The field of microfluidics presents many applications, and therefore, has undergone massive developments over the last few years. Lab-on-a-chip, point of care devices, organ-on-a-chip, cell capture, and biological and chemical analysis are some of the examples for direct microfluidic applications.
Concerning applications, microfluidic devices have a variety of geometries which can be as complex as needed, but one of the standard structures that contain these microfluidic devices is the microchannel.
A number of materials have been stated for the fabrication of the microchannel, and the appropriateness of one or another relies on the fabrication method. A few of these materials are silicon, polymers, or glass. Examples of manufacturing methods are photolithopgraphy, soft-lithography, or thermofusing techniques. However, when using soda lime glass as material, which was preferred because of its robustness, transparency, chemical resistance, and low cost, direct laser writing presents itself as one of the most ideal approaches.
It is accurate and flexible, creating very complex geometries rapidly. Furthermore, because of its non-contact nature, there is no issue of contamination and requirement of clean room facilities. When dealing in micron dimensions for this application, it is vital to have a clear image of the topography to guarantee its quality, along with all the information relating to the channel dimensions.
In this article, the structures made using direct laser writing are completely characterized by means of confocal microscopy.
Measurements
Microchannels were made over soda lime glass using direct laser writing. A Rofin Nd:YVO4 system with 20 ns pulse duration and 1064 nm central wavelength was the laser used. The configuration was made up by a galvanometer system that addresses the beam and permits the fabrication of intricate structures without the need of sample movement. The laser beam was aimed over the substrate surface by using a lens of 100 mm focal length that guarantees a working area of 80x80 mm2. Soda lime glass was acquired from a local dealer.
To attain a correct aspect ratio of the structures, more than a few laser scans were applied to the sample. Thus, a study on the evolution of the topography was carried out. Microchannels with scans from 1 to 10 times were produced. Using Sensofar S neox 3D optical profiler, a confocal image of the structured area was taken with a 20X magnification objective. The surface profile was created and the development of the depth of microchannels using the laser scans was portrayed, as can be seen in Figure 1.
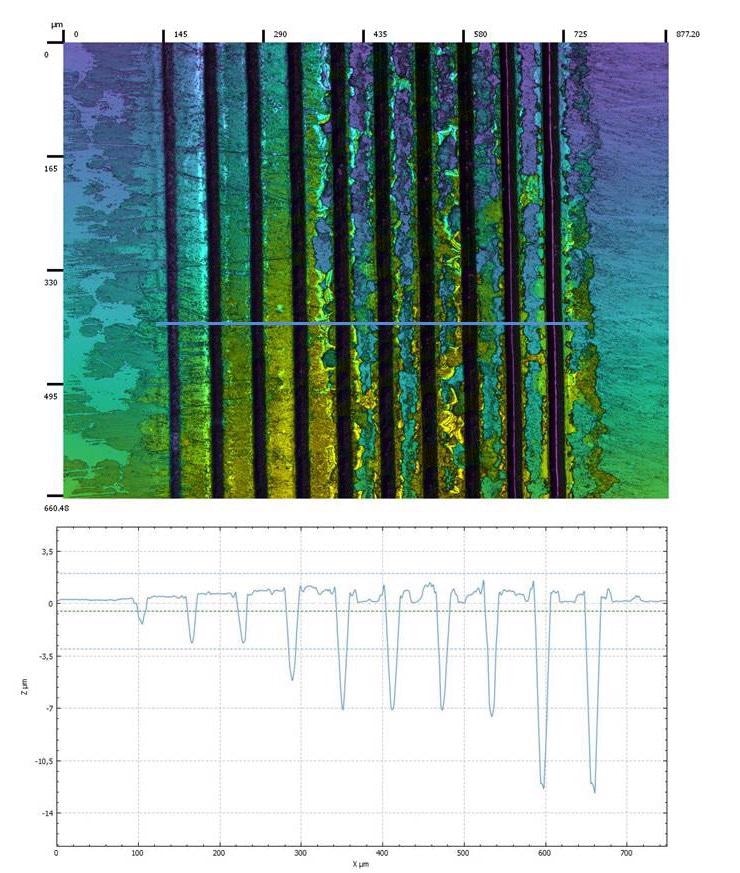
Figure 1. Confocal image of several microchannels with different laser scans, from one (left) to ten (right). The profile of the channels is also generated.
