There is a growing need for ultra- low damage specimens below 40 nm thickness as researchers surpass boundaries of HR imaging and elemental analysis with transmission electron microscopes (TEM).
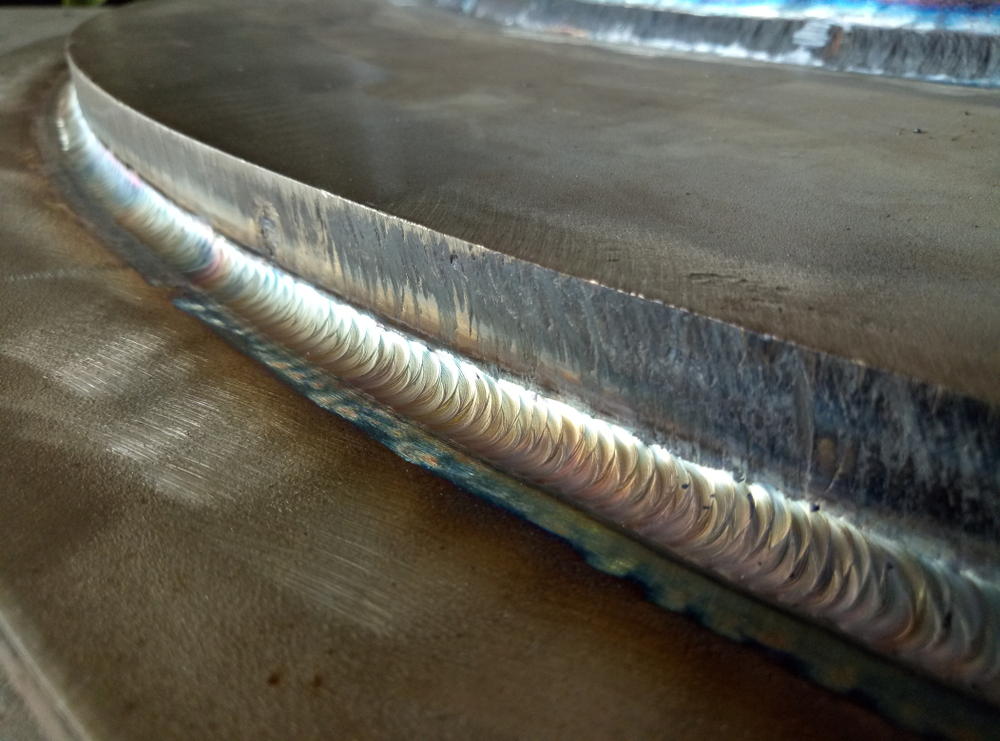
Image Credit: Shutterstock/anil Evskyi
While studying preparation techniques for these thin lamellae, factors to be considered include the class of the material being polished, and whether the technique is repeatable when applied across a range of samples. In this article, broad argon beam milling and focused ion beam milling (FIB) are discussed.
Techniques for Preparation of TEM Specimens
These two common methods are used to prepare electron transport specimens for a range of materials including metals, semiconductors and ceramics.
FIB is feasible in cases when there is a need for specific sample orientation or site specific positional accuracy. However, amorphization, implantation and vacancies due to application of high energy gallium ions, selective abrasion, surface roughness and sample alteration due to beam heating together with re-deposition, are certain damages that this technique causes.
Since FIB-induced surface amorphization reduces the signal-to-noise ratio, it is highly limiting and extensive. In order to avoid geometrical blurring for high resolution transmission electron microcopy (HRTEM) applications, sample thickness must be reduced by the square root of the feature size. A 25 KeV Ga+ FIB column can generate ~20 nm per specimen side damage in silicon (Si). In modern Si-based semiconductor devices, this can be limiting in cases where feature size is below 20 nm.
Approaches to Reduce Damage in TEM Samples
The depth of te FIB induced amorphous layer is based on beam angle, beam energy and material being milled. Some of the techniques used to limit this damage in TEM samples are:
- Gas-assisted etching - This method enhances the milling rate, however, it increases the roughness of crystalline-amorphous interface, which further damages TEM images.
- Low-energy FIB – Beam energy reduction brings down damage depth, though etching rate and positional resolution are also affected at these energies.
- Wet etching – Single-layered materials profit considerably when used with the right solution, but due to a varying etching rates, this technique cannot be used for multi-layer semiconductor devices.
