Two steel samples in the same mounting.
Purpose of Analysis
To show the ability of the Clemex Inclusion Rating (CIR) system to distinguish, categorize, measure and rate the inclusions present on the samples. The results have to be expressed in accordance with JIS G 0555, ASTM E45 and DIN K standards
Equipment Used
. |
. |
Image Analysis System: |
Clemex CIR |
Microscope: |
Leica DMi8 with a 10x objective for 100x magnification |
Camera: |
Clemex L 1.3MP (1280 x 1024) CMOS B&W |
Stage: |
Motorized Marzhauser (100x100 mm2) with auto focus drive |
Procedures
The analysis was carried out at a magnification of 100X for a calibration factor of 0.7438 µm/pixel. This setup matched with the proposed user magnification.
The first step of the analysis was to adjust the exposure and validate the Threshold, as shown in Figure 1. Based on the gray level, the Threshold defines whether an object is identified or not and whether it is an oxide or a sulfide; oxides are differentiated by their shape.
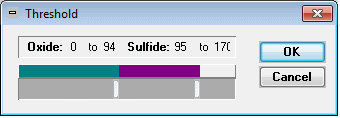
Figure 1. The gray level Threshold detects oxides and sulfides
The second step was to define the number of samples and heats to be analyzed from the WorkPlace window under the Edit option. Up to 6 heats of 6 samples each for a total of 36 samples can be analyzed. In the present project, 2 samples and 1 heat were logged for further analysis.
From the same window, the Pattern option allowed for the required processing data to be specified as shown in Figure 2. For each sample, an autofocus template, a field pattern and the orientation of the inclusions (for reconnection purpose) were specified. The Clemex CIR system immediately indicated the corresponding area covered by the field pattern. Once a sample was analyzed, the "Set" button was keyed in and a new analysis pattern was inserted at the current stage position

Figure 2. Pattern option permits specifying necessary processing information.
Whenever the pattern position needs to be changed, a field of the pattern is doubleclicked, the stage is moved to the corresponding position and the corresponding image appeared in the image window. It must be noted that all the pattern settings have to be loaded back into the Clemex CIR system during the next analysis session.
An analysis pattern of 10x10 fields and an analysis pattern of 15x15 fields were set for the first and second samples, respectively. For each sample, the total analysis area was 71.79 mm2 and 161.53 mm2, respectively. For each pattern, an autofocus template was specified.
From the Run option, the samples to be analyzed were specified. The system preselected all newly defined samples. As soon as the "Start Run" button was keyed in, the Clemex CIR system initiated the analysis taking less than 5 minutes to process the current analysis including the two samples.
Once the analysis was completed, the results window, shown in Figure 3, appeared. The Clemex CIR system subsequently selected the results option from the workplace window. A map of each category of inclusion then appeared on the image window of the currently selected sample, as illustrated in Figure 4. For each category, squares of a particular color indicated the worst fields (heavy and thin). In order to verify the results, the worst fields were doubleclicked, the stage was moved back to the corresponding sample on the corresponding position, and the detected inclusions were finally identified (Figures 5 and 6). If dust or a polishing scratch remaining from the preparation process was identified as an inclusion, it was eliminated from the results by a single click.
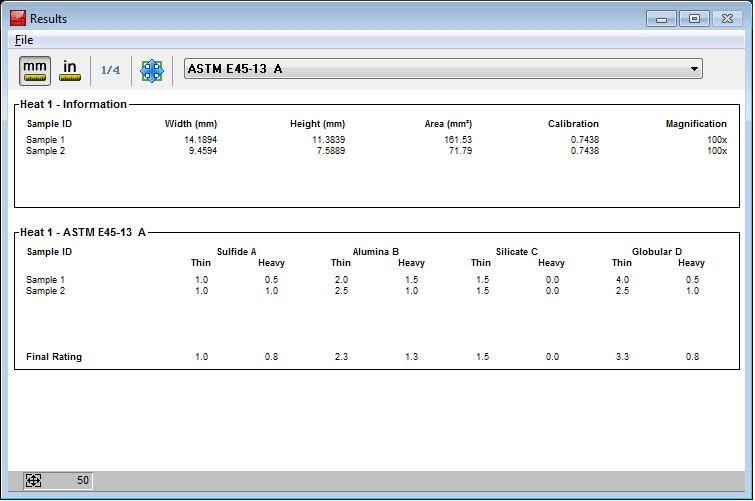
Figure 3. Results window that appears when the run is completed.

