Due to a number of current persistent trends, the requirement to control and reduce costs by manufacturers of medical devices, surgical instruments, and healthcare consumable goods has been accelerated. These include an increasing population of Medicare patients, alterations in reimbursement practices, and tax implications associated with the Affordable Care Act.
These dynamics are resulting in medical device and surgical instrument manufacturers to look for modeling, design, and manufacturing technologies that enhance NPD (new product development) efficacy and time to market while minimizing assembly and manufacturing and costs.
Many medical devices and surgical instruments contain precision-engineered miniature and micro metal components created from a large variety of expensive, and often precious, raw materials.
Manufacturers are focused on minimizing these raw material costs and looking for ways to save labor-intensive assembly costs at the same time, while improving yield and component reliability. Firstly, it is crucial to identify and understand the strengths and weaknesses of the many methods available for manufacturing micro miniature components.
Each of the practices below can be a good solution for a certain range of applications, but with each comes a number of considerations, like lead time, strength, tooling cost, part configuration and cost of ownership which must be evaluated to establish the best manufacturing technique to use on a specific part.
This article will look at the pros and cons of screw machining (or Swiss machining), stamping, cold forming (or cold forging), and metal injection molding, and give examples of how cold forming can enhance production efficiency, quality and cost of ownership in medical device manufacturing.
Traditional Manufacturing Processes
Metal Injection Molding (MIM)
Advantages
- Production velocity: Quite good but not as quick as cold forming or stamping.
- Strength: Very good, but not as strong as in cold forming. MIM may have issues with lateral fatigue potential depending on directionality of the stresses on the part. MIM often has issues with achieving “density” on par with cold forming.
- Scrap: None, very similar to cold forming. The process involves filling a mold with a powdered metal composite, so there is no waste.
- Shape: As with cold forming, an excellent process for highly complex asymmetric shapes, instead of purely axial symmetric shapes.
Disadvantages
- Part cost: The process costs more than machining, stamping or cold forming because of multiple steps.
- Lead time: Tooling can be more time consuming than that of cold forging. Multiple process steps usually require numerous castings which can take additional tune-up time. One of the issues is material shrinkage of between 25 and 30%, which makes it almost impossible to manufacture predictable parts with variations in wall thickness without extensive trials.
- Secondary operations: In order to evacuate the supporting matrix from the finished part, MIM parts have to be batch processed in a vacuum heat treating furnace. Operation and maintenance costs relative to the vacuum sintering process contribute significant overhead, increasing the total cost of part ownership.
Stamping
Advantages
- Strength: Stamping keeps the original material strength in the center of the shape as it is being reshaped not cut.
- Shape: Stamping is an economical, good solution for long-run 2-dimensional configurations.
- Production velocity: Much quicker than machining, about equal to cold forming.
Disadvantages
- Lead time: Tooling time from print to first article can be quite long when compared to cold forming.
- Strength: On deep draw operations (which produce a more 3-dimensional shape), stamping can create only a single wall thickness which, depending on the application, could compromise its structure. There can also be some weakness At the boundaries of the part.
- Scrap: Similar to screw machining, stamping removes material from sheet goods.
- Part cost: Stamping alone can be performed relatively economically, with tooling capital amortized over long runs. Yet, when accounting for scrap plus the addition of any required secondary operations, costs can be higher than those of cold forming.
- Tooling: Particularly when used for short runs it can be cost-prohibitive compared to machining, about the same or a little less than cold forming.
- Secondary operations: Usually needs deburring, polishing, and finishing. Near-finished parts frequently require other processes to create features like external ribs, knurled rings, or extensively milled morphologies, which are not necessary with cold forming.
Screw Machining / Swiss Machining
Advantages
- Tooling: Relatively low cost for short-run projects compared with stamping, MIM, or cold forming.
- Lead time: Tooling time from print to first article may be less (via CNC) than MIM, stamping, or cold forming.
- Shape: Can handle several variations among major and minor ODs around the length of the part.
Disadvantages
- Production rates: Depending on the size and geometry of the part, screw machining can create 12-15 parts/minute. Stamping and cold forging can create up to 90 to 300 parts/min.
