The LTF-631 High Speed Dielectric Cure Monitor was employed to observe the curing behavior of Bulk Molding Compound (BMC). Bulk Molding Compound is typically of identical material to Sheet Molding Compound (SMC), merely in bulk form, thus the evaluation of findings can also be applied to SMC. The data from dielectric cure monitoring (DEA) plainly indicates:
- Critical Points classify distinguishing features of the cure, including minimum ion viscosity, maximum slope of log(ion viscosity) and the time to an elected end of cure.
- Cure time decreases and reaction rate rises alongside rises in cure temperature, as anticipated for a reaction that is thermally induced.
Definitions
This article introduces and analyzes data for log(ion viscosity) and slope of log(ion viscosity), which signify the state of cure. The plots display distinguishing features, including minimum ion viscosity, maximum slope of log(ion viscosity) and the time to an elected end of cure.
In order to be concise, log(ion viscosity) will be referred to as log(IV) and slope of log(ion viscosity) will simply be known as slope.
Electrical conductivity (σ) has both frequency independent (σDC) and frequency dependent (σAC) constituents. In an oscillating electric field, σDC is a result of the flow of mobile ions, while σAC is a result of the rotation of stationary dipoles. These two responses function as electrical elements in parallel and are added together as indicated below:
(eq. 38-1) |
σ = σDC + σAC |
(ohm-1 – cm-1) |
Resistivity (ρ) is the inverse of conductivity and is represented as:
(eq. 38-2) |
ρ = 1/σ |
(ohm-cm) |
From its relationship to conductivity, resistivity also has both frequency independent (ρDC) and frequency dependent (ρAC) constituents. The levels of polymerization or crosslink density, which are measures of cure state, have an impact on both mechanical viscosity and the movement of ions, and thus, influence ρDC.
Subsequently, the term Ion Viscosity was devised to highlight the relationship between mechanical viscosity and ρDC. Ion viscosity (IV) is represented as:
(eq. 38-3) |
IV = ρDC |
(ohm-cm) |
While the strict definition of ion viscosity is frequency independent resistivity, ρDC, for ease, it is possible to use ion viscosity to describe resistivity in general, which has both frequency independent (ρDC), as well as frequency dependent (ρAC) constituents. Nonetheless, it should be noted that cure state and mechanical viscosity relate most effectively to frequency independent resistivity, ρDC, which is true ion viscosity.
Characteristics of Thermoset Cure
In a lot of instances, the transformation of log(IV) is relational to the transformation of mechanical viscosity before gelation and still indicates cure state, even following gelation. A plot of Ion viscosity is an easy method through which to portray the progress of cure. In basic form, Figures 38-1 and 38-2 display the behavior of a representative thermoset with one temperature ramp step and one temperature hold step.
.jpg)
Figure 38-1. Typical ion viscosity behavior of thermoset cure during thermal ramp and hold.
.jpg)
Figure 38-2. Ion viscosity curve and slope of ion viscosity of thermoset cure during thermal ramp and hold.
Initially, as temperature rises, ion viscosity drops due to the thermoset becoming more fluid and as a result, less resistive. The reaction rate increases alongside the temperature of the material. At a point, the rise in ion viscosity resulting from polymerization overwhelms the drop in ion viscosity resulting from rising temperature. This point is the ion viscosity minimum, which also happens at the time of minimum mechanical viscosity.
Following the minimum point, ion viscosity rises steadily until the concentration of unreacted monomers lessens and the reaction rate drops off. Subsequently, the slope of ion viscosity also dwindles until finally, ion viscosity will have zero slope once cure has entirely ceased.
Four Critical Points are characteristic of the dielectric cure curve:
- CP(1)—A user defined level of log(IV) that is usually employed to detect the start of material flow at the beginning of cure.
- CP(2)—Ion viscosity minimum, which also links to the physical viscosity minimum. This Critical Point specifies the time when polymerization and the resulting rising viscosity begin to dominate the decreasing viscosity as a result of heating.
- CP(3)—Inflection point, which pinpoints the time when the curing reaction begins to slow. CP(3) is frequently used as a signpost that can be linked with gelation. The height of CP(3) is a relative measure of the reaction rate.
- CP(4)—A user defined slope that can define the end of cure. The decreasing slope aligns with the decreasing reaction rate. It is important to note that dielectric cure monitoring continues to reveal changes in the evolving material, beyond the point when measurement of mechanical viscosity is not viable.
Figures 38-1 and 38-2 exemplify the characteristic behavior of curing thermosets when temperature slowly ramps to a hold value. When the material under test is essentially isothermal, the response is somewhat different, as can be seen in Figure 38-3.
.jpg)
Figure 38-3. Ion viscosity curve and slope of ion viscosity of thermoset cure during isothermal processing.
