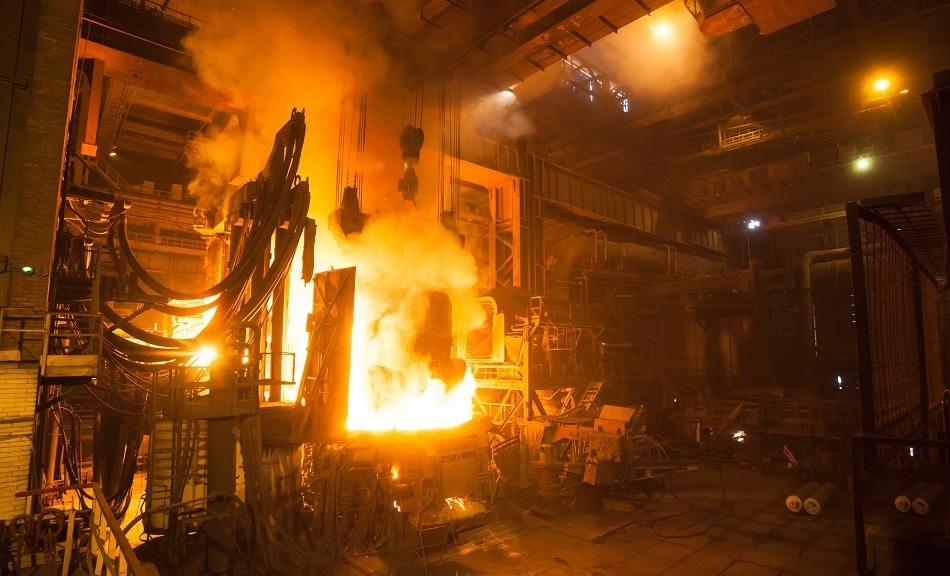
Image Credits: Norenko Andrey/shutterstock.com
Furnaces are used for many reasons and across many industries, with some of the most widely used applications being in heat treatment and smelting applications. Whilst single chamber furnaces can be sufficient for many people, multi-chamber furnaces offer a greater number of benefits, wider scopes and are often required for higher quality processes. In this article, we look at why multi-chamber furnaces should be used in lieu of single-chamber furnaces.
There are many variations that can be employed for use with furnaces, regardless of the class, and these variations can be exploited depending on the required application. Some common examples include their loading type (horizontal or vertical), internal load movement, heating design, whether they are used for a continuous or batch process, their size, production capability and how many chambers they possess. Here, we are concerned with the last point because it is one of the most crucial, and we look at a couple of different furnace types.
Scrap Metal Furnaces
Scrap metal furnaces can melt (or alloy) a wide range of metals. However, because metals melt at different temperatures, multiple furnaces need to be used if there is more than one metal in question. It is not only the type of metal that plays a role in how quickly a metal is melted, the size and form of which it is in key. The most common forms from which metals can be melted include sows, ingots and various sizes of scrap metal.
Multi-chamber furnaces are employed with different heating capabilities depending on the type and form of the metal and its relative size. This is particularly important when a large amount of material is being melted but comes as a collection of different forms. Some furnaces can even come equipped with a molten liquid area (combined with an electromagnetic stirrer) for very light metals.
The benefits of having a multi-chamber furnace not only includes different heating environments, it means that pre-heating chambers can also be combined with the furnace to provide an eco-friendlier approach; because the heat can uniformly pre-heat materials before heading into the high intensity furnace and can pre-melt some pieces of scrap with lower melting-points.
Individual multi-chamber furnace systems can bring a wide range of benefits for scrap metal melting, including high metal recovery rates, a high rate of melting, the ability to submerge materials using a liquid melt, low losses when making alloys, automatic scrap charging, gasification of organic impurities, ability to perform near-continuous heating, lower energy usage and/or no interruption of burning activities from charging and melting processes.
Vacuum Furnaces
Vacuum furnaces are often used for high pressure gas quenching (HPQC) and low-pressure carburization (LPC) applications. Also, all most all heat treatments processes performed by industry, from brazing, to annealing, sintering and tempering, are performed within a vacuum atmosphere, because it provides a better metallurgical output for the material(s) in question.
Vacuum furnaces use both heating and quenching processes to heat and subsequently cool the material undergoing the procedure. However, single chamber furnaces are not ideal for many applications because the heating process and the quenching process are separated, and do not occur within the same system.
By introducing more than one chamber into the furnace, both processes can be performed within the same contained atmosphere and can also enable selective quenching to take place. So, whilst the cold quenching and heating compartments are kept separate, they are still within the same instrument and are separated by insulating doors (heating compartment) and pressure-tight doors (quenching section), with a transfer module in the middle to switch the material between the compartments. The quenching processes can be performed at both high and low pressures, which is why both HPQC and LPC are viable using these furnaces.
The benefits of using a multi-chambered vacuum furnace include a higher throughput with a decrease in energy use, more flexible use for different batch sizes, a higher load capacity, higher surface areas that can be quenched, the reduction of localized hot zones and a higher control for both the gas and heat distribution within the chambers.
Other benefits can also be incorporated depending on the type of furnace used, and examples of using high quality furnaces include accurate radial or axial gas flows, uniform quenching, careful distribution of cooling and a high degree of uptime productivity.
Sources and Further Reading
Disclaimer: The views expressed here are those of the author expressed in their private capacity and do not necessarily represent the views of AZoM.com Limited T/A AZoNetwork the owner and operator of this website. This disclaimer forms part of the Terms and conditions of use of this website.