During the development of nano pressure sensors for biological applications, the sacrificial layer etching and the sealing of the two membranes divided by a vacuum gap to develop a Fabry–Pérot resonator is very important. Furthermore, being aware of the precise timing of the original deflection of the membrane following the fabrication process is paramount.
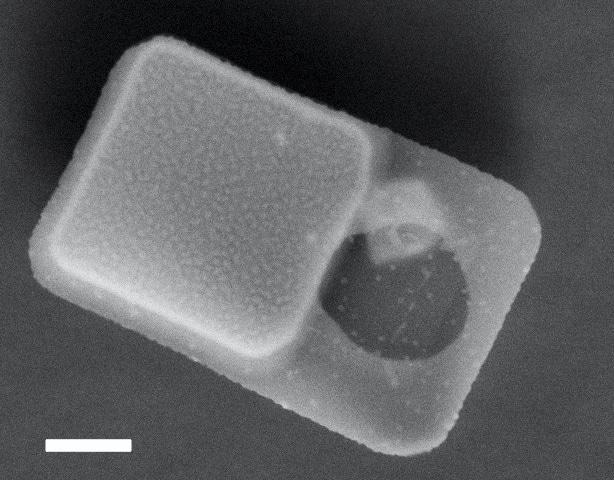
Figure 1. SEM image of the fabricated pressure sensors. Bar scale 1 µm.
Measurements
The pressure sensor is a 6x10 µm chip made up of a mechanical sensor characterized by two polysilicon membranes divided by a vacuum gap, and an optical reference area. The membranes serve as parallel reflecting mirrors, establishing a Fabry–Pèrot resonator that is partly transparent for certain wavelengths. An external pressure P deflects the membranes and alters the gap. This device was engineered to measure pressure variations within the various components of a living cell.
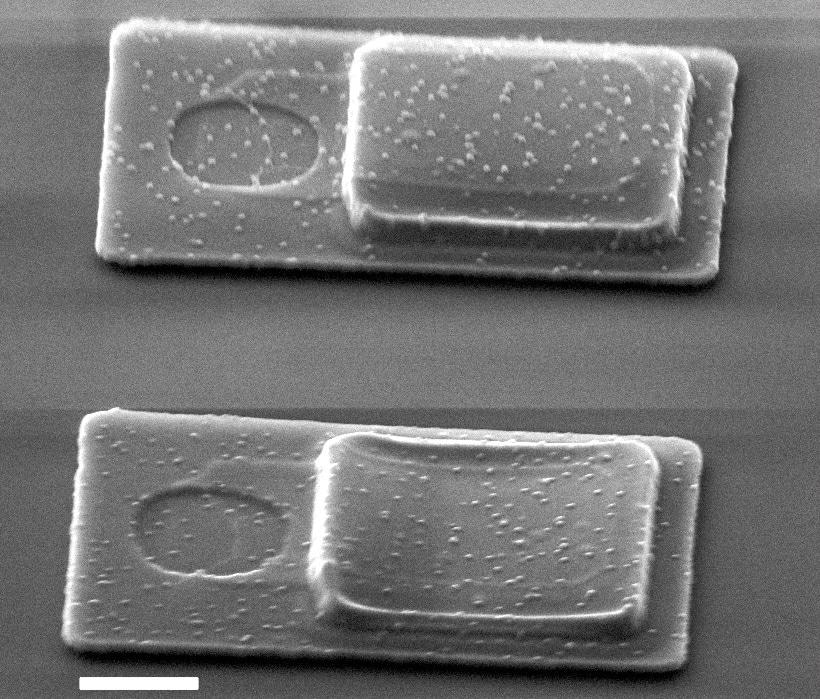
Figure 2. Device with a non-collapsed membrane (top) and a device with a collapsed membrane (bottom). Bar scale 1 µm.
Presently, membrane deflection measurements are done using Scanning Electronic Microscopy (SEM) before being internalized; however, in the SEM, samples have to be under vacuum pressure which may change their original state.
A Sensofar optical profiler enabled rapid and non-intrusive measurement of the deflection of the membranes following manufacturing. The chip’s dimensions are just a few microns, but the membrane’s curvature is closer to tens of nanometers, therefore it is essential to use a high magnification lens.