- Secondary operations: Machining often needs deburring, polishing, and finishing.
- Part cost: Parts that take longer to create have a higher contribution of fixed direct and indirect overhead costs.
- Scrap: Cutting away material is integral to the process, and removal of material causes scrap. Even if the scrap is recovered, it needs an additional step and added process cost.
- Strength: Machining destroys the grain structure of the metal, versus simply modifying the grain structure like in MIM, stamping, or cold forming, all of which – to a greater or lesser degree – preserve the native structural properties of the material.
Cold Forming: A Better Alternative?
Not as widely applied or well known in the manufacture of precision micro-miniature components, cold forming, or cold forging, is the application of force with a punch to the end of a precise metal cut-off blank which is contained within a die. The force is higher than the metal or alloy’s yield strength or elastic limit, causing plastic flow.
Instead of compromising it, as machining processes often do, cold forming retains the material’s structural properties. Cold forming is frequently utilized for component heading, extruding, trimming, thread rolling, sizing, upsetting, piercing, blank rolling and pointing operations.
Advantages
- Strength: Cold forging retains the original grain structure or native material structural integrity of the material as it has not removed or destroyed any part of the material; i.e., final part formation process eliminates destruction of grain. Instead, it reforms it into a final part. So cold forming leverages its final form from the native mechanical nature of the part, including ductility, tensile strength, and hardness.
- Scrap: Little to no material is sacrificed in part manufacture, except in trimming, which may make up under 2% of the part mass. Cold forming creates a "near net shape" (and often a complete net shape) part.
- Shape: Cold heading can be manipulated to acquire almost any variation of wall thickness, i.e., many different wall thicknesses in the same part.
- Production velocity: Cold forming has a throughput volume of part production between 90-300 parts/minute, and so it absorbs overhead over a much bigger production of parts.
- Elimination of Secondary Operations: There is no need for finishing to deburr and/or tumble parts for the removal of rough edges. Cold forging leaves clean, rolled edges versus screw machine or stamped parts that usually need deburring. Additionally, cold forming eliminates the requirement to connect two parts together by brazing, which is at once a time-consuming process and also creates an assembly with a potential weak point versus a cold formed part (eg: headed pin with lead and heat sink).
- Simplified Final Device Assembly: By decreasing the number and type of components and consolidating multiple parts into a single cold formed product, cold forming is able to eliminate assembly. It decreases additional assembly operations by virtue of delivering a more complete part than would be possible using discrete operations.
- Part cost: Due to its near net shape process and elimination of scrap, higher production velocity, and the ability to amortize tooling cost over long runs of parts, cold forming yields a lower part cost versus other manufacturing technologies. Using cold forming, material cost saving in certain medical device applications is directly proportional to the cost of the raw material, for instance, where platinum, niobium, palladium, or platinum/iridium are frequently employed in components found in electro-regulating implantable devices and diagnostic/monitoring devices.
Disadvantages
- Lead time: More than screw machining from design to first part, but about the same or shorter than stamping and MIM.
Examples of Cold Formed Components in Medical Devices
Surgical Endoscopy Forceps
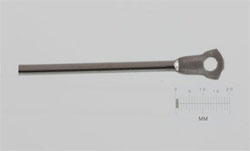
Disposable endoscopy forceps stainless steel drive wire cam actuator. Image Credit: Sussex Wire
In this device, instead of the more common braided wire (rope), a single high tensile stainless steel (piano-type) drive wire is used. Using a specially cold-formed loop in a single piece, the jaw fastens to the end of the drive wire. The “distal tip” is cold formed instead of machined, giving it tremendous strength but retaining a very tiny morphology.
Benefits include:
- Confidence: With less risk of a failed or improper procedure, surgeons can feel better about the outcome of the procedure.
- Control: Single piano wire (fine gauge stainless steel) material enables enhanced tactile response and a much better surgical experience for the doctor versus braided wire.
- Size: Single-drive wire device is half the size of that made with a braided wire version.
Medical Staples
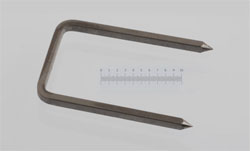
Titanium bone staple. Image Credit: Sussex Wire
These seemingly common and fairly simple staples which are utilized in joining tissues are actually manufactured to very tight tolerances. They are ideally suited to the cold forming process as it is the optimal technique to achieve the unique morphology of the shape and tolerances that the part demands.