Roughness value of the microchannel walls is an important value to be aware of as it should be quite low for microfluidic applications. As a result of the Sensofar S neox 3D optical profiler and SensoMAP analysis software, it was possible to acquire roughness values from small areas. The topography of a microchannel’s bottom with eight laser scans, attained with a 50X magnification objective, was chosen for the study (refer to Figure 2).
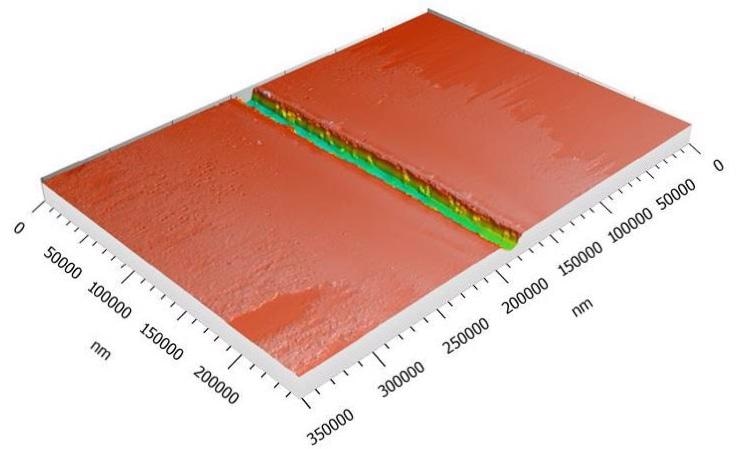
Figure 2. 3D topography of one microchannel fabricated with laser and the roughness parameters of the bottom of the channel, according to ISO 25178.
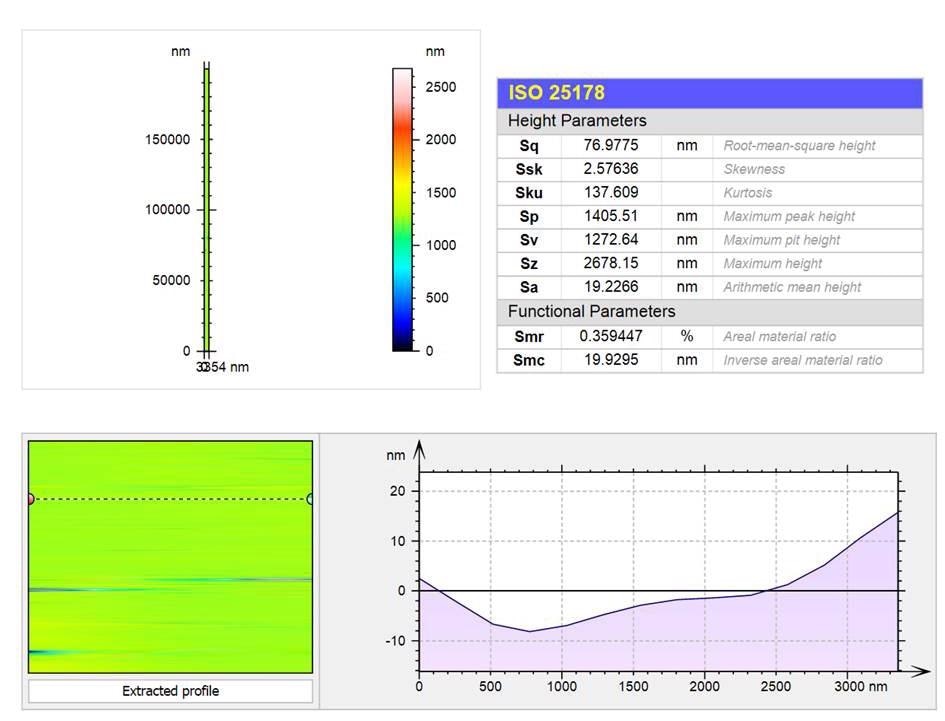
Due to the flexibility and accuracy of laser direct writing, numerous microfluidic devices can be mass-produced. In Figure 3, a few 3D confocal topographies of some of those examples obtained using a 20X objective can be viewed.
