Compressed Air is regarded as the fourth utility next to power, water and fuel (natural gas), and generally the one that all customers should produce and provide themselves. Compressed air is the preferred energy to power a wide range of applications across fleet and industrial applications. As compressors are vital for supplying power for a range of machines throughout a plant or on a vehicle, uptime and reliability of compressors are very important.
Oil analysis is a vital tool used to make sure that compressors stay up and running and that spontaneous downtime is reduced. The below “Ask the Expert video” describes the components of a compressor that are usually monitored using oil analysis, the types of tests normally run on the oil, the types of on-site instruments most appropriate for performing those set of tests, and the most common failure modes for compressors.
Ask the Expert: Compressor Oil Analysis
Types of Compressors
Compressors are similar to pumps in the sense that both move a gas or a liquid through a mechanical system by increasing the pressure on it. These mechanical devices are focused on compressing and moving gases. Air compressors generally take in a large volume of air and compress it to a smaller volume, thereby increasing the pressure enormously.

With regards to pumps, compressors are categorized into positive displacement and dynamic styles, according to working principle or technology. The market is categorized into rotary, reciprocating, and centrifugal compressors. The rotary/screw segment made up more than 45% of the global market in 2014, with compressed air being the leading application.
Oil-free air compressors make up 30% of the compressed air market. This growth is attributed to an increasing need for high-quality compressed air usually for food and beverage or pharmaceutical manufacturing. The term "oil-free" merely implies that the gas is not combined with lubricant.
The component that has to be lubricated and monitored for all compressors is bearings. Rotary positive displacement compressors also have lobes, vanes, or screws which are lubricated, typically by the fluid they are pumping, be it an oil /air mix or a lubricant.
Providing heat removal in the air end is one of the most critical roles of a compressor lubricant. A lot of heat is generated as the air is compressed. If this heat is not eliminated swiftly, the gears, seals, and bearings will all fail quickly. Poor heat removal can be traced to incorrect lubricant type or contaminated lubricant being used.
Contaminated lubricant (also called coolant, due to its heat removal importance) can occur as a result of inlet air quality problems such as:
- Particle-laden air (clogged filters)
- External air contamination (SOx, NOx from nearby engine exhaust)
- High moisture (no air driers, or saturated coalescers filters)

Taking this into account, it then makes sense to monitor the oil for contamination caused by particles in the air such as dirt and sand. In addition, it is important to monitor the oil for water, which would not only cause corrosion in the system but would also affect the acidity and viscosity of the lubricant.
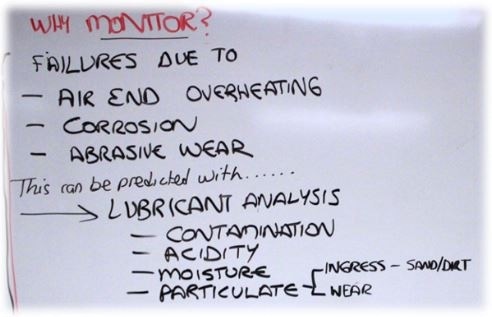
Tests to be Run on Compressor
In regards to any mechanical system, viscosity is a crucial test to run on the compressor oil. Variations in viscosity are typical indications of some other failure mode happening. Testing for water contamination is crucial to ensure that moisture is not entering the system. IR and TAN confirm whether the oil is being degraded because of acid formation from moisture or excessive heat. Particulate count and classification can be used to determine if external contamination is entering into the system owing to bad air filters or if mechanical wear is occurring that might lead to a failure. Through elemental analysis, it can be determined where particulates are originating and whether the oil’s additive levels have been used up.

Wear Debris Analysis (WDA) and Ferrography are the optional tests one might need to consider for compressors. WDA depicts either a patch or an analytical method which isolates magnetic wear particles from the oil and deposits them on a glass slide called a ferrogram. Microscopic examination of the patch or slide allows characterization of the wear mode and potential sources of wear in the machine. This method is called analytical ferrography and is an excellent indicator of abnormal non-ferrous and ferrous wear, but it is generally performed only by a trained analyst.

Using the MiniLab Series of analyzers, the recommended tests can be easily conducted on-site for industrial settings. The MiniLab 23 and 33 are capable of measuring the chemistry and oil condition. The MiniLab 53 analyzer measures ferrous wear after counting and categorizing particles, and the MiniLab 153 analyzer adds an elemental spectrometer to study the concentration of additives and wear metals.
The MicroLab 40 oil analyzer is recommended for mobile applications such as mining, trucking, and other heavy equipment.


This information has been sourced, reviewed and adapted from materials provided by AMETEK Spectro Scientific.
For more information on this source, please visit AMETEK Spectro Scientific.