Current energy trends that are shifting toward increased use of natural gas can bring about performance and economic benefits under some conditions when taken into account while designing a carbon fiber manufacturing plant. Although electricity supply is considered to be more dependable and consistent, in several regions of the world, it is a more expensive energy source.
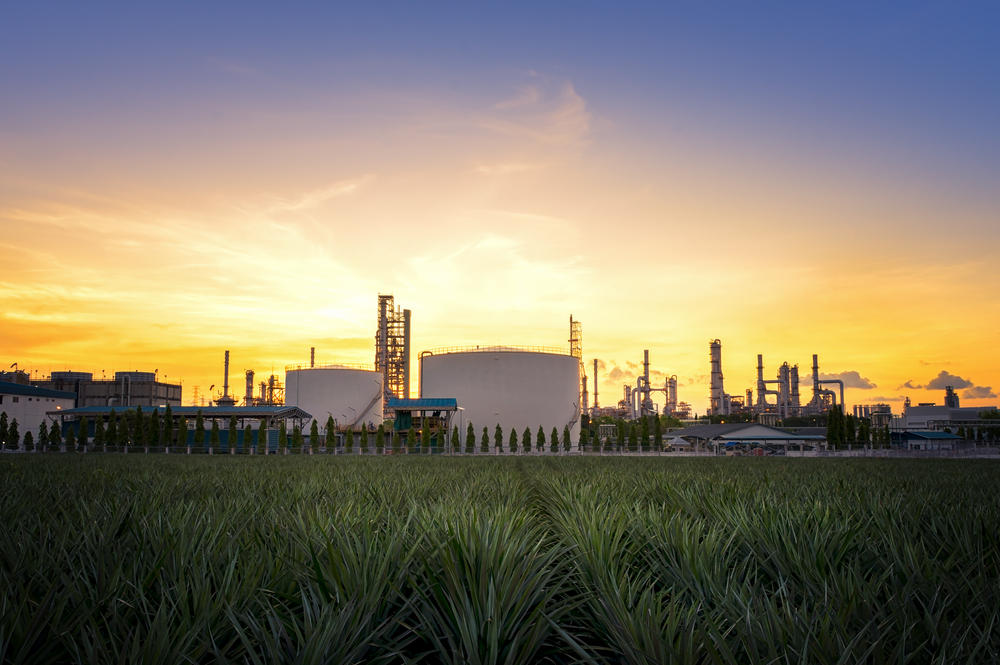
Image Credit: Shutterstock/Aunging
As the industry is striving toward solutions to develop carbon fiber of lower cost, all facets of the production process are closely monitored and the consideration of the usage of natural gas might prove to be crucial in solving the economic puzzle. This article highlights the innovations to enable a shift toward hybrid gas/electric designs and gas-fired units with enhanced thermal uniformity and control, in addition to a focus on decrease in utilities used up in the thermal conversion process. Example scenarios will be demonstrated to reveal the advantages.
Universal Plant Concept Explained
Next-generation carbon fiber plants should be designed from the scratch to function at minimum cost. Although the majority of the industry’s interest until now has been on minimizing overall utility consumption, energy still makes up 5% to 10% of the overall costs for producing carbon fiber [1]. To realize the lowest operating costs possible, carbon fiber plants will need the flexibility to utilize either electric power or natural gas — whichever is cheaper in the given area.
Complicating matters even more, fluctuating energy markets may cause this energy source of choice to change eventually. Hence, the ideal universal plant will have a hybrid design, where the same equipment in a given line is able to function either on electricity or on natural gas.
The oxidation ovens will be the focus of this hybrid technology. Of all the unit operations in a carbon fiber line, the oxidation system takes up the greater part of energy at a ratio of about 4:1. This is because of the high process atmosphere makeup flow rates and long fiber residence time, in relation to the carbonization steps, mandated by the polyacrylonitrile (PAN) oxidation process. Oxidation oven heating consumes about 32%–40% of the energy consumed in a carbon fiber line [2, 3]. Any decrease in power cost here will lead to a major decrease in the overall operating cost of the carbon fiber line.
Universal Technology and How It Works in Practice
Generally, within oxidation, there are four to eight thermal zones extended over two to four large stacks of equipment. On the other hand, a carbonization furnace can have four to ten zones within a single piece of equipment. The ovens are sufficiently large and simple to easily contain redundant heating devices and, considering that the oven process takes up 10 times as much power as the high-temperature or low-temperature carbonization processes (Omnia, LLC, 2012), stand to gain the most from hybrid heating technology. A combination of these factors results in hybrid ovens passing a cost/benefit analysis, while it is not so evident with a carbonization furnace.
