The repeated investigations of light microscopy related to the quality assurance of components are laborious tasks requiring experts with high microscopic skills. However, analysis of the same type of samples using the digital microscope Smartzoom 5 ensures a better workflow. The digital microscope facilitates easy handling by the user following a short introduction, without any compromise on the micrograph quality.
This article explains the additional advantages and benefits of using Smartzoom 5 for a ring-welded specimen, over the conventional light microscopy. With its supervisor-operator structure, Smartzoom 5 allows generation of a macro for the recurring investigations of e.g. ring welds.
Settings including the mode of illumination, magnification and objective can be defined. The weld time can be efficiently controlled using the saved job, ensuring consistent quality and reproducible output data.
Job Generation
Using the job-creating tool, users can generate a job for repeated analysis of welds on ring-welded specimens, which significantly enhances the workflow. It is possible to check nine polished specimens that can be geometrically measured in one run.
The job is saved in the background during the first examination. The first step involves providing an overview of the image of all samples using the built-in overview camera, as shown in Figure 1.

Figure 1. Generating the overview (map).
The microscope table approaches the first position to be reviewed in the map after clicking it such that the micrograph is generated based on the desired settings. Distance lines for weld penetration depth measurement were generated using the measurement tool, as illustrated in Figure 2a. This shot serves as a template and enables automatic recognition of the weld following the manual approach of the next position with desired magnification.

Figure 2a. Approaching the position, taking the micrograph, 34x, ring light, followed by object recognition for facilitated measurement
The starting points of the distance lines need to be adjusted to achieve appropriate measurement results as shown in Figure 2b. The job is accomplished following the measurement of nine polished specimens, and all measured positions are marked in the map as shown in Figure 3a. The image is acquired by a click on each of the marked position as shown in Figure 3b.

Figure 2b. Adapting the starting points of the distance lines for measuring the penetration depth
Job Operation
In order to operate a job, the polished samples need to be arranged in a certain way as shown in the map in Figure 3a. All the 18 positions need to be studied were automatically approached by the microscope, one by one. In each case, the operator was requested to take micrographs for the given settings as shown in Figure 3b.
The operator needs to adjust the starting points of the measurement lines. A specific report is generated after the job completion, explaining the snapped micrographs and measurement results, which can be saved.

Figure 3a. Marking of all 18 measured / approached positions with flags in the map

Figure 3b. Clicking on the flag shows the recorded image
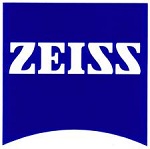
This information has been sourced, reviewed and adapted from materials provided by Carl Zeiss Microscopy GmbH.
For more information on this source, please visit Carl Zeiss Microscopy GmbH.