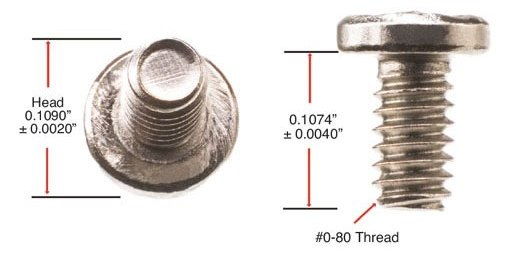
Image Credit: Sussex Wire
A manufacturer of premium fashion eyewear was looking for a way to incorporate functionality and branding into fasteners utilized on their products. They needed a logo that was clearly defined that would also work as a driver, to be designed onto a .1090” screw head. Sussex Wire provided the best solution in four ways:
- Quality through cold heading and enhanced part strength
- Drive functionality of branded fastener head
- Logo integration for brand protection
- Versatile tool package to minimize future cost and lead time
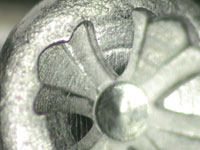
Screw head design with logo and driver functionality. Image Credit: Sussex Wire
The in-house engineering team at Sussex Wire worked with the manufacturer to develop a cold headed fastener. They ensured that the logo met the appropriate criteria for legibility, cold heading, and to permit usability as a driver.
The customer benefited from an increase in both driver functionality strength and fastener thread as a result of the cold heading process. Sussex Wire considered the future needs of the customer by designing a tool that would accommodate additional fastener lengths and threads via the tool design processes, allowing the customer to maximize investment.
Critical Tolerances
- Material with sufficient strength to use the fastener head as a driver
- Fully formed, lap free #0-80 thread
- Head diameter of .1090” ±.0020”
- Clarity of logo on screw head
Unique Benefits
- No material scrap, 100% net shape
- Brand identification
- Work hardening enhances component durability and product life cycle
- Versatile tool mitigates future lead time and cost
Material
Use
- Branded fastener for utilization in eyeglasses
Manufacturing Method
- Thread Rolling
- Cold Heading
Customers looking for a better solution for yield, strength, assembly and cost through the application of cold forming technologies should look to Sussex Wire, a global pioneer in collaborative design, development, manufacture and control of miniature and micro-miniature metal components.
Mechanical design and assembly firms around the globe look to Sussex Wire for their most advanced near-net-shape part requirements to reduce costly secondary operations, eliminate material scrap, and enhance mechanical strength.
Sussex Wire uses vertically integrated LEAN practices in design, manufacturing, order and worldwide inventory management. This includes stock custom micro and miniature components for JIT delivery to international customers in the consumer electronics, defense, energy, appliance, medical, automotive, aerospace, and semiconductor markets.
Their engineering team applies advanced progression, manufacturing knowledge and materials characterization and tooling to create cost-effective production routines for each customer's requirements.
By employing quick-turn prototyping, finite element analysis, CAD/CAM, soft tooling and in-house tool-making, Sussex has the depth and capabilities to move a project into production quickly.
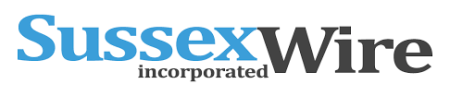
This information has been sourced, reviewed and adapted from materials provided by Sussex Wire Inc.
For more information on this source, please visit Sussex Wire Inc.