A typical oxidation oven zone includes a recirculation fan that blows air over a set of electric heating elements, elevating the temperature of the recirculation air. A temperature controller that maintains a recipe-specific temperature inside the fiber processing chamber controls the power supplied to those heating elements. In a hybrid oven, an indirect, gas-fired heat exchanger is added in series with the electric elements.
As shown in Figure 1, the first temperature controller (gas-fired heat exchanger) set-point would be set manually below the second temperature controller (electric elements). In this manner, the first heater would add a fixed amount of energy, while the second heater would complete the job of increasing the temperature of the recirculating air to the necessary process temperature. In case no gas is needed (electric heating is less expensive), the gas heater will be set to zero and the electric elements will perform all the operations. On the other hand, if no electricity is needed (gas heating is less expensive) the electric heater will be set to zero and the gas will perform all the operations.
.jpg)
Figure 1. Hybrid heating process.
Image Credit: Harper
In case a specific combination of heating sources is preferred (i.e., electric utility company asks for a reduction in consumption during peak summer days), the load could be divided among the two heaters. To heat up the oven in the shortest duration possible on startup, both heaters can be set to 100% output, realizing much more rapid heating than either would alone.
Current and Future Trends in Energy Production and Consumption
Overview
At present, the forecast for the energy industry is greatly different from forecasts in recent years. The new dynamics are affected by the superfluity of supply in the market, which is partially brought about by an overall reduction in demand and by new supply discoveries. These forces have hugely transformed the dynamics of energy in the international marketplace. Companies can capitalize on these geopolitical paradigm shifts for strategic benefits for a long period of time.
Recent Developments in Natural Gas in North America
Naturally occurring gas has been known since ancient times. However, its commercial use is comparatively recent. At present, natural gas is a crucial component of the global energy supply. Currently, natural gas supplies over one-half of the energy used by commercial and residential customers, and approximately 41% of the energy consumed by U.S. industries [5].
In North America, utility markets have undergone an extraordinary shift in recent years. The most distinguished change has been the increased production from the natural gas deposits in the Haynesville Shale in Louisiana; the Marcellus region in the eastern portion of the U.S. including New York, Pennsylvania, Ohio, West Virginia and a small portion of Virginia; the Eagle Ford Shale in southern Texas; and in the U.S. Gulf Coast.
According to IHS Energy, for instance, in the next three years, the Marcellus Shale region alone looks forward to seeing around 17 pipeline projects intended to ship about 17.3 billion cubic feet of natural gas every day out of Ohio, West Virginia, and Pennsylvania to end-users.
In North America and other places, these recent findings have stimulated policy-makers and energy experts to focus on natural gas as the main driver to achieve an extensive range of objectives: reducing dependence on foreign oil, easing the impact of energy-price spikes, speeding the transition to renewable fuels, and lowering greenhouse gas emissions.
Natural Gas Rise in North America
The Energy Information Administration (EIA) stated that in 2014, U.S. net imports of natural gas saw a 9% drop — keeping with an eight-year decline. Since U.S. dry natural gas production has attained record highs, lower domestic prices (as illustrated in Figure 2) have assisted in displacing natural gas imports. In 2014, the net natural gas imports (imports minus exports) equaled 1171 billion cubic feet (Bcf) — the lowest level since 1987.
Almost 98% of all U.S. natural gas imports are imported by pipeline from Canada, acting as the main cause of the decline in total imports. In 2014, net imports from Canada accounted for 7% of total U.S. natural gas consumption, dropping from 11% in 2009.
The exports of U.S. natural gas also decreased in 2014, but not as fast as the decrease in imports, and were still 9% above the previous five-year average. Natural gas exports to Mexico, which represent almost 50% of U.S. natural gas exports, went up 12% in 2014.
In North America, crude oil, refined into diesel or gasoline, fuels almost all U.S. trucks or cars. Coal is predominantly used for producing electricity. However, with greenhouse gases continuing to affect the environment, charting a transition to a low-carbon economy will continue at a tremendous speed in North America and other regions. This change will essentially transform the economy and utility infrastructure as it is currently known.
With the market still being largely fragmented and underdeveloped with huge supply reservoirs, a future of new policy implementation and uneven development will define the marketplace in the future.
