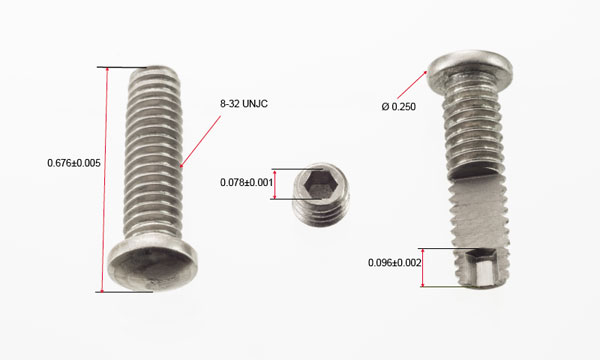
Image Credit: Sussex Wire
The CRES fastener for a new product design in an airframe latch had three different geometric challenges:
- A rolled thread over a backward extrusion
- A convex head feature
- A reverse hex extrusion
By cold forming the part in the first part of the process, Sussex Wire created the convex head and hex-shaped reverse extrusion. Due to the cold forming process, the hex created by the reverse extrusion was a stronger part than would have been possible using other methods like machining, which would have weakened the part significantly.
In order to thread-roll the part without collapsing the hex cavity, Sussex created a secondary process.
Material
Use
- Fasteners for the aerospace industry
Critical Tolerances
- 8-32 Thread to AS8879, UNJC-3A
- Inset hex depth and concentricity
- Head height and radius
Manufacturing Method
- Extrusion
- Reverse extrusion
- Cold heading
- Annealing
- Roll forming
Advantages
- Final tensile at 130,000 KSI, from original material tensile of 85,000 KSI
- No material scrap, 100% net shape
- Work hardened threads per AS8879
- Work hardened head-to-shank interface
- High throughput, low-cost alternative to machining
- Burr and silver free condition without mechanical secondary operation
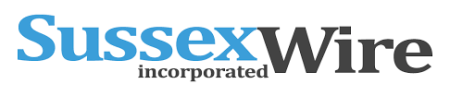
This information has been sourced, reviewed and adapted from materials provided by Sussex Wire Inc.
For more information on this source, please visit Sussex Wire Inc.