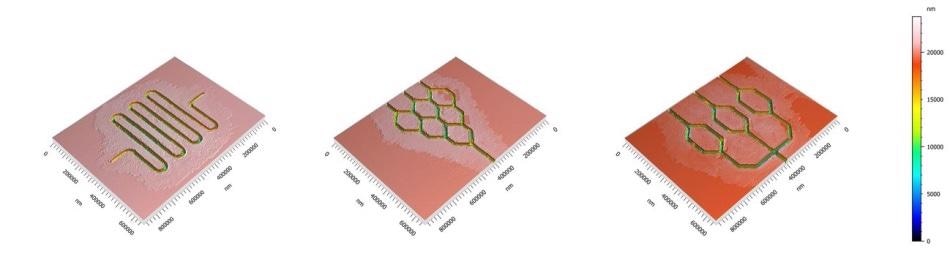
Figure 3. 3D confocal topographies detail some examples of microfluidic devices performed with laser over soda lime glass.
Conclusions
Thanks to the S neox, the 3D optical profiler from Sensofar, it was viable to simply characterize the topography of the microchannels fabricated using laser technologies. The evolution of the structural profile with the laser scans was examined by using the confocal method with a 20X magnification objective.
Furthermore, along with the SensoMAP analysis software, the roughness parameters of the manufactured channels were computed. Here, a 50X magnification objective was used when obtaining the confocal topography.
In brief, by using the S neox 3D optical profiler, each structure can be effortlessly characterized in roughness and dimensions.
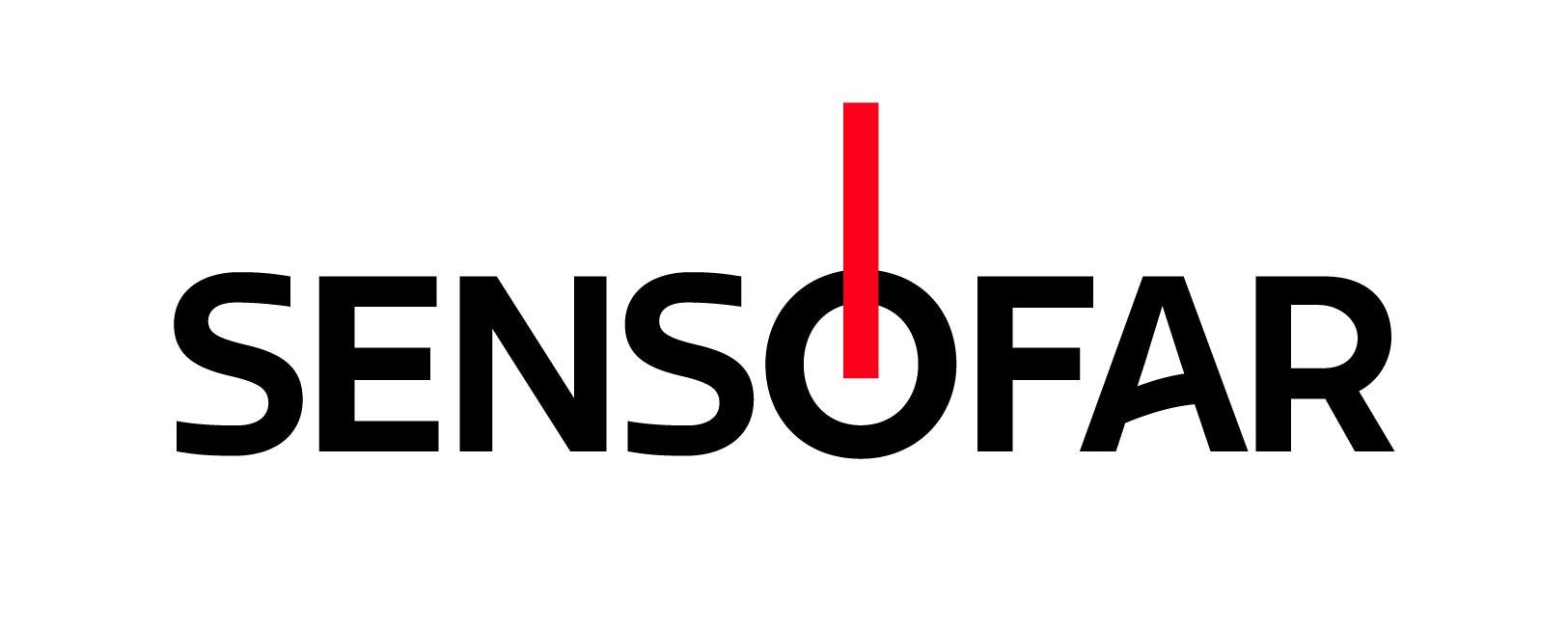
This information has been sourced, reviewed and adapted from materials provided by Sensofar.
For more information on this source, please visit Sensofar Metrology.