.jpg)
Figure 2. Energy Pricing in North America by Industrial Sector Pricing.[6]
Image Credit: Harper
Future Energy Infrastructure in North America
EIA, in its Annual Energy Outlook 2015, [7] concludes that by 2040 dry natural gas production will be the largest contributor to total U.S. energy production, giving it a 34% share.
According to the EIA, dry natural gas accounted for 30% of total U.S. energy production in 2013. Coal’s share of total U.S. energy production continues to be slightly above 20% of total U.S. energy production through 2040.
In 2013, coal accounted for 44% of total generation fuel costs, and natural gas made up 42%. In 2040, coal accounts for only 35%, when compared to 55% for natural gas. In 2013, oil, the most expensive fuel for generation, accounted for 6% of the total generating fuel costs and from 2019 through 2040, it accounts for just 3% of the total. According to the EIA outlook, nuclear fuel accounts for 6% to 8% of electricity generation fuel costs through the entire projection period.
Natural gas will play a significant role in North America’s energy infrastructure. Figure 3 depicts that natural gas production is considerably higher and cost is significantly lower in the US when compared to the rest of the world. The industry continues to expand its investments in infrastructure as policy makers in Washington, DC continue its expansion by supporting lucrative investment environmental standards. This will continue the trend of lower gas pricing for industrial users, considerably lower than electric in all categories. Due to the heavy energy usage of carbon fiber oxidation ovens and low temperature furnace technology, gas-fired technologies will drive investment decisions well into the future. Harper International is a pioneer in gas-fired, electric, and hybrid oven and furnace technologies.
.jpg)
Figure 3. World Liquified Natural Gas Estimated November 2013 Landed and Hub Prices $US/mmbtu.[8]
Image Credit: Harper
Theoretical Case Study
Effects of Hybrid Oxidation Technology on Operating Expense
In this section, a theoretical analysis of three carbon fiber lines and the impact of different oxidation energy sources on operating expense (OpEx) are considered.
Line 1 – 3 meter – Current industry standard production scale
Line 2 – 4 meter – Upcoming production scale
Line 3 – 5 meter – Future production scale
The following are two different ways of powering these lines:
Scenario 1 – Electric Oxidation
Scenario 2 – Gas Oxidation
Table 1. Major Assumptions Used for Calculations.
Line Size |
Tow Type |
Line Speed |
Tow Count |
Production Capacity (Tons/Year) |
Electricity Cost |
Natural Gas Cost |
3 Meter |
48 k |
10 m/min |
130 |
2007 |
7.04 ¢/kWh |
1.87 ¢/kWh |
4 Meter |
174 |
2686 |
5 Meter |
217 |
3349 |
These process parameters were used as inputs to Harper’s standard process models to predict the estimated energy consumed by heating the oxidation systems in three lines. In turn, these energy consumption values were multiplied by Industrial Sector costs of both gas and electricity obtained from the US Energy Information Administration’s Short Term Energy Outlook.[9] Figure 4 shows the results.
.jpg)
Figure 4. Calculated Annual Cost of Oxidation, 2014.
Image Credit: Harper
The benefit of natural gas isn’t always so great. Six years earlier costs were as represented in Figure 5.
.jpg)
Figure 5. Calculated Annual Cost of Oxidation, 2008.
Image Credit: Harper
The cost of natural gas and electric heating are much closer in other parts of the world. There are even times, such as off peak times when demand on the electric grid is low, when it is in fact cheaper to heat the oxidation ovens with electricity than with natural gas.
Effects of Gas Fired Low Temperature Carbonization on Operating Expense
To show the complexity of the issue, the effect of selecting a gas or electric low temperature (LT) carbonization furnace is considered. Increasing the process temperature will decrease the efficiency of gas heating. [10] A fairly typical temperature profile and zone count was assumed when modeling gas energy and electricity consumption. Shown in Figure 6 is the resulting cost to heat the LT furnace at 2014 utility costs. The results of the same calculations, but using 2008 utility costs are shown in Figure 7.
Table 2. LT Zone Temperatures and Natural Gas Efficiencies.
Zone |
Temperature Setpoint
(°C) |
% Available Heat
(Assume 50% Excess Air) |
1 |
400 |
72 |
2 |
450 |
68 |
3 |
500 |
66 |
4 |
600 |
58 |
5 |
700 |
53 |
6 |
750 |
49 |
7 |
700 |
53 |
Table 3. Resulting Energy Consumption Predictions.
|
Meter |
4 Meter |
5 Meter |
LT - Electric (kW) |
297 |
387 |
476 |
or |
|
|
|
|
LT - Natural Gas (m3/hr) |
66 |
87 |
106 |
.jpg)
Figure 6. Calculated Annual Cost of Low Temperature Carbonization, 2014.