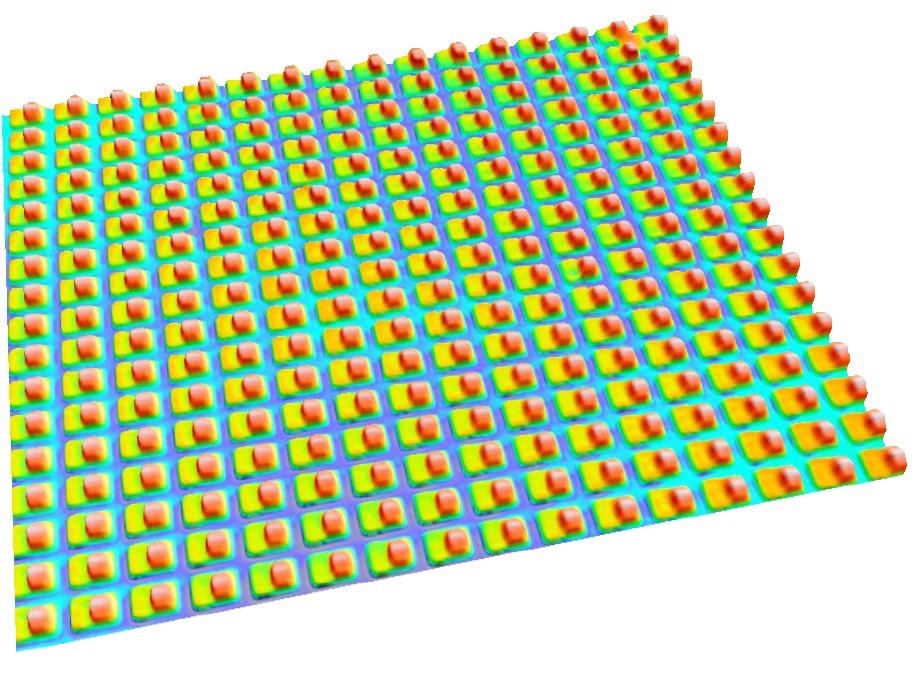
Figure 3. 3D topography of a pressure sensor’s array before the release from substrate.
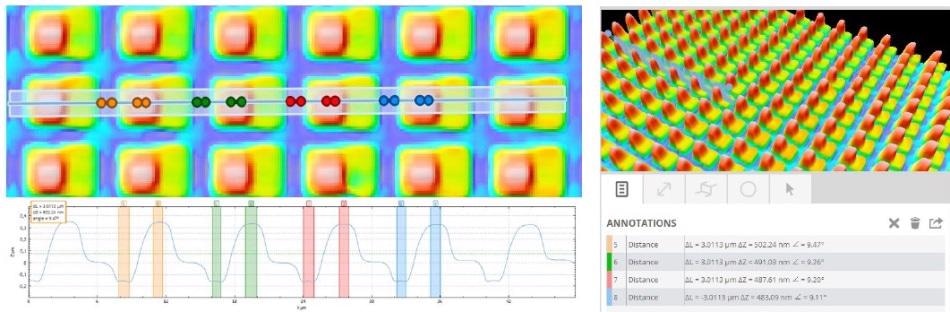
Figure 4. Profile analysis of several pressure sensors.
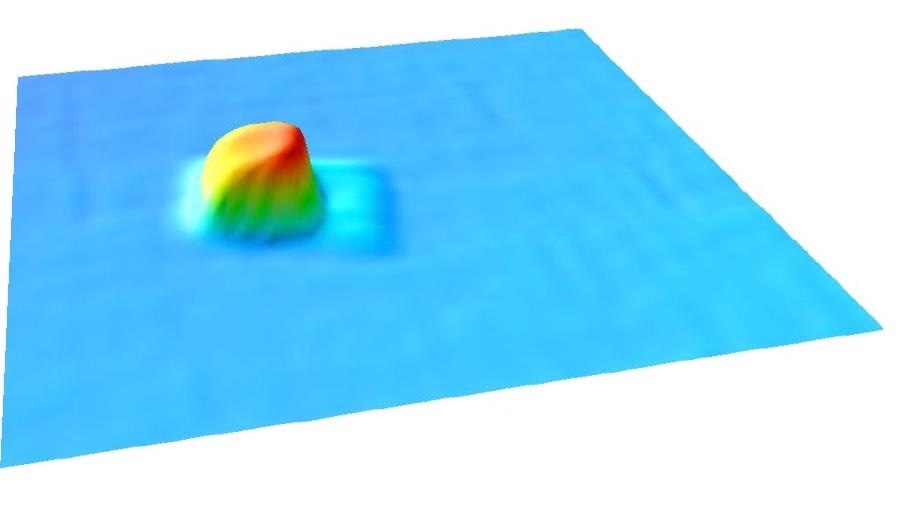
Figure 5. 3D topography of a 6x10 μm released pressure sensor.