Figure 4. Map of inclusions and worst fields (thin and heavy) from sample 2.
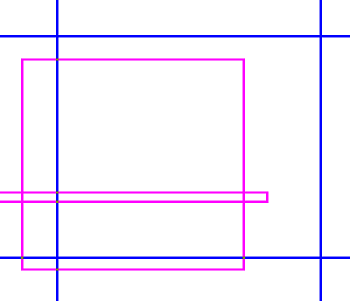
Figure 5. Zoom of the worst field of alumina (heavy) from the map inclusions of sample 1.
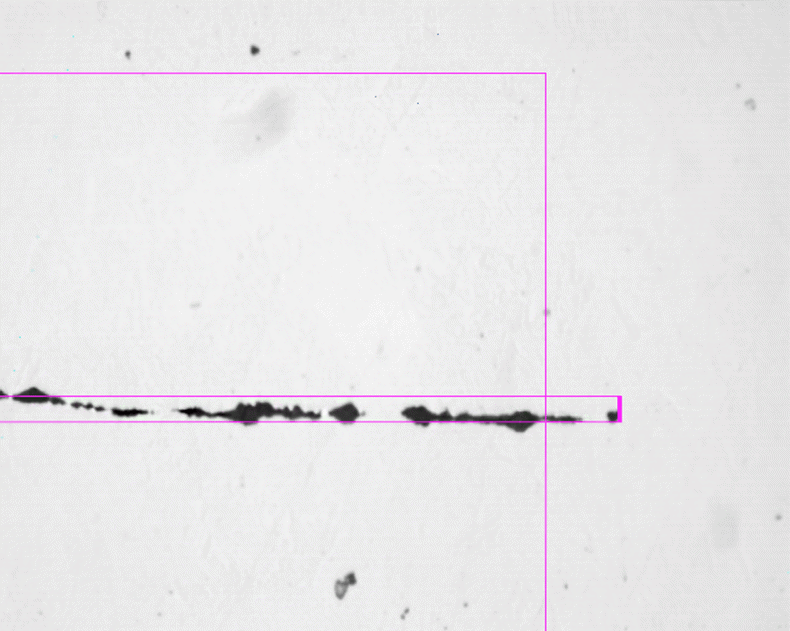
Figure 6. A double-click is performed on the worst field, the stage moves back to the corresponding position on the corresponding sample and shows the detected inclusions.
If an inclusion covered more than one field, the Clemex CIR system reconstructed the entire inclusion from the different components and the whole length was factored into the ratings.
Results
From the Results window, the results expressed in a specific and standardized way were easily accessed. There was a choice of ASTM E 45 A, ASTM E 45 C, ASTM E 45 D, ASTM E 45 E, DIN M, DIN K and JIS G 0555 methods. From the same window, the details of the rated oversize inclusions (type, width, length and sample) were visualized. The first part of the report invariably specified some vital information concerning each sample.
Next, the Clemex CIR results report was printed. The name of the company, the department and the user name were specified, and they all appeared as a header together with the time and date of the printed report. The results obtained can also be exported for later use. In either case (export or print), a specific analysis method, a combination of them, or all of them could have been selected. The oversize listing was not optional and would always show up.
When constructing a report from a text editor, any image can be copied and pasted as required.
The same thing can be achieved with the worst fields and an inclusion map.
