New product design engineers depend greatly on design and production methods learned through education, recurrent application, and empirical success. Several alternative methods are frequently approached with caution, especially on mission-critical applications where a recognized outcome is demonstrated, and thus thought to be “safe.”
Although it shows evidence of moderately low visibility, there is a time-tested production technique that needs to be better understood; it is known as cold forming. Due to this lack of understanding, it is not being fully utilized to achieve objectives in the reduction of cost, quality, yield, and waste that manufacturers look to improve quality and lower cost.
Cold forming is not a novel technology for producing micro-precision components, but it is still yet to be well known or better understood among New Product Development (NPD) teams. One reason why is that there is an extensive lack of related course work in engineering schools.
A fundamental explanation of the cold forming process, its features and advantages, and a review of some benefits compared to alternative production techniques like machining, MIM, and stamping is provided here.
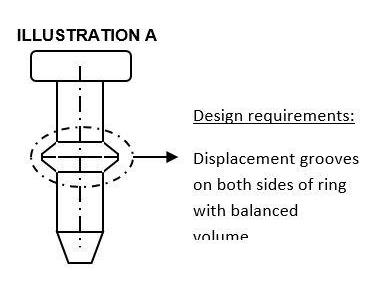
Image Credit: Sussex Wire
This is an example of a part frequently submitted for a roll-forming quote. The designer in this example has neglected to take into account "where is the material for the annular ring coming from?" (Source: Sussex Wire).
To be able to apply cold forming successfully depends inherently on every project’s four main contributors: the component producer; the materials provider; the tooling designer/producer; and lastly, the machinery producer.
An important role is played by each in deciding how a part design can be completed most efficiently and offers feedback to the customer with regards to important dimensions, tolerances, possible limitations, and alternatives to enhance strength and minimize cost at the same time as achieving all functional aims.
New product design engineers know to investigate these strengths and weaknesses in the early stages of the design procedure. They need to build a consultative relationship with the component design and production company to cooperate about alterations that could enhance the component’s strength and promote its manufacturability, while simultaneously providing the lowest cost choice available.
Frequently, in the time it takes a micro/miniature part geometry to be repaired by the NPD engineer, the possibility of making improvements passes. Although these areas might play a small role in the bigger project, their designs can be streamlined in order to meet all the designer’s aims if prior information is given.
In essence, occasionally trade-offs can be made on non-essential dimensions and tolerances to be able to meet functional requirements, particularly if the designer and component producer are collaborating prior to the final part design being approved. Indeed, this cooperative method is successful for any manufacturing process, not just cold heading or roll forming.
What is Cold Forming?
Cold forming involves force being applied with a punch to a metal blank staged in a die. The force is higher than the elastic limit of the alloy, resulting in plastic flow until the metal blank takes the shape bound by the punch and the die.
As implied by the name, this technique of forming is accomplished by force alone, without applying additional heat or cutting and shearing. Due to this, cold forming does not re-anneal or mechanically harm the material’s original metallurgical grain structure as other methods can.
There are four main benefits of cold forming:
Reduced Scrap/Cost
Cold forming is a net shape solution. During this method, wire is transformed by a sequence of die blows into a specific shape, with the material flowing to fill the part geometry and dimensional tolerances defined by the tooling engineer. Thus, there is nearly zero waste created.
Creating less scrap means there is little to zero recycling cost involved with the method, smaller amounts of lubricant to reclaim, and minimal labor to manage it all. Generally, the wire feedstock is cheaper compared to the bar used for machining. Sizing can be completed in line with the heading operation, so the tolerances on the wire feedstock do not need to be as tight as those required for the Escomatic Quality wire feedstock.
As with all types of screw machining, inclusive of single- and multi-spindle and Escomatic methods, scrap is inevitable, as well as being a significant by-product of the method, frequently the same as 50% of the final part’s mass.
Throughput
With an optimized part formation progression for a complex component, cold heading supplies yields at a rate of 90-300 parts/minute (PPM), standard. In general, yields for a similar design manufactured from a multi-spindle screw machine will be in the range between 6 – 20 PPM, an order of magnitude quicker for cold forming.
Because the price of each part must absorb a balanced share of production overhead, it becomes quickly obvious that a cold headed part can amortize that cost by several multiples compared to a screw machined part. In addition, the man-to-machine attendance rate prefers cold forming by a factor of two or more.
Strength
Cold forming is a method where die forging and punch upsetting (or heading) increases the native tensile strength of the material. It works so that for every 1% of area reduction of a part’s cross section as a result of cold forming, its tensile strength increases by a factor of ~0.6 - 1.5, alloy dependent. The work hardening rate of the material is what this physical property is also known as.
The work hardening rate differs depending on the tensile strength and material composition at the start. Stainless steels usually have higher work hardening rates compared to carbon steels. Super-alloys usually have higher work hardening rates compared to stainless steels. Ferritics (body-centered crystal structure, for example, carbon steels, annealed 410, & 430) usually have a lower work hardening rate compared to austenitics (face-centered cubic crystal structure, i.e. 302HQ, 304, 316 …).
Elements such as nickel and copper will suppress work hardening rates while elements such as carbon and nitrogen will accentuate the work hardening rate. Methods that remove material from the native shape, like screw machining, cannot achieve this.
Roll forming is an optimal technique for forming full radii, tapers, undercuts on solid material, and tubular parts with or without a head, splines, and so on. In addition, these strengthen the part simultaneously, instead of weakening it.
Roll forming is also versatile and it can form knurls, single or multiple cross threads for plastic inserts, barbs for one-way inserts, and clips, detents, or custom shapes for retaining two parts. Stronger product assemblies and grips can be achieved by engineers by implementing roll forming methods while using its optimum speed and economy as an advantage.
Eco-Friendly
Less reprocessing, along with related transportation, fuel, and labor costs are required because cold forming produces virtually no metal scrap. Lubricant is utilized in the die formation procedure but at a fraction of the rate for a screw machine (cutting) operation. Additionally, cold forming lubricants do not consist of metal scraps and are therefore cleaner and easier to recycle.
For screw machine operation, materials frequently consist of free machining additives. These free machining additives are a direct addition to the molten metal prior to casting into ingots. These additives are insoluble in the alloy composition and create discrete particles of a variety of shapes and sizes in the ingot casting.
To achieve microstructure, size and shape, the ingot goes through a sequence of hot and cold work operations and these particles, known as inclusions, get stretched out. Throughout the machining operation, these inclusions are very helpful because they act as weak spots where chips can break, as well as reducing the friction between the cutting tool and workpiece.
From a solely engineering standpoint, the inclusions have no value. From a cost standpoint, adding free machining additives are essential. They significantly enhance the capabilities of machine parts and improve rates of production.
For stainless steels, elements such as sulfur and selenium are the additives used most frequently. Grades like 303, 416, and 430F are very common in the world of screw machines. In carbon steels, sulfur and phosphorus are used in 1200 series grades while 12L14 gets an extra enhancement from Lead (~0.15 - 0.35 wt%) additions to improve its machinability. 360 brass consists of ~1.5 - 2.0% lead, solely for machinability.
These additives are not required in cold forming. From an engineering standpoint, a cold formed part lends itself to a superior possible design because the raw material has fewer inclusions.
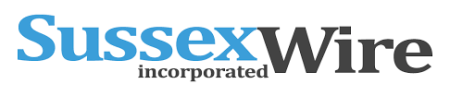
This information has been sourced, reviewed and adapted from materials provided by Sussex Wire Inc.
For more information on this source, please visit Sussex Wire Inc.