CHARACTERISTICS |
OUTGASSING, CTE/ CME OR HOT/WET DATA |
OOA/VBO |
TOUGHENED |
LOW MOISTURE ABSORPTION |
SPACE/ SATELLITE |
LAUNCH |
EX-1515 |
Cyanate Ester |
121 °C (249 °F) or 174 °C (345 °F) with post cure |
3 hours at 121 °C (250 °F) Optional post cure of 2 hours at 177 °C (350 °F) |
• Low density
• Resistant to microcracking
• Low zero stress state temp |
TML 0.179%
CVCM 0.007%
CTE 61 ppm/°C |
|
|
Ο |
Ο |
|
TC410 |
Cyanate Ester |
112 °C (234 °F) or 181 °C (358 °F) with post cure |
3 hours at 121 °C (250 °F) Optional post cure at 177 °C (350 °F) |
• Low CTE 58.4 µm/m/°C
• Extremely low CME 1205 µm/m/%
• Ideal system for stable structures |
TML 0.29%
CVCM <0.01%
WVR 0.17%
TML-WVR 0.12% |
|
Ο |
Ο |
Ο |
|
BTCy-1A |
Cyanate Ester |
185 °C (365 °F) or 207 °C (405 °F) with post cure |
2 hours at 177 °C (350 °F) Optional post cure of 60 minutes at 204 °C (400 °F) |
• Tough
• High Tg |
CTE 77 ppm/°C |
|
Ο |
Ο |
Ο |
|
RS-3/ RS-3C |
Cyanate Ester |
191 °C (375 °F) or 254 °C (490 °F) with post cure |
2 hours at 177 °C (350 °F) Optional post cure of 60 minutes at 232 °C(450 °F) |
• Extensive qualification portfolio
• Low CTE, CME
• High stability
• RS-3C is controlled flow version |
TML 0.22%
CVCM 0.01% |
Ο |
Ο |
Ο |
Ο |
|
TC420 |
Cyanate Ester |
176 °C (349 °F) or 348 °C (658 °F) with post cure |
3 hours at 177 °C (350 °F) Optional post cure at 260 °C (500 °F) |
• Good resistance to microcracking
• Capable of high temperature service
• Ideal for heat shield and ablative applications |
TML 0.41%
CVCM <0.01%
WVR 0.28%
CTE 55 ppm/°C |
Ο |
Ο |
Ο |
Ο |
Ο |
RTM Resins
|
RESIN MATRIX |
DRY Tg ONSET |
CURE TIME AND TEMPERATURE |
KEY PRODUCT CHARACTERISTICS |
OOA/VBO |
TOUGHENED |
LOW MOISTURE ABSORPTION |
SPACE/ SATELLITE |
LAUNCH |
EX-1545 |
Cyanate Ester |
173 °C (345 °F) |
2 hours at 177 °C (350 °F) |
• Toughened resin system with low viscosity of 140 cPs at 43 °C (110 °F)
• Long pot life for complex parts |
|
Ο |
|
Ο |
|
RS-16 |
Cyanate Ester |
167 °C (332 °F) or 231 °C (448 °F) with post cure |
2 hours at 135 °C (275 °F) followed by 2 hours at 150 °C (300 °F) |
• Low temperature cure resin system
• Post curable for higher Tg |
|
|
|
Ο |
|
EX-1510 |
Cyanate Ester |
193 °C (380 °F) |
2 hours at 177 °C (350 °F) |
• Low room temperature viscosity of 150 cPs
• Postcurable for higher Tg |
|
|
Ο |
|
|
Film Adhesives Epoxy
|
RESIN MATRIX |
DRY Tg ONSET |
CURE TIME AND TEMPERATURE |
KEY PRODUCT CHARACTERISTICS |
OOA/VBO |
TOUGHENED |
LOW MOISTURE ABSORPTION |
SPACE/ SATELLITE |
LAUNCH |
RS-15H |
Epoxy |
99 °C (211 °F) |
6 hours at 93 °C (200 °F) Alternate cures are available |
• Low temperature curing adhesive |
Ο |
Ο |
|
Ο |
|
TC263 |
Epoxy |
110 °C (230 °F) |
2 hours at 121 °C (250 °F) |
• High peel strength
• Ideal for metal or composite bonding |
Ο |
Ο |
|
Ο |
Ο |
TC310 |
Epoxy |
157 °C (315 °F) |
2 hours at 177 °C (350 °F) |
• Ideal composite bonding film adhesive |
Ο |
Ο |
|
Ο |
Ο |
Film Adhesives Cyanate Ester
|
RESIN MATRIX |
DRY Tg ONSET |
CURE TIME AND TEMPERATURE |
KEY PRODUCT CHARACTERISTICS |
OOA/VBO |
TOUGHENED |
LOW MOISTURE ABSORPTION |
SPACE/ SATELLITE |
LAUNCH |
EX-1516 |
Cyanate Ester |
126 °C (258 °F) |
5 hours at 121 °C (250 °F) |
• Compatible with Toray EX-1515 prepreg |
|
Ο |
Ο |
Ο |
|
RS-4A |
Cyanate Ester |
195 °C (383 °F) or 238 °C (460 °F) with post cure |
2 hours at 177 °C (350 °F) Optional post cure of 1.5-2 hours at 232 °C (450 °F) |
• Moisture resistant |
|
Ο |
Ο |
Ο |
|
EX-1543 |
Cyanate Ester |
207 °C (405 °F) |
2 hours at 177 °C (350 °F) Optional post cure of 2 hours at 204 °C (400 °F) |