Benefits include:
- Reduced cost: All of these operations are performed in a single pass, eliminating all secondary operations with the exception of passivation to prevent corrosion.
- Tolerances: Cold forming applies a combination of mfg operations to cut, form 40 degree points on the ends (+15 degrees/-5 degrees), and form the wire into a final U-shape to dimensional control standards of (min +/- 0.002”).
Hypodermic Needle Hubs
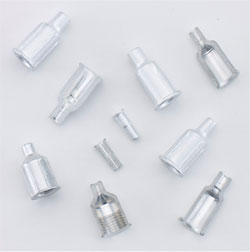
Hypodermic needle aluminum hubs and inserts. Image Credit: Sussex Wire
This part is the mechanical interface between the syringe and the cannula. The hub supplies a mechanical bond to make sure that the cannula and syringe do not break where media is tough, as in the instances of veterinary and dental medicine when encountering hard or resistant matrix such as hide, gums, etc.
Benefits of the cold headed part include:
- Cost: Cold formed aluminum supplies attractive strength (and can be shaped much more easily) at a much lower material cost than stainless steel. By cold forming, throughput can be over 165 parts/minute with no scrap, decreasing the cost of the part. The ribs on the OD of the part are formed in a die, which is a much cheaper, quicker, more dimensionally consistent process than milling by machining or screw machining.
- Strength: Better mechanical integrity of aluminum, which is a corrosive resistant, light material with excellent mechanical properties. Cold forming creates better mechanical strength versus machining.
- Finish: Cold heading and the associated finishing operations in this application create a smoother, burr-free product.
Educating the NPD Team
Why do NPD professionals depend on traditional metal component manufacturing technologies when there are so many extraordinary benefits of cold forming? Cold forming is a proven technology that has been utilized since the mid-20th century, but it is not widely known or appreciated in the general product design community.
In Mechanical Design and Manufacturing Engineering degree programs, Design for Machining is a required undergraduate academic course. In contrast, not much course work is devoted to cold forging, so it has become an unfamiliar practice.
There are only a few universities globally that provide extensive course work in cold forming technology. One of them is Aalto University in Finland. As product design/development staff have little institutional or academic education on the advantages of cold forming, they design using methods that are familiar with, like screw machining, stamping, MIM, etc.
Likewise, in the commercial world, there is limited access to training on cold forming / forging design and manufacturing methods. Most of the commercial training is provided by the machine manufacturers themselves, as there are few companies performing cold forging.
One of the suppliers of cold heading equipment for large parts is National Machinery. Micro-scale parts are commonly made on equipment from Nakashimada (Japan), which is one of the only companies in the world making cold forming equipment for long life cycle, small size precision parts.
National Machinery provides courses in cold forging, and it may be one of the only commercial resources doing so in America. While the principles of large scale cold forming are the same for micro-size parts, the scale and precision are extremely different.
New product design staff are reliant on partnering with vertically integrated cold forming / forging engineering and manufacturing firms to help them achieve their goals because of the lack of educational and commercial training resources.
These firms give collaborative development and prototyping within the construct of non-recurring engineering (NRE) agreements. The fruits of these agreements frequently manifest in supplier contracts for cold formed parts.
Materials companies like Carpenter Technologies can supply some knowledge, but mostly with cold forging companies themselves, not their customers. A potential customer can achieve a genuine proof of concept only in conjunction with a cold forging company such as Sussex Wire, Inc. located in Easton PA.
Conclusion
Medical device and surgical instrument manufacturers can benefit from a broader perspective encompassing cold forming / forging design and manufacturing to decrease cost and increase time-to-market and NPD efficacy.
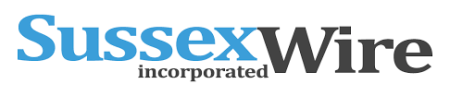
This information has been sourced, reviewed and adapted from materials provided by Sussex Wire Inc.
For more information on this source, please visit Sussex Wire Inc.