In this instance, CP(1) is either not meaningful, or occurs at t = 0, directly following the application of heat, when material flows to make contact with the sensor. Minimum ion viscosity also takes place at t = 0, or shortly afterwards, since the onset of cure is immediate.
For isothermal cures, CP(3) and CP(4) are theoretically the same as for ramp and hold conditions.
Procedure
Samples of BMC were positioned on disposable Mini-Varicon sensors, as seen in Figure 38-4, then compressed and cured in the Lambient Technologies LTP-250 MicroPress. This equipment applied pressure and heat for discrete runs at 130 °C, 140 °C, 150 °C, 160 °C and 170 °C. Earlier tests had pinpointed 100 Hz as an optimum excitation frequency for cure monitoring.
.jpg)
Figure 38-4. Mini-Varicon sensor.
An LTF-631 High Speed Dielectric Cure Monitor measured the dielectric properties of each sample, since the cure time for these samples is under two minutes. The measurement interval was 100 ms/data point and a trigger on the LTP-250 started data acquisition at a constant point in the compression cycle.
The data was gathered and stored using Lambient Technology’s CureView software, which was used again later to perform Critical Point analysis and presentation of the findings.
Results
Figures 38-5, 6, 7, 8 and 9 display data from the cures of BMC at 130 °C, 140 °C, 150 °C, 160 °C and 170 °C, in that order. For each cure, log(IV) and slope reflect the usual behavior of Figure 2. This sequence of plots clearly indicates the ability of dielectric cure monitoring to observe the effect of temperature on cure
.jpg)
Figure 38-5. 130 °C BMC cure data at 100 Hz.
.jpg)
Figure 38-6. 140 °C BMC cure data at 100 Hz.
.jpg)
Figure 38-7. 150 °C BMC cure data at 100 Hz.
.jpg)
Figure 38-8. 160 °C BMC cure data at 100 Hz.
.jpg)
Figure 38-9. 170 °C BMC cure data at 100 Hz.
As would be anticipated for a thermally stimulated reaction, the log(IV) curves rise and flatten at a greater pace as temperatures rise. The ion viscosity minimum— CP(2)—and the peak slope—CP(3)—also happen earlier at higher temperatures.
Moreover, the peak value of CP(3), which is linked to the maximum reaction rate, grows with temperature. Following the acquisition of this data, CureView was able to extract the Critical Points that typify each cure and enable direct comparison of their behavior across the temperature range.
Figure 38-10 overlays the log(IV) and slope curves for 140 °C, 150 °C and 160 °C in a stacked format. For clarity, the data for 130 °C and 170 °C is omitted. This comparison highlights the sensitivity of dielectric cure monitoring to variations in cure arising from fluctuating temperatures.
.jpg)
Figure 38-10. Overlay of 140 °C, 150 °C and 160 °C BMC cure data at 100 Hz.
As anticipated, the maximum value of slope increases with process temperature, indicating the relationship between reaction rate and temperature.
Critical Points that are characteristic of each cure are displayed in Table 38-1, with the following notes:
- The time to CP(1) indicates the beginning of flow and is not a measure of cure, so CP(1) data is not displayed.
- The slope of 0.1 to define CP(4) was randomly chosen. In reality, a user must ascertain an appropriate slope based on the requirements of the application to indicate end of cure.
Table 38-1. Critical Points from BMC cure monitoring.
Cure Temp.
(°C) |
CP(1) Crit. Visc. |
CP(2) Min. Visc. |
CP(3) Max Slope |
CP(4) End of Cure |
Value |
Time |
Value |
Time |
Value |
Time |
Value |
Time |
130 |
--- |
--- |
7.77 |
0.164 m
(9.8 s) |
2.93 |
0.681 m
(40.9 s) |
0.10 |
2.138 m
(128.3 s) |
140 |
--- |
--- |
7.74 |
0.157 m
(9.4 s) |
5.58 |
0.373 m
(22.4 s) |
0.10 |
1.321 m
(79.3 s) |
150 |
--- |
--- |
7.72 |
0.153 m
(9.2 s) |
9.36 |
0.249 m
(14.9 s) |
0.10 |
0.908 m
(54.5 s) |
160 |
--- |
--- |
7.71 |
0.135 m
(8.1 s) |
15.42 |
0.189 m
(11.3 s) |
0.10 |
0.681 m
(40.9 s) |
170 |
--- |
--- |
7.66 |
0.144 m
(8.6 s) |
18.14 |
0.180 m
(10.8 s) |
0.10 |
0.517 m
(31.0 s) |
As plotted in Figure 38-11, the times to reach each Critical Point are lower for cures at hotter temperatures, which is predictable in thermally stimulated reactions.
.jpg)
Figure 38-11. Critical Point time vs. cure temperature for BMC.