Image Credit: Harper
.jpg)
Figure 7. Calculated Annual Cost of Low Temperature Carbonization, 2008.
Image Credit: Harper
In 2008, heating a Low Temperature carbonization furnace with electricity would have been cheaper than with natural gas. This year was an anomaly, when the cost of natural gas in the United States was temporarily inflated by market forces. The intention of this analysis is that even in regions such as the United States, where the cost of natural gas is usually lower than electricity, the choice is not always clear. Here the heating source preference would be as follows:
Good – Electric Ovens, Gas LT
Better – Gas Ovens, Gas LT
Best – Hybrid Ovens, Gas LT
This good/better/best scenario of gas vs. electric heating applies to regions where natural gas is consistently the lower cost energy source. It may vary in other parts of the world. Therefore, a hybrid plant design is universally optimal.
Other Considerations
Reliability
In a hybrid oxidation system, the redundant heating sources would result in greater reliability. The electric heating elements and gas fired heat exchangers would both be sized for the full heating load for housing either electric or gas heating entirely. Therefore, simple reliability through redundancy would be achieved. In case a heating source fails, the other would be able to sustain operation until the end of the campaign when the faulty unit can be replaced.
Daily Operation
Electric utility companies usually structure their customer contracts in such a way that there are expensive penalties for high consumption during peak demand times, such as mid-day in the summer months. In order to avoid this, plants that can effectively scale back often reduce their production during these times. For instance, during mid-day hours in the summer, industrial gas plants generally reduce the output of their cryogenic air separation units.
However, this is not an option for carbon fiber lines where a reduction in output during a campaign, for example slowing the line speed, would alter the time/temperature recipe and thus ruin the product fiber. Diverting some of the load to a secondary heating method (natural gas) during the peak hours is the only way to reduce electricity consumption during a campaign.
High Temperature and Ultra High Temperature Furnaces
High temperature (HT) and ultra-high temperature (UHT) — the last thermal processing steps in a carbon fiber line) — are not discussed here. These processes operate between 1200 °C and 2800 °C. As processing temperature increases, the efficiency of natural gas decreases. Therefore, natural gas generally makes sense for the oxidation ovens (250 °C) as well as for the LT Furnace (800 °C), but it is not a feasible option for the HT and UHT furnaces. The preferred technology in these processes is electric heating.
References
1. Alexander Coker, J. G. (2011). Carbon Fiber PERP 2011S9. White Plains NY: CHEMSYSTEMS
2. Warren, C. D. (2010, June 9). Low Cost Carbon Fiber Overview. Oak Ridge, Tennessee, USA: Oak Ridge National La-boratory / US Department of Energy
3. Stry, B. (2013). How Mass Automotive Use Will Affect The Way Carbon Fiber Producers Must Think About Their Facili-ty's Carbon Footprint. GoCarbonFiber. Seattle.
4. Omnia, LLC. (2012). Assessment of Carbon Fiber Manufacturing Costs. INVEST in Iceland.
5. A Brief History of Natural Gas. (2012). Retrieved June 29, 2014, from American Public Gas Association
6. Energy, U. D. (2015, June 9). Short Term Energy Outlook. Retrieved June 25, 2015, from US Energy Information Admin-istration: http://www.eia.gov/forecasts/steo/tables/?tableNumber=8#
7. Conti, J. J., Paul, D. H., James, R. D., Sam, A. N., Michael, S., James, T. T., et al. (2015). Annual Energy Outlook 2015. Washington, DC: US Energy Information Administration.
8. Pascual, C. (2013). Global Energy Outlook. Atlantic Council Energy and Economic Summit (p. 18). Istanbul: The Atlantic Council.
9. Energy, 2015
10. Reed, R. J. (1986). North American Combustion Handbook. Cleveland, OH: North American Mfg. Co.
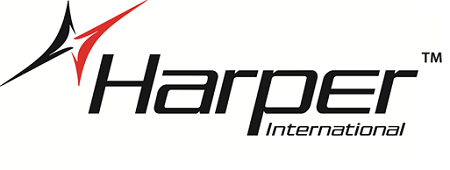
This information has been sourced, reviewed and adapted from materials provided by Harper International.
For more information on this source, please visit Harper International.