From scalers and scoops to personnel carriers and pallet handlers, diesel-powered equipment plays a key role in underground mining. Diesel power supplies a reliable, rugged, and economical energy source to the mine.
.jpg)
As expected, underground mining poses various challenges when it comes to the safety and efficient use of diesel-powered mining equipment:
Exposed exhaust and engine components - Diesel exhaust can be very hot. Since underground mine activities often take place within confined spaces, employees are always at risk of severe burns caused by uncovered engine components and exhausts.
High ambient heat – Diesel-powered equipment releases heat that can increase the temperature of an already sweltering underground environment. Moreover, such condition may lead to malfunctioning of heat sensitive sensors and cables.
Diesel particulate matter – It is necessary to have proper filtering of exhaust from diesel powered mining equipment to protect workers from noxious fumes.
Fire safety – Oil from an engine leak or a burst hydraulic hose can start to smoke on contacting exposed exhaust components.
Meeting the Challenges: How Insulation Blankets can Help
An important step to address the challenges of operating diesel-powered equipment is blanketing the exposed exhaust and engine components. Proper insulation not only reduces ambient heat, but also protects personnel from burns. A good ventilation system is indeed important to ensure the removal of hot air, entry of cooled air, and elimination of noxious fumes from the mine.
.jpg)
It is necessary to have pollution control equipment such as particulate filters and catalysts to remove most of the noxious material before it exits the exhaust. With proper insulation, exhaust pollutants can be more effectively burnt by catalysts through the maintenance of an optimal high exhaust temperature as the exhaust moves along the piping and towards the catalyst.
Standard Insulation Blankets: Why They Sometimes Fall Short
The two features of standard insulation blankets make them less suitable for an underground mining environment:
The non-combustible fiberglass material is typically used in the underside of a regular-issue insulation blanket and is secured in place by a wire mesh. While suitable for most applications, in an underground mine, oil from an engine leak, or a broken hydraulic hose line, can seep through an insulation blanket and reach the insulation material. Isolated from the hot component by only a wire mesh, the mixture of insulation material and oil can cause a fire hazard – the last thing one wants in an underground mine.
The outer cover of standard insulation blankets is their second limitation. The outer cover is typically made up of silicone impregnated fiberglass and is engineered to be durable and endure normal tear and wear for several years. However, in an underground mine environment, the potential rock falls and confined spaces can cause sharp objects to contact with insulation blankets. Standard insulation blankets are not designed to survive this kind of treatment, they can be vulnerable to puncture or tearing.
.jpg)
MineWrap™ Insulation Blankets: Designed for the Underground Mine
A blanket was designed by Firwin’s R & D department to address the specific requirements of underground mining. It is called MineWrap™ Mark II, which is equipped with a stainless steel inner liner to seal off the insulation material and prevent any oil from seeping in.
.jpg)
MineWrap Mark II stainless steel inner liner
A Mark III version of MineWrap™ is available for use in applications where extra rigidity and strength is required to reinforce its outer cover. The Mark III blanket consists of a reinforced stainless steel foil exterior, which, in turn, is sheathed by a stainless steel mesh. It is possible to add joint safety seals to further seal off any exposed exhaust between blanket sections.
.jpg)
Thanks to its added features of rugged exterior and increased fire safety, MineWrap™ has turned out to be the preferred insulation blanket for a number of mines and equipment manufacturers.
Firwin Hard Coat™: A Permanent Insulation Solution for Underground Mines
Some underground mines may need a permanent insulation solution for their hot exhaust components. The Hard Coat™ insulation system from Firwin Corporation is an ideal option for such mines. It comprises of a lightweight, durable exterior, and is typically applied to insulate components such as exhaust piping, elbows, turbochargers, and exhaust manifolds. Removable insulation blankets are typically wrapped around an exhaust or engine component and fastened with a fastening system, such as stainless steel lacing wire. However, the Hard Coat™ insulation provides a permanent insulation that can be directly applied to the component being insulated. As a result, the insulation material is completely covered and protected from exterior elements, thereby eliminating the risk of equipment oil or fluid leaks that might otherwise reach the insulation material and lead to a potential fire hazard.
.jpg)
According to Firwin President Paul Herman, “For certain high-temperature applications where safeguarding for oil leaks is a priority, space is at a premium, and a removable insulation product is not required, Hard Coat™ insulation is a definite option, and may be more economical in the long run.”
Paul Herman went on to say that, “While permanent insulation such as Firwin Hard Coat™ has its advantages, for instance it compactness and durability, there are drawbacks as well. It cannot be removed should a part require servicing. The coating must be applied at our factory. It is also more expensive up front than traditional insulation blankets.”
.jpg)
Conclusion
.jpg)
While it is necessary to insulate exposed hot exhaust components in underground mines, selecting the correct insulation solution is also important to avoid any new safety concerns that may arise due to insulation itself. MineWrap™ Removable Blankets and Hard Coat Composite Insulation offered by Firwin Corporation have been developed to provide effective insulation to mining equipment exhaust components to address the safety concerns associated with underground mines.
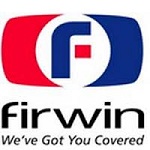
This information has been sourced, reviewed and adapted from materials provided by Firwin Corporation.
For more information on this source, please visit Firwin Corporation.