Conclusions
With this method, a quick and non-destructive measurement of the deflection of the released membrane before and after sealing is possible, mainly to verify if the membranes have collapsed. Earlier, they had to be examined by SEM which caused variations in the deflection of the membrane because of the vacuum, and the deflection value was not as consistent. These measurements were acquired with a Plµ 2300 using a confocal method with a 100X brightfield objective.
Sensofar equipment offers non-contact 3D surface profilers founded on three technologies: Interferometry, Confocal, and Focus Variation methods. With Sensofar equipment, high-resolution measurements can be performed rapidly and in a non-destructive way, and easy-to-use software offers technical support as necessary.
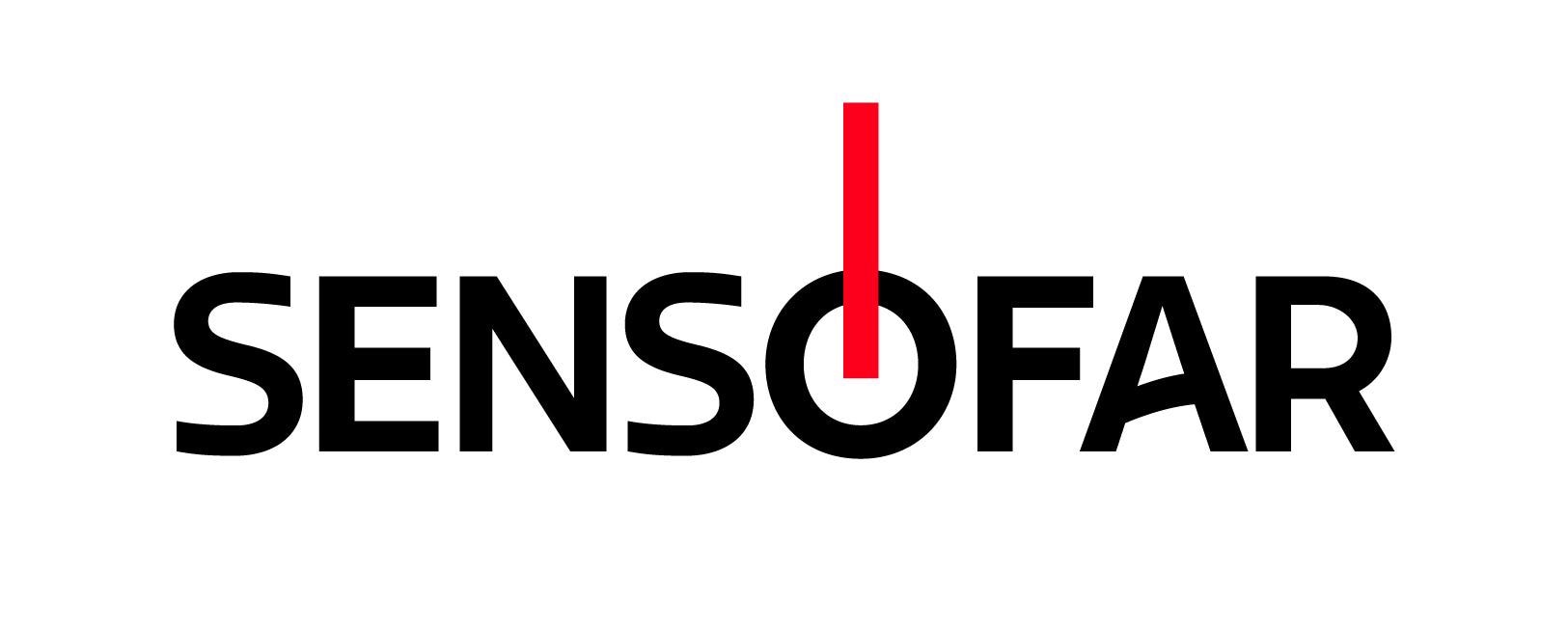
This information has been sourced, reviewed and adapted from materials provided by Sensofar.
For more information on this source, please visit Sensofar Metrology.