- Argon ion milling – This is a highly promising technique for multi-layer materials, as none of the drawbacks mentioned are present. The original FIB damage layer is substituted by a newly formed Ar ion-induced damage layer. This layer thickness is based on the milling energy, angle and time, which are all parameters controlled by the user in the Gatan PIPS™ II System.
Practical Aspects of Argon Ion Polishing of FIB Specimens in PIPS II System
In order to optimize new layer thickness formed during Ar polishing of FIB-induced amorphous layer, while preventing re-deposition or specimen contamination, a number of parameters need to be considered:
- Beam energy – Low energy ions have a very shallow penetration depth, which reduces ion-induced surface damage. Beam energies lesser than 300 eV are recommended.
- Milling time – Since the Ar ion beam is well focussed at low energies in the PIPS II system (~ 1 mm FWHM), current density at the milling area is high, hence material removal rate is also high. Milling time needs to be optimized in order to remove enough material to enhance sample quality, but the specimen should not be over-thinned. The specimen must be milled for a few tens of seconds (<60 s), then checked in a microscope and milled further if needed.
- Milling angle: Even though it is known that a higher beam angle improves the ion induced surface damage, at low beam energies commonly used for this specific application (<0.5 keV), stopping and range of ions in matter (SRIM) models show that the sputtering yields are almost the same at high and low angles. Higher angles are more appropriate for post-FIB polishing in PIPS II System, in case of constraints from the mounting grid geometry. The chances of the thin areas causing lamella bending are reduced by milling from top and bottom.
- Sample temperature – For the prevention of heat-induced damage caused by ion bombardment, the stage (specimen) temperature is brought down to make sure that the milling area remains close to ambient temperature during milling.
- Ion milling mode – It has been observed that keeping the sample stationary and milling with just one gun at a time offers ideal results and the minimum amount of re-deposition (PIPS II Stationary milling mode).
- Type of supporting grid – Molybdenum (Mo) and Copper (Cu) are typical grid materials. The sputtering rate of Mo is low, reducing the chance of re-deposition from grid onto the FIB lamella.
- Position of FIB thinned area with respect to the milling gun – FIB specimens are either H-bars, or lift-out type (mounted on a grid fingertip or side wall). The sample is positioned at the PIPS II home position (Figure 1c) after mounting in the DuoPost™.
The thin lamella is brought to the center of rotation with the touch screen alignment page and X-Y stage movement available on the PIPS II System. The stage orientation angle is arranged such that the ion beam passes above the lamella prior to milling the grid or the substrate in order to minimise re-deposition. The PIPS II stage is rotated about 5° offset from the pre-set positions in the alignment page (Figure 2) for lift-out specimens placed on the side wall of the grid finger. While choosing this offset angle, remember that the Ar beam is 1 mm wide and not as small as the lamella.
.jpg)
Figure 1. PIPS II optical images of: (a) FIB H-bar sample and (b) FIB lift-out specimen mounted on the side wall of a Cu grid. (c) Top view cartoons show samples in home position as they are inserted in PIPS II System for post FIB polish.
.jpg)
Figure 2. Cartoons show how FIB H-bar and lift-out specimens are oriented with respect to the left and right guns. When lamella is mounted on the side wall of a grid finger, it is better to rotate the specimen at least 5° offset, so the beam does not deposit grid/substrate or weld material on the specimen thin area. Note that as shown in images on the right, the thickness of the lamella is much less than the grid, as a result the lamella can be welded at different positions on the finger.
Results
It can be inferred from these examples that there was an improvement in the quality of FIB-prepared TEM samples and the FIB induced amorphous layer thickness reduced by applying low energy (<300 eV), broad beam ion milling in the PIPS II system. Lift- out samples were mounted on Mo or Cu OmniProbe grids. Imaging of specimens was performed before polishing in the PIPS II System as reference of the sample condition after FIB preparation.
Using low energy Ar ion guns in stages with sequential TEM observation, the samples were polished. Milling was carried out at incident angles >7° from either top or bottom. Using the PIPS II X-Y stage, the lamellae were centered and aligned with regards to each gun then milled with stationary milling mode. Samples were cooled during polishing in order to minimise heat induced damage (-80 °C). Figure 3 shows micrographs depicting removal of FIB produced amorphous surface layers in a Niobium sample.
