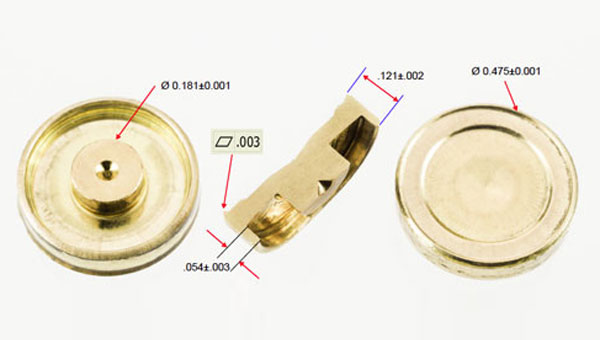
Image Credit: Sussex Wire
A new valve design that is used in a fuel pressure regulator for a major automotive part manufacturer presented a number of challenges for manufacturability. To begin with, the design of the valve seat limited the weight of the part, so to decrease weight, the material between the spring and rubber seal had to be as thin as possible.
Secondly, to ensure the rubber over-mold retention ring provided precise and repeatable seating, the rubber seal molded into the valve seat had to comply with a strict flatness specification of +/- .002 ”.
Sussex Wire created the part with a very thin wall meeting the flatness specs, whilst simultaneously enhancing the valve’s surface strength by virtue of work hardening the material property from the cold forming process. Production quantities were above 4,000,000 parts per year, with no degradation of part compliance or tooling.
Advantages
- Increased tensile strength
- 70 % cost reduction
- Consistent quality at high tolerances
- Five times faster throughput
- No material scrap/waste, 100 % net shape
Material
Use
- Fuel Pressure Regulator - Hybrid Vehicles
Manufacturing Method
- Extrusion
- Upsetting
- Cold Heading
- Finishing
- DeBurring
For customers looking for a better solution for strength, yield, assembly and cost through the application of cold forming technologies, Sussex Wire is a global pioneer in collaborative design, manufacture, development, and control of miniature and micro-miniature metal components.
To increase mechanical strength, eliminate material scrap, and reduce costly secondary operations, mechanical design and assembly firms around the globe look to Sussex Wire for their most advanced near-net-shape part requirements.
Sussex Wire uses vertically integrated LEAN practices in manufacturing, design, order and global inventory management. These include stock custom miniature and micro components for JIT delivery to international customers in the consumer electronics, medical, energy, appliance, automotive, defense, aerospace and semiconductor markets.
Their engineering team applies materials characterization, advanced progression, tooling and manufacturing knowledge in order to develop cost-effective production routines to fit each customer's needs.
Sussex has the depth and capabilities to move a project into production quickly, by using finite element analysis, CAD/CAM, quick-turn prototyping, soft tooling and in-house tool-making.
Advantages
- Significantly lower cost than machined part
- Tight tolerances pressure regulator valve pin
- 100% Net Shape – no material scrap
- Eco-friendly lead-free brass
- Work hardening increases component durability and product life cycle
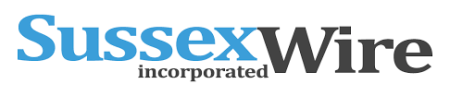
This information has been sourced, reviewed and adapted from materials provided by Sussex Wire Inc.
For more information on this source, please visit Sussex Wire Inc.