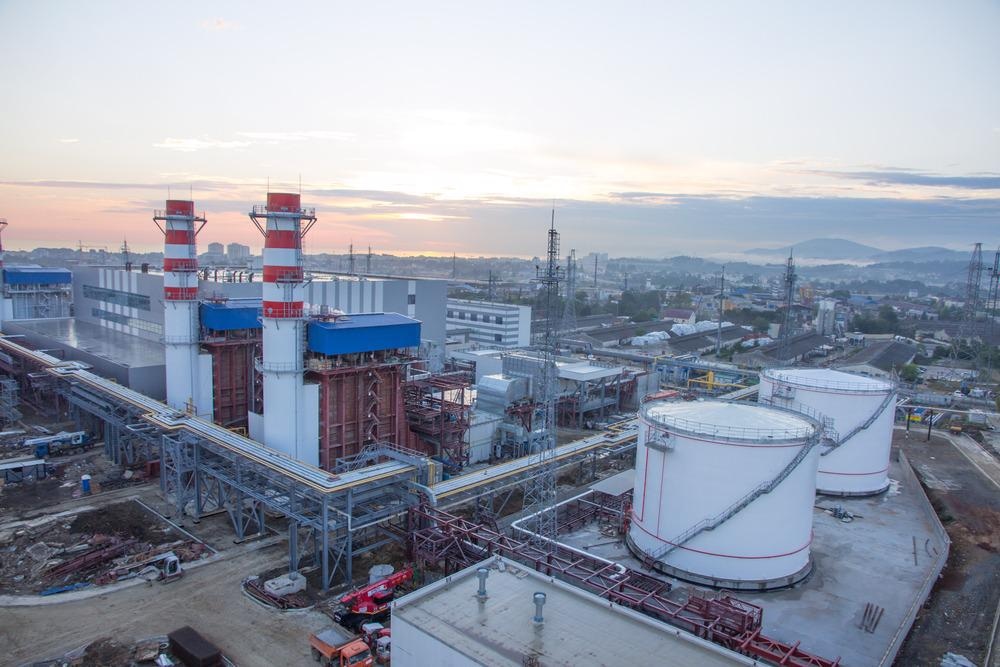
Image Credit: Merkushev Vasiliy/Shutterstock.com
There is an increasing need to look deeper into the technologies that make renewable energy more possible - one of them is thermal energy storage (TES).
What is Thermal Energy Storage?
TES is a versatile technology that can be used to address the mismatch in energy supply and demand. For example, thermal energy supply from concentrated solar power is highly susceptible to the changes in daily and seasonal solar radiation i.e., the absence of sunlight at night and the longer nights in winter. To make it efficient, it needs to supply uninterruptible energy — this is where TES comes in.
This article focuses on medium to high-temperature materials (140 - 400°C). They are promising in applications such as food industries, dairy, metal preheating, and chemical processes.
There are three major thermal storage technologies:
- Sensible storage stores thermal energy by raising the material's temperature, be it solid (e.g., clay bricks in home storage heaters) or liquid (e.g., molten salts and water). Water is a common sensible thermal store at homes or in industries. An inexpensive option, its use is limited to 100 °C.
- Phase change material (PCM) stores energy as it undergoes a phase change, most commonly from solid to liquid. The energy uptake and release, as latent heat, occur at a constant temperature.
- Thermochemical method stores energy by breaking and reforming molecular bonds in an entirely reversible chemical reaction. This technology is still new and subject to further research, but it has a high potential for future use.
Phase Change Materials
Phase change materials store and release heat during melting and solidification, respectively. They are preferable to sensible stores primarily due to their uniform charging/discharging temperatures and higher energy densities, leading to compact spatial requirements. The smaller size of PCMs can lead to industrial implementation, where space is often a premium, and in cases where modularity is prized i.e. transportable storage devices.
There are three major aspects of PCM deployment:
- Material selection
- Heat exchanger design
- Process integration
We will discuss more on material selection in the next section. For PCMs, robust heat exchanger designs are essential to remediate their common feature of low thermal conductivity. The means to integrate into the process e.g., via heat transfer fluids, are equally important.
