Toray Advanced Composites provides a range of polyimides, cyanate esters and BMIs that operate in temperature extremes of 260-371 °C (500-700 °F). These specialized materials are available on a wide range of ceramic ad carbon reinforcements, replacing titanium and other metals and providing design flexibility and considerable weight savings.
.jpg)
Through its partnership with PROOF Research™, Toray Advanced Composites is developing advanced, high temperature prepregs for structural, defense and aerospace applications. Under exclusive license, Toray supplies prepregs that are made with P2SI® polyimide resins. P2SI® has extra resins such as NRPE and variants of AFRPE polyimides that Toray supplies as prepregs.
.jpg)
Toray’s high temperature advanced composites are commonly used for:
- Leading edges on hypersonic vehicles
- Jet engines, stators and ducts
- Rocket engine nozzles, thrusters and powerplants
- Heat protection and heat shield systems
- High temperature composite tooling
- Titanium replacement in launch vehicles and aircraft
Product Applications
- Toray’s high temperature epoxy and BMI materials have superior long term thermal resistance and are perfect for nacelle structures.
- Toray's polyimide-based prepregs offer excellent thermal stability and can replace titanium for weight savings. The next-generation military jet engines employ Toray’s high-temperature materials to realize significant weight savings.
- Toray’s Cyanate Esters achieve high Tg with low moisture absorption, ad are ideal for leading edges and heat shields on supersonic vehicles.
.jpg)
Product Overview
Thermoset Prepregs
|
RESIN MATRIX |
DRY Tg ONSET |
CURE TIME AND TEMPERATURE |
KEY PRODUCT CHARACTERISTICS |
RS-8HT |
BMI |
310 °C (590 °F) |
2 hours at 177 °C (350 °F) followed by 6 hours at 232 °C (482 °F) |
• Excellent high temperature thermal stablility
• Good moisture resistance
• Available in RTM resin form |
TC420 |
Cyanate Ester |
176 °C (349 °F) or 348 °C (658 °F) with post cure |
3 hours at 177 °C (350 °F) Optional post cure of 90 minutes at 260 °C (500 °F) |
• Excellent thermal stability
• Epoxy-like processing with Tg of BMI
• Used on heatshields and supersonic leading edges |
RS-51 |
Polyimide AFRPE-4 |
366 °C (690 °F) |
Call for cure details |
• Ultra high service temperature for jet engine applications
• Based on P2SI’s AFRPE-4 |
TC890 |
Polyimide 900HT |
454 °C (850 °F) |
2 hours at 371 °C (700 °F) |
• Non MDA PMR-15 replacement
• Service temperature capability of 538 °C (1000 °F)
• Used in heat shields and ablatives
• Based on P2SI's 900HT |
Film Adhesives
|
RESIN MATRIX |
DRY Tg ONSET |
CURE TIME AND TEMPERATURE |
KEY PRODUCT CHARACTERISTICS |
TC310 |
Epoxy |
157 °C (315 °F) |
2 hours at 177 °C (350 °F) |
• Ideal composite bonding film adhesive |
TC4015 |
Cyanate Ester |
176 °C (349 °F) or 321 °C (610 °F) with post cure |
2 hours at 177 °C (350 °F)
Optional post cure of >60 minutes at 232 °C (450 °F) |
• Excellent high-temperature properties
• Service temperature of 232 °C (450 °F) after post cure
• Compatible with TC420 |
Syntactics
|
RESIN MATRIX |
DRY Tg ONSET |
CURE TIME AND TEMPERATURE |
KEY PRODUCT CHARACTERISTICS |
TCF4001 |
Cyanate Ester |
176 °C (349 °F) |
2 hours at 177 °C (350 °F)
Optional post cure of 60-90 minutes at 232 °C (450 °F) |
• Low density foam 0.35 - 0.42 g/cc (22 - 26 pcf)
• Mechanical properties achieved through OOA/VBO processing |
TCF4050 |
Cyanate Ester |
176 °C (349 °F) or 232 °C (450 °F) with post cure |
2 hours at 177 °C (350 °F)
Optional post cure of 60-90 minutes at 232 °C (450 °F) |
• Expanding syntactic film/core splice
• Density of 0.28-0.55 g/cc (17-35 pcf)
• Tensile strength up to 260 °C (500 °F)
• Compatible with TC420 prepreg system |
SF-4 |
BMI |
295 °C (563 °F) |
2 hours at 204 °C (400 °F), then 6-hour post cure at 250 °C (452 °F) |
• Low-density syntactic film 0.62 g/cc (39 pcf)
• Compatible with RS-8HT and other BMI systems |
.jpg)
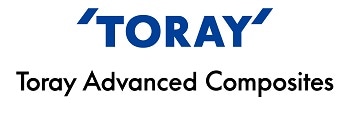
This information has been sourced, reviewed and adapted from materials provided by Toray Advanced Composites.
For more information on this source, please visit Toray Advanced Composites.