• Compatible with 177 °C (350 °F) curing cyanate ester prepregs
• Low shrinkage
• Low outgassing |
|
|
Ο |
Ο |
|
TC4015 |
Cyanate Ester |
176 °C (349 °F) or 321 °C (610 °F) with post cure |
2 hours at 177 °C (350 °F) Optional post cure of >60 minutes at 232 °C (450 °F) |
• Excellent high temperature properties
• Compatible with TC420 |
Ο |
|
Ο |
Ο |
Ο |
Syntactics Epoxy
|
RESIN MATRIX |
DRY Tg ONSET |
CURE TIME AND TEMPERATURE |
KEY PRODUCT CHARACTERISTICS |
OOA/VBO |
TOUGHENED |
LOW MOISTURE ABSORPTION |
SPACE/ SATELLITE |
LAUNCH |
EM-3 |
Epoxy |
~116 °C (240 °F) |
60 minutes at 121 °C (250 °F) |
• High expansion (8-10 x)
• 0.64 g/cc (40 pcf) density
• Tg estimated from base resin data |
|
|
|
Ο |
|
TCF4035 |
Epoxy |
140 °C (284 °F) |
3 hours at 130 °C (265 °F) |
• Low density 0.64 g/cc (40 pcf)
• Compatible with TC250, may be post cured for higher Tg |
Ο |
|
|
|
Ο |
Syntactics Cyanate Ester
|
RESIN MATRIX |
DRY Tg ONSET |
CURE TIME AND TEMPERATURE |
KEY PRODUCT CHARACTERISTICS |
OOA/VBO |
TOUGHENED |
LOW MOISTURE ABSORPTION |
SPACE/ SATELLITE |
LAUNCH |
TCF4001 |
Cyanate Ester |
176 °C (349 °F) |
2 hours at 177 °C (350 °F) Optional post cure of 60-90 minutes at 232 °C (450 °F) |
• Low density 0.38 g/cc (24 pcf) |
Ο |
|
|
Ο |
|
TCF4050 |
Cyanate Ester |
176 °C (349 °F) or 232 °C (450 °F) with post cure |
2 hours at 177 °C (350 °F) Optional post cure of 60-90 minutes at 232 °C (450 °F) |
• Expanding syntactic film/core splice
• Density of 0.28-0.55 g/cc (17-35 pcf)
• Compatible with TC420 prepreg system |
Ο |
|
|
Ο |
|
EM-5A |
Cyanate Ester |
204 °C (400 °F) |
2 hours at 177 °C (350 °F) Optional post cure of 60-90 minutes at 232 °C (450 °F) |
• Expansion ratio of 4 x |
Ο |
|
|
Ο |
|
Syntactics Other Thermoset Matrices
|
RESIN MATRIX |
DRY Tg ONSET |
CURE TIME AND TEMPERATURE |
KEY PRODUCT CHARACTERISTICS |
OOA/VBO |
TOUGHENED |
LOW MOISTURE ABSORPTION |
SPACE/ SATELLITE |
LAUNCH |
SF-4 |
BMI |
295 °C (563 °F) |
2 hours at 204 °C (400 °F), then 6 hour post cure at 250 °C (452 °F) |
• Low density 0.62 g/cc (39 pcf)
• Compatible with RS-8HT and other BMI systems |
Ο |
|
|
Ο |
|
BMC Thermoset Epoxy
|
RESIN MATRIX |
DRY Tg ONSET |
CURE TIME AND TEMPERATURE |
KEY PRODUCT CHARACTERISTICS |
OOA/VBO |
TOUGHENED |
LOW MOISTURE ABSORPTION |
SPACE/ SATELLITE |
LAUNCH |
MS-1A |
Epoxy |
164 °C (327 °F) |
15-30 minutes at 138 °C (280 °F) followed by post cure of 1-2 hours at 177 °C (350 °F) |
• Chopped fiber epoxy BMC with high modulus fiber |
|
|
|
Ο |
Ο |
MS-1H |
Epoxy |
191 °C (375 °F) |
15-30 minutes at 138 °C (280 °F) followed by post cure of 1-2 hours at 177 °C (350 °F) |
• Chopped fiber epoxy BMC with intermediate modulus fiber |
|
|
|
Ο |
|
MS-4H |
Epoxy |
191 °C (375 °F) |
15-30 minutes at 138 °C (280 °F) followed by post cure of 1-2 hours at 177 °C (350 °F) |
• Chopped fiber epoxy BMC with high strength (standard modulus) fiber |
|
|
|
Ο |
Ο |
BMC Toray Cetex® Thermoplastic
|
RESIN MATRIX |
DRY Tg ONSET |
Processing Temperature |
KEY PRODUCT CHARACTERISTICS |
OOA/VBO |
TOUGHENED |
LOW MOISTURE ABSORPTION |
SPACE/ SATELLITE |
LAUNCH |
MC1100 |
PPS |
90 °C(194 °F) |
330 °C (625 °F) |
• PPS based BMC
• Fire retardant |
|
Ο |
Ο |
Ο |
Ο |
MC1200 |
PEEK |
143 °C (290 °F) |
385 °C (725 °F) |
• PEEK based BMC
• Fire retardant |
|
Ο |
Ο |
Ο |
Ο |
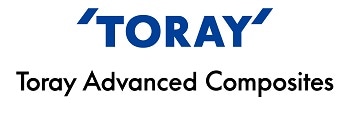
This information has been sourced, reviewed and adapted from materials provided by Toray Advanced Composites.
For more information on this source, please visit Toray Advanced Composites.