Discussion
The Clemex CIR system has been specifically developed for this type of analysis. It can differentiate the silicates from the globulars, the sulfides from the aluminas and rate them in accordance with DIN, JIS and ASTM standards.
With integrated algorithms, the Clemex CIR system discriminates a wide range of inclusions. The analysis time takes about 1 second per field, but it also takes about 2 seconds for each autofocus. For sample 2, the surface required by the ASTM standard (160 mm2) was not considered because the samples were not large enough.
Horizontal polishing scratches and dust remaining from the preparation were detected as inclusions. Although these were effortlessly eliminated from the results, starting with as clean a sample as possible would have decreased the validation processing time.
All the above results obtained are reproducible.
References
1. Results
Clemex CIR Report
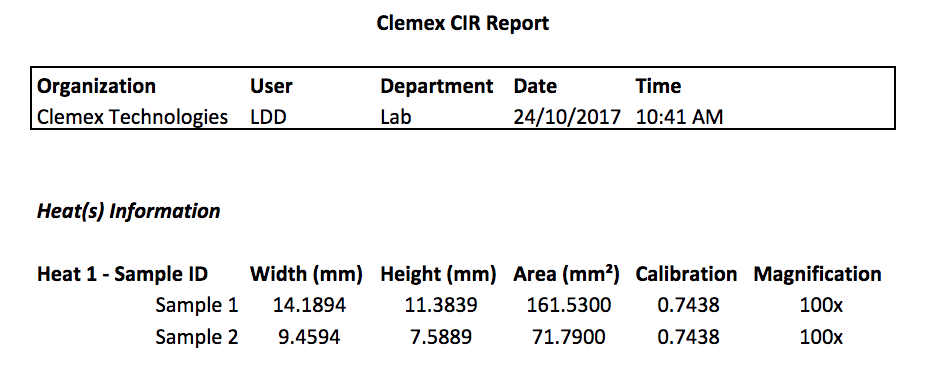
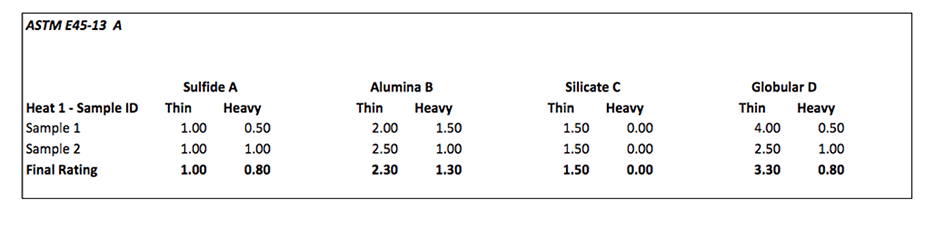
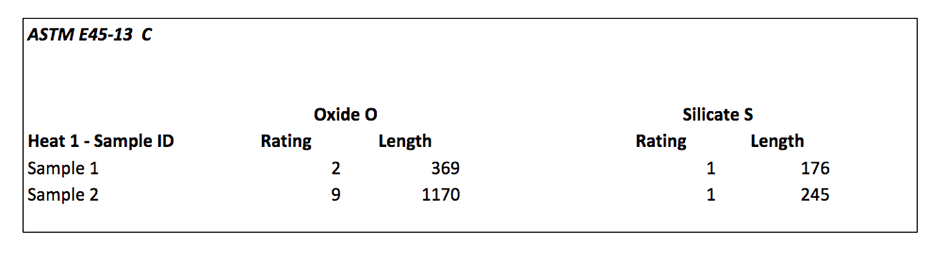
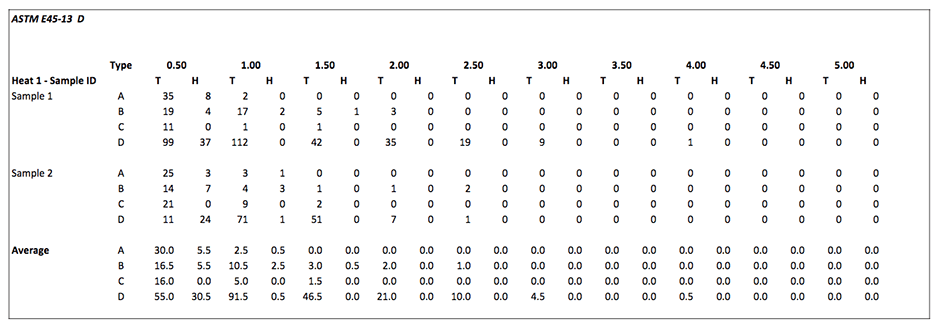
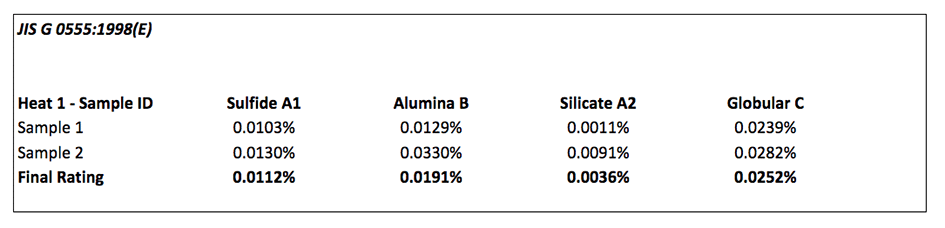
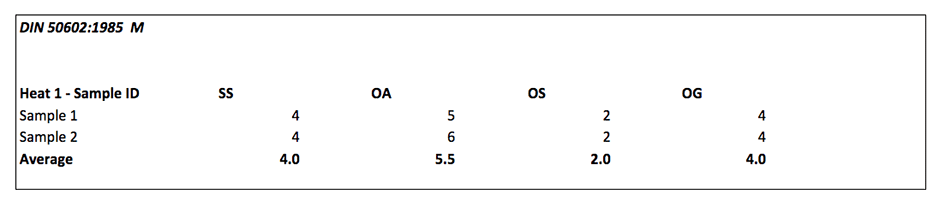
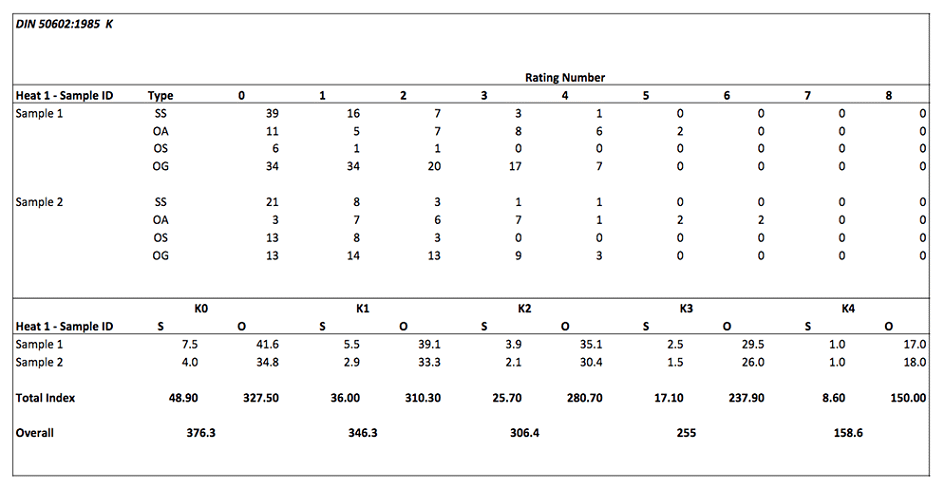
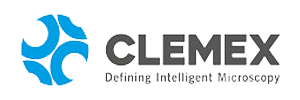
This information has been sourced, reviewed and adapted from materials provided by Clemex Technologies.
For more information on this source, please visit Clemex Technologies.