As part of TAPAS 2 (Thermoplastic Affordable Primary Aircraft Structures 2), a Dutch innovation program, NLR has developed a method to manufacture thick and large thermoplastic composite parts using AFP (Advanced Fiber Placement).
The part, manufactured using Toray Cetex® TC1320 C/PEKK unidirectional tape, measures 6 meters long and has a thickness of 28 millimeters.
Aircraft manufacturers can reduce weight and production costs by using a pylon upper spar made of composite instead of steel, thereby reducing fuel consumption of aircraft.
Toray Cetex® TC1320 C/PEKK Unidirectional Tape
- Good impact resistance and toughness
- Resistant to solvents and chemicals
- Flame retardant
- Low moisture uptake, good hot/wet strength retention
- Good compression after impact performance
Toray® C/PEKK unidirectional tape is appropriate for automated fiber placement, which when combined with excellent mechanical properties, allows efficient automated production of a high-performance aerospace structure.
Using its sophisticated fiber placement machine, NLR laid elongated thermoplastic tracks beside each other and then “fused” them to form a pylon upper spar in Fokker’s autoclave. By using AFP, locale build-ups can be made without scrap edges and as a result, the “buy-to-fly ratio” of the material is high.
Recyclable
It is more sustainable to manufacture a composite pylon upper spar than making a structure that contains steel. Only little residual material is left by the cutting process, and the remaining is recyclable. In addition, the pylon upper spar itself can be fully shredded and reused at the end of its service life. The technique developed by NLR is not only suitable for other aircraft parts, such as stabilizer spars, wing spars, and floor beams, but also appropriate for applications outside the aviation sector.
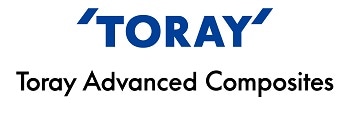
This information has been sourced, reviewed and adapted from materials provided by Toray Advanced Composites.
For more information on this source, please visit Toray Advanced Composites.