![Removal of FIB produced amorphous surface layers in a Niobium (Nb) sample can be readily seen in these micrographs. The right image shows changes after 30 seconds of milling at 300 eV. During this time, the amorphous layer was reduced from approximately 5.6 nm to 3.5 nm (~40% reduction). [FIB prepared specimen provided by University of Chicago, Illinois.]](https://d12oja0ew7x0i8.cloudfront.net/images/Article_Images/ImageForArticle_11933(3).jpg)
Figure 3. Removal of FIB produced amorphous surface layers in a Niobium (Nb) sample can be readily seen in these micrographs. The right image shows changes after 30 seconds of milling at 300 eV. During this time, the amorphous layer was reduced from approximately 5.6 nm to 3.5 nm (~40% reduction). [FIB prepared specimen provided by University of Chicago, Illinois.]
Figure 4 shows TEM micrographs of a multi-layer sample as prepared in FIB.
![TEM micrographs of a multi-layer sample as prepared in FIB (left), after polishing in PIPS II System at 300 eV for 60 seconds (center), after polishing in PIPS II System for additional 40 seconds (right). Due to FIB-induced amorphization, the second layer in the middle is not visible in the first two images (left and center), but after sufficient Ar ion polishing it is clearly visible in the last one (right). [FIB prepared specimen provided by Texas Instruments, Dallas Texas.]](https://d12oja0ew7x0i8.cloudfront.net/images/Article_Images/ImageForArticle_11933(4).jpg)
Figure 4. TEM micrographs of a multi-layer sample as prepared in FIB (left), after polishing in PIPS II System at 300 eV for 60 seconds (center), after polishing in PIPS II System for additional 40 seconds (right). Due to FIB-induced amorphization, the second layer in the middle is not visible in the first two images (left and center), but after sufficient Ar ion polishing it is clearly visible in the last one (right). [FIB prepared specimen provided by Texas Instruments, Dallas Texas.]
.jpg)
![Color images (left) show sample thickness maps* in the device, captured after milling in FIB (H-bar) and low energy milling in PIPS II System (300 eV beam, stationary milling mode, 130 seconds). Sample thickness is compared in these two images using profile lines averaged along the graph arrows shown below. TEM micrographs (right) show high resolution images taken before and after low energy ion milling in PIPS II System (taken from yellow square areas shown on the thickness maps). By reducing sample thickness, parts of FIB-induced sample surface damage have been removed. [FIB prepared specimen provided by Texas Instruments, Dallas Texas.]](https://d12oja0ew7x0i8.cloudfront.net/images/Article_Images/ImageForArticle_11933(6).jpg)
Figure 5. Color images (left) show sample thickness maps* in the device, captured after milling in FIB (H-bar) and low energy milling in PIPS II System (300 eV beam, stationary milling mode, 130 seconds). Sample thickness is compared in these two images using profile lines averaged along the graph arrows shown below. TEM micrographs (right) show high resolution images taken before and after low energy ion milling in PIPS II System (taken from yellow square areas shown on the thickness maps). By reducing sample thickness, parts of FIB-induced sample surface damage have been removed. [FIB prepared specimen provided by Texas Instruments, Dallas Texas.]
.jpg)
.jpg)
Figure 6. TEM micrographs of a multi-layer sample. The left image was captured as prepared in FIB. The right image was taken after polishing in PIPS II System for 90 seconds. Due to FIB-induced amorphization, and sample thickness, layers are not clearly visible in the first image, however after Ar ion polishing they are clearly visible. The EELS data (right) shows no sign of re- deposition of grid material (Mo) on the sample.
Conclusions
FIB samples were effeciently polished at below 300 eV. This enhanced the sample quality without redepositing the holder material or the grid. This was possible due to innovative features such as the optical camera along with DigitalMicrograph™ Imaging Software, focused ion beams at low energies (~ 1 mm in diameter), X-Y alignment stage and custom milling angles in PIPS II System.
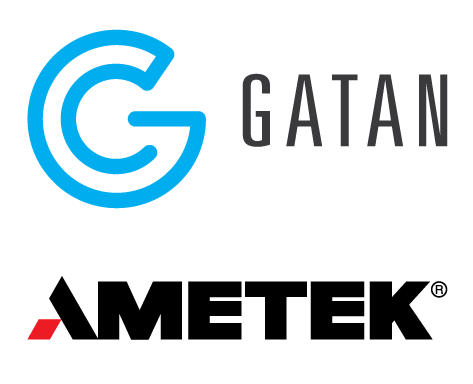
This information has been sourced, reviewed and adapted from materials provided by Gatan Inc.
For more information on this source, please visit Gatan Inc.