The time to Critical Point 2—CP(2)—is the point when the BMC has the lowest mechanical viscosity. This information is frequently helpful in identifying the ideal time to apply compression to squeeze out voids, consolidate the layers of a laminate or fill a mold.
The time to Critical Point 3—CP(3)—specifies the moment of the speediest reaction. Before CP(3) the reaction is quickening, as temperature rises from the exotherm and external heating. After CP(3) the reaction decelerates, as the network grows and monomers are depleted. While CP(3) is not the gel point, CP(3) is frequently used as a signpost linked with the gel point.
The time to Critical Point 4—CP(4)—is the time to a user defined slope signifying end of cure. True end of cure takes place when the reaction ceases and the material is no longer fluctuating; at this point, the slope is zero.
The reaction may go on at a very low level for a lengthy period, so for practical reasons, a small, non-zero slope is typically designated, with a value depending on the requirements of the application.
Figure 38-12 indicates the way in which the maximum value of slope increases with temperature. Again, this relationship is predictable, since the height of CP(3) is a relative measure of the maximum reaction rate.
.jpg)
Figure 38-12. Value of maximum slope vs. cure temperature for BMC.
DEA in Quality Control and Manufacturing
Temperature measurements, which fluctuate with the thermal environment, configuration of the mold, volume of material and other factors, have occasionally been used to observe cure through circuitous methods. In fact, a number of brands of thermoset curing ovens present their use of thermocouples for precisely this purpose.
Conversely, dielectric cure monitoring (DEA) directly measures material properties—ion viscosity, in particular—that indicate cure, delivering immediate insight in real time. Due to the simplicity and repeatability of DEA, manufacturers of BMC and SMC employ dielectric cure monitoring in their quality control departments.
Samples of each batch of BMC or SMC are tested at a controlled temperature. Critical Points, such as those detailed in Table 38-1, characterize the ion viscosity curve and these Critical Points are logged to monitor consistency in the material.
Satisfactory batches of BMC or SMC will have Critical Points that remain within a narrow range. Results outside this range indicate a process that could be out of control, meriting investigation or remediation. In this way, a manufacturer can uphold the quality of outgoing material.
Likewise, molders of end products using BMC or SMC can test incoming material to check that it will cure as anticipated. Some have fitted reusable dielectric sensors in their molds to monitor and record the processing of each part, accruing a manufacturing history for statistical quality control.
DEA in Closed Loop Process Control of BMC and SMC
The real time information offered through dielectric cure monitoring opens up the prospect of closed loop process control. Manufacturers of molded thermosets employ timers to govern when products are cured and may be removed from a press.
This typical practice must account for standard variation in process temperature and other factors that have an impact on cure. To be cautious, demold time is selected to ensure that all parts are good, with the upshot that some parts may be cured longer than is required. Over many thousands of parts, the use of timers wastes substantial amounts of time, effort and productivity.
One study of closed loop process control employed the hardware of Figure 38-13 at a company that produces commercial SMC products. A reusable dielectric sensor was fixed in the lower mold. The sensor was coated with mold release prior to the loading of each charge of SMC, after which the 2000-ton press was closed. Upon sensing end of cure, the dielectric cure monitor automatically delivered a signal to open the press.
.jpg)
Figure 38-13. Closed-loop process control with dielectric cure monitoring.1
Figure 38-14 illustrates the distribution of cure time during the production of approximately 1,000 parts. A fixed timer would have been set for 60 seconds to guarantee 100% good parts. In comparison, closed loop control with dielectric cure monitoring lowed average press cycle time to 50 seconds1. This reduction of 10 seconds would have saved $70,000/year/press in labor costs alone.
.jpg)
Figure 38-14. Distribution of SMC cure time for 1000 parts.1
Conclusion
Dielectric cure monitoring (DEA) allows for the observation of bulk molding compound (BMC) cure in real time, and the extraction of Critical Points quantify the distinguishing features of the reaction. Critical Points enable direct comparison of the cure of materials under different conditions. The ion viscosity data demonstrates the direct correlation between temperature and rate of cure.
As the only technique able to measure cure state in real time under actual process conditions, dielectric cure monitoring offers the ability to produce laboratory results that are directly applicable in manufacturing processes.
References
- Day, D.R. and Lee, H.L., “Analysis and Control of SMC Part to Part Variations,” Session 13-C of Proceedings of the 17th Annual Conference, Composites Institute, the Society of the Plastics Industry, Inc., Feb 3-6, 1992.
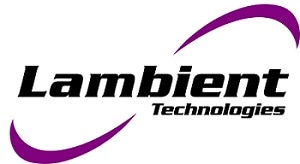
This information has been sourced, reviewed and adapted from materials provided by Lambient Technologies.
For more information on this source, please visit Lambient Technologies.