Crucial Properties of Phase Change Materials for Successful Industrial Deployment
PCM material selection is the most important first step, and it will inform the subsequent steps of heat exchanger design and process integration. It is based on these primary criteria:
Melting temperature
The first property to look at is the melting temperature, which is related to its intended application. For example, the preheating process in the metal industry has a temperature demand of 220 °C. Therefore, we need to select candidate materials that charge/discharge heat at this temperature. For example, NaNO3-KNO3 (46-54%) melts/solidifies at 222 °C, compared to LiNO3-NaCl (87-13%) at 220 °C. Both materials are examples of eutectic salt PCMs. PCMs can be of salts, metals, paraffins, eutectic salts/alloys, sugar alcohols, or any other types. Subcooling, where a material discharges heat during solidification at a lower temperature than its melting temperature, must also be assessed through testing and subsequently remedied.
Latent energy density
Latent energy density dictates a PCM store size and weight, often preferable for a small and compact device. The energy densities of NaNO3-KNO3 and LiNO3-NaCl are 100 kJ/kg and 290 kJ/kg, respectively. Therefore, the latter is the preferable material.
Thermochemical stability
This criterion can inform on the longevity of PCM stores. We do envision a long storage lifespan to ensure a healthy return on investment. As a rule, a material melting temperature and latent heat of fusion should not significantly degrade after 1000 thermal cycles. Formation of by-products, decomposition, and phase separation should also be assessed. For example, d-mannitol (sugar alcohol, melts at 166 °C) melting enthalpy decreases by 9% after 500 cycles, whereas LiNO3 (melts at 254 °C) decomposes to Li2O at 400-450 °C.
Thermal conductivity
Aside from metal-based PCMs, thermal conductivities are generally low. For example, LiNO3-NaCl’s thermal conductivity is at 0.57-0.60 W/m.K and NaNO3 (melts at 306 °C) at 0.51-0.59 W/m.K. This complicates heat charge/discharge processes as they will occur very slowly. This is why innovative heat exchanger design is a crucial aspect in PCM development (e.g., designs with fins and metal foams) — this is a topic of research in its own right.
Volume expansion and material compatibility
During a phase change, volumetric expansion/contraction (typically expansion as solids melt into liquid) will need to be accounted for in the heat exchanger/containment designs. For example, LiNO3 expands in volume by 21.5% as it melts. Material compatibility and corrosion tests must also be carried out to ensure longevity and operational safety.
The Future is Bright for Phase Change Materials
PCM research is getting more rigorous over time as its potential in carbon reduction and cost reduction is huge e.g., in waste heat recovery, renewable energy, and residential thermal storage. Unfortunately, many works focus heavily on the melting temperature and energy density properties only, without delving deeper into the criteria aforementioned in this article. There is a surprising lack of PCM thermal stability data in literature that must be addressed to respond to the numerous developmental challenges. Robustness in PCM material selection is crucial to ensure economic returns on novel thermal store investments.
References and Further Reading
Crespo, A., Barreneche, C., et al. (2019) Latent thermal energy storage for solar process heat applications at medium-high temperatures – A review. Solar Energy. 192, 3–34. https://doi.org/10.1016/j.solener.2018.06.101
Neumann, H., Niedermaier, S., et al. (2018) Cycling stability of d-mannitol when used as phase change material for thermal storage applications. Thermochimica Acta. 660, 134–143. https://doi.org/10.1016/j.tca.2017.12.026
Tamme, Bauer, et al. (2008) Latent heat storage above 120oC for applications in the industrial process heat sector and solar power generation, Int. J. Energy Res. 32, 264–271. https://doi.org/10.1002/er.1346
Disclaimer: The views expressed here are those of the author expressed in their private capacity and do not necessarily represent the views of AZoM.com Limited T/A AZoNetwork the owner and operator of this website. This disclaimer forms part of the Terms and conditions of use of this website.