The incorrect analysis of the carbon content in steel can eventually result in a number of problems, making reliable and accurate carbon analysis very crucial. The OES expert Willy Sanders examines the reason.
.jpg)
Used for almost 2,000 years, carbon steel gained prominence during the late industrial revolution when steel makers really started to exploit the properties that a little carbon can impart to iron products. Compared to raw iron, carbon steel is harder and stronger which makes it suitable in construction and in a whole series of manufacturing contexts. From cooking pots through to buildings and transportation, carbon steel makes life more comfortable.
However, the correct application of carbon requires knowing the accurate carbon content in steel or stainless steel. Despite the strength carbon lends to a given grade of steel, its presence can affect the melting point, brittleness, and workability of the substance. Carbon content between 0.15 and 2% is present in most carbon steel but in alloys such as the L-grade group of austenitic stainless steels the carbon content must be lower than 0.03%. Such small amounts present a challenge in reliably assuring the correct proportions.
Importance of Accurate Carbon Analysis
Incorrect analysis of carbon and L-grade stainless steels can result in numerous challenges. The carbon content of the substance not only decides its strength and its brittleness in application, but also affects the workability of the metal. If an incorrectly graded piece of steel is subsequently worked into a part, it can break because of being too thin or too brittle which, in turn, will result in mechanical failure. This may lead to lawsuits, costly product recalls, and loss of reputation. Therefore, reliable quality control is very important.
In addition, an incorrectly graded piece of carbon or L-grade stainless steel may end up being worked at the wrong temperature or being used in a process it is not suited to. This may eventually destroy the material, adding to waste and additional costs in replacement.
Some of the most common issues caused by incorrect analysis or falsely stamped stainless and carbon steels are discovered after they have been welded. The application of welding techniques and temperatures which are not suitable to the specific metal causes corrosion, discoloration, and even breakage. For instance, years of service life can be lost on an alloy heat exchanger if it is fitted to a flange fabricated from incorrectly specified metal.
Getting the carbon content right is an important concern across industries, from foundries to laboratories and factories.
Positive Identification
Manufacturers, and anyone along the carbon steel supply chain, require an ultra-reliable method for analyzing steel samples for their carbon content before it is being applied. Thousands of steel producers rely on spark optical emission spectroscopy (OES) technology because of its rapid, reliable, and accurate carbon analysis results. OES enables rapid and trustworthy identification of all pertinent elements in steel including carbon, manganese, silicon, sulfur, phosphorous, nickel, chromium, nitrogen, boron, and more — without the inconvenience or expense of sending samples for wet analysis in a laboratory. Additionally, OES is a recommended method for assuring API 5L, and other global industry standards.
Reliable Solution
Both mobile and lab-based OES solutions are available, offering fast and accurate verification of carbon and stainless steel grades. Hitachi High-Tech’s PMI-MASTER Smart is a popular option for companies looking for reliability and versatility, as it is fast, portable, and highly accurate. With multi-CCD optics, a UV Touch Probe, and the capability of displaying and storing data on the go, the PMI-MASTER Smart can be used to test a wide range of metallic samples from huge pressure equipment, construction parts and tubes through to wires measuring only 1 mm in diameter. Results on even the lowest carbon values are available in just under 20 seconds, with a level of detection (LOD) right down to 30 ppm.
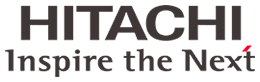
This information has been sourced, reviewed and adapted from materials provided by Hitachi High-Tech Analytical Science.
For more information on this source, please visit Hitachi High-Tech Analytical Science.